目次
ギガキャスト用鋳造機はいくらする?
アルミ合金鋳造機と言えば、日本では型締力3000トン程度が最大だ。鋳物は製品の形になる鋳型に溶けた素材(溶湯=ようとう)を流し込んで作る。製品を取り出すために鋳型は最低でも2分割されている。複雑な形状の鋳物の場合は4分割、6分割の場合もあり、それぞれの金型を異なる方向にスライドさせて製品を取り出す。
現在のアルミ合金鋳物自動車部品は、ほぼすべて高圧鋳造という方法で作られる。鋳型の中の空気を引き抜きながら高い圧力で溶湯を押し込む方法だ。エンジンのシリンダーブロックのように重量で20〜30kgの溶湯を使う大物でも、溶湯注入は0.1秒程度で終わる。何もないところへ瞬時に大量の溶湯が流れ込むため、鋳型を大きな力でしっかりと閉じておく必要がある。その力が「型締力」である。
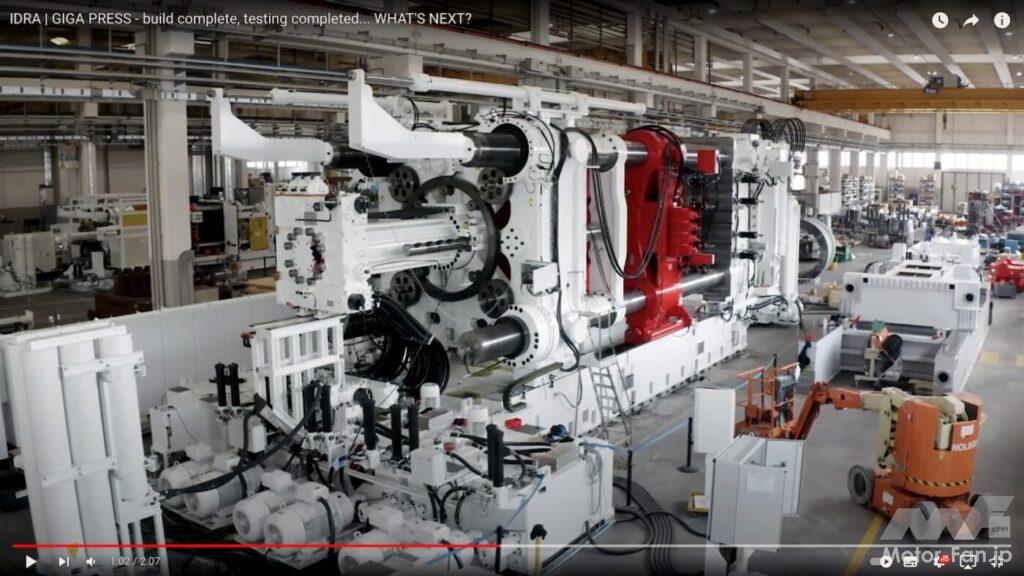
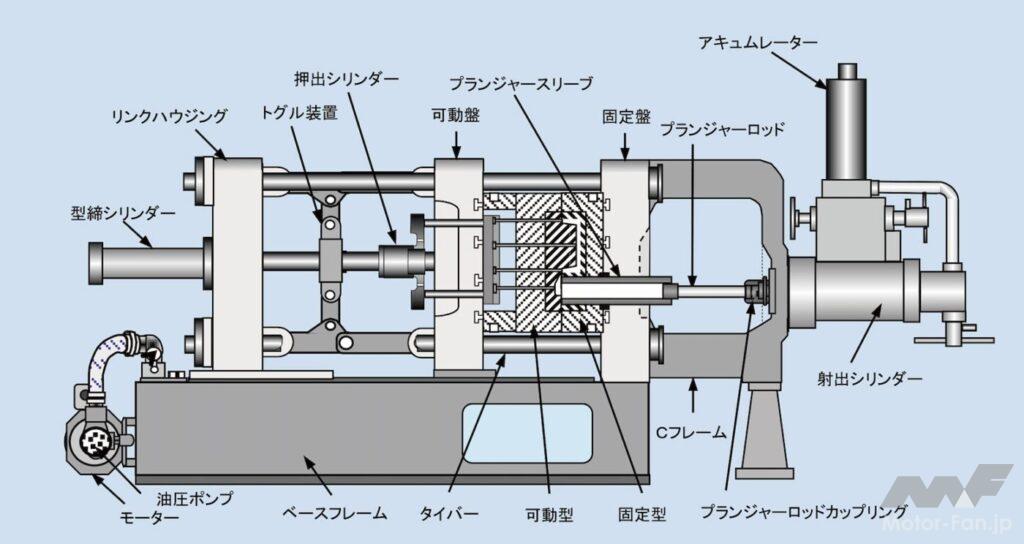
米・テスラが最初に使ったイタリア・イドラ(IDRA)製の大型アルミ合金鋳造機。いわゆるギガ・キャスティング・マシン(以下GCMと略)は、この型締力が4500トンだった。この鋳造機を使ってテスラ「モデルY」のボディ後部骨格を左右2分割のアルミ合金鋳物で作った。約70点のプレス鋼板を溶接して作っていた「モデル3」比べ「モデルY」はほぼ同じ構造を2点の部品に集約した。
現在、テスラは「サイバートラック」用のアルミ合金鋳物を作るため型締力9500トンというさらに大型のGCMを導入した。鋳造機メーカーによると、型締力8000トン級のGCMで1回の鋳造に100kg程度のアルミ溶湯を使う場合でも、金型への溶湯注入は0.1秒程度だと言う。ただし、8000トンの型締力を得るための油圧装置や、巨大な金型を保持する装置、そしてこれらを支えるGCM本体の土台部分は極めて大きくて重たいものになる。
いま、鋳造機メーカーが取り扱っているGCMのスペックを拾い集めると、その重量は型締力の10〜12分の1程度になる。型締力8000トンのGCMなら重量は670〜800トンが相場だ。
これほどの重さの機械を、たとえば部位ごとに15程度まで分解しても、ひとつの重量は単純な割り算で平均45〜55トンになる。だから輸送は大変だ。道路管理者(国や自治体)に重量物運搬を申請し、運搬ルート内に橋がある場合は強度計算を行なって「通れるかどうか」を見極め、橋の強度が不足している場合は補強を行なう(運搬が終わったら補強は撤去)必要がある。
このような道路での運搬のための許可申請には半年ほどかかる場合もある。実際、国内ではリョービによる申請がほぼ6カ月かかった。そして、50トン級の重量物をすべて運ぶだけでも運搬費用は1億円を超えるという。さらに、大型鋳造機を入れる建物には、巨大な金型を吊り下げるための巨大クレーンが要るほか、建物は基礎工事をしっかりと行う必要がある。これらの設備費用は10億円単位になる。
GCMそのものは、たとえば中国の海天金属(Haitian)や伊之密(Yizumi)の場合は型締力8500〜9000トン級でも4000万人民元(1元=20年で計算して8億円)程度という見積もりのようだ。関係者に訊いても「10億円はしない」という。テスラが導入したIDRA製GCMについてコストシミュレーションしたコンサルティング企業は「米国では輸送費は日本ほど高くならない。運搬の許可は州によって異なるが、日本よりは非常に簡素」「欧州も米国も地盤は日本よりしっかりしているため建物側のコストも日本より安い」という。
ちなみにイタリア企業のIDRAは2008年に香港資本のLKテクノロジー・ホールディングに買収された。同社は持ち株会社であり、傘下に中国など国籍の異なる企業をいくつも抱えた多国籍企業だ。アルミ合金鋳造機はLKマシナリーが製造を担当しており、最近はとくにGCMに力を入れている。
日系OEMは、設備導入するだろうか?
日系OEMは、こうしたGCM導入のための費用負担を覚悟してギガキャストを導入するだろうか。ただでさえ鋼材に比べて材料価格が割高になるアルミ合金だから、出来上がった鋳物を長距離輸送するのはコスト面でナンセンスであり、GCMは自社の車両工場内に置くのが理想だ。テスラや中国勢はそうしている。そのための設備を新規に導入する費用を日系OEMは受け入れるだろうか。これが「迷い」の理由のひとつめだ。
2つめは商品企画、商品戦略に関わる部分だ。ギガキャスト部品を「1車種専用」にするか、複数車種で使い回すか、だ。テスラがギガキャストを使っているのは「モデルY」と「サイバートラック」であり、ともに兄弟車も派生モデルもない。両車のギガキャスト部品はまったく別物であり、共通化はしていない。
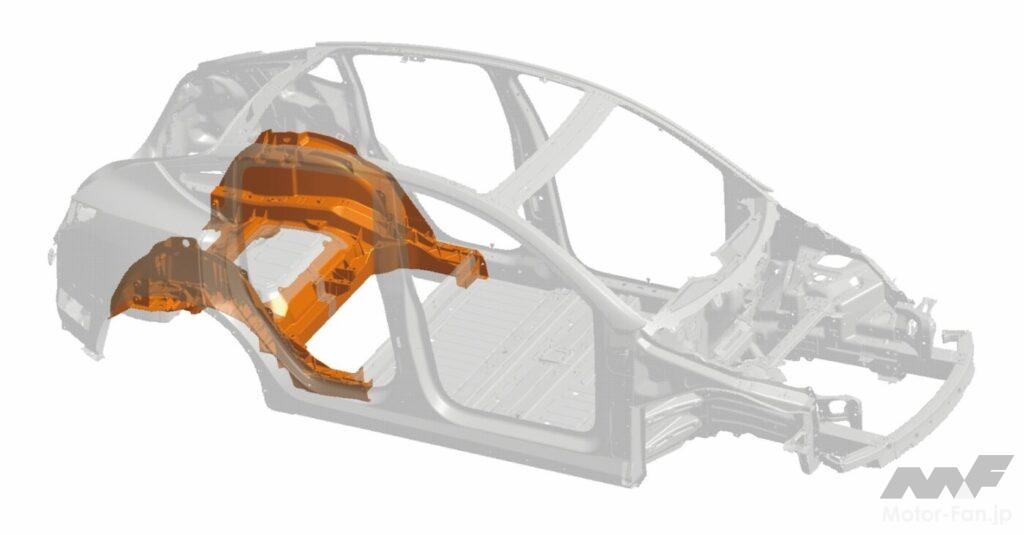
自動車ボディの骨格部分は、クルマの大きさが同程度ならそれほど大きくは変わらない。構造を見れば「モデル3」と「モデルY」の設計統合はある程度まで可能だし、ボディの大きさがほぼ同じになればギガキャスト部品の共有も可能だろう。当然、両方のモデルから派生車種を作ることもできる。
しかし、その場合はGCMの能力が問題になる。GMCをフル稼働させ鋳造回数(ショット数)が増えれば、それだけメンテナンスは頻繁に行なわなければならない。一般にアルミ合金鋳造機では金型のメンテナンス間隔は10万ショット程度だ。製品が増え、金型交換の頻度が増えればGCMそのもののメンテナンス間隔も短くなる。
たとえばトヨタのように全世界で100車種以上というフルラインアップを持つOEMが、骨構造を共有できる5〜6車種だけにギガキャストを採用にするにしても、工場ごとに複数のGMCを持たなければならない。まずは国内向けの高級モデルだけ、あるいは北米で生産するモデルだけというところから着手するという選択肢にならざるを得ない。
将来、さらに多くの車種でギガキャストを使うとなれば、それぞれの車両工場にGCMを少なくとも3台は導入しなければならない。あるいはGCMは2台にとどめ、金型のスピーディな交換で対応するか。トヨタは後者を検討している。
1工場ごとにギガキャスト部品が複数になれば、金型の交換を日常的に行わなければならない。金型重量は、2分割の場合で50〜60トン以上になる。これを素早く、たとえば30分以内で終わらせるとなると工場内に吊り上げ能力100トン級の天井クレーンが要るほか予備の金型を備える必要も出てくる。
逆に、1台のGCMを「ひとつのギガキャスト部品」専用にして効率よく大量生産するとなると、それを採用する車種は設計を共通化しなければならない。なるべく設計の自由度を奪わないようギガキャスト部分を設計する必要がある。
ギガキャストでクルマは軽くできるか?
ここまでの問題を整理する。
設備投資面でギガキャストを導入すべきかどうか迷う場合、コストの問題さえ片付けばGOできる。「長い目で見ればGCMを導入するほうが製造コストは安くなる」ことがわかればいい。ギガキャストを採用すれば部品点数は確実に減る。テスラは70部品を2部品に統合した。当然、スポット溶接の点数も減る。この点は圧倒的に有利だ。
いっぽう、商品展開に悪影響を与えない、設計の自由度を奪わないようにギガキャストを利用法する場合は、プラットフォーム設計も含めた商品戦略との連携が必須になる。どのようにギガキャスト部品の採用を進め、どこまで鋼板プレス&溶接と置き換えるか、10年程度先までのロードマップを描く必要がある。
次に3つめの問題。果たしてギガキャスト部品を使えば車両重量を軽くできるのか、という点だ。
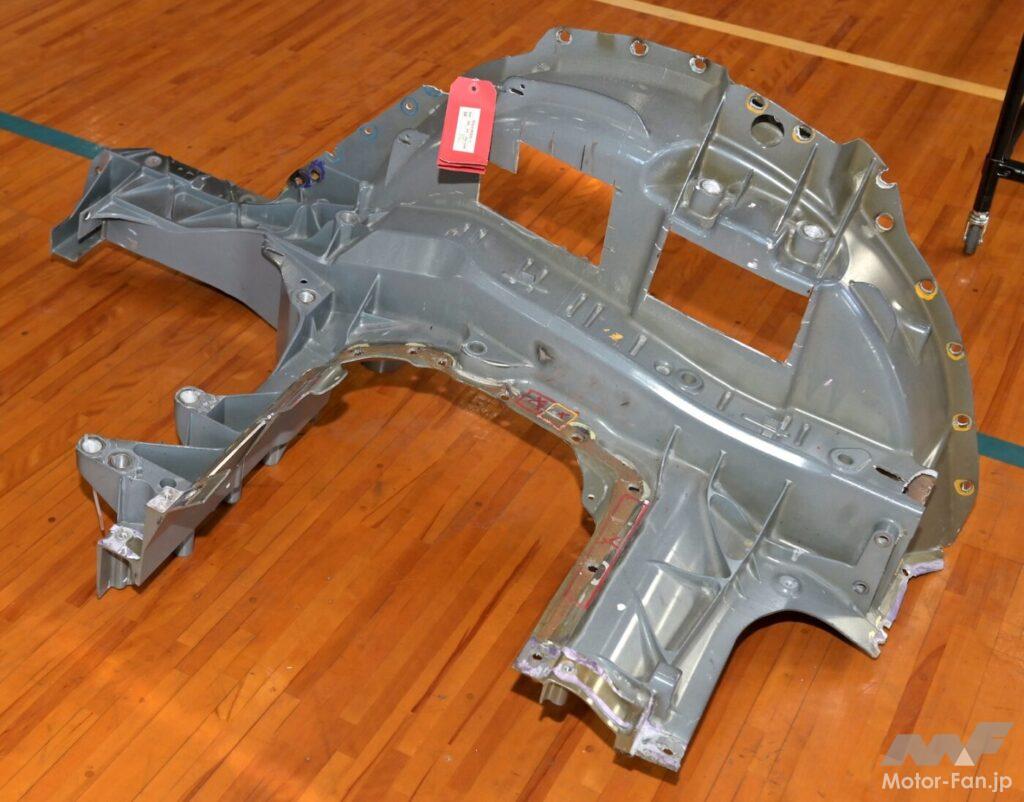
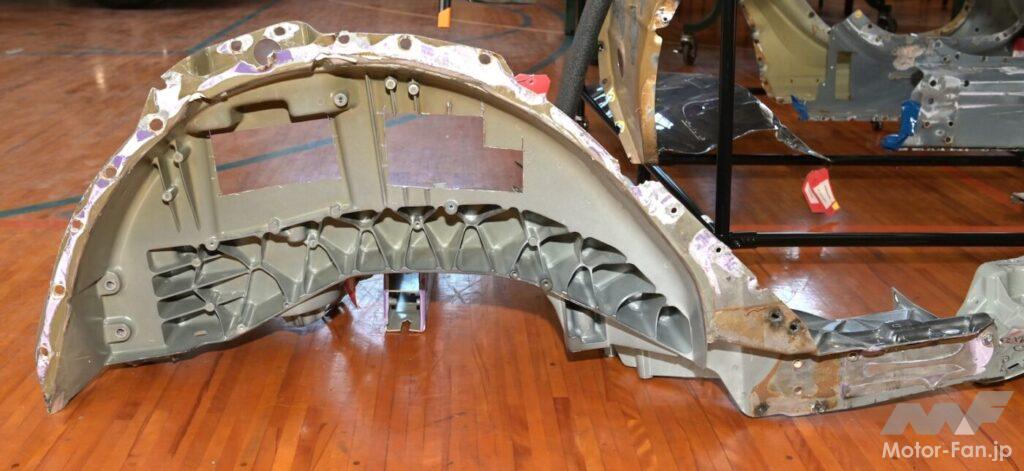
テスラ「モデルY」に使われた左右2分割のリヤサスペンションおよびリヤサイドメンバーについてはESP(エンジニアリング・サービス・プロバイダー=開発支援会社)やリバースエンジニアリング企業、素材メーカーなどが分解調査を行なった。その結果、プレス鋼板を溶接した構造より「モデルY」のギガキャストのほうが重たかった。
私が実際に見た「モデルY」のギガキャスト部品は、厚いところでは3mm以上の肉厚があった。ボディ剛性は断面積に比例して高くなるから、鋼材使用で設計して1.6mm厚が必要な部分に3mmのアルミ鋳物を使えば剛性は極めて高くなる。しかしこれは過剰性能である。
テスラが最初に導入した型締力5500トンのGCMでは「細かい部分の薄肉化が難しい」と素材メーカーで聞いた。「鋼材とアルミ合金の継ぎ接ぎではなく、最初からアルミ合金鋳物と押出材を使う前提でボディを設計すれば事情は変わる」とは、日系OEMのコメントだ。
中国・吉利汽車や小鵬汽車は「ギガキャスト専用設計にすれば鋼材で作るよりも15%程度軽くできる」と言う。たしかに素材スペックをもとに「剛性値同等」という条件で計算すれば、プレス鋼板の溶接で作るよりも大きなアルミ合金鋳物のほうが軽くできる。
衝突安全性の確保が難しい?
一方、日系OEMのボディ開発アンジニア諸氏はこう言う。
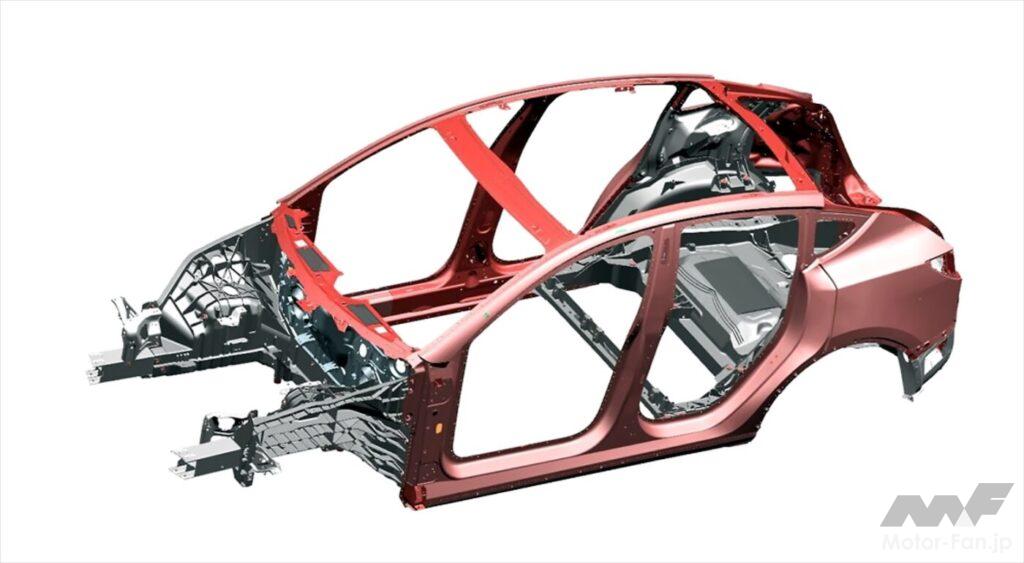
「鋳物は品質管理が難しい。エンジンのように内部で発生する力に対応するだけなら問題ないが、衝突という外からの力に対しては未知の部分がある」
「鋼に比べてアルミは比重が3分の1なので、うまく使えば軽量化のポテンシャルがある有益な材料だが、衝突安全性を鋼と同等に持っていくには形状の工夫だけでは難しい」と言う。
以上が3つめの「迷い」だ。4つめの迷いは衝突安全性への疑念だ。
ある欧州ESPはこう言った。
「衝突エネルギーを吸収する骨格部分にギガキャストを採用するのは難しい。衝突安全性の法規試験だけ満足させるのであれば、車体の潰れ方は問題にならない。ダミー(人体を模したデータ計測用の人形)が受ける傷害値が基準以下なら法規には適合できる。しかし、リアルワールドで起きる事故では、車体の潰れそのものが問題になる。乗員の生存空間を確保できるかどうか、だ」
プレス鋼板で作ったボディは、大きな衝撃でぐしゃっと「潰れる」。しかしアルミ鋳物は衝突の衝撃でポキンと割れたり粉々に粉砕されたりする。テスラはマイナーチェンジ版のモデルYで車体前部(フロントサイドメンバーとストラットハウジング周辺)にギガキャストを採用したが、米国のFMVSS(連邦自動車安全基準)にはない方法での試験でモデルYの車体前部が粉々になった。
偶然の一致かもしれないが、FMVSSには規定のないスモールオフセット試験(車幅に対して運転席側の10〜25%だけをぶつける)の動画が拡散した後でVW(フォルクスワーゲン)がギガキャスト部品の採用を白紙撤回した。さらにテスラは、米IIHS(保険業組合)が実施する法規外のボランティア試験にマイナーチェンジ後のモデルYを提供していない。マイナーチェンジ前のモデルYは提供していた。
ある欧州OEMのボディ設計担当者は「衝突の衝撃を吸収するフロントサイドメンバーにギガキャスト部品を使うと、とくにスモールオフセット試験では被害予測が難しい。設計どおりに壊れてくれない危険性があることは我われも認識している」と語った。
日本勢は迷走中か
ギガキャスト部品を採用すべきかどうか……日系OEMの「迷い」を整理すると、設備投資、商品戦略との整合制、軽量化効果、衝突安全性の4点に集約される。さらに付け加えるなら、これにアルミという素材のコストが乗る。企業経営の視点では、コストがもっとも大きな懸念だろう。
欧州に目を向けると、メルセデス・ベンツはすでに「ほぼギガキャスト」と呼べる鋳物部品を「EQS」のボディ後方に使っている。ボディ前方にはアルミ合金押出材を使っている。BMWやVWグループは「ギガ」ほど大きくない鋳物はすでに10年以上前から使っているが、ギガキャストはいまのところ将来計画には入りそうにない。
中国のOEMは一気にギガキャスト採用へと動いている。これはテスラの影響が大きい。中国国内では現在すでに20基程度のGCMが稼働していると言われるが、リョービの調べでは今後3年程度で80ほどまでGCMが増える見通しだと言う。2030年代初頭には100を超えるかもしれない。
ギガキャストを採用するかどうかの判断は、いまのところ世界的に見るとテスラと中国勢が積極派だ。しかし、けしてこれが主流派ではない。何事にもセオリー重視の欧州勢は慎重派もしくは懐疑派で、「高くても買ってもらえる」メルセデス・ベンツのようなブランド勢は少々積極派に近い。それでもボディ前側はストラットハウジングにとどめており、衝突の衝撃を受け止めるフロントサイドメンバーには使っていない。
同じドイツブランドでもBMWは慎重派だ。以前、BMWのエンジニアは「左右のサスペンションを連結するようなアルミ合金鋳物の使い方ではBMWらしい乗り味にならない」と言っていた。「アルミは乗り味も硬い」と。
日本勢は慎重派と言うよりは迷走中だ。果たして周囲に流されない判断ができるだろうか。「よそがやっている」で追従するとロクなことはない。
かつ日本の自動車産業は、DOHCエンジンを大衆化し、4WS(4輪操舵)を真っ先に実用化し、クロスオーバーSUVというカテゴリーを創り出し、HEV(ハイブリッド車)を産んだ。これらはすべて20世紀の実績だ。21世紀に入ってからは量産FCEV(燃料電池電気自動車)を世に送り出した。しかし、その創造力は近年、すっかり衰えてしまった。
軽くて、丈夫で、衝突安全性が高く、部品点数が少なく、安く作れる。こういうクルマを産み出すためのひとつの手段としてギガキャストが有効なら、やらない手はない。そこに向けた「解」を見つけるべきだ。ただし、テスラの真似は見たくない。これからやるのであれば強烈なオリジナリティが欲しい。
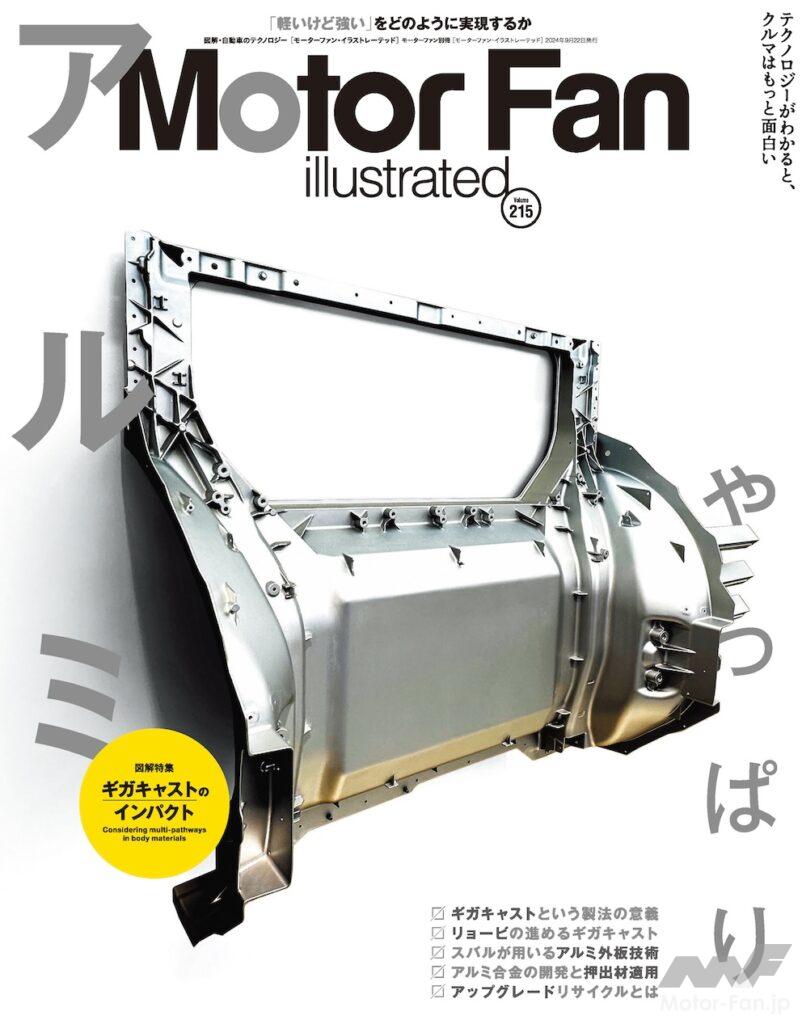