風力発電の故障率は25%
「現在、風力発電用風車の故障率は25%程度だ。故障は多岐におよぶ。いちばん厄介なのはローター(プロペラ)の回転部分にあるベアリング(軸受け)だ。洋上風車の場合、故障すると船で故障した風車まで出かけ、故障箇所を調べ、交換用部品を発注する。部品が届く前に足場を作り、修理作業の準備をするのだが、高所の狭い場所で修理作業は非常に厳しい。ベアリング交換となると、下手すると2年以上かかる」
これは洋上風車のメンテナンスを請け負う欧州企業を取材したときのコメントだ。ある大学の研究チームにカメラマンとして同行しデンマークとスウェーデンを隔てるエーレ海峡に設置された風車群と製造メーカー、部品のサプライヤー(供給業者)およびメンテナンス企業を訪問した。そのなかの一社である。
エーレ海峡を渡る列車の車窓からは海上に並ぶ風車が見えた。日本にはない、非常に珍しい光景だった。残念ながら当時の写真の使用許可を得られず、無断使用しないという契約なので、写真を掲載できない。
エーレ海峡は、それほど波は高くなかった。デンマークのヘルシンオアから対岸のスウェーデンのヘルシンボリ(大昔は同じ都市だったので綴りは同じで読み方だけが違う)へフェリーで渡る際も船は揺れなかった。国際フェリーのため、船が岸壁を離れた瞬間に免税品売店に人が押し寄せ、たばこがあっという間に売り切れになるのが印象的だった。
イギリスでもスペインでも、あるいはバルト海沿岸でも、洋上風車を建てるのは難しくない。欧州大陸の沿岸には日本のような台風は発生しない。いっぽう、日本の海岸線は長いが、台風が勢力を保ったまま通過しそうな地域以外で安定して強風が吹く地域を選ぶとなると、選択肢は狭くなる。あるいは平均風速57m/秒の大型台風にも耐えられる「クラスT」の洋上風車を選ぶか、である。
日本にも風力発電設備のメンテナンスについてのデータがある。平成29年度(2017年)に経済産業省商務情報政策局産業保安グループ電力安全課がコンサルティング会社・デロイトトーマツに委託した調査だ。その調査報告のなかから故障についてのデータをいくつか紹介する。
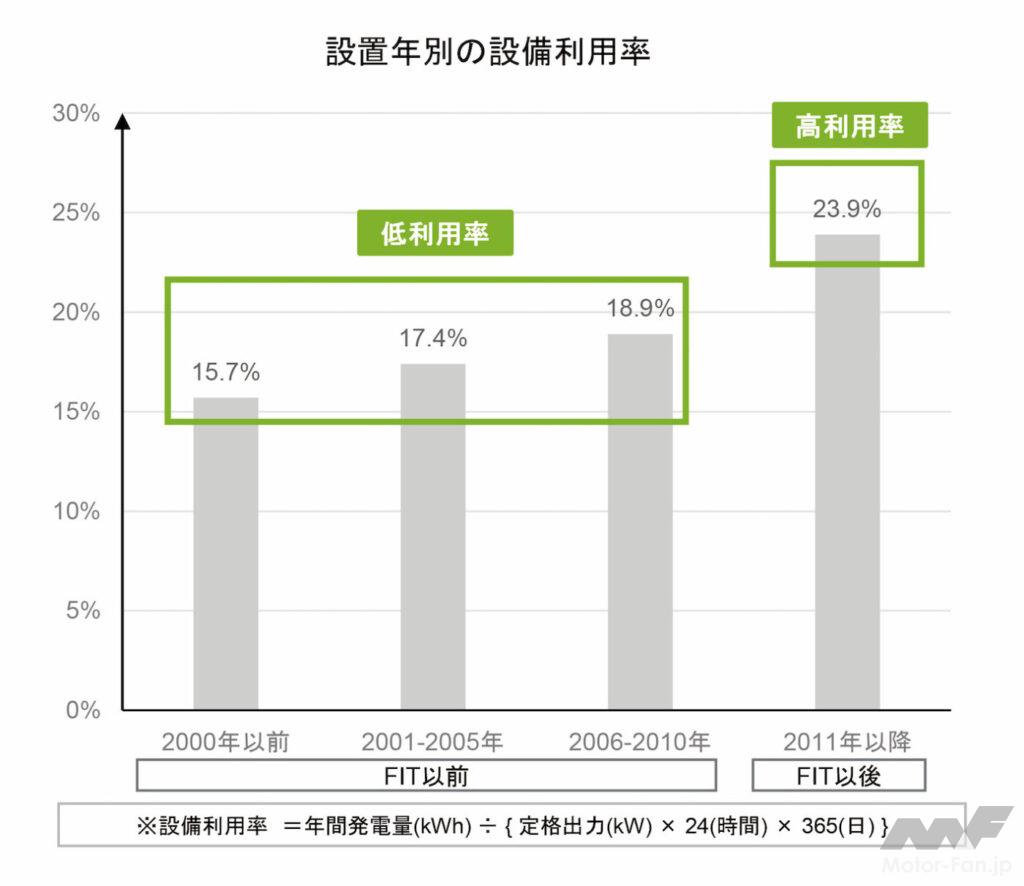
まず、設備利用率の例を示した【グラフ1】。これは365日24時間のなかで「どれくらいの時間にわたって発電しているか」を示す比率だ。1時間に500kW(キロワット)を発電する能力がある風車なら、365日24時間フルに発電すれば500kW×24×365=43.8万kWになる。これが設備利用率100%の状態である。稼働率とは計算方法が異なる。
日本がFIT(固定価格買い取り制度)を導入した2012年以降は「どんどん発電して売電すれば利益が出る」ことから太陽光も風力も全国でほぼフル稼働になり、風力発電は高スペックの大型風車へと主力が移った。
一定以上の強さの風が吹けば、その風車が備えている発電機の定格出力に達する。多少風が弱い場合は、プロペラのピッチ(迎え角)を操作して発電効率のよい状態にもっていく。とはいえ、日本にはつねに強い風が吹いているエリアはあまり存在しない。設備利用率は高くても23.9%にとどまった。
設備利用率が低かった最大の原因は「故障・不具合の発生」で、これが圧倒的に多かった。2番目は「想定していたほど風が吹かなかった」、3番目は「台風や強風のため風車の停止時間が想定以上に長かった」である。
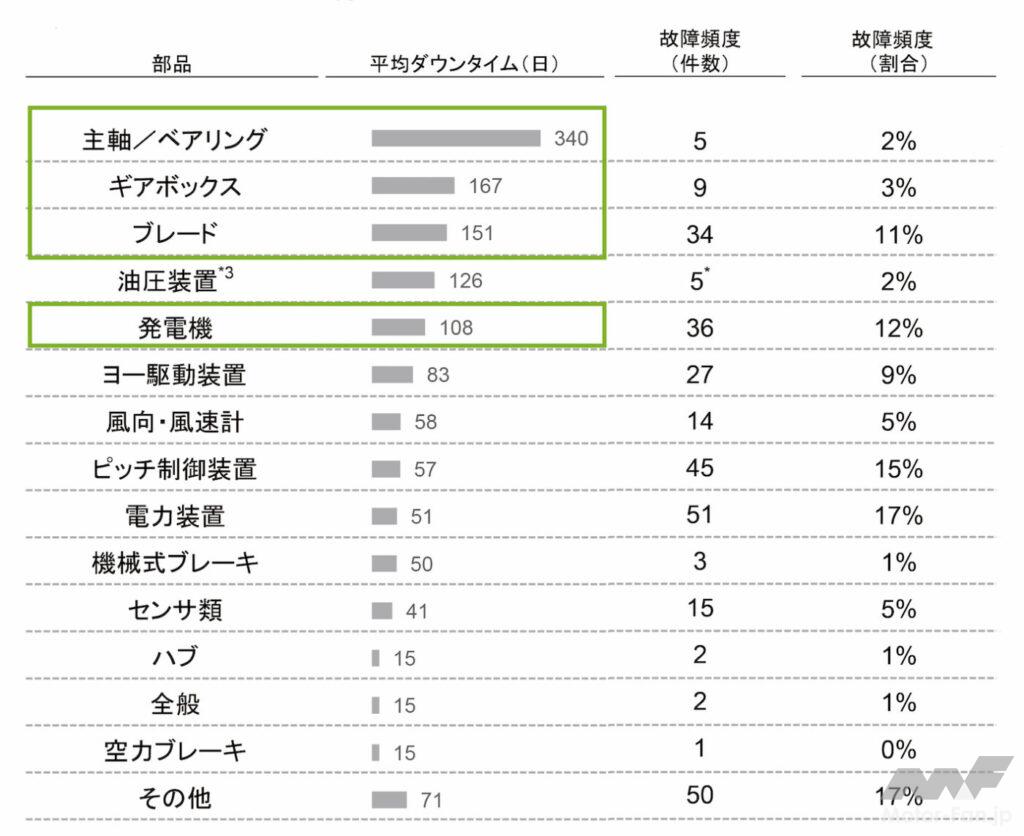
いっぽう、故障・不具合によって発生したダウンタイム、つまり「風車が止まっていた時間」を故障部位別に見た【グラフ2】では、風車の主軸とその軸受け(ベアリング)が故障すると、その修理のために平均340日も風車を止めていることがわかる。
ベアリングの故障頻度は2%だが、ひとたび故障すると復旧には長い時間がかかる。日本では修理に2年以上かかった例がある。前出の欧州のメンテナンス会社でも、ベアリング交換には「下手すると2年以上かかる」と言っていた。日本も同様である。
ベアリングの故障は、自動車ではほとんど考えられないが、風車の場合は温度変化による結露が最大の原因だという。つねに風車が回っていて潤滑油が供給され続けていれば問題はないが、止まっている間に結露が起きると故障につながるケースが多いそうだ。メンテナンス会社は以下のように言っていた。
「20MWh級の巨大な風車となると、プロペラブレードの主軸を支えているベアリングには大きな負荷がかかる。たとえ風車メーカーが20年の寿命を保証しても、本来はこまめなメンテナンスが必要であり、部品によっては2年以下で壊れる。プロペラのピッチを変える歯車はサイズが小さいので本題ないが、ベアリングは難しい」
こういう話もあった。
「公共事業には、良いものに対して正当な対価を支払うという発想がない。競争入札の場合は安ければいい。カタログスペックが良くて安いものが会議だけで選ばれる。多くの場合、その選定に関わったスタッフは人事異動で配置展転換になり、20年経ったら誰も残っていない」
実際、現在の日本国内では「故障率が25%を超えている」という話を聞いた。しかし、海外製風車の場合は部品を取り寄せるのに時間がかかり、ダウンタイムは自然と長くなる。「部品をストックしておくメンテナンス業者はほとんどない」とも聞いた。前編で取り上げたイギリスとデンマークの例と同様、日本が洋上風の建設を本格化させた場合、こうした問題に直面するのは間違いないだろう。
日本での経産省調査の報告書にも、交換した部品の値段が書かれていた。風車のブレードは約5,000万円、ベアリングは約4,000万円、風車の回転を増速し発電機に送るためのギヤボックスは約3,500万円、発電機は約3,000万円‥‥である。壊れなければいいが、機械は必ず壊れる。部品ごとの故障頻度は【グラフ2】に示したとおりだ。
再エネ発電設備は、使い続ければどんどん発電コストが下がる。これが正しいのなら大歓迎なのだが、欧州でも、陸上風車時代の日本でも、風車はよくこわれる。その事実がデータとして残っている。前編では発電コストがどれくらい上昇したかのグラフも示したが、大型洋上風車は建設した段階ですでに発電コストは小型陸上風車の約4倍である。同時に、大型洋上風車の発電コストは「9年後に約2倍」となる予測だ。
なぜかこうしたデータは世の中にほとんど出て来ない。