目次
3D図面、AR(拡張現実)の技術
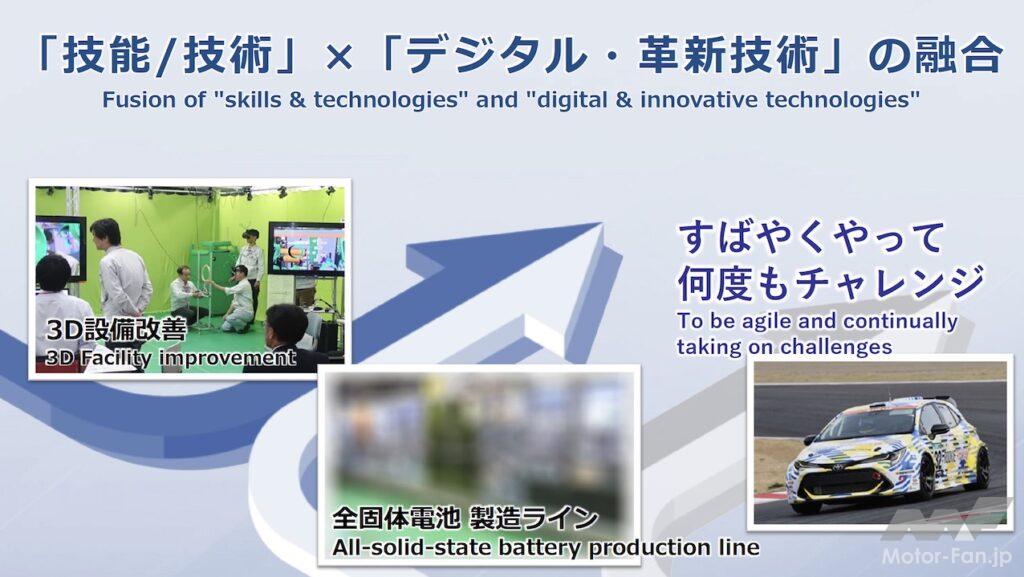
世の中にない新しい製品を作るには、新しい製造設備が要る。その前に作り方だ。例えば、新しいモーターの効率を高くするためにコイル線の形状を変えるとする。その新しいコイルをきれいに並べるにはどうすればいいか。まずはポンチ絵(下書き)を書いてアイデアを共有し、手治具と呼ぶ手作りの工作物をつくって機能を確認する。
つくり方のアイデアが固まったら、そのアイデアを量産する設備の設計に落とし込む。設備を設計し、設計した部品を加工して組み付け、最終的には量産工場に導入する。
従来から、加工や組付、確認会で「加工できない」「正しく動かない」「作業しにくい」といったやり直し案件が生じないよう、設計の段階でモノづくりの現場の人たちと意見交換を行なってはいた。だが実際には多くのやり直しが生じ、製作リードタイムの多くの部分を占めていたという。
やり直しが発生していた理由は、設計図が2D(二次元=平面)だったからだと、設計側は分析している。二次元の設計図では、設計者の意図を読み取ることが難しく、的を射た改善点が出にくい(出しにくい)のだ。そのため、結局のところは現物を見ながら改善点を出していくことになり、これがやり直しにつながっていた。
そこでデジタルである。現在は3D(三次元=立体)で設計しているので、部品を加工する人や設備を組み付ける人、そして設備を使う人といった現場のメンバーが実物の様子を把握しやすい。その特徴を生かして設計段階で仕事の前出しと同期化を行ない、「やり直しゼロ」を目指して設備づくりに取り組んでいる。
それだけではない。3Dデータを活用し、部品を加工するプログラムを自動で作成したり、組付手順を前もって確認したりするようになった。組付の際は前もってどの順番で組めばいいかアニメーションで表示させ、それを見ながら確認を行ない、やり直しゼロを目指している。最終確認会では配線の3Dモデルと実際の配線を画面上で重ねて確認する。ポケモンGOをイメージするとわかりやすいが、AR(拡張現実)の技術を使ったものだ。
設計段階で前出し・同期化を行ない、製作段階で3Dデータを使ったさまざまな効率化を行なうことにより、やり直し件数は10分の1、リードタイムは2分の1、設備費は4分の3を実現したという。
デジタルを活用した「やり直し削減」の事例を体験した。モーターの製造設備はコイル線を切断すると刃物が摩耗する。定期的な刃物ユニットの交換が欠かせないが、どうやって作業者の負担を軽くするか、関連するメンバーが集まり、配線・配管が邪魔にならないか、手が入る隙間があるかなど、デジタルで確認したという。

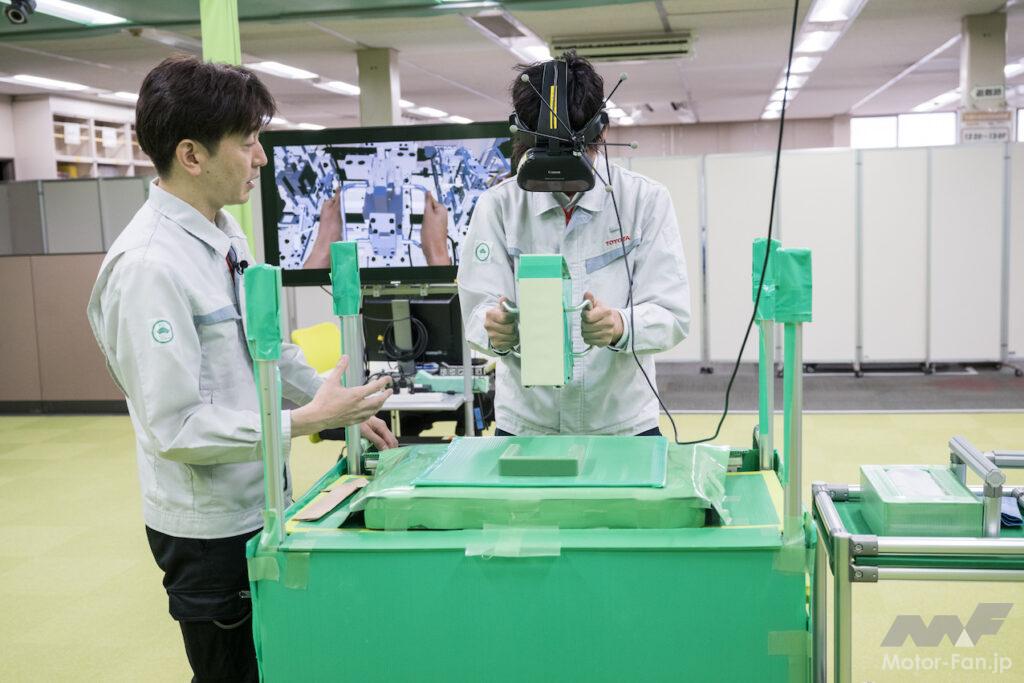
「1/1D R」と記してある大型のモニター(手作りだ)には、実物大の設備が裏から投影されている(表から投影すると作業者が影を作ってしまうので、これを避けるため)。実物大とはいえ奥行き感をつかむのは難しく、VRゴーグルを使う検討を取り入れた。筆者が体験したのはこれだ。
ゴーグルを装着した筆者は、コイル線を切断する設備の前にいる。バーチャルの設備に食い込まないよう、設備を模した台があり、実際の設備と同じ縁が再現してある。ゴーグルの中で見えている設備の質感と、手に触れた縁の触感がピッタリ合い、思わず「おぉ!」と感嘆の声を漏らしてしまった。手を伸ばすと刃物ユニットがある。取っ手は実物だが、刃物ユニットは実際には四角い箱だ。ゴーグルの中ではリアルであり、約8kgの重さも再現している。
従来は刃物ユニットをその場で持ち上げ、手前に引き出していたという。使う人の意見を取り入れ、刃物ユニットを手前にスライドさせてから持ち上げるようにした。重さも含めて体験してみると、改善案のほうが圧倒的に負担は少ない。「使う人を楽にしてあげたい」と説明者は語る。
デジタルは設備単体だけでなく、工場全体で活用
デジタルは設備単体だけでなく、工場全体で活用している。安全なラインをつくるためだ。3Dスキャナーで工場全体を測定。見通しが利くよう、設備類の高さを1500mmに抑えているが、それが狙いどおりにできているかどうか確認しているという。
調整中に設備を動かそうとしたら正しく動かないといった事例に対しても、デジタルで解決した。設備は操作盤で操作する。内部には制御機器があり、動作プログラムが入っている。その動作プログラムの信号で設備は動くが、動きの組み合わせは約6000通り。正しく動かすにはプログラムの行数は8万行に達するという。どこかに見落としがあり、いざ動かそうと思ったら動かず、修正~また動かない~再度修正の繰り返しだった。
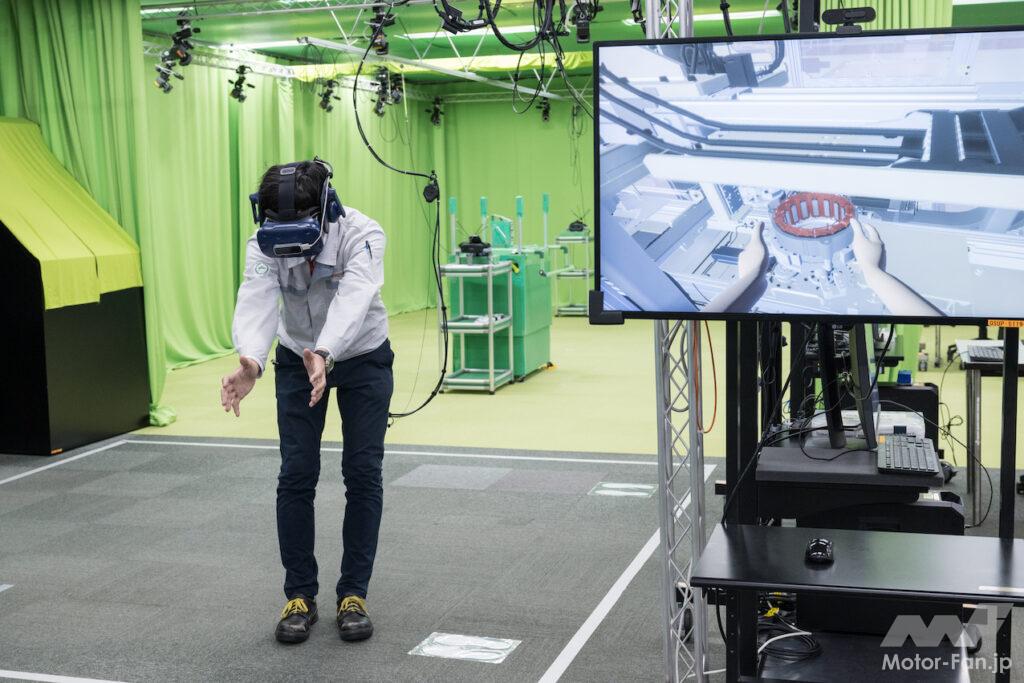
実物でこれをやっては手間がかかるので、デジタル上で確認~修正を行なうのが現在だ。ワークショップではモーターのコイル線をローターコアに組み付けていく工程を例に説明があった。プログラムが不完全な状態だと、組み付け中に止まってしまったり、組み付けたのにワーク(作業対象の部品)が出ていかなかったりする。これを前がかりで修正した。実機だと物理的な損害が生じるが、デジタルならその心配もなく、多くの面で効率的だ。事前にデジタルデータで設備の構造を確認することができるので、メンテナンス側の視点で役立つことも多いし、操作トレーニングにも活用しているという。
デジタルで設備が操作できるようになったので、海外のメンバーはわざわざ日本に来なくても、現地で設備の動きを確認できるようになった。これも、デジタル化の恩恵だ。従来は設備を使う人と保全する人が実物を使って操作手順を覚える必要があったが、それがリモートでできるようになった。
デジタルによる設備の検討は2018年頃から始めており、デジタルで設備の動作プログラムを確認するリアルシミュレータは2014年頃から導入しているという。リアルシミュレータは貞宝工場に16台あり、動作プログラムの作り込みを行なっている。
デジタル技術を活用した設備製作や動作プログラムの確認はトヨタグループをはじめ協力メーカーに広げている。グループ全体で競争力を最大化するためだ。過去5年間で社内外約4000名にデジタル技術を使った設備づくりのうれしさを伝え、仲間づくりを拡大中。説明会を開催するだけでなく、設備メーカーに出向いて状況を把握し、解決案の提案を行なってもいるという。
「そうはいってもまだ、現物でのやり直しは多い」のが実状。デジタルを活用したモノづくりで、トヨタグループだけでなく、「世の中のモノづくりに貢献したい」と大きな目標を掲げる。