目次
エアレスで塗装するとなにがいいのか?
自動車の塗装工程は、生産ラインのなかでもっとも多くのCO₂を排出する工程だ。その塗装工程のなかでも塗装ブースでスプレー塗装する工程のCO₂排出が多い。
そこで、トヨタが開発したのは「高塗着エアレス塗装」という新しい塗装技術である。
我々が案内されたのは、自動車の塗装の評価を行なう実験場。実験場とはいえ、実際の生産ラインの塗装工程で使っているものと同じスケールの設備が導入されている。
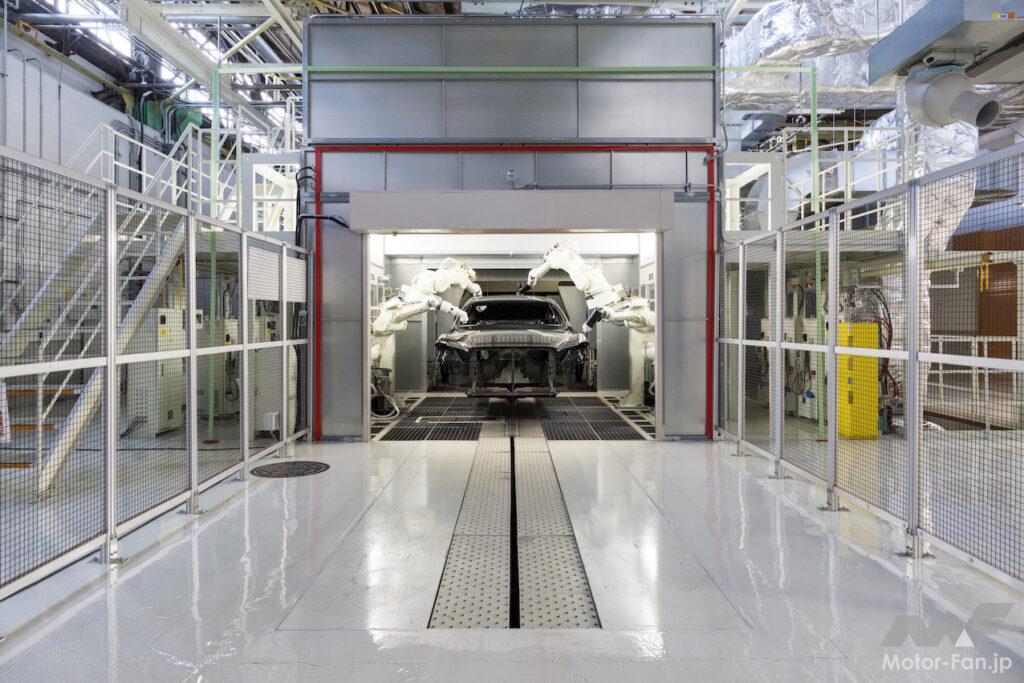
塗装ブースには車両もボディが置かれていて、その左右に塗料を吐出するロボットが設置されていた。向かって左側が従来の塗装(スプレー塗装)、右側が高塗着エアレス塗装のロボットだ。
まずは従来の塗装。
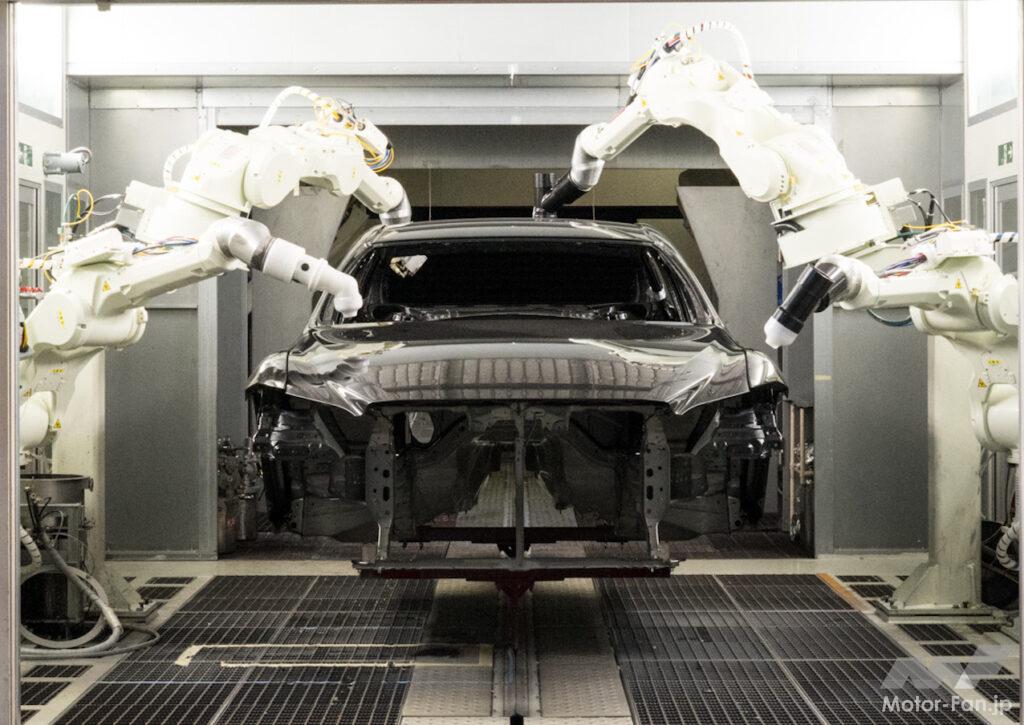
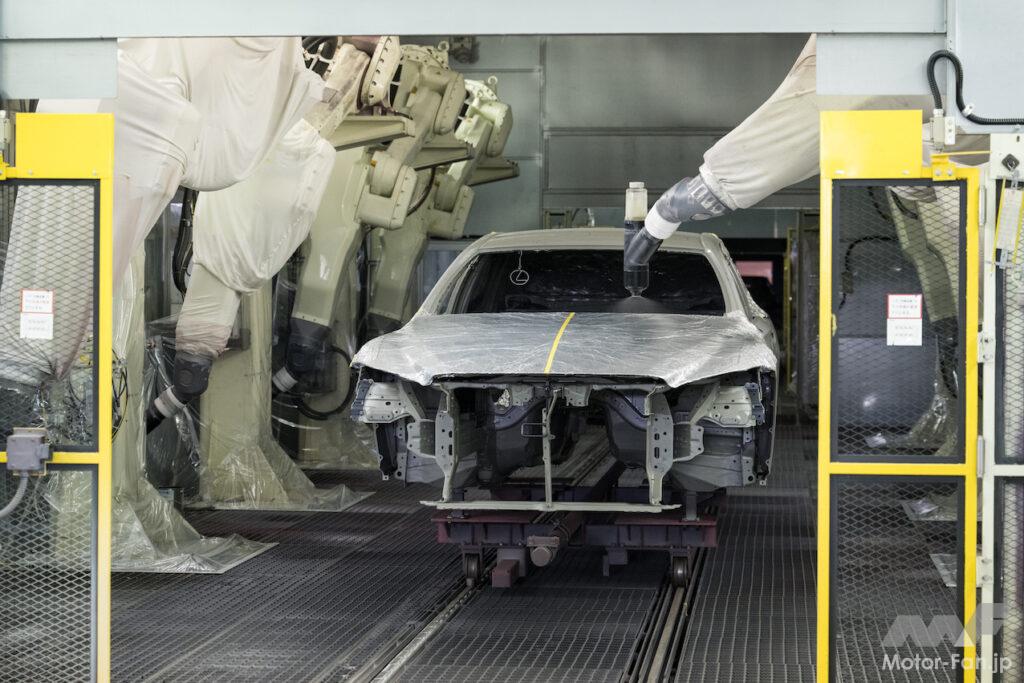
従来はエアを使ったスプレー塗装をしていた。エアを使っているので車両に付着しなかった塗料ミストは飛散し、塗装設備に付着、また床下へ溜まっていく。そのために定期的な清掃が必要だった。実際に車両に付着するのは吐出した塗料の70%だ(つまり30%はロスしていた)。
今回開発した技術、高塗着エアレス塗装技術は、エアの代わりに静電気の力で塗装する。静電気を使うので車両に吸い付くような塗装が実現できる。吐出した塗料のほとんどが車両に付着。じつに95%は車両に付着できるという。塗料ミストを大幅に削減できる。
ここだけでCO₂排出量を従来から7%削減できたという。
静電気を利用した塗装機について、もう少し詳しく説明してもらった。右側のロボットの先端に円筒形のヘッドが装着されている。
- このヘッドが回転する。
- 回転している間に中から塗料が吐出される。
- 吐出した塗料は円筒形のヘッドの内側に濡れ広がるようにして広がっていく。
- ヘッドの先端には特殊な形状の溝が彫ってある。溝ごとに塗料が濡れ広がって先端の部分でマイナスの電荷を掛けることでヘッドの先端にマイナスの電荷が溜まっていく。
- このマイナスの電荷、マイナスとマイナスの電荷の斥力が塗料をちぎるような働きの力を与えて、小さな粒子となって飛ぶ。
- 一方の塗装されるボディはアースがとってあって、マイナス電荷との電位差を利用してマイナスに帯電した小さな塗料の粒子が電位差にともなって、車両に吸い付くように飛んでいき、車両に付着する。
というような原理だと説明された。いわゆるクーロン力を利用しているのだろう(理解が浅いのは筆者の責任で説明した方は丁寧に説いてくださった)。
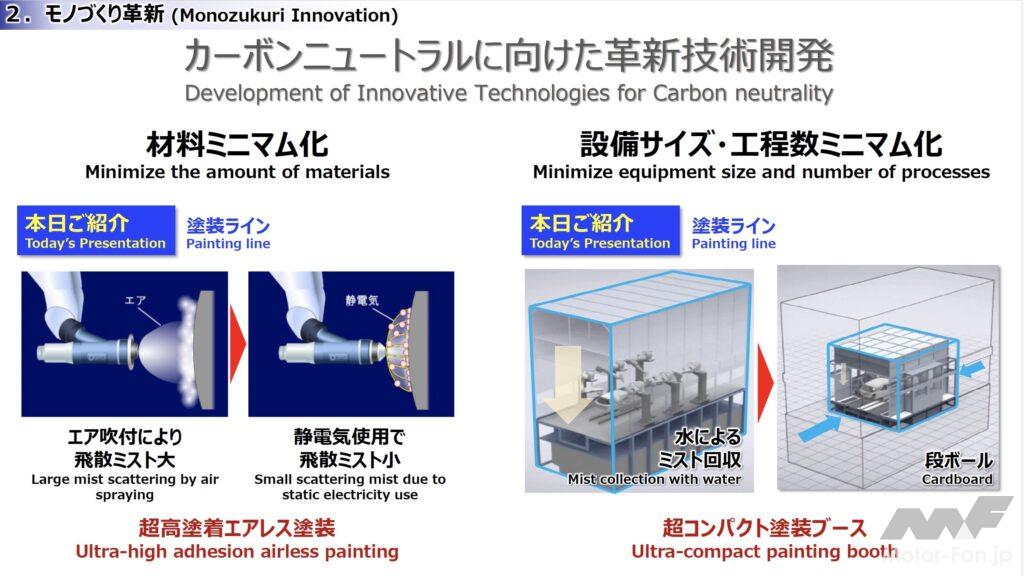
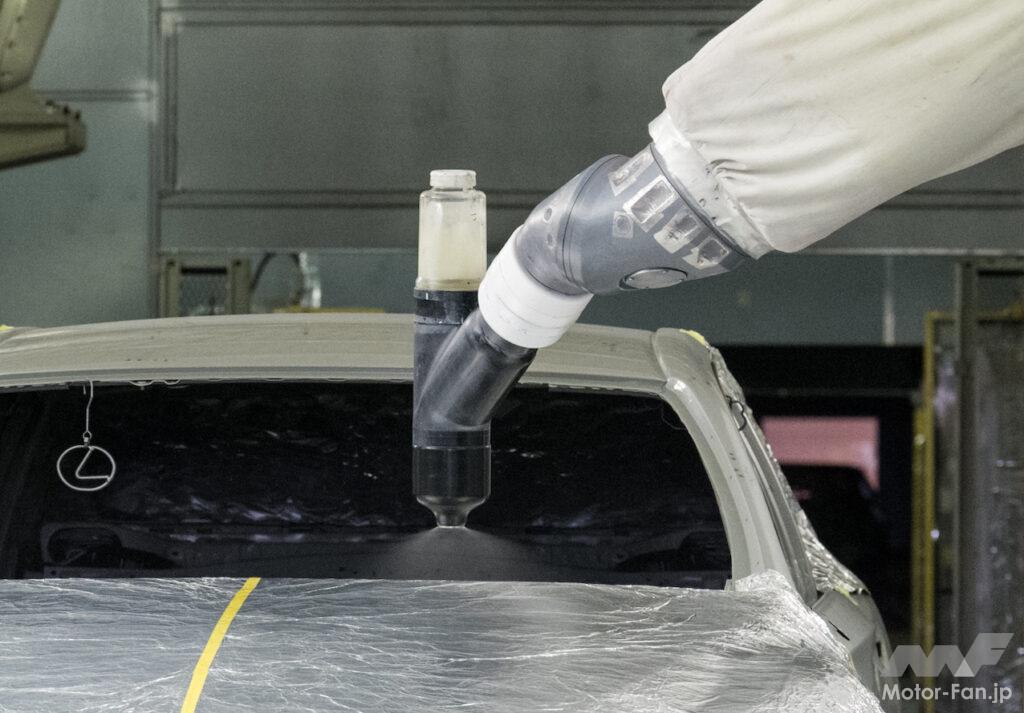
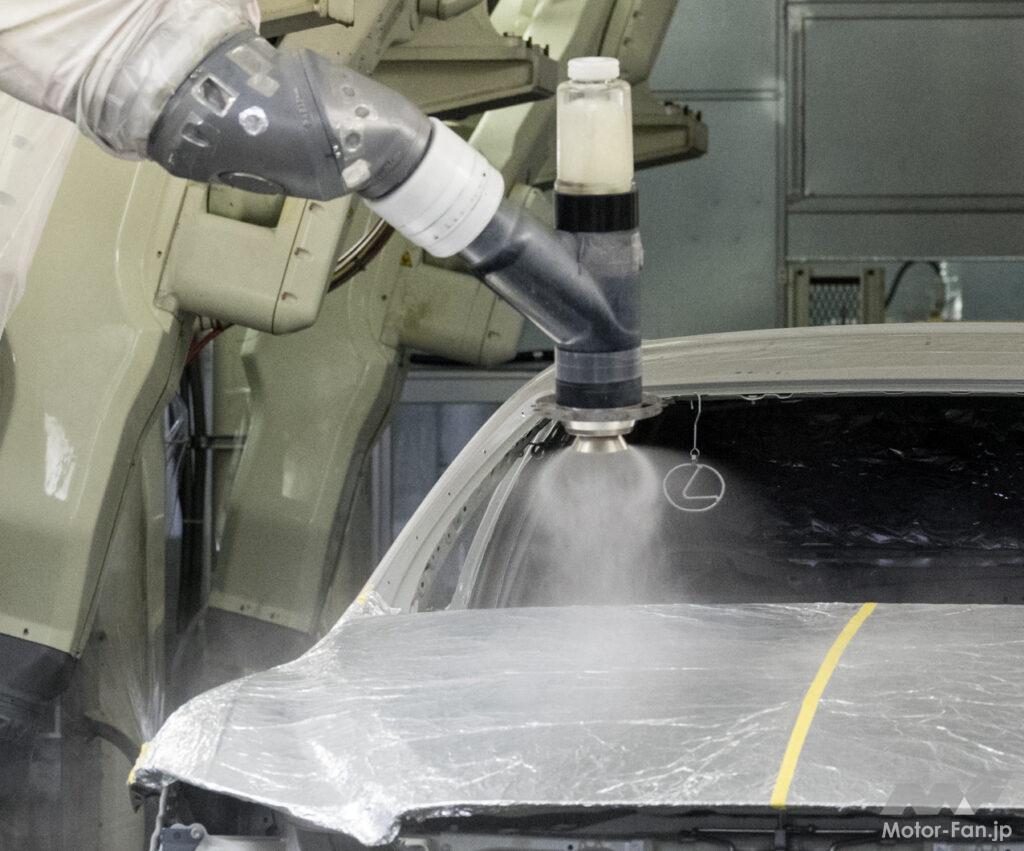
どうやら、回転ヘッドの内側に切った溝の形状に秘密があるようで、初期の試作から完成まで84回も試作をしたのだという。
ちなみに塗料自体は、従来のものとほぼ同じ。塗装品質は従来方法と同等以上だという。
この高塗着エアレス塗装は。2017年から採用が始まっていて、すでに6割ほどが導入済みだ。
段ボールを使ったフィルターを採用
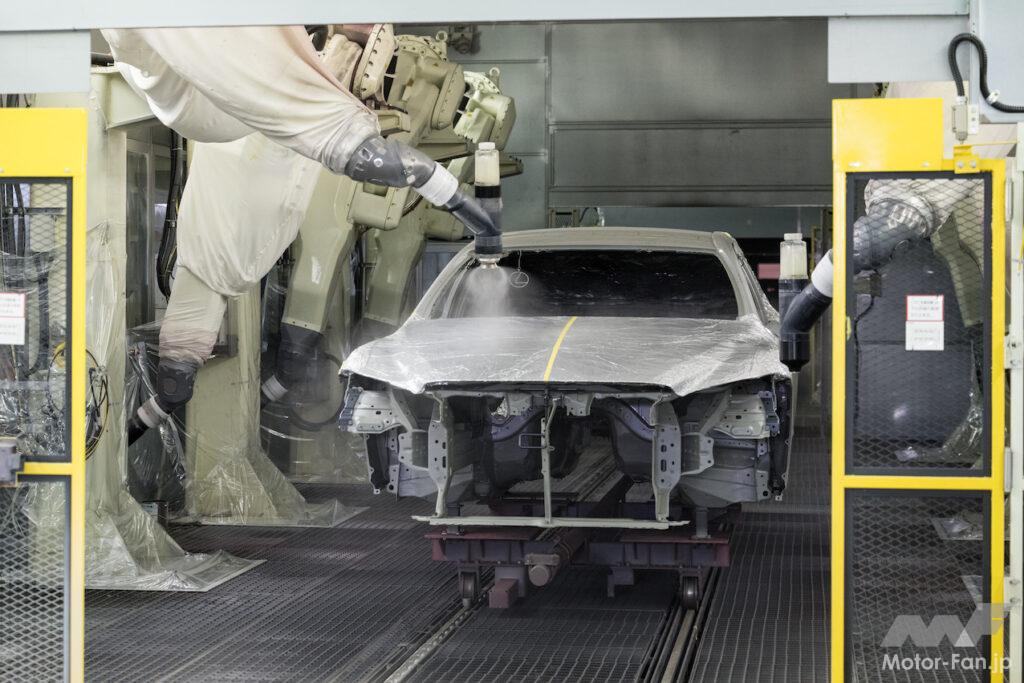
ふたつ目の技術革新は段ボールドライフィルターの採用だ。
従来の塗装では付着しなかった塗料を、塗装ブースの下にある水の中に溶け込ませて回収。その水を溜めておく設備、水を処理する設備が必要だった。ここで大きなエネルギーが必要とされた。
エアレス塗装を導入することで飛散する塗料ミストが大幅に減ったので、水を使った設備の代わりに特殊構造の段ボールを使った高効率な捕集システムを導入した。既設の水を使った設備を改造して特殊構造の段ボールを設置することで、付着しなかった塗料ミストを段ボールの中に捕集するわけだ。
段ボールだと水を使わないので大がかりな捕集システムやその水を処理するための設備が不要となる。段ボールドライフィルターを導入することで、塗装工程のCO₂排出量を約12%削減できた。
塗装ブース内は温度・湿度を年間通して一定にする必要がある。そのための巨大なエアコン設備で膨大なエネルギーが消費される。従来の工程だと1日1ラインあたりドーム球場数個分のエネルギーが使われていた。
従来の塗装工程のスペースは、下(塗装ミストを処理するための水の設備がある)と中(塗装ブース)と上(エアコン設備がある)で高さは10m以上もある大きな設備だ。またライン長も長い。
従来のスプレー塗装では、塗料ミストが飛散するので、ロボットとロボットの間隔を2.5mほど離して設置する必要があった。間隔が広いために大きなロボットを使用する必要があった。ロボット間隔が広いので、ブースも大きく工程長も長い。温湿度を調整すべきエリアも非常に大きい。そのためにエアコン設備も大きくなり膨大なエネルギーが必要になる。
CO₂削減にはブースの大きさをコンパクトにするのが大きなポイントになる。
エアレス塗装機を使うと、ロボットとロボットの間隔は2mから75cmまで短くなる。ロボットもコンパクトになり、ロボットと車両の距離も近くなった。塗装ブースの体積も約6割(!)も小さくなったという。
高塗着エアレス塗装と段ボールドライフィルター、コンパクトブースの3つの革新技術で塗装工程のCO₂排出量を36%削減できたのだ。
コンパクトブースは、設備の入れ替えや新ライン創設時に導入しているという。CO₂削減、コストも下がる、そして塗装品質は従来同等以上。自動車の塗装技術も見えないところで大きく進化していたのである。