目次
異なるシルエット、パワートレーンの多車種を混流生産するノウハウ
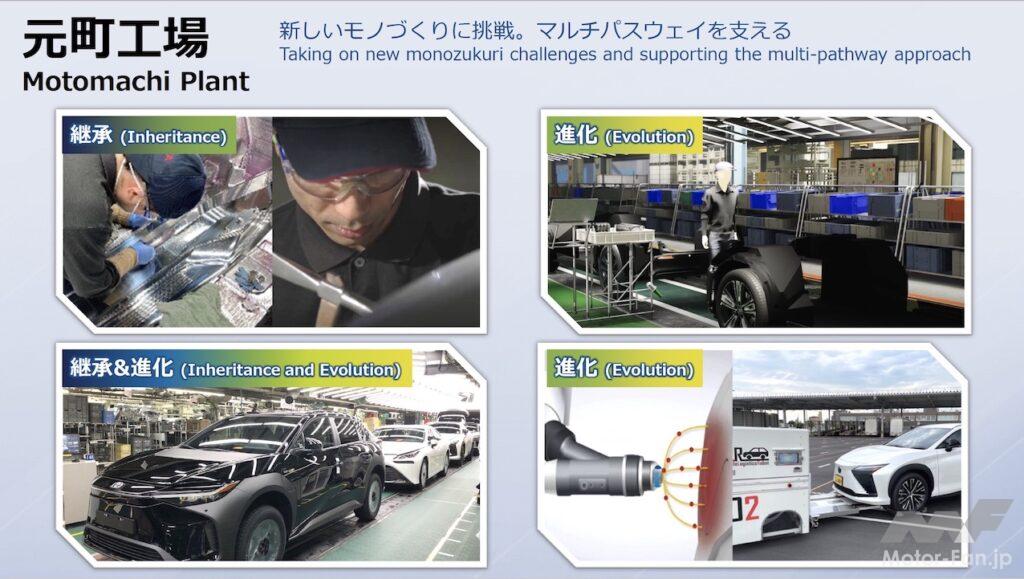
今回のトヨタ・モノづくりワークショップのテーマは「人中心のモノづくりで、工場の景色を変え、クルマの未来を変えていく」というものだった。報道陣に公開されたのは、元町工場だ。
元町工場は1959年に生産を開始した”由緒ある”工場で後輪駆動のセダンを中心に生産してきた。現在は、C+pod、センチュリー、GRシリーズなども生産している。見せてもらったのは、9車種の生産を行なっている第一組立ラインだ。
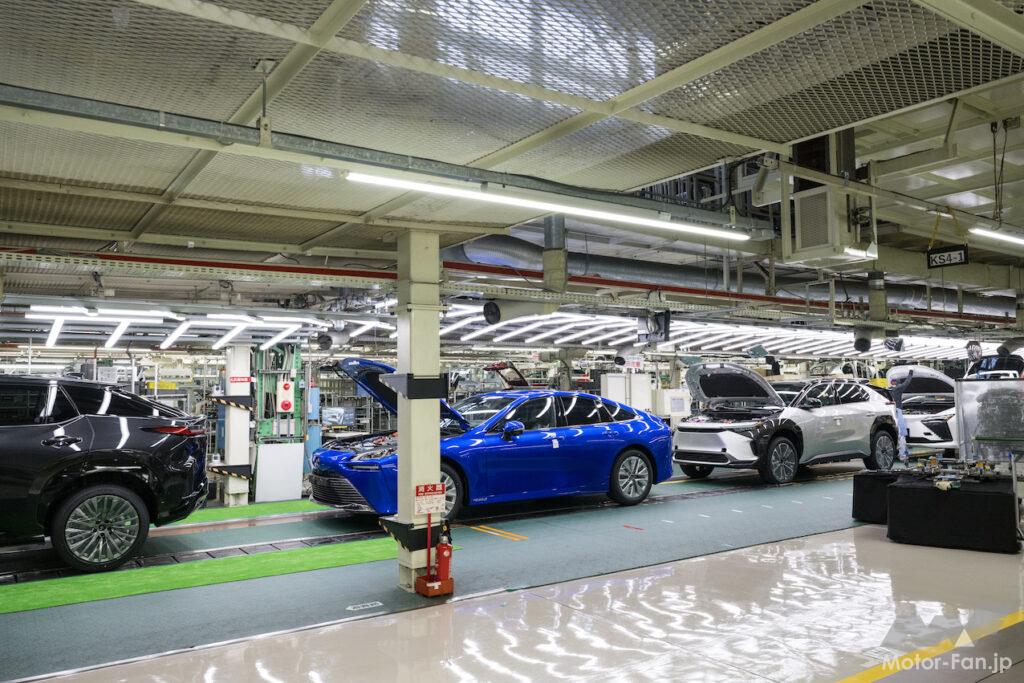
現在、第一組立ラインで生産しているのは
パトカー(HEV/ICE)
MIRAI(FCEV)
ノア/ヴォクシー(HEV/ICE)
bZ4X/ソルテラ(BEV)
クラウンクロスオーバー(HEV)
レクサスRZ
クラウンSDN(HEV/FCEV)
組立の量産ラインでは4つの異なるパワーユニット(ICE/HEV/FCEV/BEV)、異なる3つのボディシルエット(セダン/ミニバン/SUV)を混流生産している。現在は、連続二直体制で稼働している。
いまや混流生産そのものは、多くのメーカーで実施されているので珍しくはないが、これほど多彩なモデルを混流には、当然難しさがある。たとえばMIRAIとbZ4Xは1台あたりの作業時間に大きな差がある。説明のボードには「MIRAI:11.3時間/ノア:9.6時間/bZ4X:8.8時間/パトカー:10.1時間」と書かれていた。これをタクトタイムを104秒/台に揃えるのだという。作業の組み合わせ、生産の仕方を工夫し、同じ車種を連続して流すのではなく、それぞれの車種を量に応じて均等に並べて、混流することで工数差のロスを吸収するのだ。
メインラインは、「川」の字を繋げた1本のラインで、すべての車種はこのラインで組み上げられていく。水素燃料電池車のMIRAIの水素タンク組み付け工程は、専用ラインで行うが、それ以外はメインラインで混流生産している。
カイゼンを重ねて無駄・無理のない工場へ
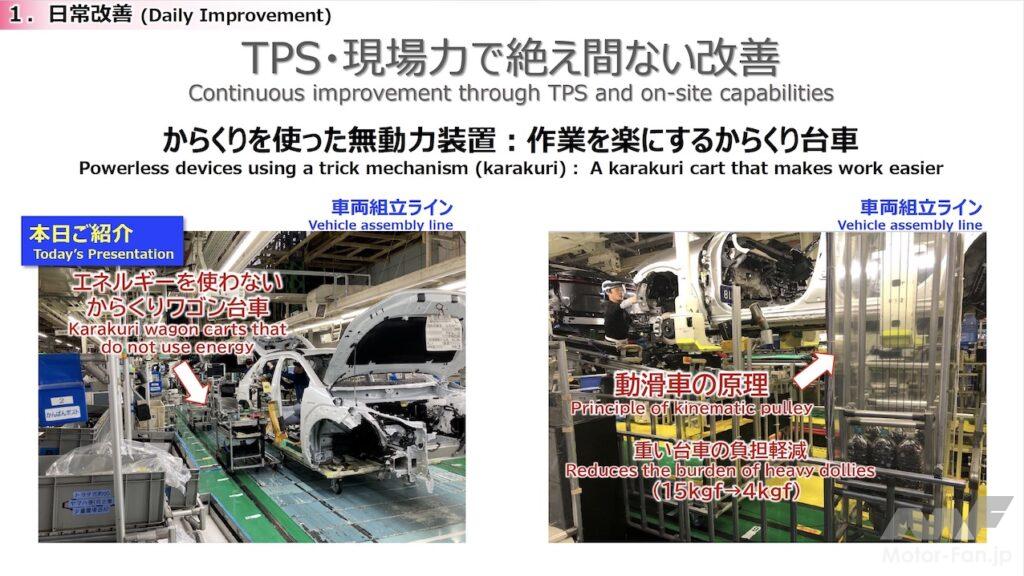
例えば、セダン、ミニバン、SUVとシルエットが違う車両を生産する場合、クルマの後方ライト類の配線を取り付ける際に、車両の後方で作業をすることになる。そのときの作業者は、セダンだと目の前、ミニバンはちょっと高いところで作業しなくてはならない、SUVは奥で上になるから、身体をかなり伸ばさないとできない。やりにくい作業だ。これをどんな車種がきても作業しやすくしたいということで、カイゼンしたワゴン台車を見せてもらった。
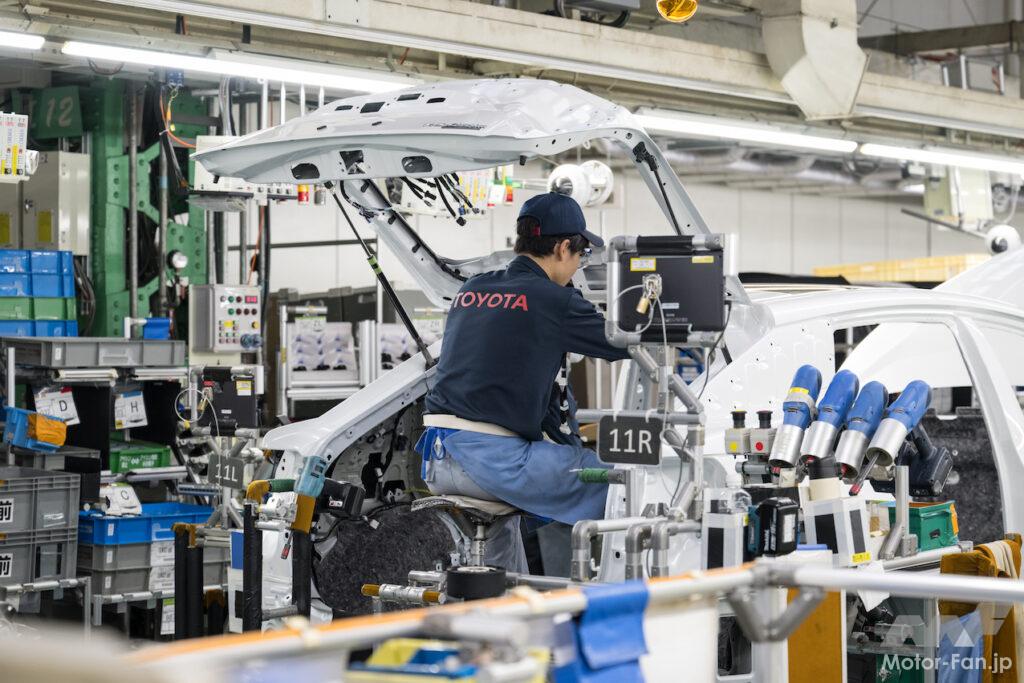
レクサスRZの後方で作業している作業者は車両の中に入って一番作業しやすいところで椅子に座って組み付けを行なっていた。組み付けが終わると、作業者は階段を降り、椅子を畳み、標準的なワゴン台車の中に椅子を収納する。ワゴン台車が親なら階段が子で椅子は孫といったカタチになっており、これでセダン、SUV、ミニバンに対応する。
また、ワゴン台車は、ごく一部を除いて、エア、コイル、電気の配線がない。つまり動力を使っていない。だから身軽に台車を動かせるのだ。工程変更に対しても対応がしやすい。
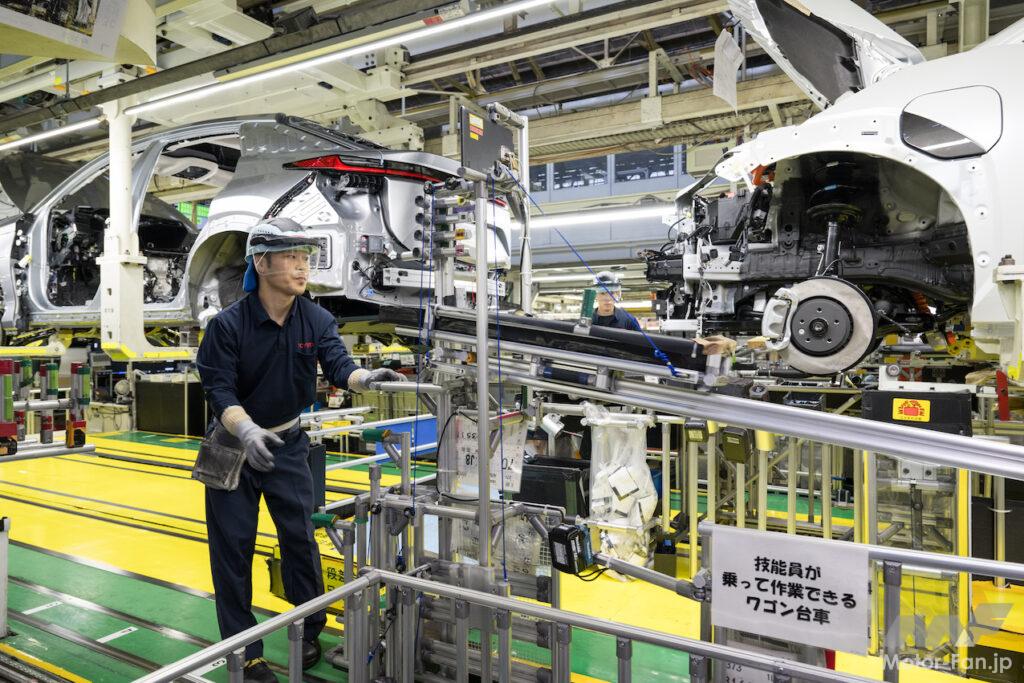
ラインにはさまざまな工夫”からくり”が施されていた。見せていただいた改善事例では、大きなワゴン台車を作業終わりに後続の車両に送る際に、台車と繋がった重りと動滑車の原理で、軽い力で動かしていた。動力は不要。重りは廃却するボルトを使っていた。
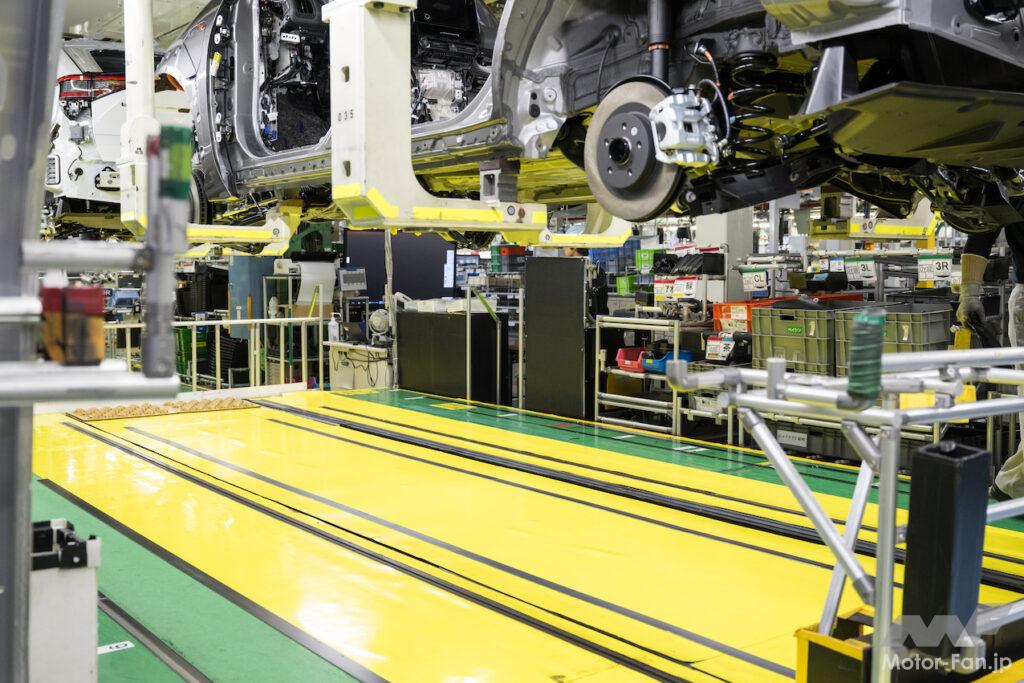
シャシーラインでは、床が黄色と緑色に塗り分けられていた。床下に入って作業する場合、暗くて作業がしにくい。カイゼン前はライトをワゴン台車につけていたが、カイゼンで床を黄色くしたことで70ルクス、照度を向上できたという。これもエネルギーロスはゼロだ。
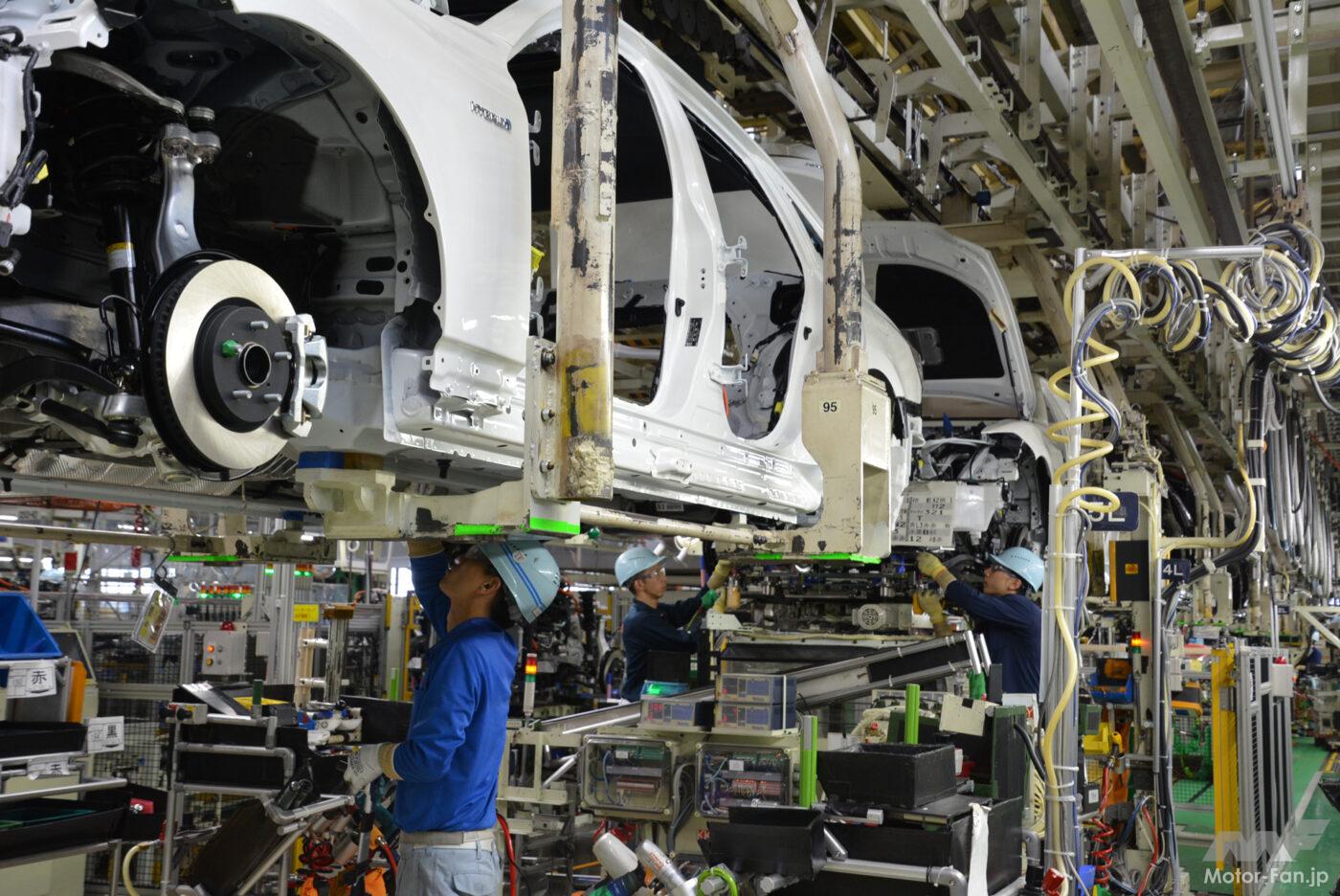
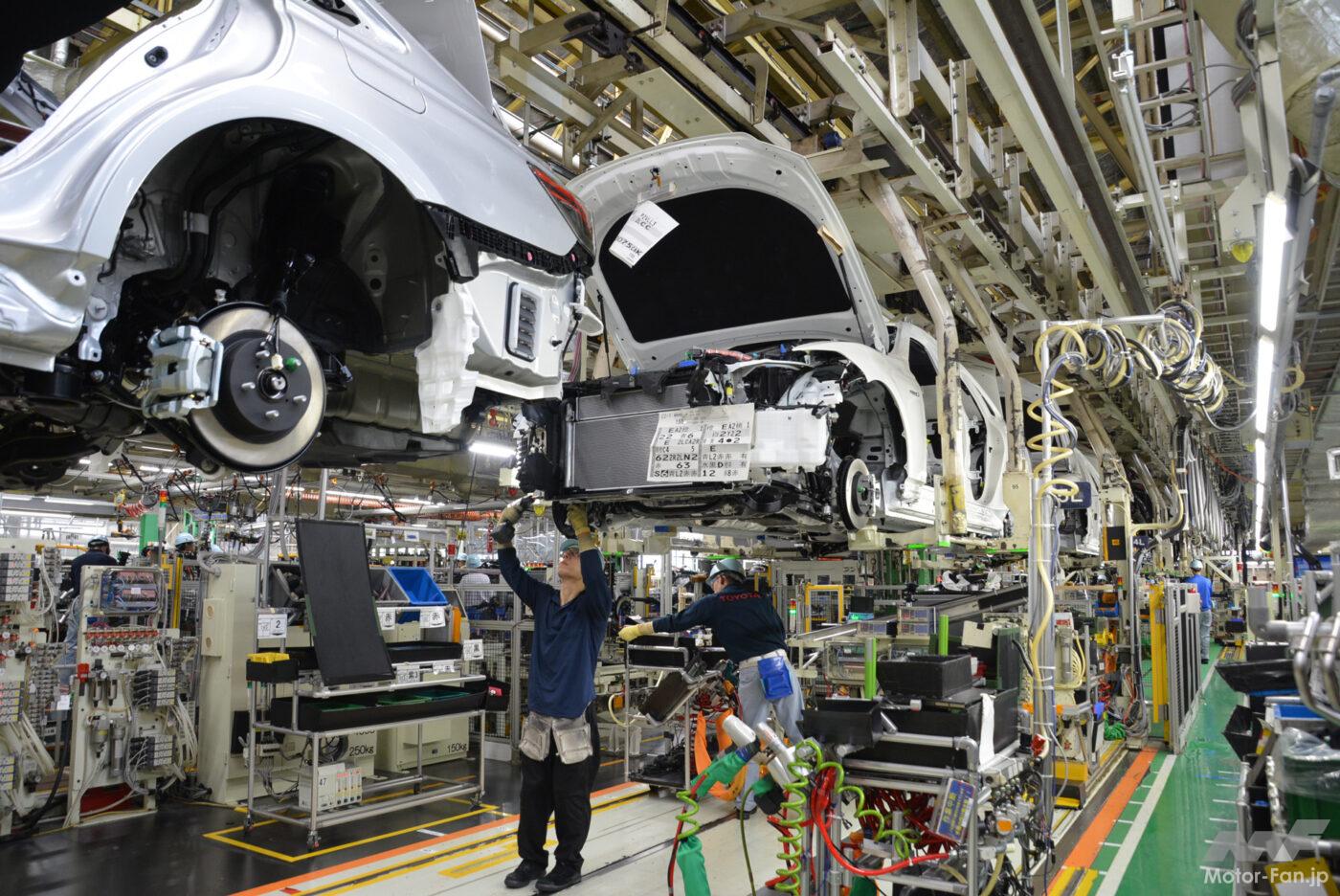
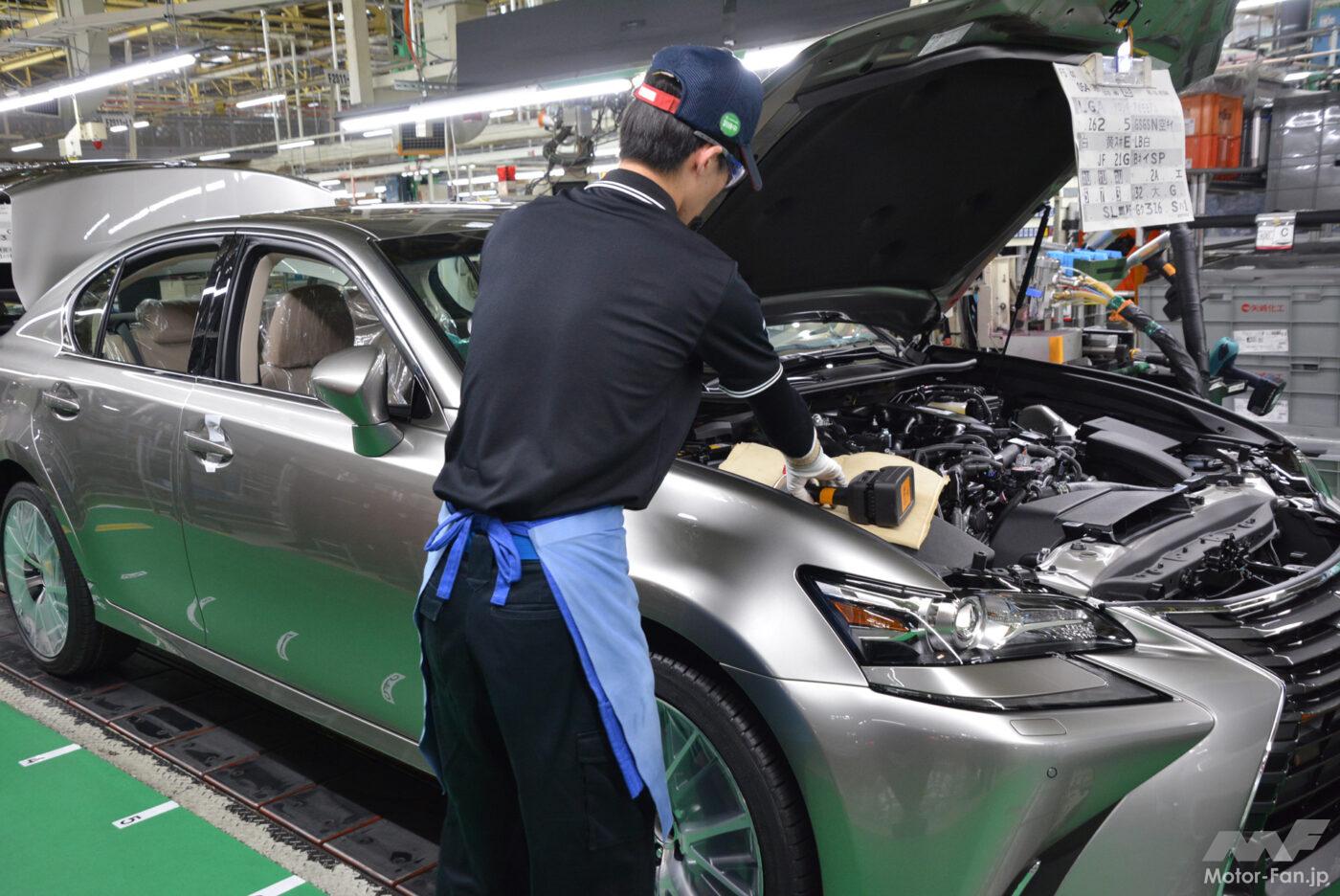

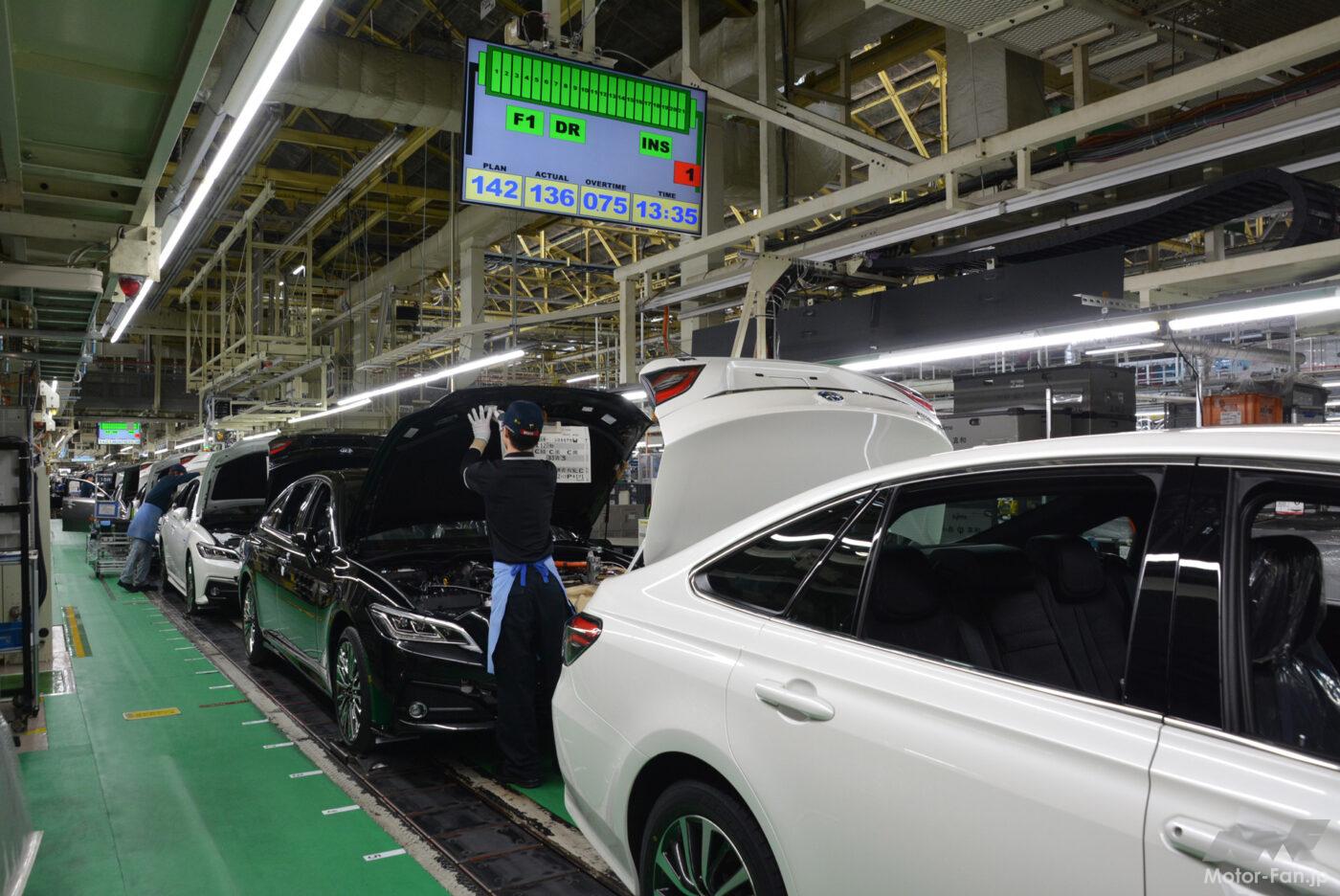
電池パックの搭載工程
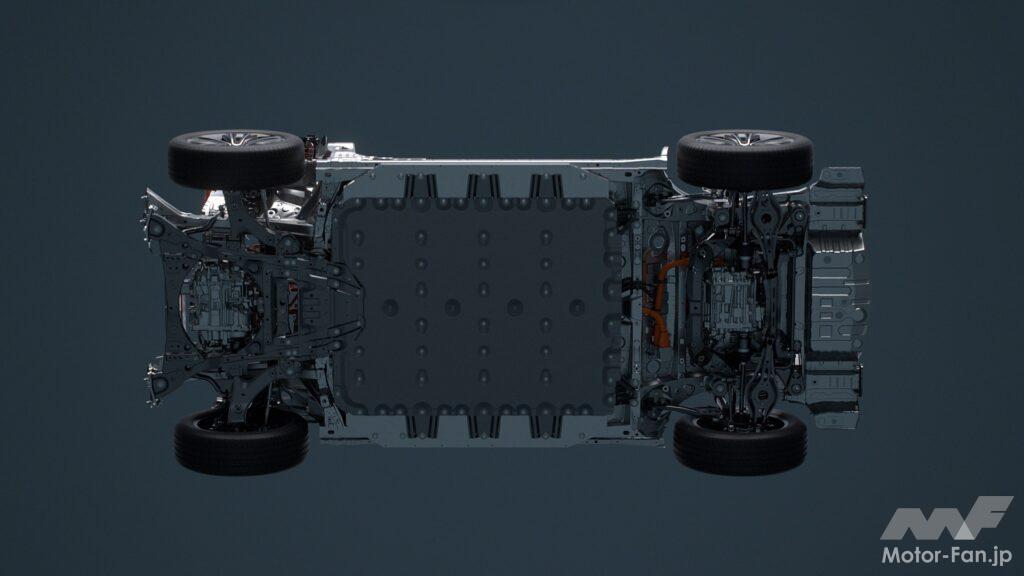
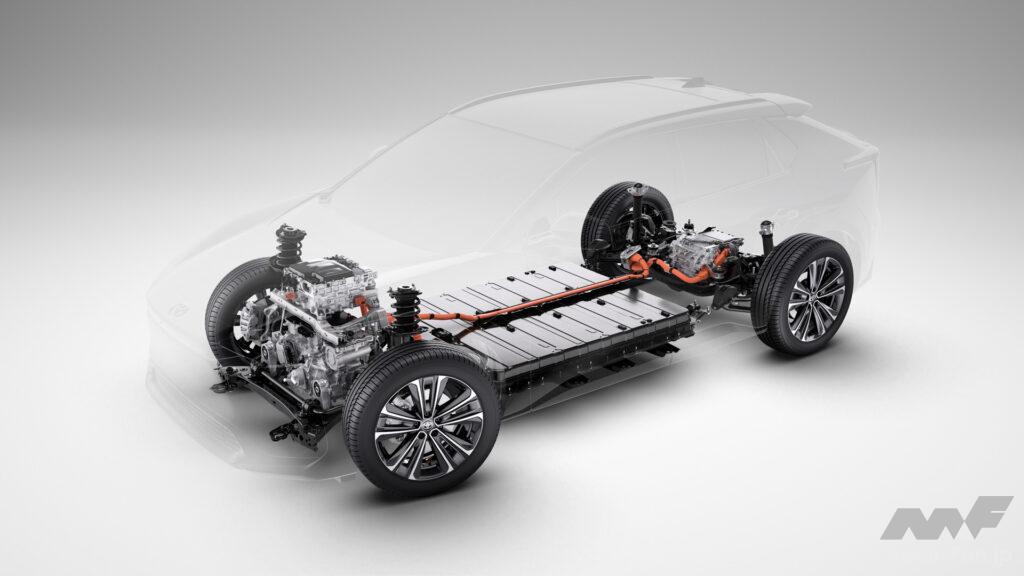
元町工場では、bZ4X/ソルテラのBEVも生産している。BEVには大きくて重いバッテリーパックを組み付けなければならない。この夏の連休以前は、電池パックだけ専用工程で組み付けていたが、現在はこれもインライン化した。隣の工場から車両の生産順に届けられた電池パックがリフターで車両下部に持ち上げられて組み付けられていく。電池パックの重量は460kg。BEVの車重は2250~2300kgにもなる。当然車両を吊るハンガーもそれに対応する汎用性が求められるわけだ。
カイゼンに次ぐカイゼン。トヨタ生産方式(TPS)の「ニンベンの付いた自働化」という考え方が隅々まで徹底した元町工場では、どんな車種でも作れそうだ。もちろん、将来クラウンがBEVになってもここで生産できるという。
進化する工場の凄味を感じた。