テスラのテキサス工場はセクシーか?
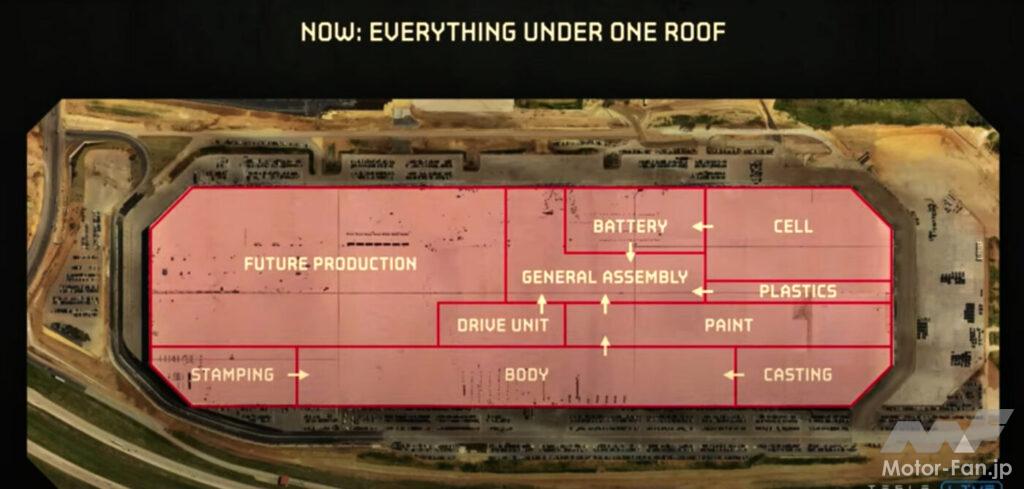
工場は生き物だ。完成することがない。完成する前に生産システムとしての寿命が訪れる。建物が完成し、設備を入れ、それを動かし、生産が始まる。しかし、どんどんと改良される。新しいクルマ、新しいパワートレーン、新しい装備が製造方法に変化を要求し続けるのだ。より高い効率、より高い製造品質を求めてつねに改良される。そして20年、30年と時が経てば、さらに改良を続けるよりも「設備を一新したほうがいい」と判断される。新しい工場が完成すれば、古い工場の役目は終わる。
テスラのテキサス工場について、その開所式に招待された人たち(多くは若い株主のようだ)にイーロン・マスクCEOがステージからビデオ画像を使っていろいろと説明した。ほとんどの人が歓声を上げている様子だったが、果たして過去に自動車工場を見たことのある人は、そのなかにどれほどいただろうか。彼らはSNSで「アメイジング」「セクシー」「エクスタシー」といった単語を使ってこのテキサス工場を称賛したが、いままで見たことのない光景、自動車工場初体験だから「セクシー」に見えたとしか思えないのだ。
興味深い点はいくつかあった。まずは工場内のレイアウトだ。テスラのカリフォルニア工場は元NUMMI(ニュー・ユナイテッド・モーター・マニュファクチャリング・インク=GMとトヨタの合弁工場)の工場であり、そこをテスラは格安で譲り受け、最初の世代の商品を製造した。ボディがアルミ合金のため、NUMMI時代のボディ溶接ラインはガラッと様子を変え、生産台数が少ないため設備投資を無理せず、ボディショップ(ボディ製造ライン)からペイントショップ(塗装工程)への搬送には台車を使っていた。
テキサス工場は、まだ床面積に余裕がある。そのため使っていないエリアがある。一方、生産ラインになっている部分は、作業の流れと生産材搬入の導線を太い一本戦にまとめた。整然としている。いまどきの車両工場お典型である。
資材を搬入し、金型プレス(stamping)を行ない、ボディショップでBIW(ボディ・イン・ホワイト=何も取り付けていないドンガラ状態のボディ)を作る。鋳造(casting)工程ではボディに使う大物アルミ部品を鋳造し、ボディショップに送る。完成したBIWは塗装工程に回される。バッテリーセルは鋳造ラインの反対側にあり、パッケージ化されたバッテリーが一車両般組み立て(general assembly)ライン、通常の表現で言えば最終組み立てライン(final assembly)に運ばれ、ここで車両になる。【Fig-01】
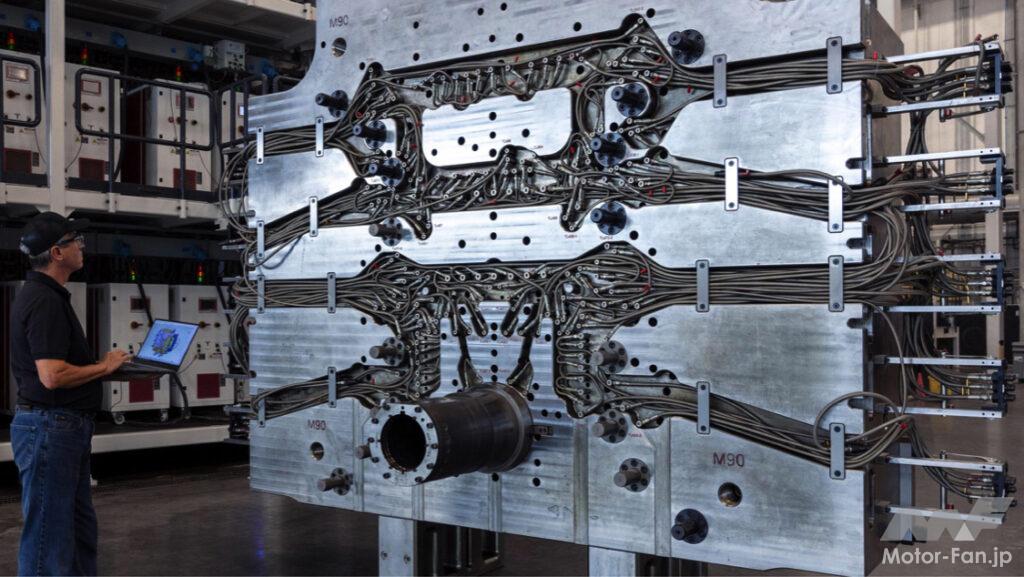
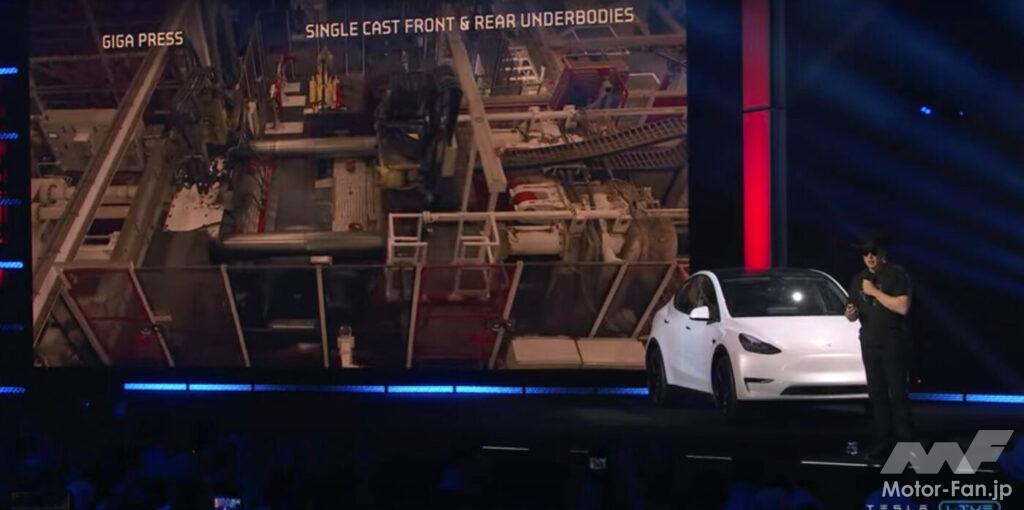
ボディ製造工程でもっとも興味深い設備は、メガキャスティングと呼ばれる超大物アルミ鋳造機だ。フロント左右とリヤまわりはアルミ一体ものであり、これを一発で鋳造する。その金型はこういう巨大なサイズだ。【Fig-02】装置全体は【Fig-03】で、2本の太いパイプ状のものが2つの金型(凸と凹)を合体させるためのガイドである。向かい合った金型を閉じ、その中の空間部分に溶けたアルミを高圧で流し込み、金型の隅々にまでまんべんなくアルミを行き渡らせ、固める。
その様子は【Fig-04】のようなものだ。このイラストに描かれている数字は、エンジンブロックを作るときの溶けたアルミの「湯流し」の速度と圧力だ。そして【Fig-02】のテスラの設備に負けず劣らず大きいのが【Fig-05】の金型。これはスバルの水平対向エンジンのエンジンブロックを作る金型だが、中央部分のほんの少しだけ見えているのがブロック部分の金型であり、それ以外の部分は溶けたアルミを高圧高速で流すために必要な「重量」である。
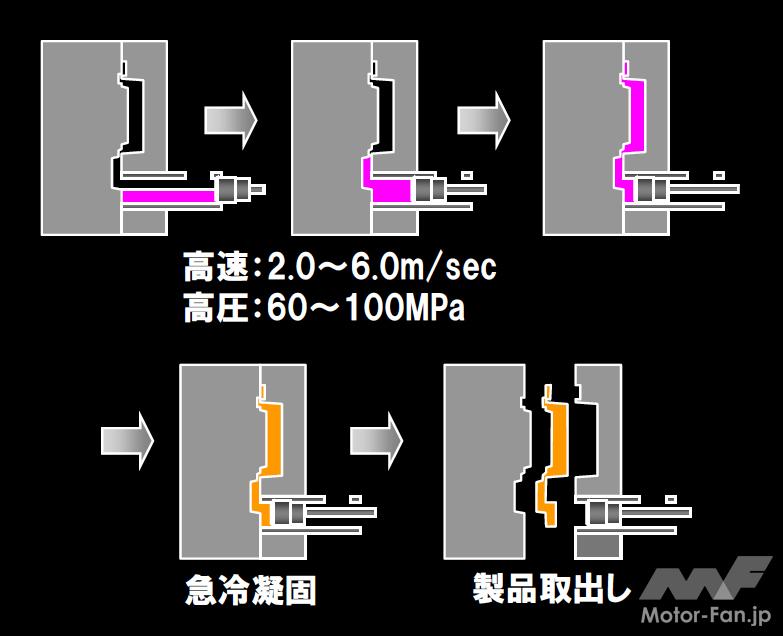
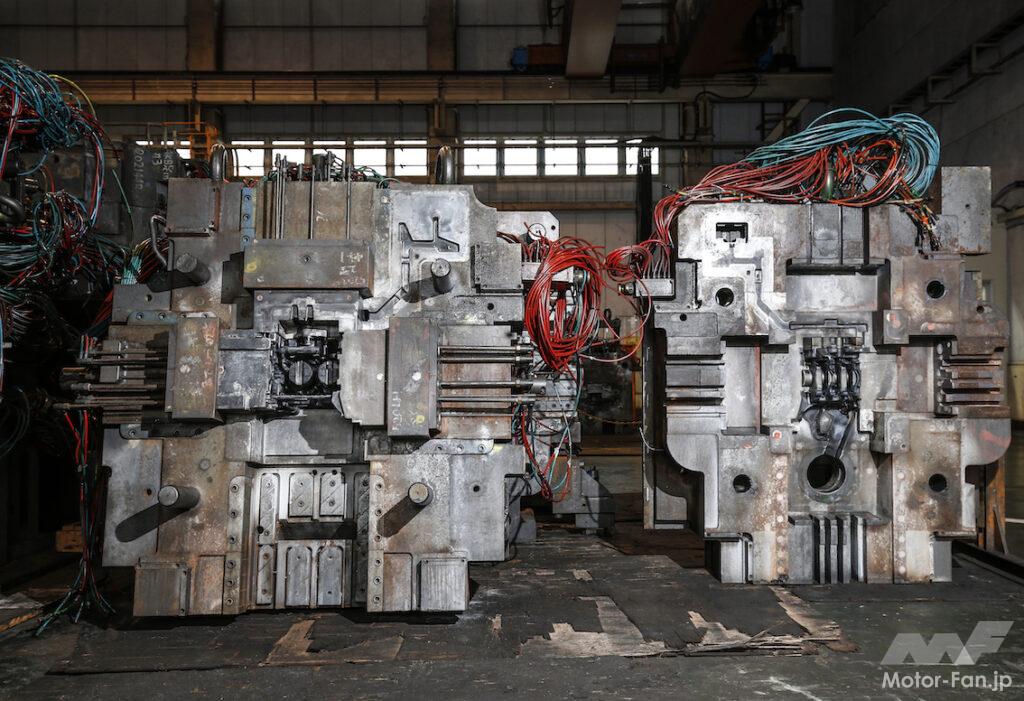
テスラはこうしたアルミ鋳物工程をメガキャスティングと呼んでいるが、とりたてて驚くほど大きな金型ではない。直6のエンジンブロックを作る金型とさほど変わらない。ただし投資はかかる。大物部品を一体の鋳物にするということは、その部分の寸法が決まってしまうことを意味する。ボディサイズの異なる車種やサスペンション形式が異なる車種を作るとなると、同じ部位で寸法違いの金型が別に必要になる。
【Fig-06】はテスラ「モデルY」のリヤセクションの比較だ。左は小さなプレス板を溶接して組み立てる従来の工法。右はメガキャスティングによる一体成形の左右ホイールアーチとクロスメンバーを中心に、数点の部品で構成した新しい工法だ。もっとも、大物のアルミダイキャスト部品という意味では【Fig-07】のBMW i3という先例がある。シャシーをアルミ鋳物とアルミ押出材の接合で作っている。
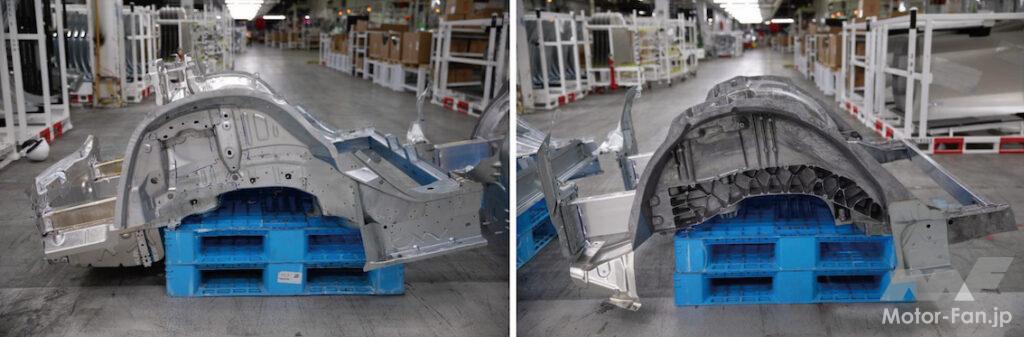
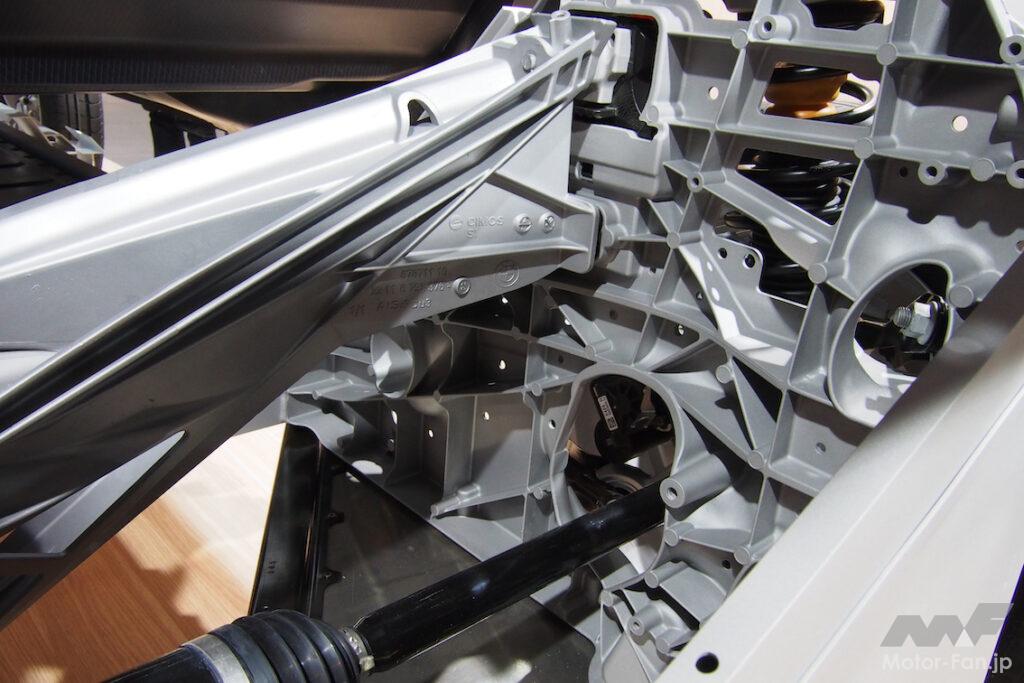
じつは、日本の自動車メーカーもフロントの左右ホイールアーチからストラットタワー、さらにバルクヘッドまでを一体のアルミ鋳物で作ろうと考えた例があり、試作まで行なったケースもあった。しかし、金型コストを抑えるためには複数車種で同じ形状の大型パーツを使うことになり、バリエーション展開ができない。アンダーボディ以上に「縛り」が大きくなり、車種ごとの金型がいる。それではコスト面で合わないという理由で却下された。ボディの作り方で言えば、日本がもっとも保守的であり、従来設備を流用できる構造意外はなかなか採用しない。
いっぽうBMWは、フロントとリヤの左右ストラットタワー周辺にアルミ鋳物を使い【Fig-08】のような構造にした。2016年デビューのG30型「5シリーズ」である。エンジンルーム内の左右サイドメンバーと、キャビン後方の左右リヤサイドメンバーを、それぞれダンパートップマウントとなる部分まで一体の鋳物にした。2003年登場のE60型「5シリーズ」はエンジンルーム全体をアルミ合金の薄板と押出ブロックと鋳物の組み合わせで作っていたが、試行錯誤の末に【Fig-08】のような構造になった。
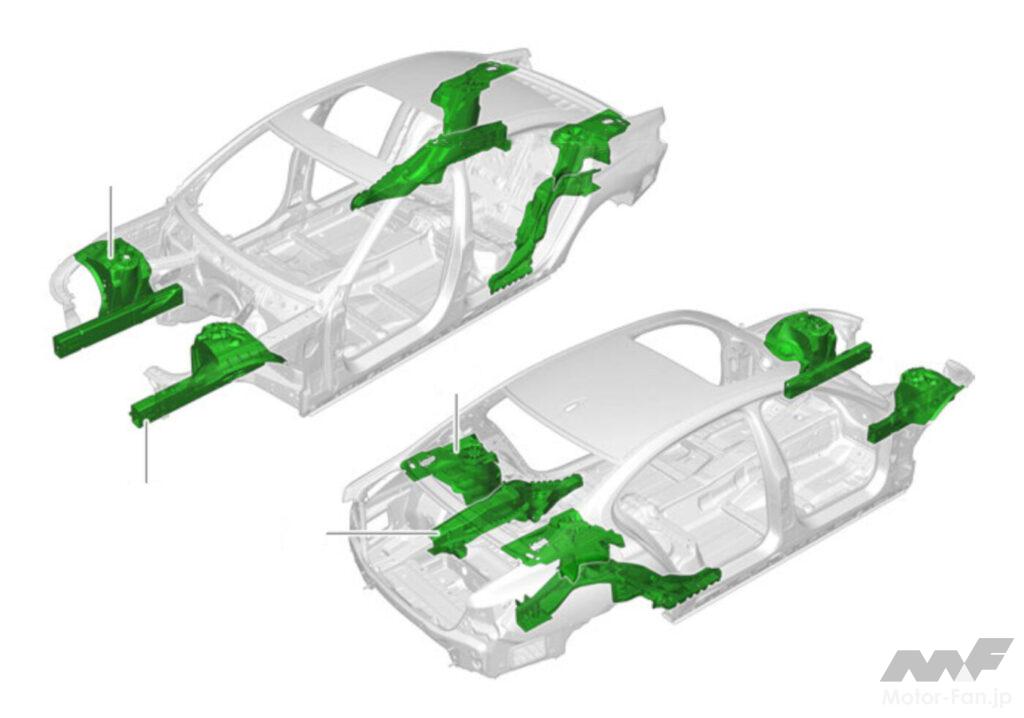
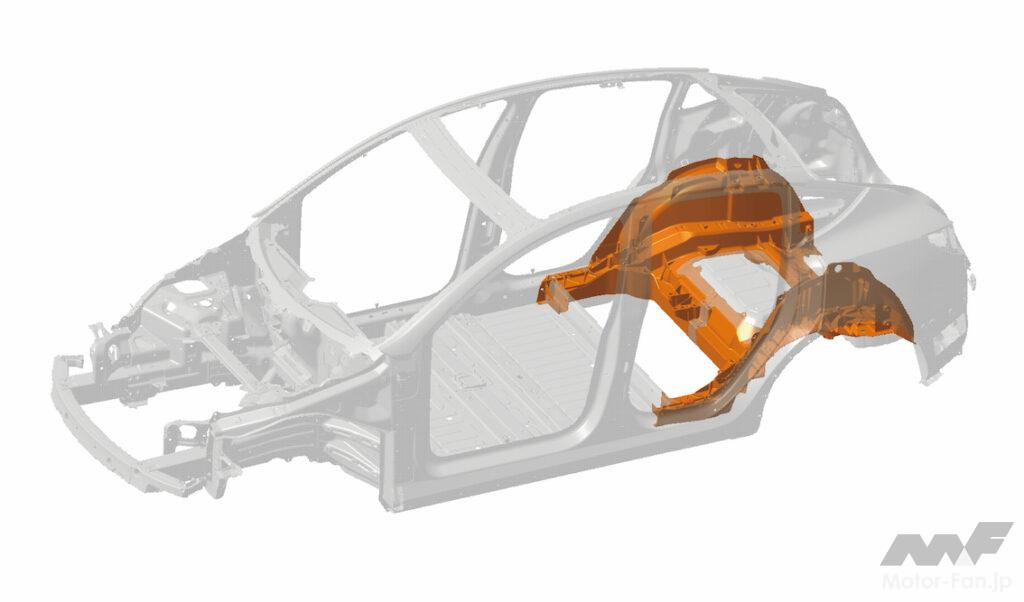
「アルミは靭性(しなり)がない。左右をアルミで一体化すると、ねらった乗り心地にならなかった」と、BMWのボディ設計担当者は当時、筆者のインタビューに答えた。「振動モードの周波数も高くなり、気持ち良くない」と。ボディ骨格をどう作る方は「考え方によりけり」である。ちなみにモデルYの構造は【Fig-09】であり、黄色い部分がメガキャスティング部品である。
テスラのアルミボディを構成するパネルのプレス(スタンピング)工程は、いつも見慣れたものと変わらない。【Fig-10】はサイドストラクチャーのプレス。キャビン側面のA/B/Cピラーとサイドシル、ルーフサイドレールで囲まれた部分を一体成形する工程だ。たいがいの場合、サイドストラクチャーは3回ほどのプレスで成形する。3セットの金型を固定しておき、順番にプレスされる。金型間の移送はロボットが素早く行なう。その設備をトランスファープレスと呼ぶ。ちなみに【Fig-11】はスバルのプレス設備。15年前の説部だが、仕組みは【Fig-10】のテスラとまったく同じだ。
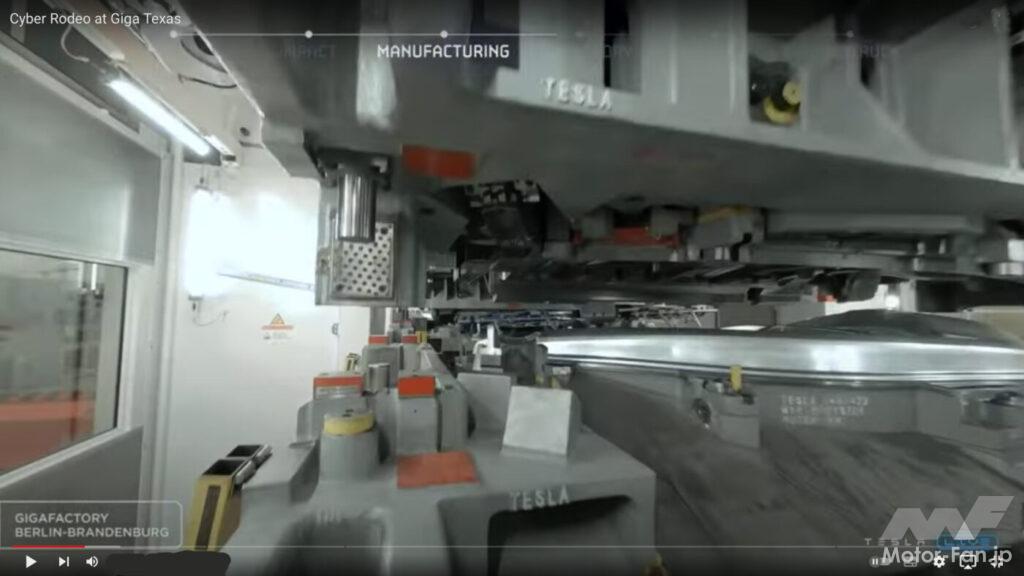
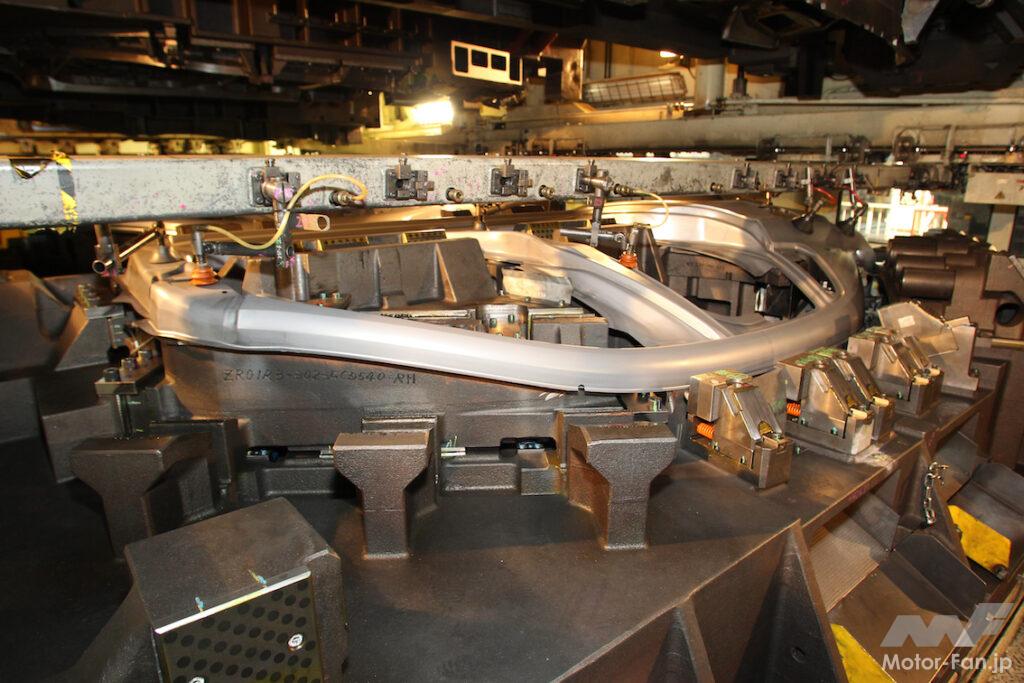
残念ながらボディ溶接ラインは鮮明な画像がなかった。しかし、作業内容は普通の自動車工場と同じで、6軸ロボットによる溶接だった。分解したモデルYを見ると、スポット打点や構造接着剤の使い方は至って普通である。パネルの重なりや切望部分を見れば組み立て順序はわかる。少々不器用な設計にも見える。
BIWが完成すると【Fig-12】のロボットが階上にある塗装工程への移送ラインへとBIWを送り出す。通常、この作業はリフト(エレベーター)で行なうことが多いが、テスラはリフト寸法によって扱えるボディの大きさが決まってしまうことを嫌ったのだろうか、汎用性の高いロボットを使っている。赤いアーム部分にはボディを4か所で固定するロケーターピンが取り付けられている。
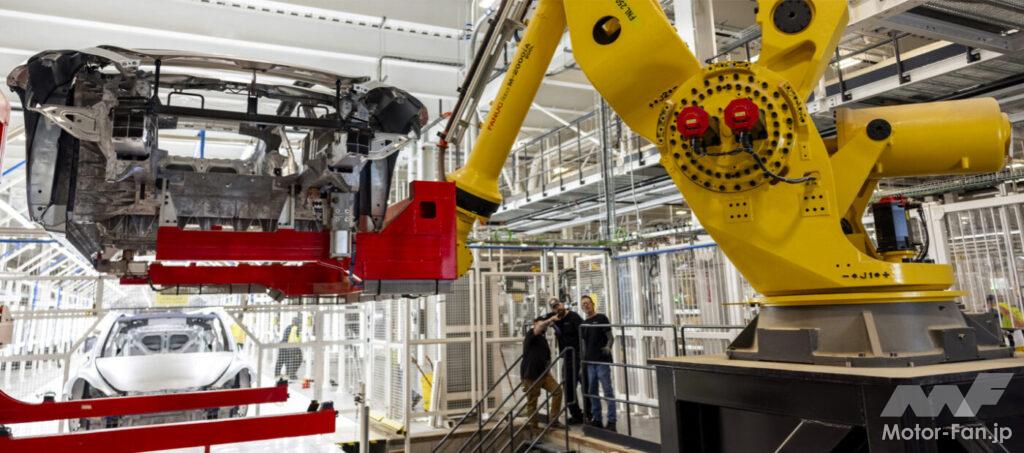
このあと、BIWは自動搬送で塗装工程へと向かう、つづきは後編でお伝えするが、ここまで見た感想で言えば「セクシー」でもなければ「エクスタシー」でもない。合理的に設計された、最新設備の車両工場。そう表現するのが正しい。