A-D-Aサイクルとは? Aは現場(アクチャル)Dはデジタル
貞宝工場の一角に、1990年に導入された加工設備がある。ギヤの鍛造に使う金型の加工機だ。この設備を動かすには材料を投入する必要があり、その材料を削る刃物(ドリル)を入れる必要がある。どちらも手作業。つまり、人が付いていないとこの設備は動かせない。
人がいない夜間や休日でもこの設備を動かせないかと貞宝工場の人は考えた。そうすれば生産性が上がる。設備に張り付いて面倒をみなければならない働き方からも脱却したいと考えた。そんな現場の思いを現場自らがデジタルを活用して実現した。
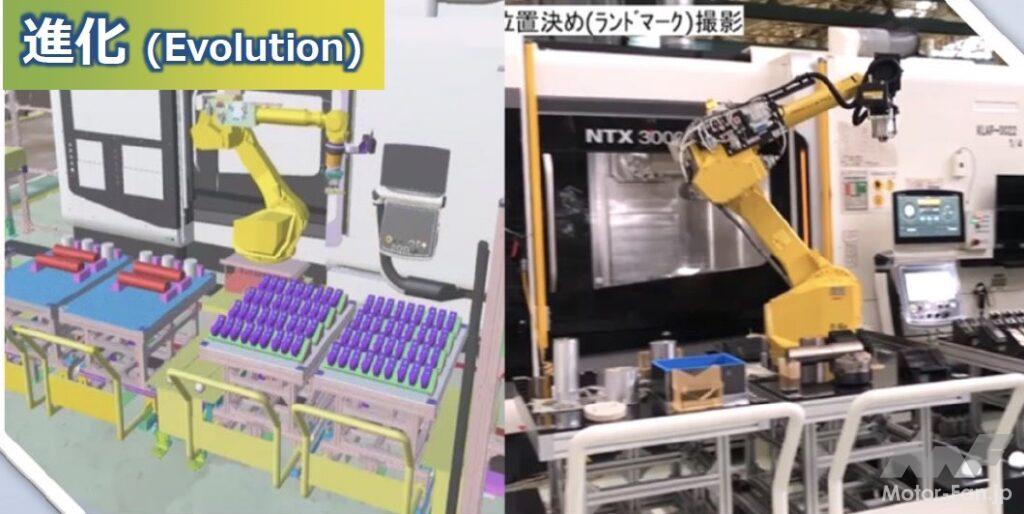
刃物の投入を自動化したのだ。交換する刃物は約4kgある。なかなかの重量で、こうした“重たい物”のハンドリングを自動化する場合は大きめのロボットを使うのが一般的だという。小型ロボットでは力が足りないし、リーチ(長さ)が不足するのが主な理由だ。また、大きなロボットを使う場合は安全柵が必須で、そうなるとスペース的にもコスト的にも厳しくなってしまう。
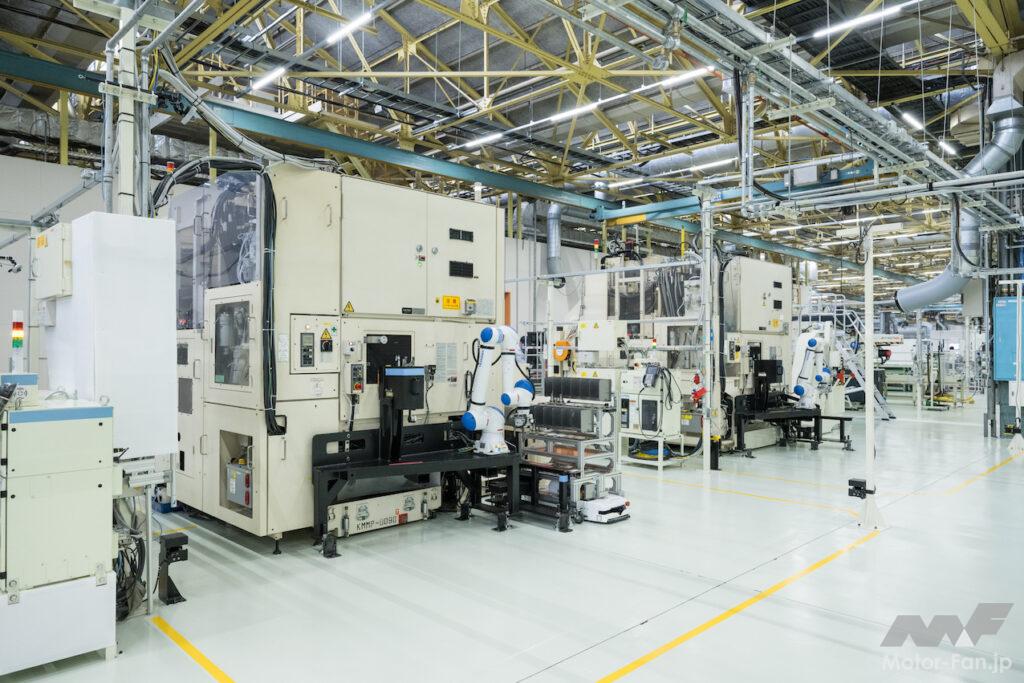
現物でトライ&エラーを繰り返すとリードタイムが長くなる。いっぽうで、「人が楽に作業できるようにする」「簡易な装置で実現する」のコンセプトをトヨタは伝統的に掲げており、これらのコンセプトを短いリードタイムで実現すべく、デジタル上で治具のトライアンドエラーを重ねた。
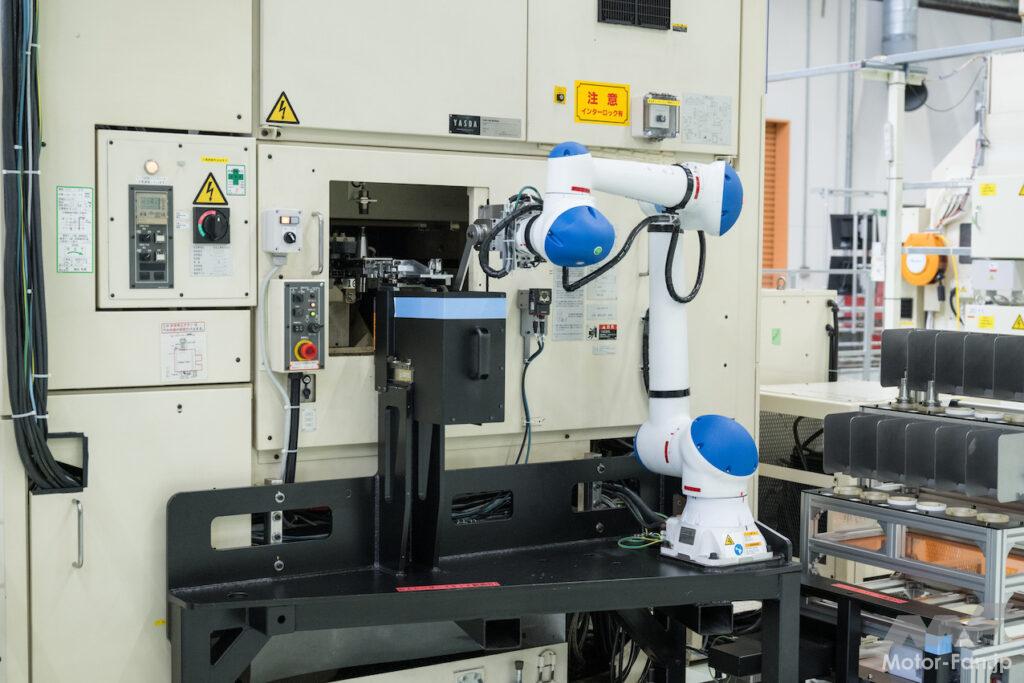
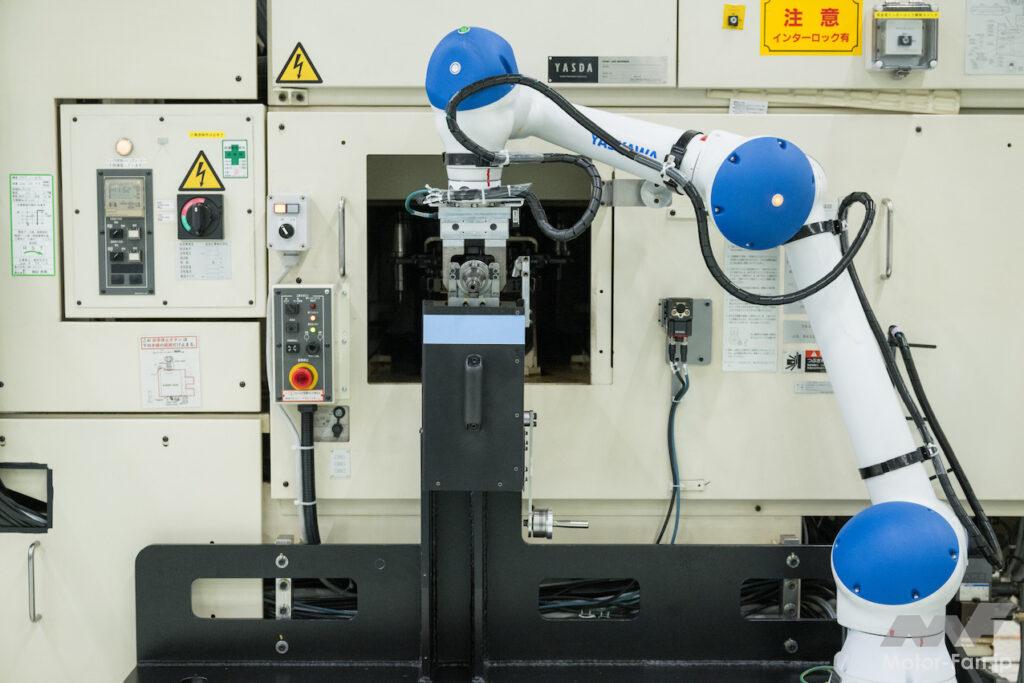
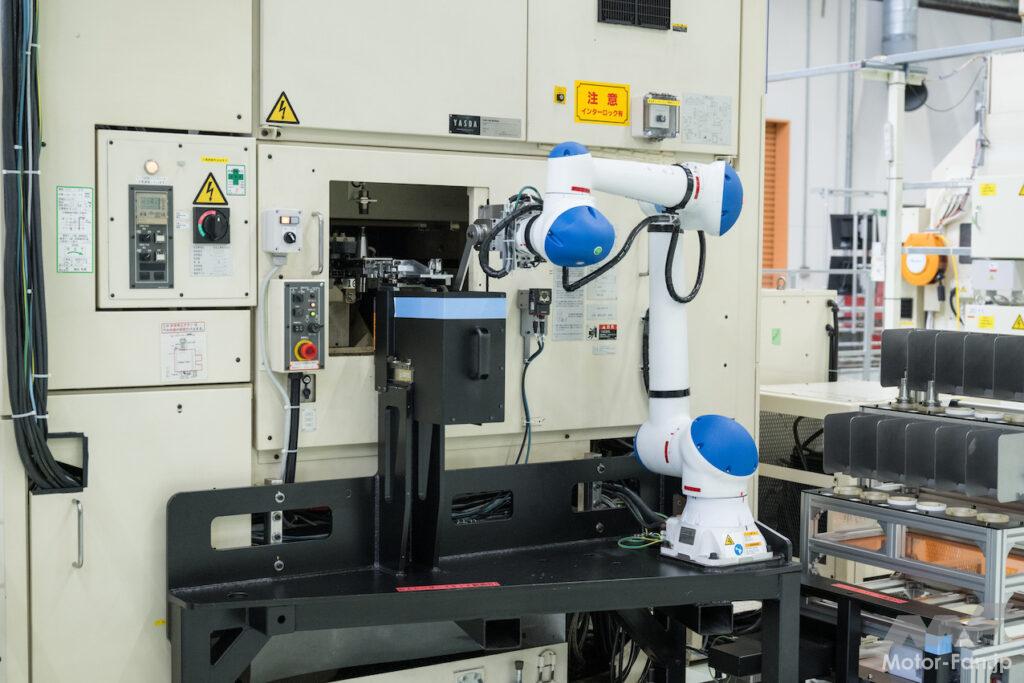
まず、小さなロボットで楽に作業できるよう考えた。大きなロボットではなく小型の協働ロボットにすれば安全柵を設ける必要はない。問題は、人が2本の手で行なっていた3つの作業、すなわち、1.向きを変える、2.奥まで投入する、3.受け渡す・引き取る、をロボットの1本の手で実現することだった。
ロボットの手がワンアクションで一連の作業ができるよう、ロボットの特性を現場が学び、デジタルを学び、そこに、長年のモノづくりで伝承されてきた技術から生まれたからくり(機械的な仕組み)を組み合わせることで、ロボットにやさしい治具をデジタル上で実現した。デジタル上で完成したその動きを現場のロボットに転写することで、小型の協働ロボットで自動化を実現することができたという。
小型の協働ロボットが実際に作業する様子を見せていただいた。見てのとおり、非常にすっきりした状況である(安全柵がないのは一目瞭然)。台車の上に投入する刃物が載っている。ロボットはまず、センサーで台車の位置を確認する。位置がずれていたら自分で修正し、作業を続ける。次に、設備の扉を開ける。扉には、ロボットでも開けやすいように取っ手が追加された。扉を開けたら、刃物を持って投入する手順に進む。その際、正しい刃物かどうか、アームに付いたカメラで確認する。
ここからが、からくりを用いた治具の出番だ。刃物を治具に載せ、治具のハンドルを握ってぐるっと回すと、向きが変わって奥に挿入される。刃物を取り出す際は、逆の手順をたどる。一糸乱れぬ動きとはこのことだ。
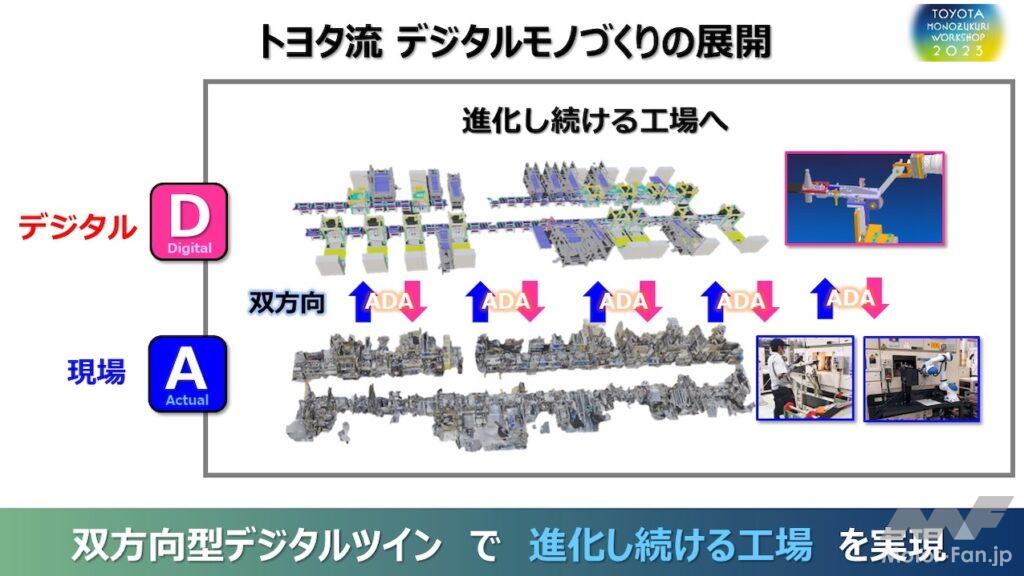
見せていただいたのは金型を加工する設備の事例だが、貞宝工場では工場全体で、現場自らデジタルを活用した改善を実施している。現場(アクチュアル=A)で行なわれている作業をデジタル(D)に転写し、デジタル上で改善。改善の結果をアクチュアルに戻す。このA-D-Aのサイクルを工場全体に展開しているところだ。
ワークショップでは、デジタル技術を使って技能伝承を行なう事例も公開された。設備の改善ではなく、人の動きの改善である。組立工場ではたくさんの人が働いている。その人たちが“より楽に”働けるよう、トヨタでは以前から改善に取り組んできた。従来の改善スタイルは、ビデオカメラで熟練者と新人の動きを撮影し、撮った映像を見比べて改善ポイントを探すやり方だった。非常に手間がかかるし、改善ポイントを見つけ出すには経験が必要で、熟練者の協力が欠かせなかったという。
誰でも素早く改善できるようにするため、熟練者と新人の動画から動きを抽出してデジタル化。動きの違いを誰でも素早く検討できるようになったという。加えて、従来はアナログで作成していた「標準作業組み合わせ票」という作業分析のグラフをデジタルで生成。やはり、改善ポイントが「誰でも・素早く」わかるようになり、スピーディに改善が進むようになったそう。
自動化改善の事例では、生産性を約3倍に向上させた。人作業改善の事例では、改善にかかるリードタイムを約3分の1に短縮することができたという。これらの取り組みを継続していくことで、労働者不足への対応や、モノづくりの変化に対しより早く対応していきたいとしている。これまではデジタルで検討したものを現場に展開する一方通行で終わることが多かったが、A-D-Aのサイクルを双方向型で回し、進化し続ける工場を実現するのが最終的な狙いだ。