目次
短期開発はタイパでありコスパ
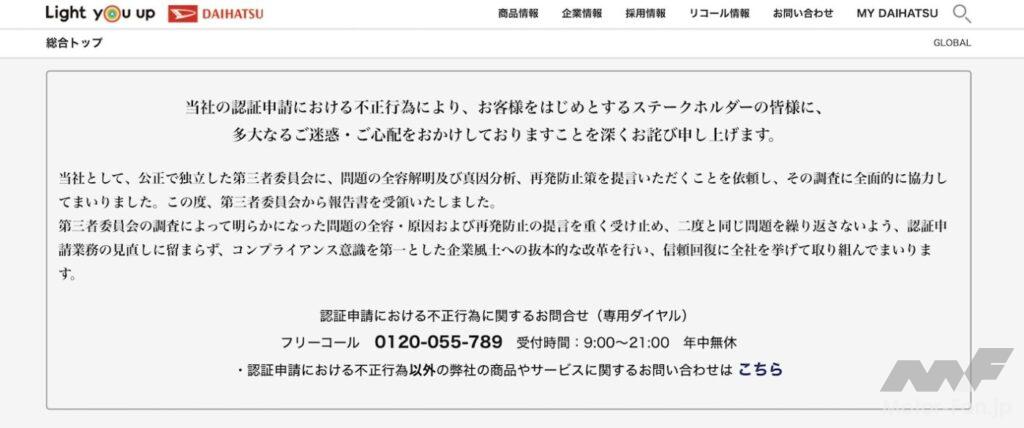
発売時期の変更は許されない。しかし、開発期間は短くしたい。短くすれば開発工数は減る。工数=コストだから、コストも削れる。短期開発はタイパでありコスパでもある。
同時に、部品点数も減らしたい。よく「自動車は3万点の部品で作られる」と言われる。何を「ひとつの部品」と呼ぶかにもよるが、たとえばねじ1本、電子回路の中の部品ひとつというレベルまで部品点数を列挙すると、現在のクルマは軽自動車でも3万点では済まない。従来は3つの部品で構成されていたものをひとつにまとめれば、部品のコストを削れる。自動車に限らず工業製品の世界では、部品代は1+1+1=3ではない。2.2か、それ以下になる。部品点数を削ることは、間違いなくコスパになる。
ダイハツが行なった不正のなかに「側面衝突試験」があった。この試験は「乗員がどれくらいのケガをするか」を見る。運転席ドアにほかのクルマが突っ込んで来たことを衝突センサーが検知したらすぐにカーテンエアバッグまたはサイドエアバッグを展開し、乗員への危害を弱める。試験では乗員の代わりに実験用ダミーを座らせ、そこに取り付けたいくつものセンサーのデータから「もし生身の人間元だったらこれくらいのケガをする」という予測値を導く。
相手車両がドアを突き破って突進しないよう、ドア内部には補強バーが入っている。ボディ全体も衝撃に対しては相当に丈夫に作られている。側面にクルマが突っ込んで来る衝撃は相当なものだが、ボディ設計術と素材の進歩によってボディ変形はかなり少なくなった。この丈夫なボディにエアバッグを組み合わせることで、時速40kmくらいで真横に突っ込まれても、乗員は致命傷を追わないで済むようになった。
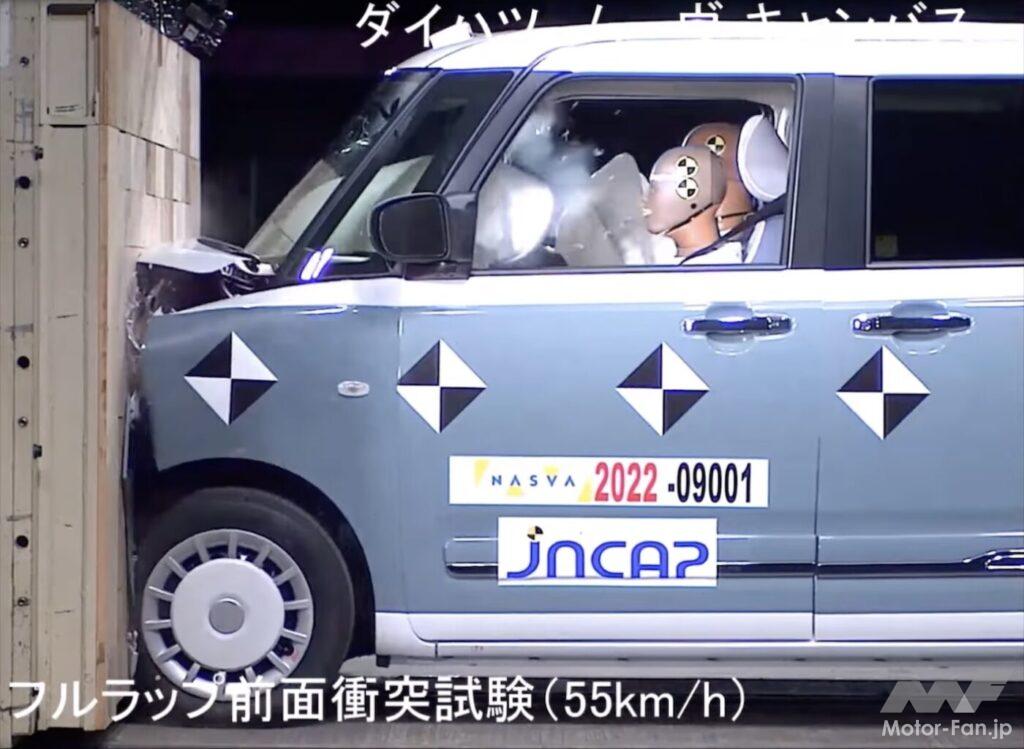
ダイハツの不正は、この側面衝突試験だけでも複数あったが、筆者がもっとも重罪と判断するのは、エアバッグの展開をエアバッグECU(コンピューター)からの直接指示ではなく、あらかじめ「衝突の0.0x秒後」というようにタイマーを設定して行なったことだ。
その理由は、衝突試験実施の時点ではエアバッグECUが完成していなかったためだ。しかし、衝突試験はさっさと終わらせたい。だからタイマーによる展開指示という不正を行なった。
タイマーにセットされた時間は、設計目標値だったと思う。衝突センサーが衝突を検知し、現実的に「いままでのクルマではこうだった」という時間差がタイマーにセットされたのだろう。現在、衝突試験はシミュレーション上で繰り返され、実際にクルマをぶつけるのは「最後の確認試験だけ」と言われる。「シミュレーション上ではちゃんとできていたから、タイマー指示でも問題はない。
こういう判断だったのかもしれない。
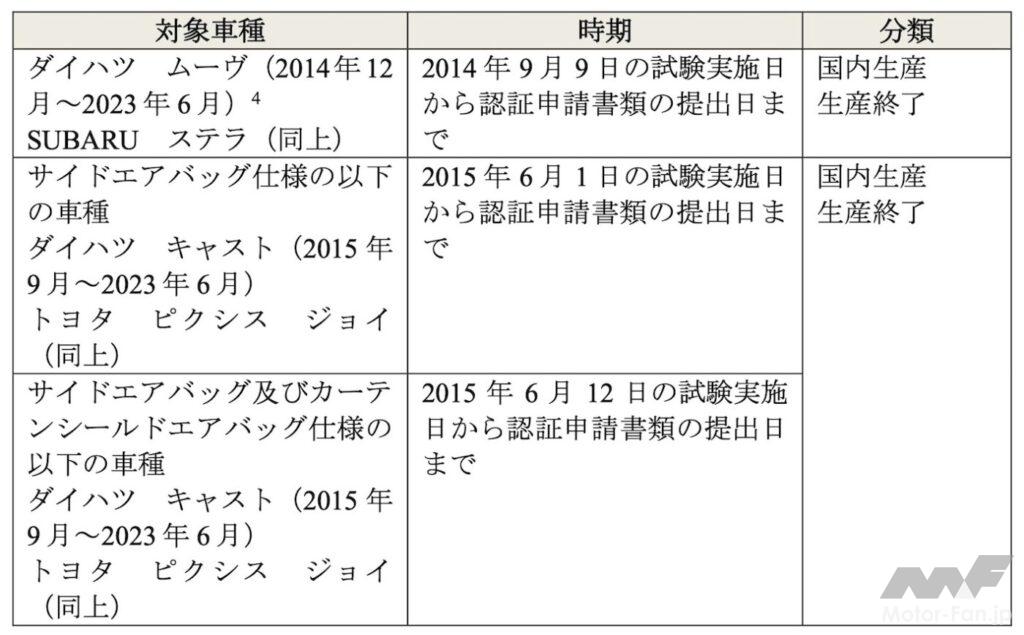
調査報告書(概要版)には、以下のように記載されている。 エアバッグのタイマー着火(不正加工・調整類型) 安全性能担当部署の試験実施担当者等は、側面衝突試験における認証試験では、本来、衝突時の衝撃をセンサーで検知してサイドエアバッグ及びカーテンシールドエアバッグをエアバッグECUで作動(以下「自力着火」という)させる必要があるにもかかわらず、届出試験の時点ではエアバッグECUが開発されていない段階であったため、届出試験において、衝突時の作動をエアバッグECUではなく、タイマーにより作動(以下「タイマー着火」という)するように以来する試験依頼票を作成した上、サイドエアバッグ及びカーテンシールドエアバッグをタイマー着火させる方法で届出試験を実施して、同試験によって得られたデータを記載した試験成績書を作成して、認証申請を行った。
実際、クルマをぶつける衝突試験でも、座らせたダミーが記録するデータはプラスマイナス10%程度の誤差が出る。良心的なOEMなら「試験でプラス10%の数値になったとしても、障害基準値より低くなるようにしておく」と考える。ダイハツはカーテンエアバッグ用ECUの完成を待たずにシミュレーション的な衝突実験をした。
もし、ここで「サイドエアバッグ用ECUの完成を待つべきだ」と試験を担当する現場が判断しても、開発スケジュールを管理する部署や設計部部門からは「そうしよう」という回答はも間違いなく来ないだろう。スケジュールは厳守なのだ。これは開発に携わるすべての部署が共有する認識だ。
そもそも開発スケジュールが「非現実的なくらい短かった」のか?
では、そもそも開発スケジュールが「非現実的なくらい短かった」のか。個々の車種についての開発機関は公表されていないが、ダイハツはミラ・イースで開発期間2年(24カ月)を切った実績がある。こういう数字はひとり歩きしてしまう。「2年あれば十分だろ?」と開発上層部が言えば、部下は「いや、無理です」とは言いにくい。
いま、実際にクルマを一台作るフルスケール(実物大)の試作は、ほとんどの場合で一度しかない。すべての部分の設計を終え、部品を発注し、それをすべて集めてクルマを組み立ててみるのは、ほぼほぼ1回だけ。せいぜい2回である。欧米でも同様だ。
すべての設計はコンピューター上で行なわれる。バーチャル設計だ。バーチャルでひとつひとつの部品を設計し、複数の部品を組み合わせたユニットに仕上げ、その段階でシミュレーションを行ない作動を確認する。ユニットをいくつも集めたモジュールを設計する場合も、同じ手順で徹底したシミュレーションが行なわれる。この作業を総称してバーチャル・ステージと呼ぶが、この手順はダイハツでも同様だ。
そして、部品の現物を試作したら、それを持ち寄ってモジュールに組み上げてみる。中心になるのはティア2(2次下請)が多い。これがフィジカル・ステージ。この段階で「一発成功」という例は、筆者はほとんど聞いたことがない。何がしかの手直し、設計変更が必要になる。その作業はそれぞれの部品を担当するサプライヤーが行なう。
フィジカル・ステージが1回だけという例は多い。なので、まるごとクルマ一台を仕上げる試作車製作も1度だけだ。昔は一次試作、二次試作、場合によっては三次試作を経て量産試作車が作られたが、現在は一次試作車=最終試作車であり、これが量産試作車になる例も多い。開発期間短縮は世界中のOEMでつねに行なわれている。
日本のOEM(オリジナル・エクィップメント・マニュファクチャラー=自動車メーカー)は、欧米に比べて社内での開発が多い。欧州は、本当にざっくり言って7割が外注あるいは「その道の専門企業がOEMにエンジニアを送り込んで開発を全面サポートする」というケースが多い。「我われはクルマのコンセプトと車両のパッケージング(どこに何を置くか)を決めればいい」と公言するOEMの役員もいる。
開発の外注という需要に対応するため、ロベルト・ボッシュ、ZFフリードリヒスハーフェン、コンチネンタル、フォルシアといったメガ(巨大な)サプライヤー(部品・素材の供給元)が育ち、各社がOEMにエンジニアを派遣し、クルマの開発を手伝い、部品の供給も行なっている。
また、オーストリアのAVL、ドイツのFEV、IAV、イギリスのリカルドといったESP(エンジニアリング・サービス・プロバイダー)が生まれ、OEMからの開発依頼をこなしている。FEVはアーヘン工科大学から、IAVはミュンヘン工科大学からといったように、機械工学系の名門大学からスピンアウトしたESPが欧州には多い。
日本ではESPが育っていない。トヨタ、日産、ホンダなど大手OEMがそれぞれ「おもに取引する系列サプライヤー」を組織し、自動車開発を支援させてきた。しかし、車種や輸出仕向け地または海外現地生産モデルの増加にともなって日系OEMでは社内開発だけで対応できる限界を超えた。現在は国内サプライヤーだけでなく欧州ESPにも仕事を依頼するようになった。同時に、日本のサプライヤーやOEMから欧州系ESPに転職するエンジニアも増えてきた。
もちろん、欧米のOEMでも開発機関の短縮と製造コストの低減は必須であり、その意味ではコスパとタイパが求められている。この状況は日本と変わらない。しかし、コスパとタイパを追求するという自社の利益のために法規制で定められた試験を端折ったり、あるいは省略したりはしない(普通は)。
アメリカなら制裁金が2兆円規模になる?
もし、今回のダイハツのような長年にわたる数多くの項目と数多くの車種についての不正がアメリカでNHTSA(国家道路安全局)に告発されたらどうなるか。筆者は制裁金が2兆円規模になると想像する。
ディーゼル車の排ガス不正が2015年9月にアメリカで発覚したVW(フォルクスワーゲン)は、アメリカでの制裁金1.5兆円、集団訴訟の和解で1兆円など、合計3.7兆円(2016年6月~2018年6月の為替レートで)を支払い、株価がディーゼルスキャンダル以前の水準に戻るまで7年かかった。
ダイハツは非上場企業でありトヨタの100%子会社。トヨタから送り込まれた幹部もいる。この上下関係から想像すると、開発期間の厳守とコスト低減目標の必達をダイハツ側がなりふり構わず進め、トヨタの顔色をつねに気にしていたという想像は成り立つ。当然、トヨタへの忖度もあるだろう。親会社と子会社の関係はどこでも似たようなものだ。
第三者委員会は「過度にタイトで硬直的な開発スケジュールによる極度のプレッシャー」「現場任せで管理職が関与しない態勢」と指摘した。これが大元であり、その結果として「コンプライアンス意識の希薄化と認証試験の軽視」が蔓延し「チェック態勢の不備な職場環境のブラックボックス化」へと落ちていった。筆者はそう考える。
ただし、第三者委員会が言う「法規の不十分な理解」は当たらないだろう。十分に理解していても社内事情が優先された。つまり確信犯だった。筆者はそう考える。
赤信号、みんなで渡れば怖くない。こんな文句を思い出す。