ミシュラン太田サイトに設置される「ミシュランAMアトリエ」には金属積層造形装置、いわゆる3Dプリンターが2台置かれている。できあがった印刷物の非常に微細かつ立体的な造形は見る者すべての心をつかむ、とは言い過ぎではないくらいの迫力。その繊細な作りはいったいどうやっているのか。
ミシュラン×群馬積層造形プラットフォーム(GAM)が採用しているのはAddUp社のFormUp 350という機種。パウダーベッドフュージョン:PBFという技術で積層印刷していくのが特徴である。粒径40μmのパウダーを、縦横350mmのベッドに敷き詰めていき、レーザー照射して固めていくというプロセス。なお、ベッド高さは縦横値と同じく350mmで、このベッド内の寸法で立体造形する。
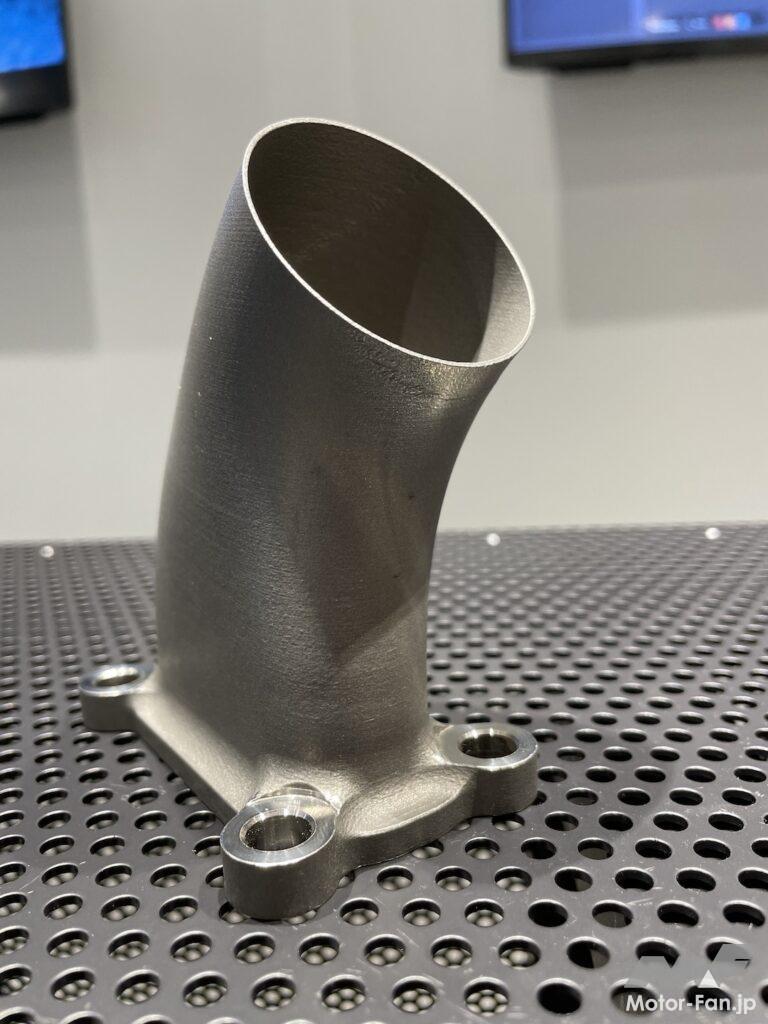
3Dプリンターの印刷の仕組みとは、たとえば上のマニフォールドであれば、これを水平方向にごく細かく輪切りにしていった各層(レイヤー)を積み重ねていくイメージである。写真をよく見れば、水平方向に筋目がついているのがご覧いただけるだろう。輪切りにしているから内部にどのような形状を入れ込んでも印刷が可能、鋳造や切削では到底実現できないような立体的な網目なども自在に造形できる。
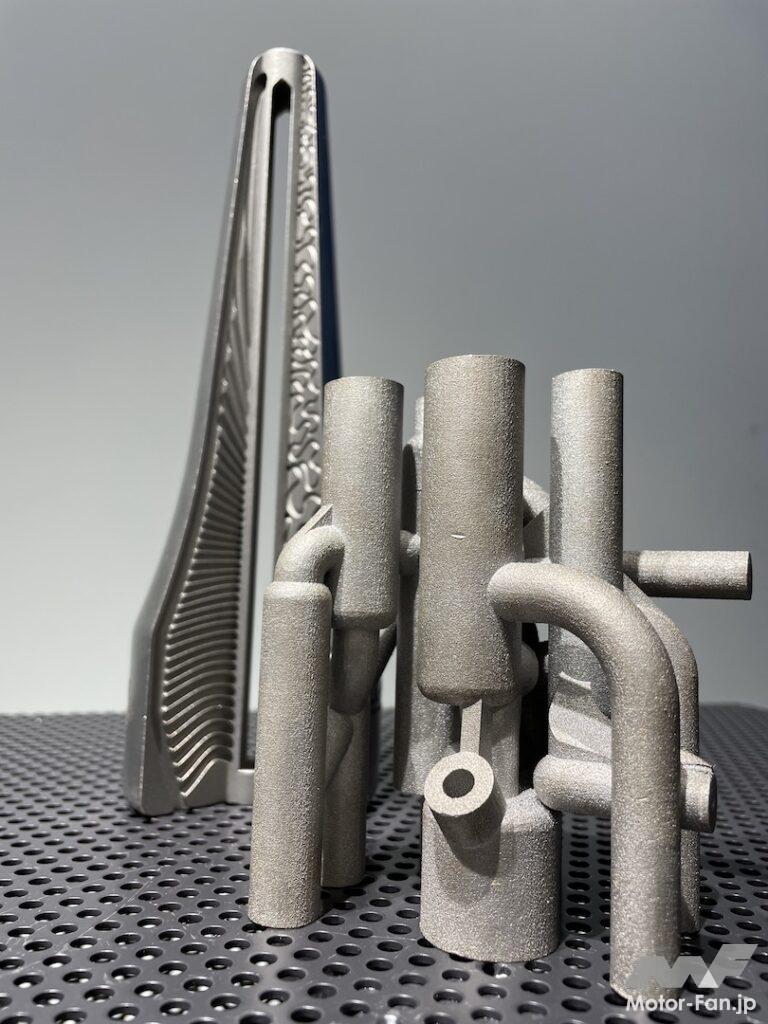
FormUp 350の造形プロセスを見せてもらった。パウダー上をレーザーが走り、必要な部位だけが焼き固められると、次のレイヤーのためのパウダーがそのまま敷かれる。するとまたレーザーが焼き固め——の繰り返し。外から眺めていると、見えるのは直前のレイヤーだけである。作業が終わるとパウダーの回収機(掃除機のような構造)でベッドの白い部分、つまり焼き固められていないところを吸っていき、それに連れて立体造形された印刷物が姿を表す。
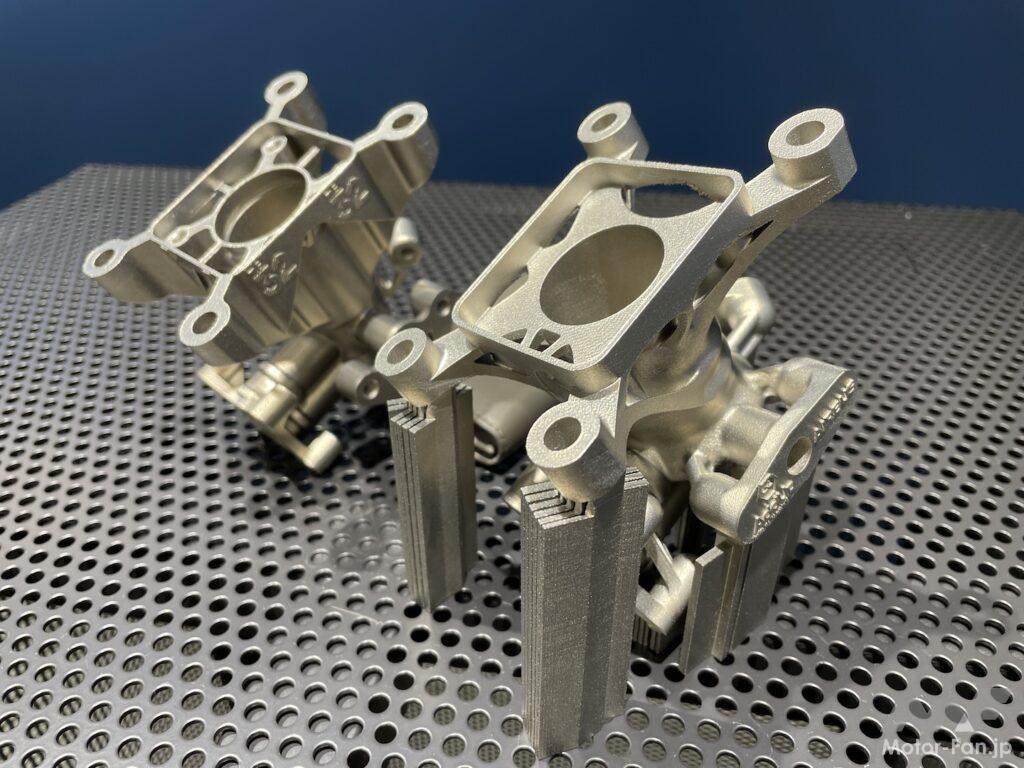
どのようなレイヤー構造にするかは、設計者の腕の見せ所。たとえば直径20mm×高さ300mmの直管(そんなものを3Dプリンターで印刷する意味がないというご指摘はご容赦)を印刷するときに、立てるより寝かせて印刷するほうが圧倒的に早いのはご想像のとおり。上の写真もマニフォールドの例で、曲がった管構造としたいことから、印刷中に増していくアンバランスを解決するために最初のレイヤーから柱を設けている。印刷後にはこの柱は不要になるので切り飛ばす必要があり、いかにももったいない。そこで形状を工夫し、奥の製品では(少々の肉は増えてしまうものの)アンバランスで倒れないようにし、柱を設けなくとも製品単体で印刷できるようにした。同じ形状であっても方向に着目したり、目的を達成するために違う形状として印刷を早くしたりというセンスが求められるのだ。
なお、現在のところパウダーは40μmを用いているが、もっと大きな粒径として印刷速度を増すことも可能。レーザーの照射速度は現在のところ一定とのこと。印刷終了後に回収したパウダーは、次の印刷のために再び使用される。パウダーの素材としてはアルミ合金、ステンレス、チタン合金などが使用可能。