「車重が重くなることが分かっていましたので、少しでも軽く。さらに、効率良くつなげたいということで、エキゾーストマニフォールド一体型を開発することになりました」と、開発を担当したIHIの石井聡氏は説明する。「ヨーロッパ向けにエキマニ一体ターボを作っていますが、それはエキマニの中央にターボが位置するタイプ。GT-R用のように片側にターボを置くレイアウトは初めてでして、これが非常に難しかったです」
難しかったのは480ps/60.0kgmという国産車最大級の出力/トルクを絞り出すことだったのかというと、そうではなかった。
「簡単というほどではありませんでしたが、ターボ1基あたりにすれば240ps出せばいいわけですから。ものすごく高い数字だったわけではありません」
考えてみれば、排気量1.9ℓあたり240psである。今や2ℓの排気量で300psオーバーの出力を絞り出す市販車用エンジンもある。難しかったのは、レスポンス向上のため容積を極力小さくしたとはいえ、3気筒分をとりまとめるエキマニの鋳造だった。エンジンルームのレイアウト上、排気を最短距離で触媒につなぐ必要上、重量配分の適正化上、ターボユニットをエンジンルームの後方にレイアウトしたかった。そのためには、エキマニの最後部にターボチャージャーを取り付けるのが効率的である。
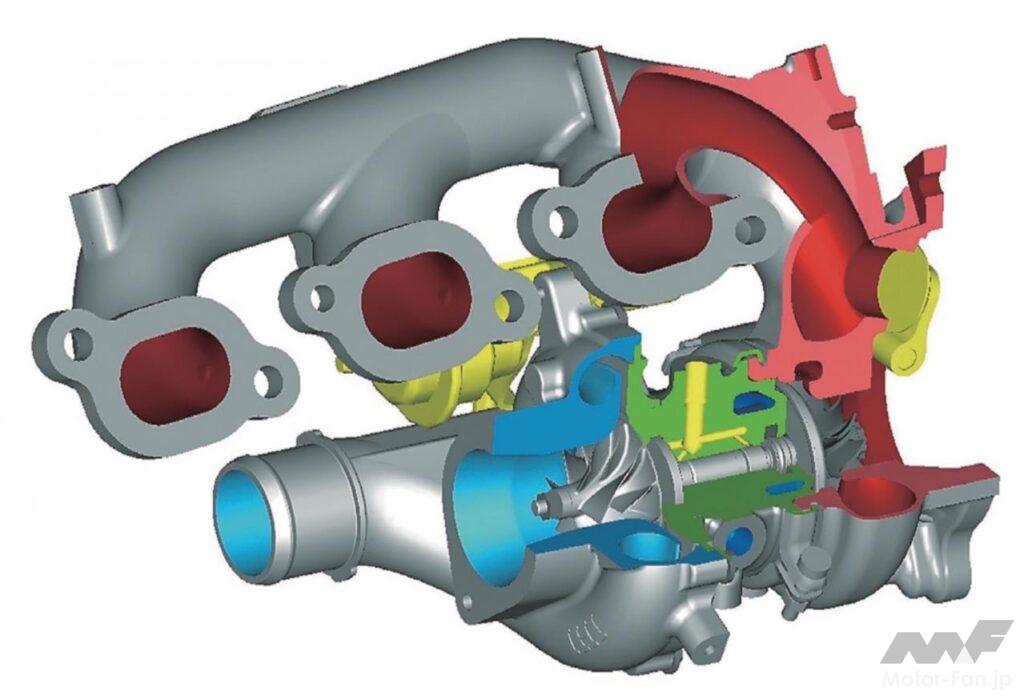
「鋳造品ですから、長い物だと鋳込んで冷やす段階で変形してしまう。精度管理が大変です。鋳造は専門の業者さんにお願いしているのですが、相当苦労を掛けています。鋳物の経路、流し方ですね。しかも、我々はとにかく薄く作ってくださいとお願いしていますから」
3.5mmが一般的な数値だというが、GT-R用のエキマニは厚さ2.5mm。もちろん、エキマニで余計な熱を奪われることなく、燃焼室で生まれた熱エネルギーをできるだけそのままの量、ターボチャージャーに導くためである。小さなサイズでは2.5mmを経験したことはあったが、GT-R用のような大物は初トライだったという。
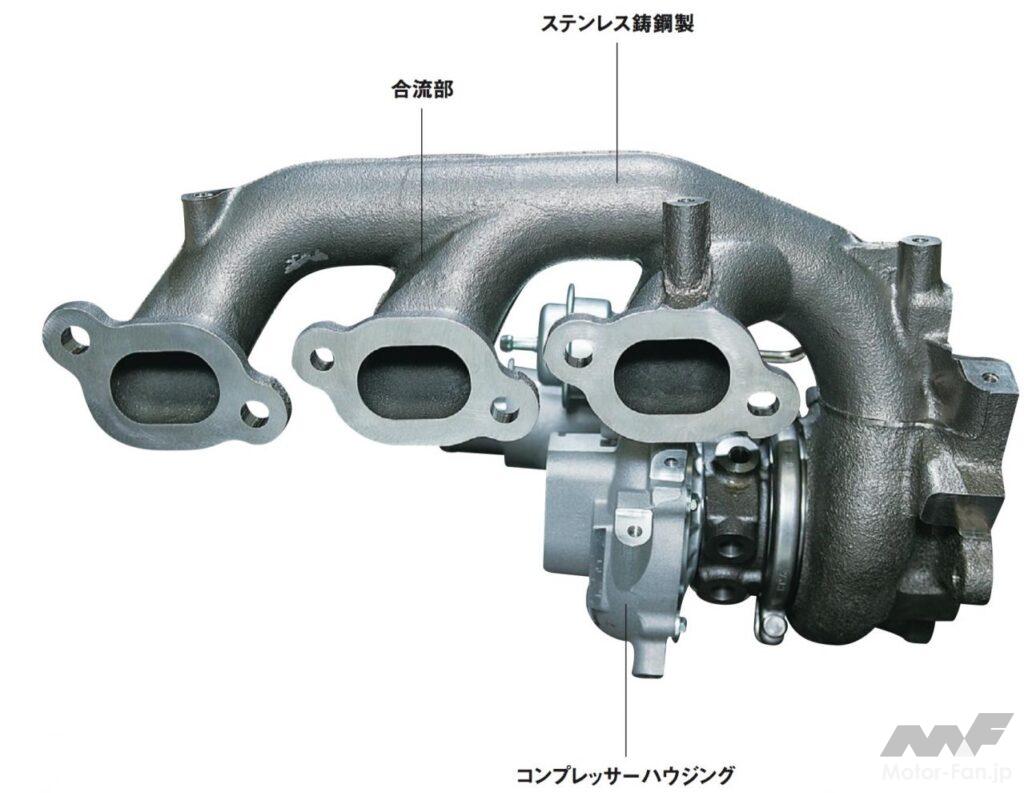
素材はステンレス鋳鋼。素材自体は1000°Cオーバーまでの耐久性を備えているはずだが、台上で耐久試験を行なうと、トラブルの連続だった。1000°Cより低い温度でクラックが入るのである。
「イメージで言うと、中東の方が買われて、冷機状態からいきなり300km/hを出す。それを毎日繰り返しても大丈夫なように、ということでした。国内での使用だったら絶対に起きないような状況ですが、GT-Rは全世界に出すクルマですので、考え得る状況には対処しておく必要がありました。そこで、クラックの問題です。条件が過酷ですので、通常は割れないようなところが割れました」
タービンハウジングのフランジ、各ポートの集合部などにクラックが生じやすく、CAEによる熱
応力解析を行なっては形状を変更し、試作~テストのループを繰り返した。厳しい開発だったが、それだけに石井氏は日産サイドの「GT-Rに懸ける意気込み」を感じ取ったという。
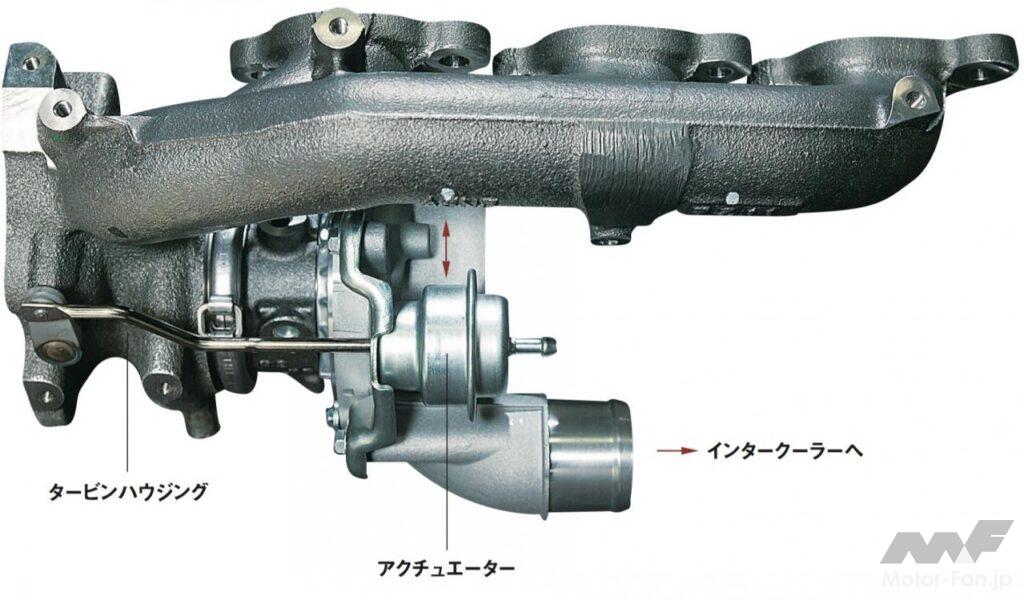
ヒートマスを低減したエキマニとなったことで、排気は従来よりも熱を失わないままタービンホイールに当たる。だから材質は耐熱性の高いインコネルとした。軽さが魅力のチタンアルミでは950°Cまでしか対応できず、見送ったという。
GT-Rと聞いてスペックを追い掛けるばかりだと思っていたそうだが、実際はレスポンスが第一。しかも、従来の常識では考えられないような耐久性を要求された。それを支えているのはエキマニの設計と鋳造技術である。