目次
2022.07.21 3社合同のニュースリリースより 株式会社BluE Nexus(本社:愛知県安城市、取締役社長:尾﨑 和久、以下BluE)と、当社、株式会社デンソー(本社:愛知県刈谷市、取締役社長:有馬 浩二、以下デンソー)は、「1モーターハイブリッドトランスミッション」を新たに開発しました。本製品は、本年秋頃発売を予定しているTOYOTA/新型クラウンのCROSSOVER RSに採用されました。 今回3社で開発した「1モーターハイブリッドトランスミッション」は、新設計のDirect Shift-6ATと、駆動モーター、インバーターを一体化した製品で、高い加速性能と燃費貢献が特徴です。車両リアに搭載されるeAxleと合わせて、2.4Lターボエンジンを最大限に活用しながら、プレミアム車両に相応しい走行性能を実現し、TOYOTA新型クラウンの魅力向上に貢献しています。 <本製品の開発のポイント> ■ダイレクト感のある走りと上質なドライブフィーリングの実現 新開発の高耐熱発進クラッチを採用し、さらにその高度な制御によって、高い発進応答性を実現しました。また、Direct Shift-6ATをベースに新たに設計した駆動モーターを組み合わせることで高いトルクアシスト効果を発揮し、ダイレクトかつトルクフルな走りを実現しています。 また、発進用とエンジン切り離し用のクラッチを協調制御することにより、車両発進時や走行時のあらゆる状況で、スムーズかつ静粛にエンジンの始動や停止をすることができます。 長年培ってきた世界最高レベルのオートマチックトランスミッションの変速技術に、これらの新技術を組み合わせることで、ダイレクト感とスムーズさを両立し、プレミアム車両に相応しい上質な乗り心地の実現に貢献しています。 ■小型化技術、機電一体構造による車両搭載性の向上 駆動モーターは、コイル拡張組付けなどの新開発生産技術によるステーター軸長短縮や、コイル冷却、磁石配置最適化により、大幅に体格を低減しました。大径扁平タイプとすることで、2つのクラッチをモーターのローター内側に配置することができ、製品自体の全長増加を抑えています。また、インバーターをトランスミッションに直上搭載した機電一体構造などにより、車両搭載性が向上しました。 今後も、BluE Nexus、アイシン、デンソーは、強みとノウハウを結集し、小型、高効率、低コストの製品開発を進めていきます。また、BluE Nexusを通じて、あらゆる電動車に製品を搭載いただくことで、社会のカーボンニュートラルに貢献していきます。
BluE Nexusによるプレゼンテーション
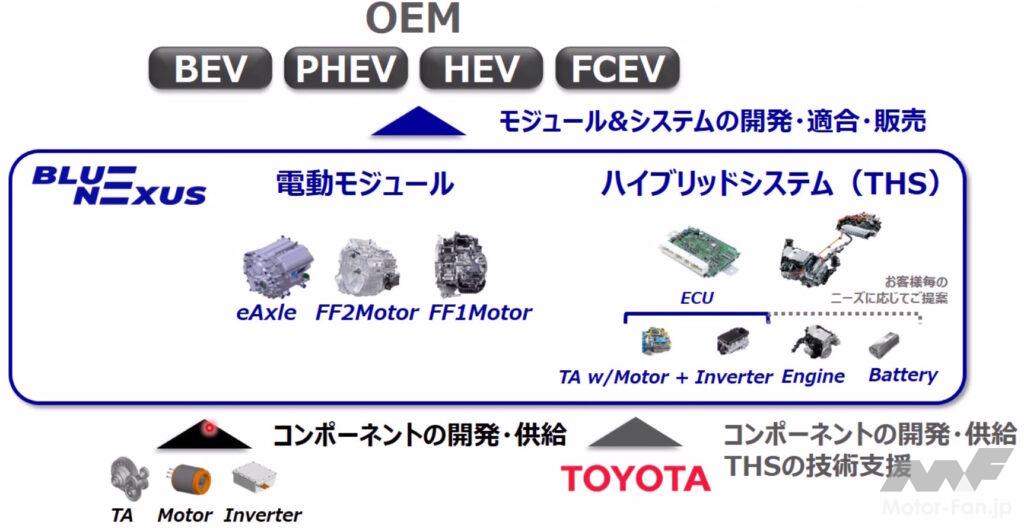
青い囲みがBluE Nexus(以下BN)の事業内容、中央が本日発表のFF1モーターハイブリッドトランスミッション。顧客=OEMからの要求をティア1としてBNが要求を受け、BNから各コンポ設計=アイシンとデンソーに要求を提示し、開発を行った。今回の場合は、デンソーがインバーター、アイシンがモーターとトランスミッション、それらを一体にしたアセンブリをBNが担う。なお、インバーターとの合体を含めたアセンブリの製造についてはアイシンが担う。
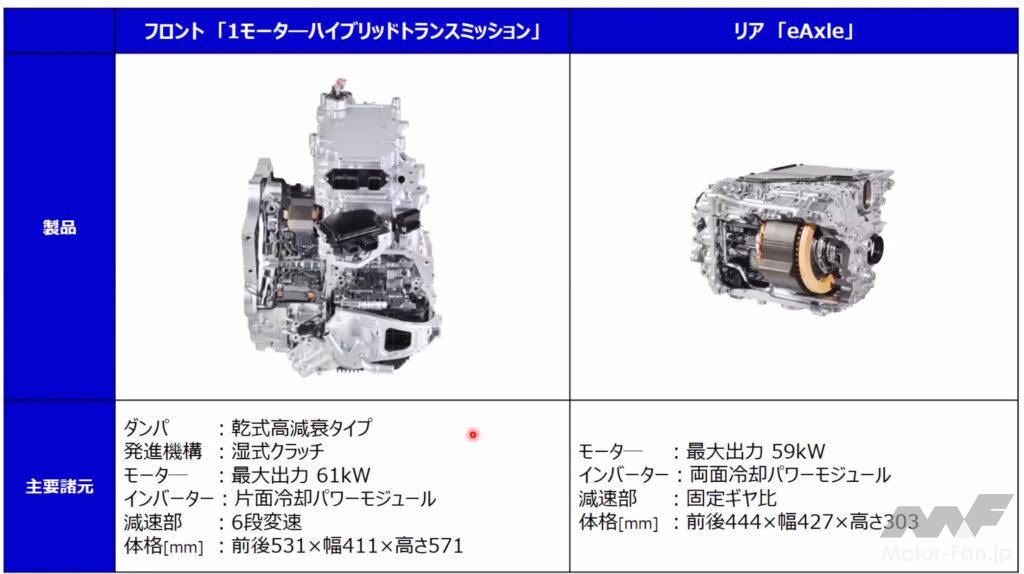
上が、クラウンに搭載された製品。左側がフロントに搭載される1モーターハイブリッドトランスミッション、右側がリヤに搭載されるeアクスル。なお、eアクスルは、bZ4Xに搭載されたeアクスルを流用している。
下段主要諸元と特徴。ダンパと発進機構については、エンジンと締結されるハイブリッド特有の項目で、ダンパーは大トルク対応をした乾式減衰タイプを、発進機構は湿式クラッチを採用した。モーターの最大出力は61kW。インバーターは片面冷却パワーモジュールを、より小型化するために採用した。減速部としては6段変速。
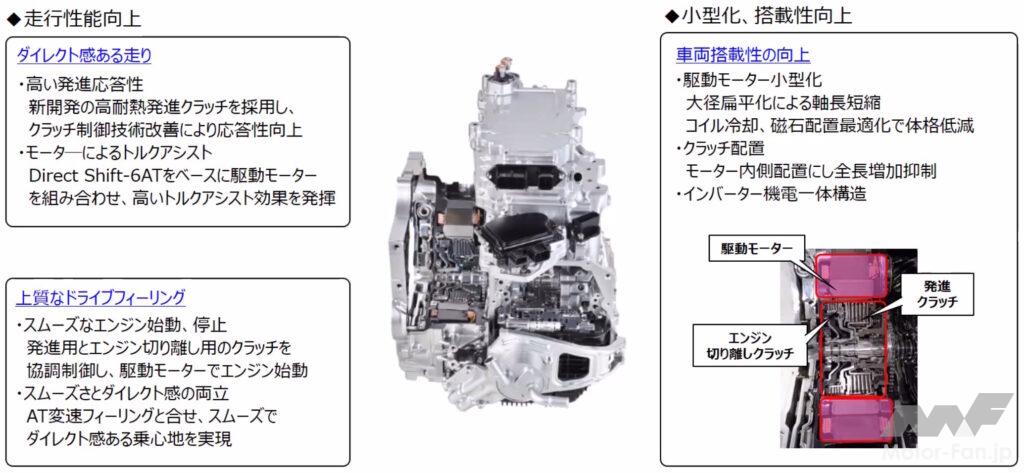
1モーターハイブリッドトランスミッションの開発の狙いには大きく2項目、走行性能向上と、小型化搭載性向上が挙げられる。まずダイレクト感ある走りの実現に向けて、高い発進応答性を実現するために、新開発の高耐熱発進クラッチを採用した。コンベンショナルなオートマチックトランスミッションではトルクコンバーターを採用し、流体を介したトルク伝達となっているが、今回はよりダイレクトな発進クラッチを採用した。さらにその発進クラッチの制御技術の改善により、応答性を高めている。
モーターによるトルクアシストは、ダイレクトシフト6ATをベースに、新開発した駆動モーターを組み合わせ、高いトルクアシスト効果を発揮している。アクセル操作に対してレスポンスよくトルク伝達することで、ダイレクト感ある走りを実現した。
続いて上質なドライブフィーリングについて。スムーズなエンジン始動/停止を行うために、今回、発進用のクラッチと切り離しのクラッチ二つのクラッチを採用。これらのクラッチを協調制御することで、駆動モーターにより、車両の走行状態によらずショックなくスムーズにエンジン始動することができた。
続いてスムーズさとダイレクト感の両立について。AT変速フィールと合わせ、スムーズでダイレクト感ある乗り心地を実現した。上の項目でダイレクト感ある走りを実現したという説明をしたが、ダイレクト感を追求していくと、ショックやギクシャク感に繋がる懸念もある。エンジン始動/停止、変速時のクラッチ制御技術により、発進需要をコントロールして、スムーズさとダイレクト感を両立した。
(以上、株式会社BluE Nexus システム開発部 主査・表 賢司氏)
アイシンによるプレゼンテーション
MG、エンジンの切り離しクラッチ、発進クラッチ=発進デバイス、そして変速部について。今回のFF1モーターハイブリッドユニットの構造的な特徴として、左上の模式図にあるように、エンジン切り離しクラッチと発進クラッチを分けている。それらをMG=駆動用モーターの前後に搭載する。この構造にすることで、車両の停止状態、または走行中、いかなる状況においても、駆動用モーターでエンジンが始動できるようにした。
続いて、開発のポイントとなる織り込み技術について。まず発進クラッチは、既存のATのトルコンから置き換えるものであり、ドライバーのアクセル操作に対応して期待通りの応答性が必要とされる。それを実現するために油圧センサーを採用した。この油圧センサーでリアルタイムに油圧を補正することで高い応答性を実現している。また、この発進クラッチと、エンジンとの切り離しクラッチ、そして駆動用モーター、これらを協調制御することで、スムーズなエンジン始動と停止を実現している。
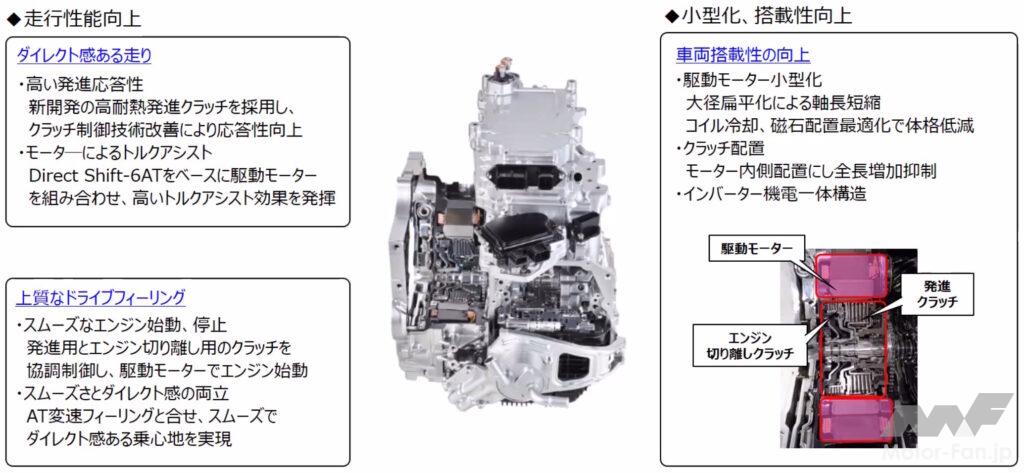
続いて変速について。今回の1モーターハイブリッドユニットは、変速部に6速ATを採用した。今までアイシンで培ってきた制御技術、変速制御の技術、そして今回エンジンと併用して駆動用モーターを積極的に活用することで、滑らかでダイレクト感のある変速を実現している。
次に小型化技術について。FF用(横置き)なので、限られたエンジンルーム内に搭載することから全長アップは致命的になる。そこで今回、駆動用モーターの中に、ふたつのモータークラッチを入れ込んだ。
エンジンは460Nmと非常に大きなトルクであり、それを受け持つこのクラッチをこの小さなスペースに織り込むとなると、熱的な課題が出てくる。そこを解決するために、高電圧の電動オイルポンプでの大流量潤滑制御によって熱的な課題をクリアし、この配置を実現した。
もうひとつ小型化技術として、駆動用モーターの全長の短縮を実現した。こちらは、まずコイルエンドの高さを抑えるために、同芯カセットステータという構造を採用している。これにより、コイルエンドの高さを抑えつつ、さらに磁石の配置を最適化することでモーターの積み厚自体も低減し、モーターの体格を低減している。
最後に車両コスト低減について。今回のユニットは変速部に6速ATを使っていることから、コンベンショナルなユニットとの部品の共通化、製造ラインの共通化を図ることで、コスト低減に繋げた。車両側の部品の低減も実施し、エンジン切り離しクラッチと発進クラッチを分けることで、走行中のエンジン始動を可能にしている。これにより、車両側の始動装置=スターターの削減を可能にした。
(以上、株式会社アイシン HV技術部 グループ長・前塚慎吾氏)
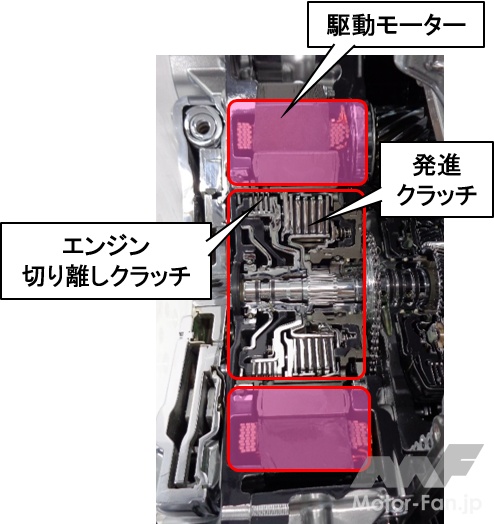
駆動モーターの生産技術について。今回採用した「同芯カセットステータ」は、従来ステータ=SCステータに対して軸長を約13%程度低減することができた。SCステータが軸方向に溶接するのに対し、同芯カセットステータは径方向に溶接する構造とした。溶接の継手方向を変えることで軸長を低減できている。
これを実現した生産技術は大きく二つ。一つ目がカセットコイル成形、二つ目がコイル拡張組付技術。
まず、カセットコイル成形技術について。従来は、セグメントコイルというU字型のコイルを485個、円環状に並べる構造としていた。この場合、溶接点数が480ヶ所と非常に多く、その溶接の加工スペースを取るためにどうしても軸方向に溶接継手を配置する必要がある。それに対して、今回コイルを三次元的に一本のコイルで成形するするカセットコイル技術を開発した。これによって従来5本のセグメントコイルであったものが1個のコイルになり、結果96個のコイルを円環状に配置することでステータにすることができる。溶接箇所も96ヶ所になり、その減った溶接箇所を径方向に配置することができるようになった。
もう一点がコイル拡張組付。カセットコイル構造にすると、従来のように軸方向からオイルをコアに組み付けるということができなくなる。そこで、今回はコイルを最初にコアの内径側にセットし、それを径方向に変形させながら組み付けるという新しい技術を開発した。
組み付け前は小さい細長い六角形のコイルとし、これを径方向に広げながら組み付けていく。このときにコイルの六角形の上下の山が広がっていきながら、だんだん太った六角形になっていく。この形を制御する拡張技術を開発することで今回の軸長低減を達成した。
(以上、株式会社アイシン 第1ユニット生産部 主幹・佐藤真吾氏)
デンソーによるプレゼンテーション
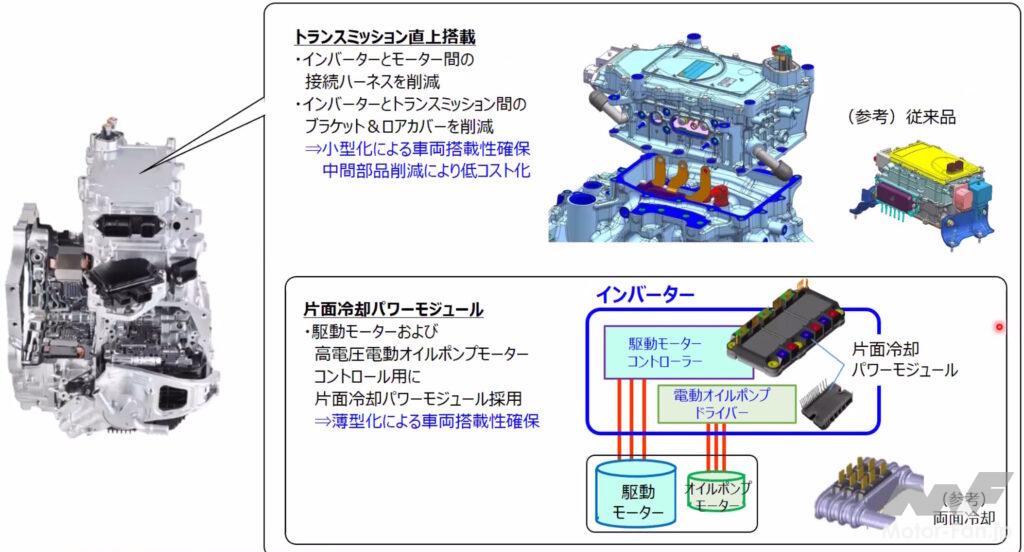
続いて、インバーターについて。インバーターの特徴としては二つ。まず一つ目は、トランスミッション直上搭載で、トランスミッションの上にボルトでインバーターを固定するという構造をとった。従来構造の、インバーターとモーター間の接続ハーネスの削減、さらにインバーターとトランスミッション間のブラケットおよび下側のロワカバーを削減でき、小型化による車両搭載性確保、中間部品削減による低コスト化を図ることができた。
ふたつ目の特徴が、片面冷却パワーモジュールの採用。駆動モーターのコントローラーおよび、高電圧電動オイルポンプモーターのドライバー、それぞれに片面冷却パワーモジュールを採用し、デンソーの特徴である両面冷却のインバーターに対して薄型化を図ることで、車両搭載性を確保した。
(以上、株式会社デンソー エレクトリフィケーション機器技術1部 担当課長・大村伸治氏)