近年はトルコンの代わりに電動モーターを備えたHEV(ハイブリッド・エレクトリック・ビークル)用のステップATも登場しているが、まだ多くのステップATがトルコンを装備する。そしてその作り方は、最新技術を駆使した超精密加工。トルコンは「精度が命」なのである。
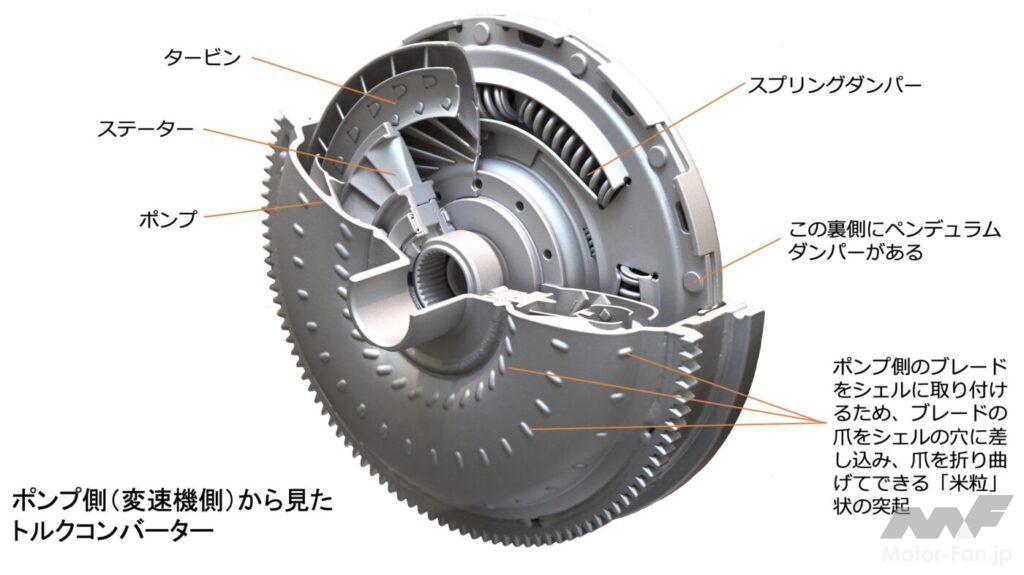
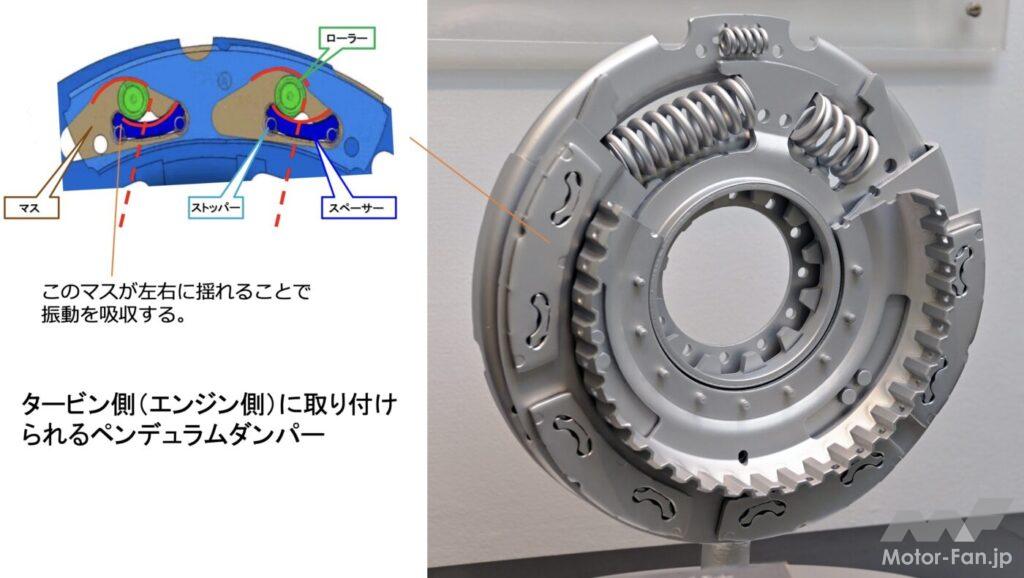
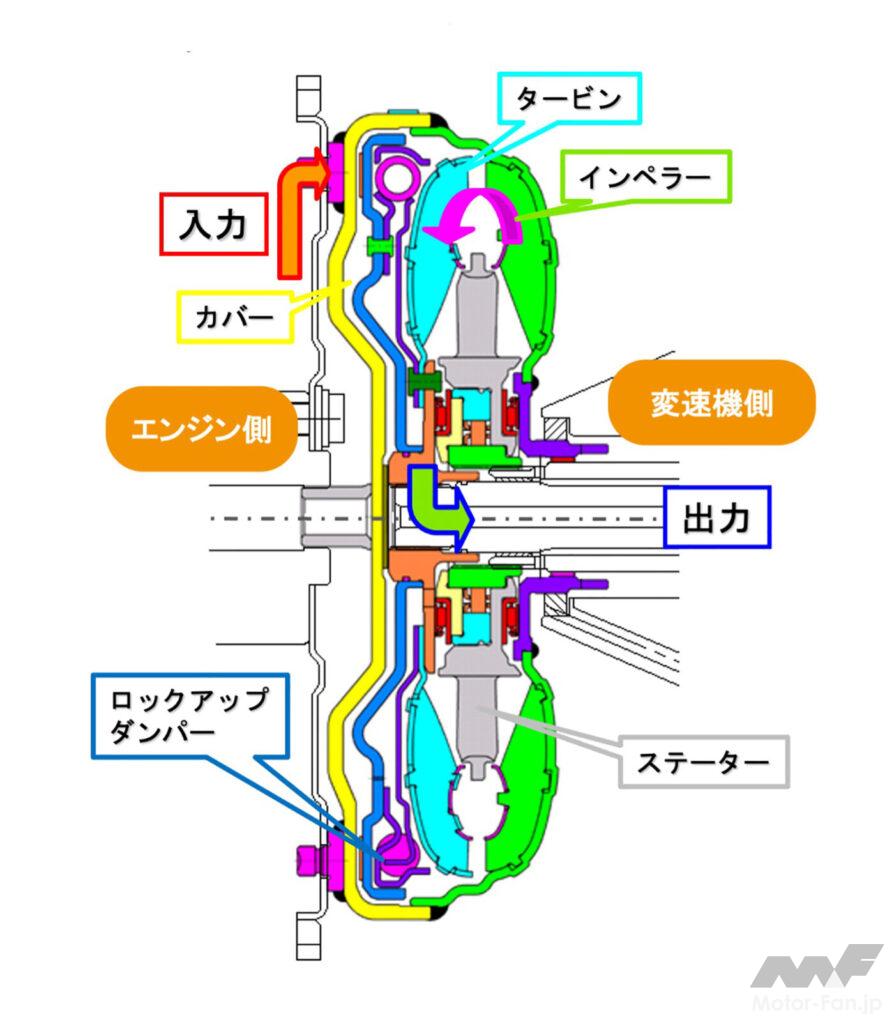
ヴァレオカペックジャパンのトルコン製造ラインを取材した。もともとはユニシアジェックス(現・日立オートモーティブシステムズ)の時代にトルコンのコンポーネンツを生産していた神奈川県・厚木市の工場であり、現在はフランスのメガサプライヤーであるヴァレオ傘下のバレオカペック、その日本法人であるヴァレオカペックジャパンが所有する工場だ。
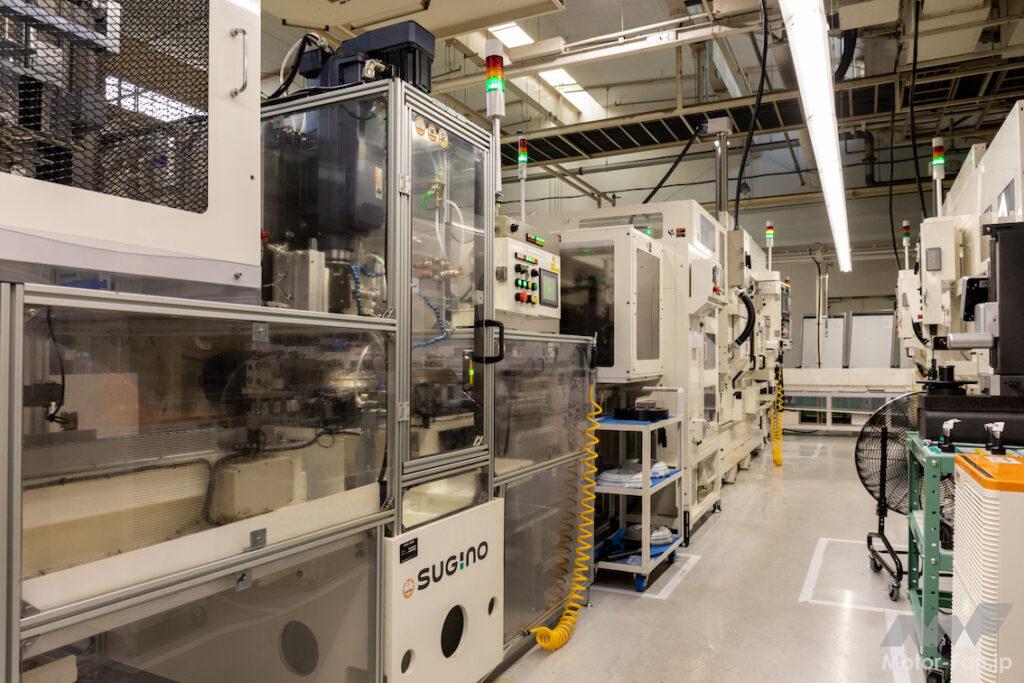
ヴァレオではトルコンの設計から製造までを一貫して行なっている。金融業界やメディアの間には製造設備を持たないファブレス(製造しない)企業を礼賛する風潮があるが、設計から製造までを一気通貫で行なうからこそ、性能と信頼性と、製品に万一何かあった場合の素早い対応が約束される。ファブレス企業を礼賛し従来からの設計・製造一貫企業を「ムダな設備を抱える企業」と見るのは大いなる偏見。設計専門のファブレス企業が外部に生産委託をした製品は、過去の例を見てもトラブル対応が「伝言ゲーム」になるケースが少なくない。
設計どおりに製造することは、じつはとても難しい。設計図面のとおりに製造すると機能・性能が微妙に保証されないとか、いま使える生産設備ではどうしても設計図面どおりに製造できないとかいったズレは、ほとんど必ずと言っていいくらいの確率で発生する。その「小さなズレ」を修正し、製造できるように書き換えた図面が製造図面であり、ものづくりの現場では必ず製造図面が用意される。いま使える生産設備にフィットするよう、性能・機能は変えずに設計図面の細部を変更するのだ。
この図面書き換えは、設計チームと製造チームの共同作業になる。機能・性能を落とさずに、余計なコストをかけずに、計画どおりの数をスムーズに量産できるよう製造方法を工夫し、それを設計図面に取り込む作業だ。そして、機能・性能もコストも妥協しない製造方法は生産技術部門が考える。
ヴァレオカペックジャパンでこの作業を担当するのが製造部門であり、各工場に製造部門がある。トルコン生産ラインを担当する製造部長・曽根利晴氏はこう言う。
「トルコンは生産技術者にとって非常におもしろい部品。構成部品の半分以上が熱処理を必要とし、接合方法も数種類におよぶ。熱伝導率もヤング率も違う素材を加工し、同じケース内に入れて機能と精度を保つ。ここが特徴的で、言ってみれば製造技術の見本市のような製品がトルコンだ。しかも、現在のトルコンはショックを吸収するダンパーの搭載が必須で、そのためポンプ/タービンはどんどん薄型になり、作りにくくなっている。部品同士の隙間もほぼ限界まで狭くなった。しかしトルコンの外形は大きくできない。どんどん増える機能を、従来型と同じか、あるいは小さな筐体の中に成立させる製造技術はチャレンジングであり、我われ生産技術部門にとっては腕の見せ所だ」
日本でヴァレオカペックが生産するトルコンは、ペンデュラムダンパーというヴァレオ独自の振動低減メカを組み込んだものだ。いまどきのステップATは、昔と違って「流体継手」というトルコンの基本機能を使うのはほぼ発進時だけというのが主流だ。発進し、1速ギヤでクルマを引っ張った後は、2速にシフトアップするかしないかのあたりでトルコンの動きを止める。これがロックアップだ。トルコンの動きを止め、エンジンとステップAT内のギヤを直結にする。直結だから燃費がいい。ATがズルズル滑るような感触もなくなる。
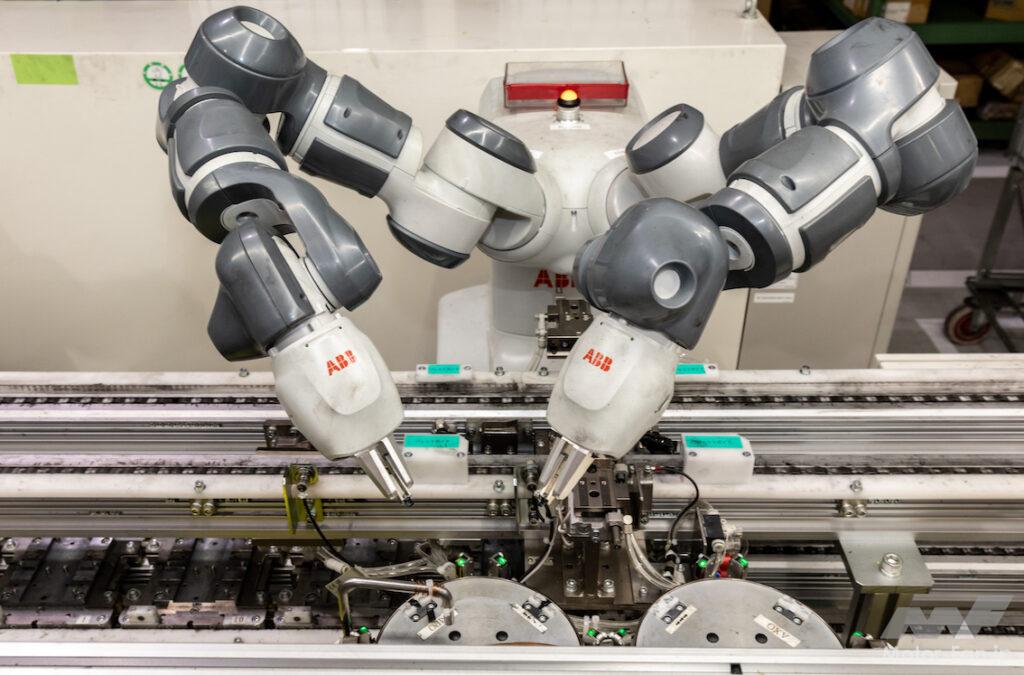
トルコンを滑らせることでトルクを増幅させる効果を得ることがかつてのステップATでは当たり前だったが、いまどきは「即ロックアップ」「なるべく長い時間ロックアップ」が主流だ。しかし、ロックアップする瞬間には振動が出る。せっかくスムーズな変速をしてくれるトルコン付きATなのに振動が出てしまっては台無し。そこで、ロックアップ時の振動を吸収するロックアップダンパーが考案された。
通常、このダンパーはスプリングだが、ヴァレオは「オモリ」を振り子のように揺らすことで振動を吸収するペンデュラムダンパーを開発し、通常のスプリングダンパーとセットで使う。このペンデュラムダンパーを、従来と同じ寸法のトルコンサイズの中に組み込む。そのために製造技術部門はさまざまな工夫を注いだ。
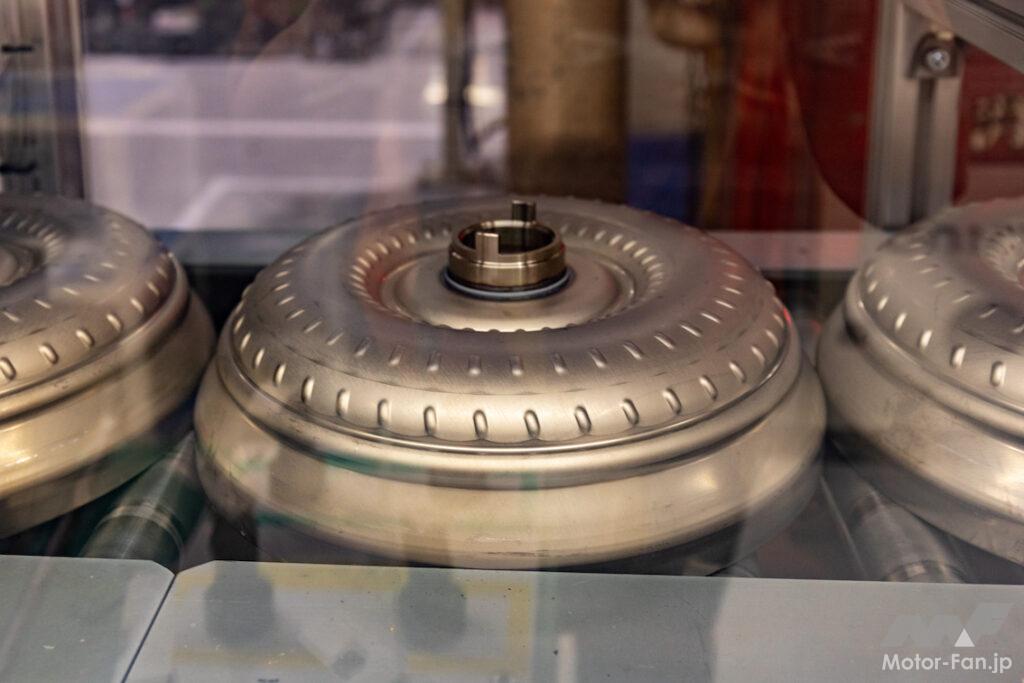
そのひとつが「バランス取り」だ。ホイールにタイヤをセットするとき、何グラムかの小さなオモリをホイールに貼り付ける。タイヤもホイールも、製造段階では「完全な円形」になるよう細心の注意が払われるが、誤差はゼロにはならない。誤差のある回転体同士を合体させるには、合体させた状態で回転がブレないよう重量バランスを取る。この作業はトルコンでも行なわれる。
「タービン、ステーター、ダンパー、ペンデュラムの状態でそれぞれバランス取りを行なう。タービンはプロジェクション溶接でオモリを付ける。ステーターはアルミ製なので削りでバランスを取る。トルコンAssy(アセンブリー)としては、タービンとステーターを固定した状態でバランス取りを行ない、スポット溶接でオモリを取り付ける」
曽根部長はこう説明してくれた。つまり、回転する部品のすべてが、まず単体として「ブレなくきれいに回転する」ようバランス取りを行なう。そして、必要な部品すべてを組み付けた状態でもバランス取りを行なうのだ。
「ペンデュラムダンパーだけは、正しく機能するかどうかの性能確認が従来とはまったく違った方法で行なわれる。小さな振り子状のマスが揺れることで振動を吸収するが、左右に(円周方向に)動くマスを同期させて計測しないと正しく組み付けられたかどうかを確認できない。この測定方法の開発が難しかった」
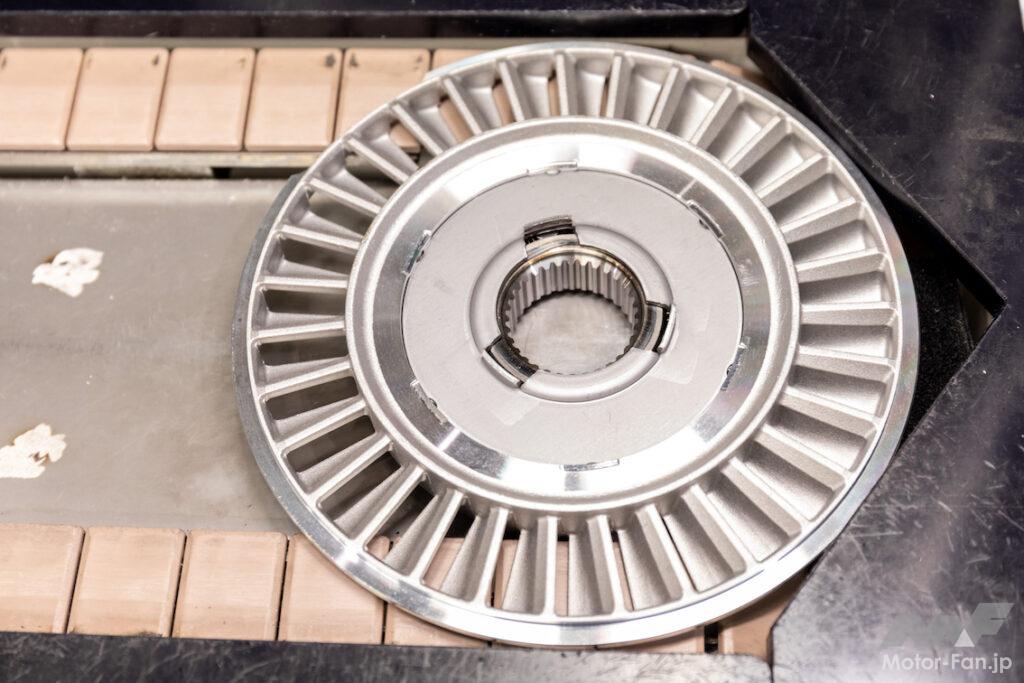
トルコンの中心部となるタービンとポンプは、ドーナツを半分にスライスしたような形状のハウジング(ヴァレオカペックではシェルと呼ぶ)内にブレードを固定してある。ブレードから出ている爪をシェル側の穴に差し込み、爪を折り曲げて固定し、ブレードとシェルの隙間が密着するよう、銅部品をセットして熱処理炉に入れる。
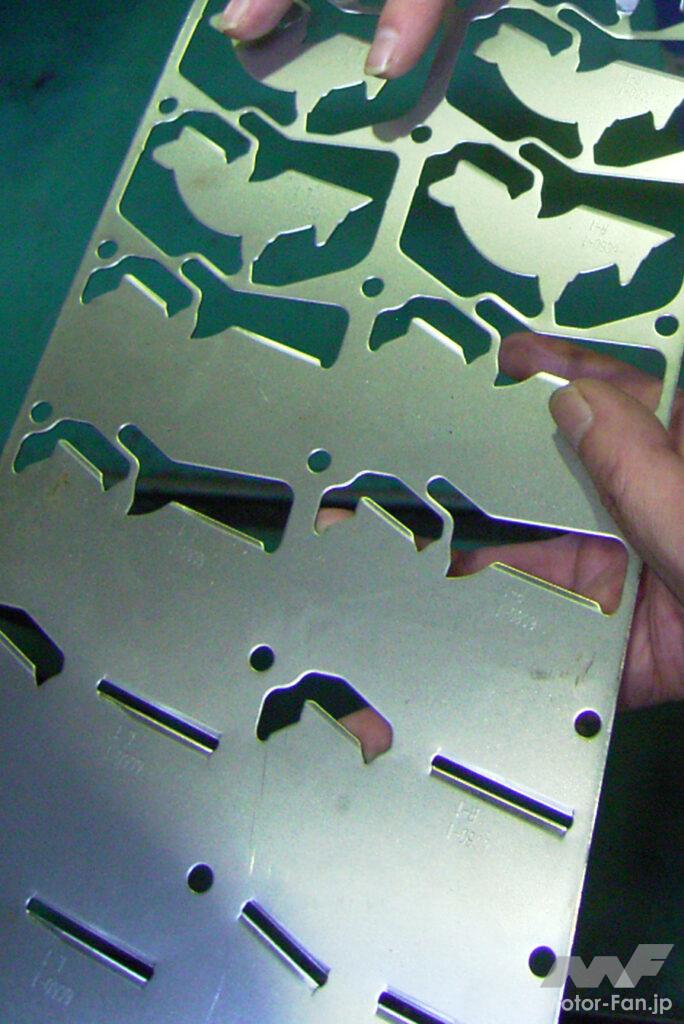
ブレードの素材は1.2mmだが、シェービング(研ぎ出し)してあるところは手が切れそうなくらいに薄い。1mm以下だ。ブレードの製造工程は取材できなかったが、べつのトルコンメーカーで撮影した写真を参考までに載せておく。薄板を6〜8工程で連続加工し、打ち抜きと成型を行なう。2秒に1個くらいの速度で自動加工機からブレードが出てくる。
トルコンの外見で特徴的なのは、ぐるっと円周上に並んだ「米粒」のような凸部分だ。これはブレードの爪を折り曲げ、隙間に銅が流れ込んでできたものだ。この「米粒」の形も「微妙に変化している」と曽根部長は言う。
「シェル外側はローリングで爪を曲げる。折り曲げ形状も微妙に変わっている。ブレージングするとわからないが、Rの大きさと折り曲げる角度は厳しくなってきた。昔は爪を曲げてがっちりくっつけ、ベタッと密着させていたが、現在は爪を折り曲げるときに微妙にRを付けて隙間を設けている。薄肉ブレードなのでパキッと折り曲げてしまうと強度が落ちるからだ。隙間の部分には銅が入り込んで埋まる」
見ていて「なるほど」と思う。ブレードの厚みは前述のように1.2mmしかない。10年前のトルコンはもっと厚かった。
タービンと向き合うポンプ側のシェルもタービン同様にブレードを埋め込んで作られるが、回転受けの部分となるポンプハブはフリクション溶接(FSW=フリクション・スクリュー・ウェルディング/摩擦攪拌溶接)で取り付けられる。約1万rpmくらいで高速回転させた工具を使って金属の表面を「溶けるか溶けないか」のあたりまで流動化させ、金属組織そのものを融合させるという方法だ。
「ブレージングしたシェルとポンプハブは、従来はMag溶接していたのだが、1000台に1台以下の確率でリーク(漏れ)があった。FSWは母材同士がくっつくのでリークがほぼゼロ。ポンプハブを取り付けたら外周をバニッシュ仕上げし、これで面粗度を出す。そのあとベアリングローラーで面を潰してならす。組み付ける前に洗浄、ブロー乾燥、目視確認する」
タービンとポンプはトルコンのコア部品であり、回転は「極めてなめらか」でなければならない。だから製造にも気を遣うのだ。そして、タービンとポンプの中間にステーターが入る。
「ステーターは転造で作られ、高周波焼き入れなど加工の済んだ状態で納品される。これにアウターレースという部品を取り付けて圧入するが、普通にアルミに鉄を圧入するとアルミが割れてしまうので、アウターレースの外側に歯が切ってあって、アルミを切りながら圧入するようになっている。ここで切り粉が出るが、切り粉は一カ所に溜まるようにして外に漏らさない。溜まったところで残さず吸い取る」
このようにして、重さも形状も素材も違う回転体を高精度で仕上げ、ひとつの筐体の中に組み込み、トルコンは完成する。エンジンが7000rpmになればトルコンも7000rpmで回る。ブレずに回る。最後に全体バランスと取るときにプロジェクション溶接されるオモリは約5グラムだった。14グラムなら規格内らしいが、手で持てばずしりと重たいトルコンAssyが、わずか5グラムのバランスウェイトによる修正で完成する。
曽根部長はこう言った。
「トルコン製造は全部で約80工程。溶接だけで5種類を使う。一般的なMag(ガス)、強度が必要で溶接部分が細かい場合はTig、できるかぎり変形を抑えたいときはFSW、細かい部分溶接でスパッター(火花)が嫌われるところは抵抗接またはスポット溶接。加工は旋盤、マシニングセンター、ミーリング、研磨,バニッシュ(鏡面加工=シールリングが入るようなところ)、カシメ(リベット/圧入/ローリング)で行なう。そして、正しく加工・取り付けができたかを確認する測定技術。トルコンは昔から存在するステップATのための部品だが、いまの製品は超精密機械だ」
精度の高いトルコンをロックアップ状態で使うと、ステップAT全体の動力伝達効率は93%程度以上になる。もはやMTと遜色のない効率だ。これは作り続けてきたからこその成果であり、技術の継続がいかに大事かがわかる。