目次
モーターファン・イラストレーテッド vol.117「エンジン回転系部品大図鑑」より転載
原理原則を究めれば、量産もF1も基本は同じ
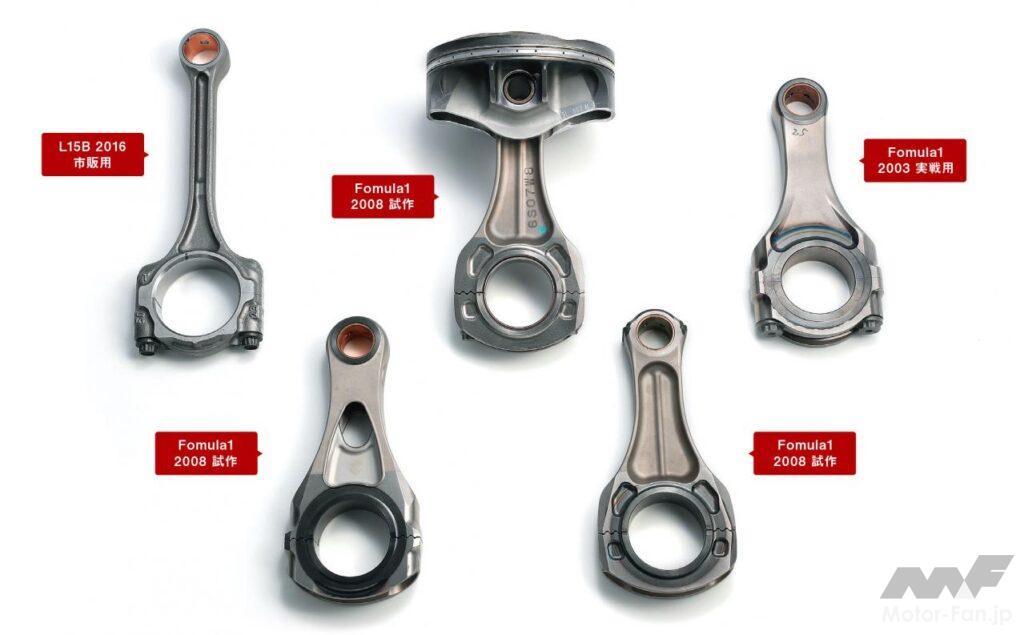
量産コンロッドのキャップの合わせは「かち割り」だが、08年のF1コンロッドは「ウェイビー」。第3期(00年~08年)初期はノックピンを使用していたが、途中から切り換えた。結果、コンロッドキャップ組み付け時の位置ずれ精度が一気に良くなったという。ワイヤー放電加工によって処理。量産ピストンのクーリングチャンネルはトップランドとリング溝を守るのが主目的だが、第3期F1のピストンは天井中央が弱点だった。オイルジェットを複雑に進化させて冷やす努力と並行して、入れたオイルがすぐに出てこないような構造にもトライした。F1~量産~F1と経験したエンジニア氏は量産とF1について、「基本は同じ」だと語る。「原理原則を究めてしまえば、差異があるわけではない」と。
2008 実戦投入ピストン ピストン & 冠面 コンロッド
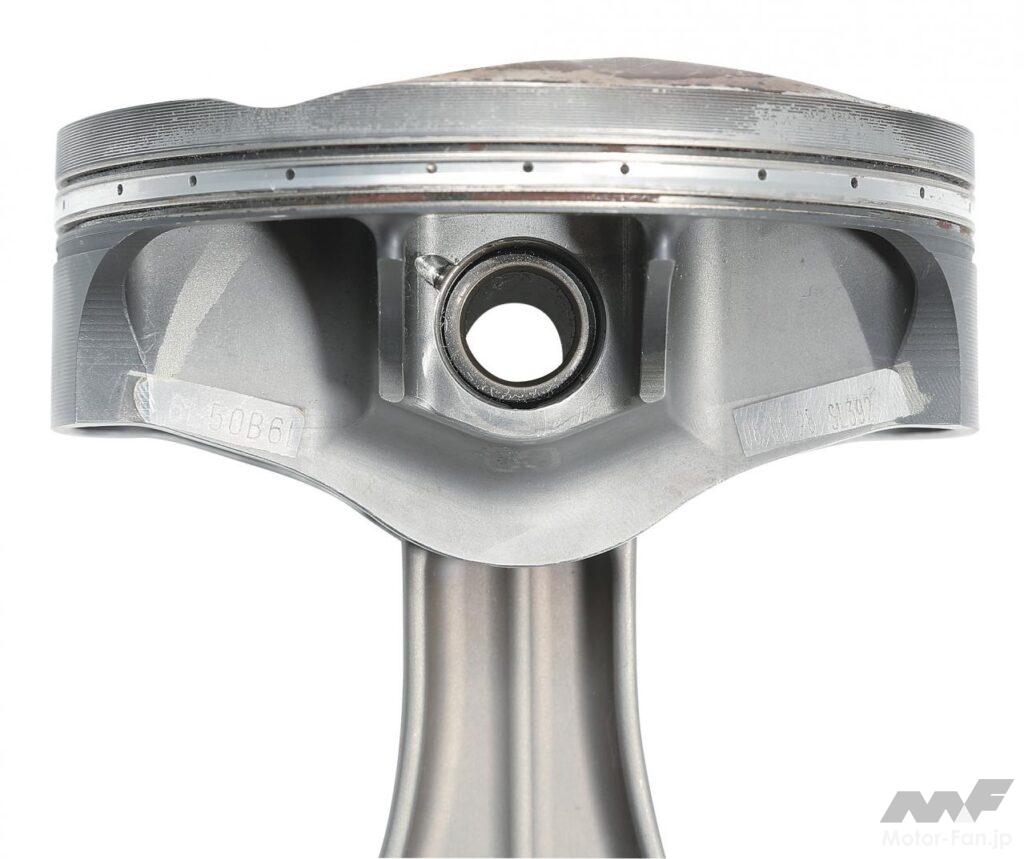
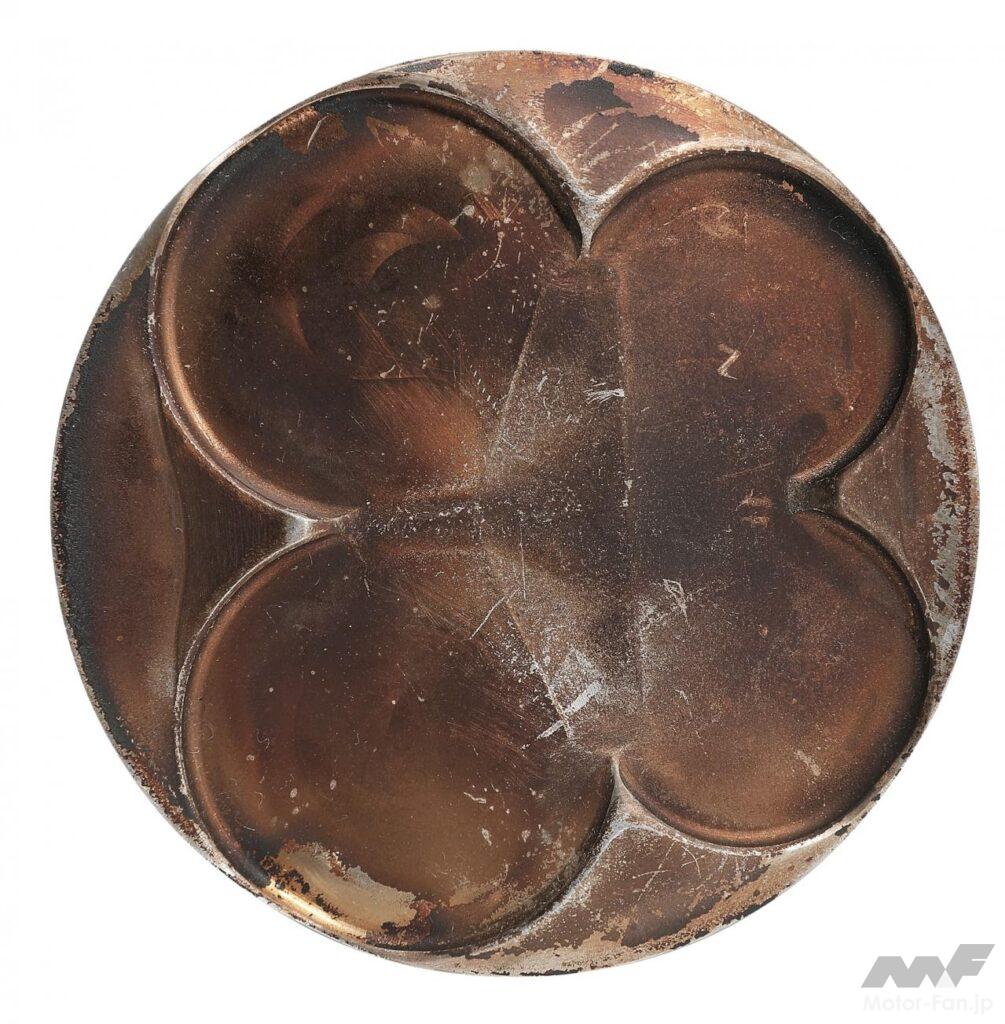
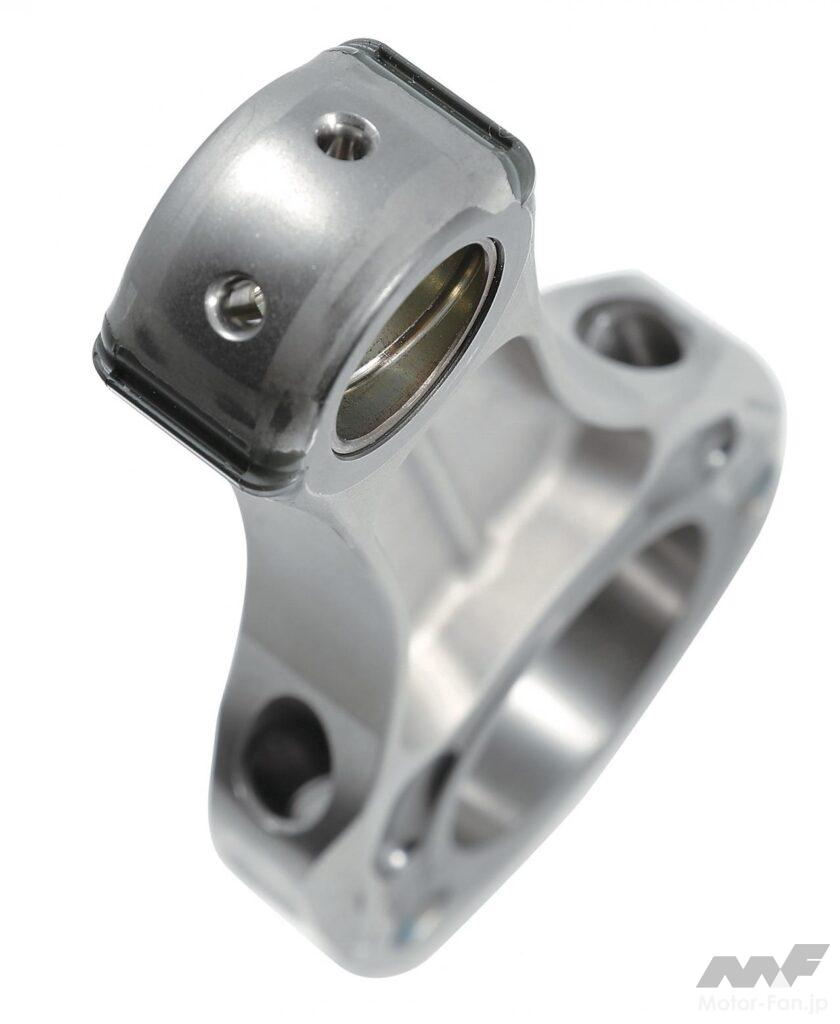
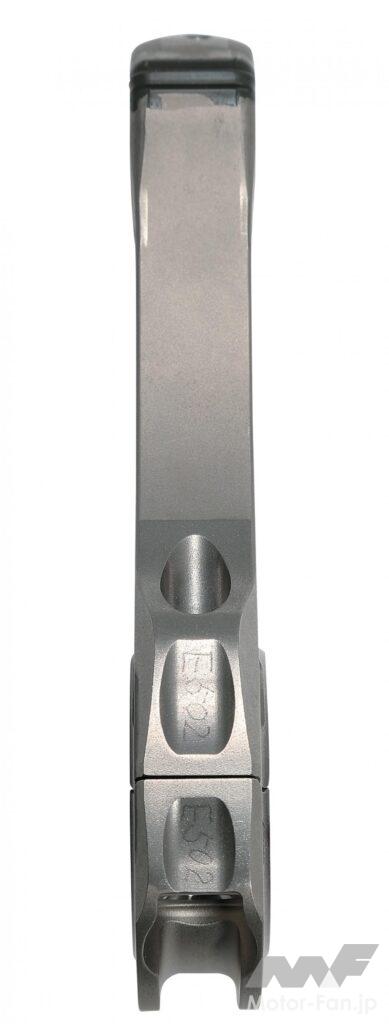
2003年実戦投入仕様 V10/2003
SPECIFICATION
ストローク 40.52mm
クランクピン径 34mm
ピストンピン径 17mm
小端大端中心間距離 102.3 mm
連棹比 5.049
小端部幅 18.8 mm
大端部幅 19.3 mm
重量 255g
上は中空断面形状のボックスコンロッド。SP700チタン合金を拡散接合して製作。05年に接合構造が禁止されたため、以後はI型形状に。右上は第3期最終年にあたる08年のコンロッド。棹部中央にある隆起の内部には、クランクピン側からピストンピン側に供給するオイルの通路(放電加工で製作)が設けてある。これを機能させるためにはメタルにも穴を開ける必要があるが、その結果、メタルの信頼性が犠牲になってはいけない。常時適用していたわけではなく、適用できる構造にしておいた。
2008年試作仕様 V8 /2008
SPECIFICATION
ストローク 40.52 mm
クランクピン径 34 mm
ピストンピン径 17 mm
小端大端中心間距離 103.1 mm
連棹比 5.089
小端部幅 18.7 mm
大端部幅 19.8 mm
重量 219g
2008年試作仕様 V8 /2008
SPECIFICATION
ストローク 40.52 mm
クランクピン径 34 mm
ピストンピン径 17mm
小端大端中心間距離 102.3 mm
連棹比 5.049
小端部幅 18.8 mm
大端部幅 19.1 mm
重量 256g
ホンダ第3期 F1エンジンのコンロッドと回転系部品の開発
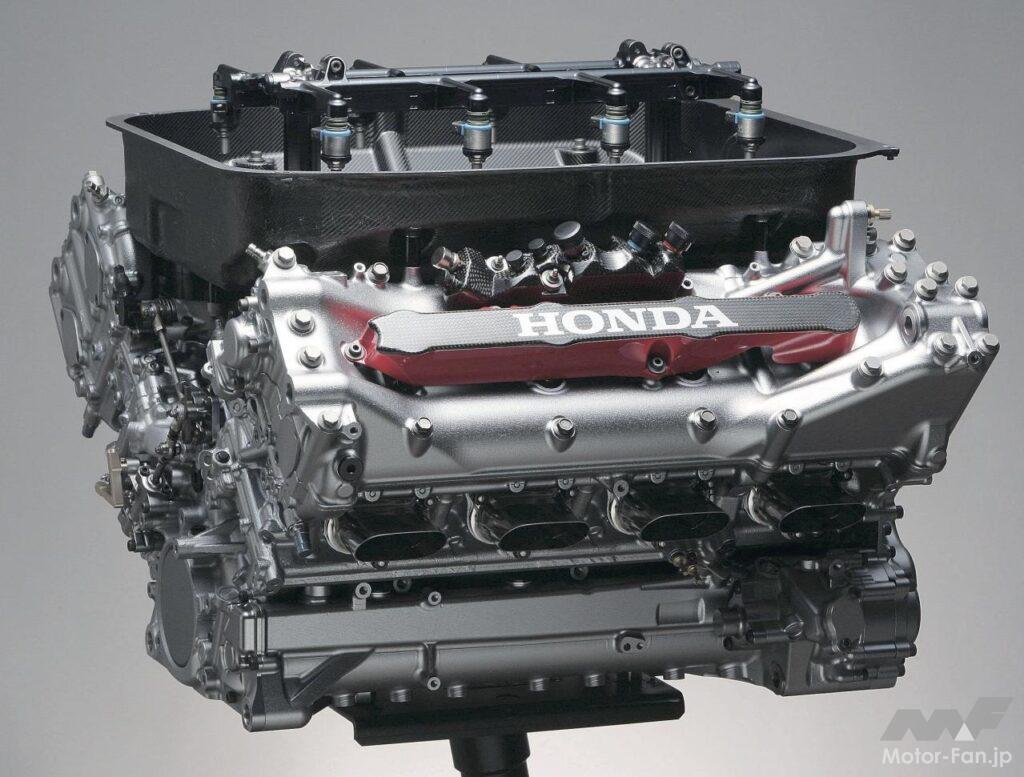
F1エンジンが比較的制限が少ない状況で開発できたのは、3.0ℓ・V10の最終年にあたる2005年までだった。ホンダのレーシングエンジン開発拠点であるHRD-Sakuraで、第3期(00~08年)途中からF1エンジンの設計に携わったエンジニア(第3期後、量産エンジン開発を経て現行F1エンジン設計に再登板)は、「究極のF1エンジンは05年」と言い切る。
F1エンジンの規定は06年に2.4ℓ・V8に切り替わったが、排気量とシリンダー数の変更を強いられただけでなく、材料や構造、寸法や重量に関する縛りが厳しくなった。例えば、ホンダはクランクシャフトのメインジャーナル中央部をフリクション溶接で接合する中空クランクシャフトを開発していたが、06年から中空構造が禁止されたため、実戦投入の機会を逃した。
コンロッドは05年に接合構造が禁止されたため、03年に開発した中空コンロッドをⅠ型に戻した。06年にはピストンに対するMMC材(メタル・マトリックス・コンポジット。実態はセラミックス分散強化のアルミ合金)の使用が禁止されたため、A2618改良材に切り換えた。
「MMCは強かったですね。とくに300℃を超えてからの強度がすばらしかった。しかも、強靱なのに変形を許す。ちょっと変形しただけでは壊れませんでした。(レース後に)天井が変形した状態で出てきたこともありました。通常の材料では割れてしまっていたでしょう。ただ、現在の技術があれば、MMCを使わなくても当時のMMCと同等の性能は確保できます」
なぜか。
「シミュレーション技術が格段に進歩しているからです。計算できるだけでは価値がありません。計算と実証を突き合わせて、シミュレーションの精度を上げなければならない。我々は幸いなことに第3期でさんざん壊した経験を積んでいますので、それをもとに突き合わせができています。それを量産に持っていって育て、現在のF1に生かしています。現在は手に取るようにと言ったら大げさですが、応力の分布、温度の分布、変形の状態がことごとく見てとれる。シミュレーションで何十通り、何百通りと出した仕様から最も優れたものを選び出す最適化設計システムも構築できています。だから、問題らしい問題はほとんど起こしていません」
量産部品との対比で言うと、F1のコンロッドは要求性能が異なる。07年に19000rpmの回転上限が設けられるまでは、常用20000rpmを目指した開発が行なわれていた。慣性過給とラム圧(走行風圧)を利用するため充填効率は120%を超えていたといい、NAとしては高い燃焼圧を発生していた。その高い燃焼圧(圧縮)に耐えるために骨格は堅牢にしなければならない。一方で、2万回転近いスピードで回っているため、強い力で引っ張られる。「1万Gは出ていた」というから、ピストンとコンロッド合わせて450gなら4.5tの力で飛んで行こうとする。その引っ張りを支えなければならない。
「問題になるのは棹部です。単純な引っ張りのみならず、クランクシャフトの挙動による影響を受けてねじれるからです。エンジンが1回転する間に2回ねじれる2次、これが非常に大きい。ピストン冠面を見ると、吸気バルブのリセスが楕円なのがわかります。当時は毎週のように耐久試験を行なっていましたが、バルブがあたるとそこを逃がす。それを繰り返しているうちにできた形が楕円形状でした。コンロッドを単体で試験すると、6~7tの引き圧に耐えるのだが、実機だと3.5tくらいで引きちぎれてしまう。当初はメカニズムがわからなかったのですが、高速度カメラを使った可視化などでわかるようになりました。理由はねじり共振です。±5度の範囲の振幅でねじり振動していたのです」
03年に開発した中空断面形状のボックスコンロッドは、軽量化を追求する目的もあって取り組んだ技術だったが、ねじり剛性を高めるうえでも非常に有効で、従来品に対し2.5倍のねじり剛性向上を果たしたという。
コンロッドに付随するメタルの耐久性確保にも苦労した。径と幅は軽自動車用エンジンと同等ながら、荷重は数倍、摺動速度は2.6倍、摺動抵抗による発生熱量は10数倍にも達する。とくに、大きな燃焼荷重を受ける上側メタルの耐久性確保に苦労したという。規則の変更によって開発は困難を極めたが、最終的にはシリコン添加銅合金に落ち着いた。
銅が持つ熱伝導性の高さを生かすために、背面圧を引き上げ、決して熱伝導がいいとは言えないチタン合金へメタル摺動熱を逃がす必要がある。だから、コンロッドボルトは強力に締め上げた。回転数の自乗で増えていく慣性力に耐えるよりもむしろ、メタル背面圧の要求から、強力に締め上げた。その結果、低粘度オイルでも深刻なダメージは発生せず、メタル焼き付きによる不具合はなくなった。