モーターファン・イラストレーテッド vol.193より一部転載
クランクシャフト、コンロッド、ピストン、バルブ、カムシャフト……ICE内部の可動部品をすべて組んだ状態のSKYACTIV-D 3.3がコンプレッションテスターに無人のコンベア輸送で運ばれてきた。部屋の中に入り扉が閉められる。ここでは燃焼室圧縮比とバルブ開閉タイミングが計測される。
上から6本の棒が降りてきた。センサーが仕込まれた棒だ。各シリンダーに上からセットされる。インテークマニフォールドとエキゾーストマニフォールドにはジグが取り付けられる。吸気側にはエアを送るパイプが見える。ジグをセットした状態が左の写真だ。ちなみに左ページ下の写真がジグをセットする前。金網とシートの向こうに、まだ3分の1ほどしか組み上がっていないSKYACTIV-D 3.3がいる。計測は生まれる前の儀式である。
この部屋に来る前に機械抵抗測定を済ませている。シリンダーブロックには電子ペンで番号が打刻されている。すでに識別番号を持った個体だ。4気筒シリーズはスタンプ刻印だったが、6気筒のブロックは重たくスタンプの反力も大きくブロックに負荷がかかる。そのためロボットがペンを持って刻印する電子ペンに切り替えた。
さて、いよいよ試験が始まる。
「クランクシャフトを外部の電気モーターをフライホイール側に連結し、200rpmで回す。吸気側のジグから空気が送り込まれ、ICEが吸い込み、排気側から吐き出される。そのときにどのタイミングで、どれくらいの空気が入り、どれくらい圧縮されたかを検出している。入り口と出口の間の圧力差を、上から降りてきた6本の棒の奥にあるセンサーで読む」
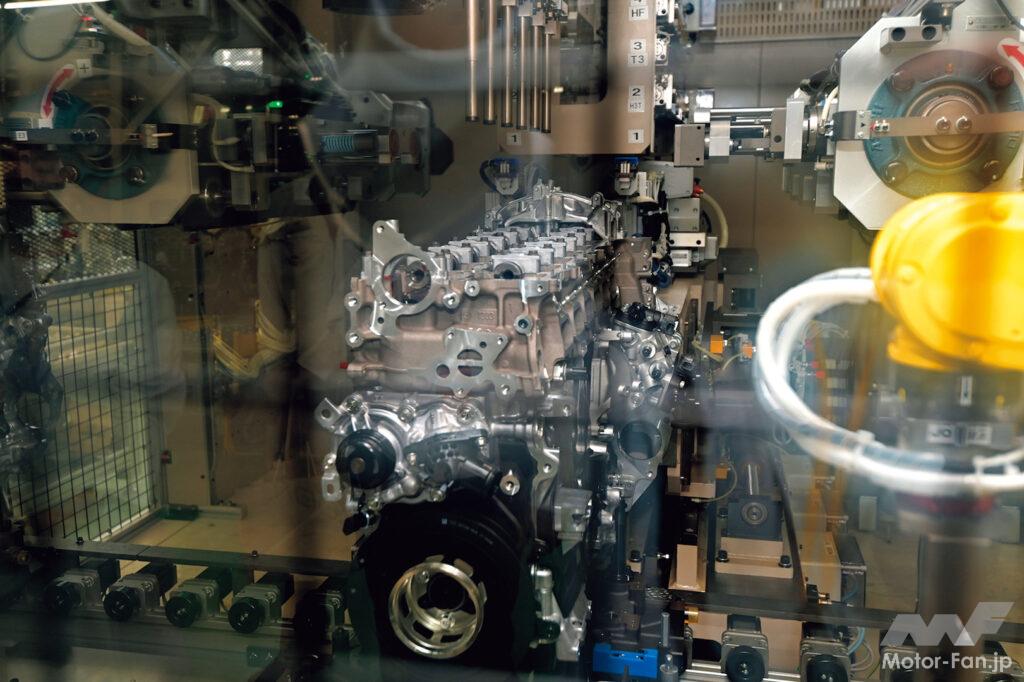
これはSKYACTIV初代から行なわれてきた試験だ。マツダは機械圧縮比を製造段階で精密に作り込むことにこだわっている。
「4気筒も6気筒もこの同じ計測機を使いジグだけ持ち替える。ガソリンICE(SKYACTIV-G)は点火プラグの位置で測る」
そう。これがいまのマツダの常識だ。ICE製造工程に専用の加工機や計測機はほとんどなくなった、ICEブロックの削り出しは全ブロック共通のマシニングセンターを使い、その日の気温や切削用モーターの発熱などによるジグの変位量まで見ながら自動加工する。この6気筒はどうなのだろう。4気筒と同じ加工機を使うのか。その部分は見せてもらえなかったが、初代SKYACTIV-G/SKYACTIV-Dの導入とともに一新された設備は汎用性と高精度で一皮も二皮も剥けた。だから、あれだけ高価な部品を使ったICEでも製造原価を抑えられた。
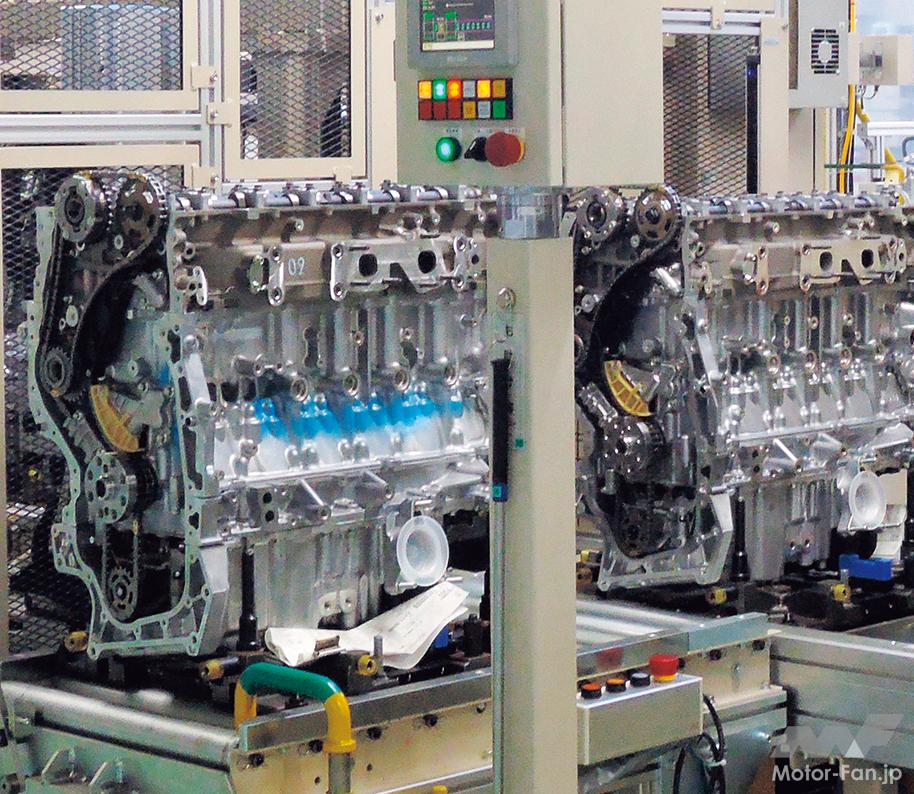
この方法にはオマケがあり、ずらり並んだ加工機の、「この日にはA機がよかった」「この季節だとC機がよかった」というデータを蓄積できた。車検・点検時にはICEごとの燃費・排ガスデータがチェックされる。シリンダーブロックを含むICEのほとんどの部品に2次元コードが刻印されており、燃費・排ガスが優秀な個体の製造データはすぐに呼び出せる。加工条件の微妙な差を追い込み、これを全加工機で共有すると、設計変更も改良もなしに燃費・排ガス性能が良くなるのだ。その意味では、マツダの工場は直結BtoCである。
SKYACTIV技術は初代からコモンアーキテクチャーを標榜していた。しかしそれは、単に異なるシリンダーブロックのボアピッチや部品を共通化するのではなく、設計時のキャリブレーションから製造段階まで、あらゆる段階でコモン=共通を貫いた。そこが新しかった。
こんどは6気筒だ。シリンダーライナーが6個あるだけでICEはカッコよく見える。理由はない。いかにもメカらしくてカッコいい。カッコいい代わりにシリンダー数が1.5倍になることでの製造要件の厳しさが加わる。製造ラインは6気筒と4気筒の混流、何が来ても作れるラインにする。床面に固定物を置かず、機種ごとの生産台数変動や機種追加に即応する。そんな製造現場を目指した。

いま、目の前のコンプレッションテスターから出て行ったSKYACTIV-D 3.3の「生まれる前」の個体は、このあとの工程で部品をどんどん身にまとい、油・水路機密性検査、油圧測定、負圧測定、部品機能動作試験を順次受け、最後に2,000rpmでのコールドテストを受けて電気系、吸排気系、VGターボの流量などあらゆる部分が保証され、車両工場へと送られる。
シリンダーブロックとシリンダーヘッドは隣接した場所で加工され、この4/6気筒組み立てラインに運ばれる。3つに分かれたコンベア搬送ステージ(セル工程)を経て、最終組み立てステージにやってくる。ここはAGV搬送であり、エリア全体の床面がデジタルマップ化されており、その上をAGVが移動する。
「現在、AGVはこのエリアだけ。ほかで使ってもメリットがないという結論だ。今後、生産機種が増えたりICEの機構が変わったりして既存ラインでは対応できなくなることを想定し、既存ラインにもこのAGVシステムを同じ制御でコストを抑えて導入できるようにチャレンジしている。その雛形のラインがここ」
ICEごとに製造に要する時間は違う。それを吸収するため、従来はメインラインから横に張り出したバイパスコンベアで作業時間を吸収していた。AGVなら走行ルートの調整でライン全体が伸縮可能になる。「コンベア生産のいいところは残しながら、安全性、品質確保、コストのバランスを考えたライン」だと言う。
AGV工程ではスタッフの前にAGVがICEを運んで来る。その順番は、最初にこの工場にシリンダーブロックが運ばれるときから決まっている。床にはAGVが停止するエリアが描かれている。これはAGVが回転するためだ。スタッフは青い床の上で作業を行なう。
「ICEを載せたAGVと、そのICEに必要な部品をキット化したトレイを載せたAGVはペアで動く。部品トレイもICE本体も、作業順に合わせて自動で回転する。なので床面に黄色と黒で描いたエリアにはスタッフは入らない」
どういうことか、と思って見ていたら、備品を順番どおりに組み付けるため、ツール(工具)もその順番で使う、ツールはスタッフの目の前にぶら下がっていて、使い終わった工具を戻すと作業終了の信号がAGVに送られ、自動的に回転して次の作業面がスタッフの目の前に来るという仕掛けだった。
「ん、あのベルトは何だろう」
スタッフは全員、同じ形のベルトというかウェストポーチのようなものを身に着けている。
「ツールに取り付けるアタッチメントや締め付け用のソケットなどを持っている。だから違う工程へ行ってもすぐに作業できる。工程ごとに追加で必要になったらそれも持つ」
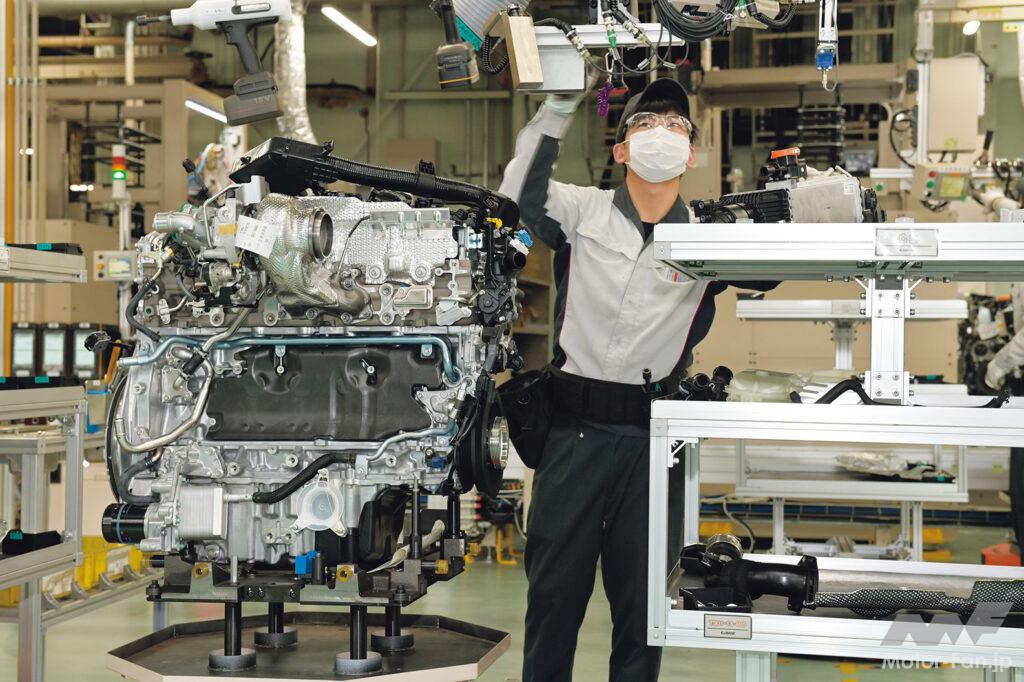
なるほど。日本の工場スタッフのユニフォームや携行品も少しずつカッコよくなってきた。しかし、見ているとAGVラインはスタッフひとり当たりの作業量がとても多い。
「幸い、スタッフがよく覚えてくれる」
AGVラインは最後の工程であり、これ以降は出荷検査だけだ。SKYACTIV-D 3.3を製品として送り出す工程はすべて人間の手作業になる。これが最後の儀式。SKYACTIV-D 3.3が、金属のゆりかごから旅立つ場所。AGVを見送るスタッフは、その立会人である。
筆者が「いいね」と思ったのは、車両工場と完全同期生産とは言っても、何かトラブルがあったときのためにほんの少しのストックを持っていたことだ。過去に筆者は300か所以上の工場を見て、完全同期は机上の空論に近いという持論に至った。そこはほどほどでいい。ほかは十分に節約してるのだから。