「鋳物」というと、多くの方が「ローテク旧技術」という印象を持たれるのではないかと思う。しかし、実際には正反対である。鋳鉄はハイテクである。
素材を溶かして溶湯状態にし、それを型に流し込んでカタチをつくる。しかし、溶かすものはさまざまな添加物の入った合金であり、添加物をどのようなタイミングでどんな順番で添加するかという部分だけを取っても素材の性質にまでさかのぼった研究が必要になる。しかもエンジンブロックともなれば形状は複雑であり、中子の形状や割り方、溶湯の流し方など最先端の冶金学的検証が要る。設計されたエンジンを設計図面のとおりに実物にするためには、製造部門の知見・経験が不可欠である。
トヨタブランドの量産第一号車である「トヨダA型」は、当時の豊田自動織機自動車部の作品である。エンジンの鋳物は現在の豊田自動織機本社がある刈谷で生産された。以来、半世紀以上にわたり同社は、エンジンをつくりつづけてきた。エンジン設計部門と生産技術部門と製造現場が一体になって「いいモノ」をつくる。日本のものづくりでは当たり前のことだが、同社の鋳物には「見所」がある。無駄な肉はびた一文たりとも盛らない。盗めるところからは寸法も肉も徹底して盗む。コストを抑えるために大胆な分割・締結に挑戦する。そうした前向きな「鋳物」である。
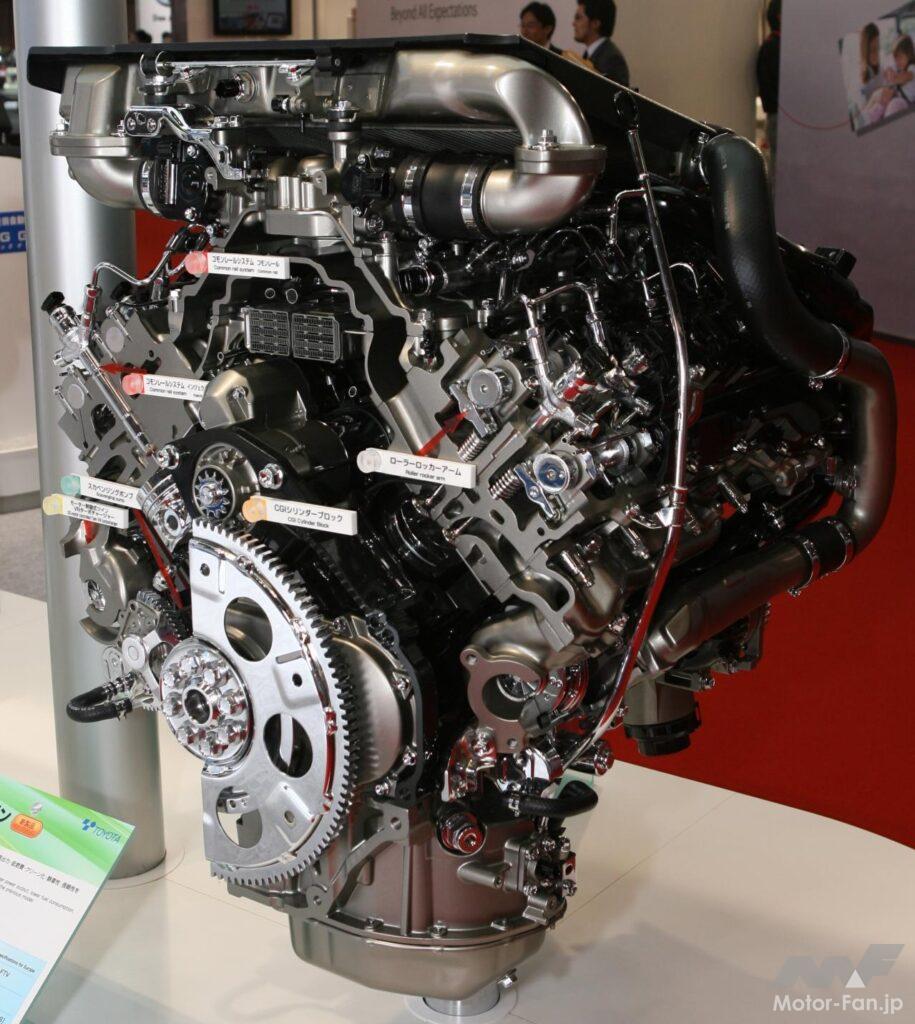
たとえば、ここで紹介するVD型エンジンは、ブロックにFCV(バーミキュラー黒鉛鋳鉄)を使用している。FCD(球状黒鉛鋳鉄)とFC(ネズミ鋳鉄)の中間的な芋虫状の黒鉛形状を持ち、引っ張り強度は350〜500MPa。鋳造が難しく加工性も悪いが、このディーゼルエンジンの筒内燃焼圧に適した強度を持ち、FCDほど品質過剰ではないことから採用に踏み切った。鋳造工程では、黒鉛の球状化率を20〜40%の狭い範囲に収めるため、添加されるMg(マグネシウム)の残留量をシビアに制御し、溶湯の中でのMg蒸発を抑えるためセリウムを添加する方法を考案した。加工性の悪さは鋳造寸法精度を攻めて乗り切り、切削速度を抑えて刃具の寿命延長に成功した。
こうした努力がディーゼルエンジンを支えているのである。
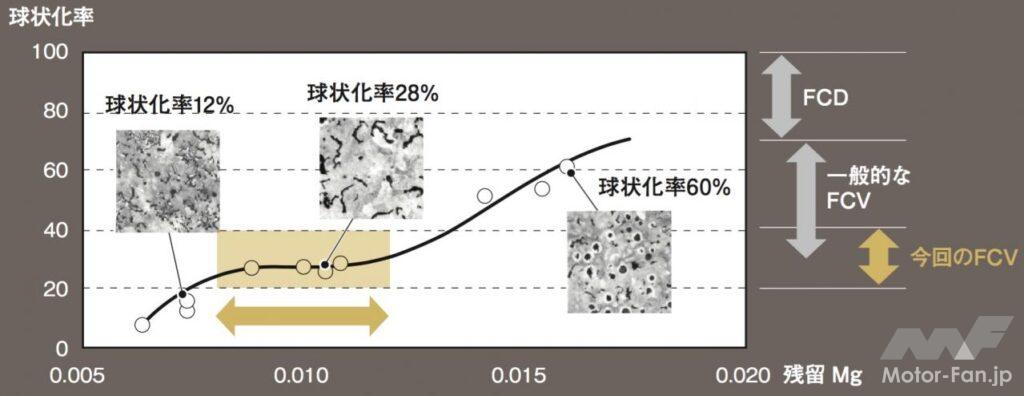
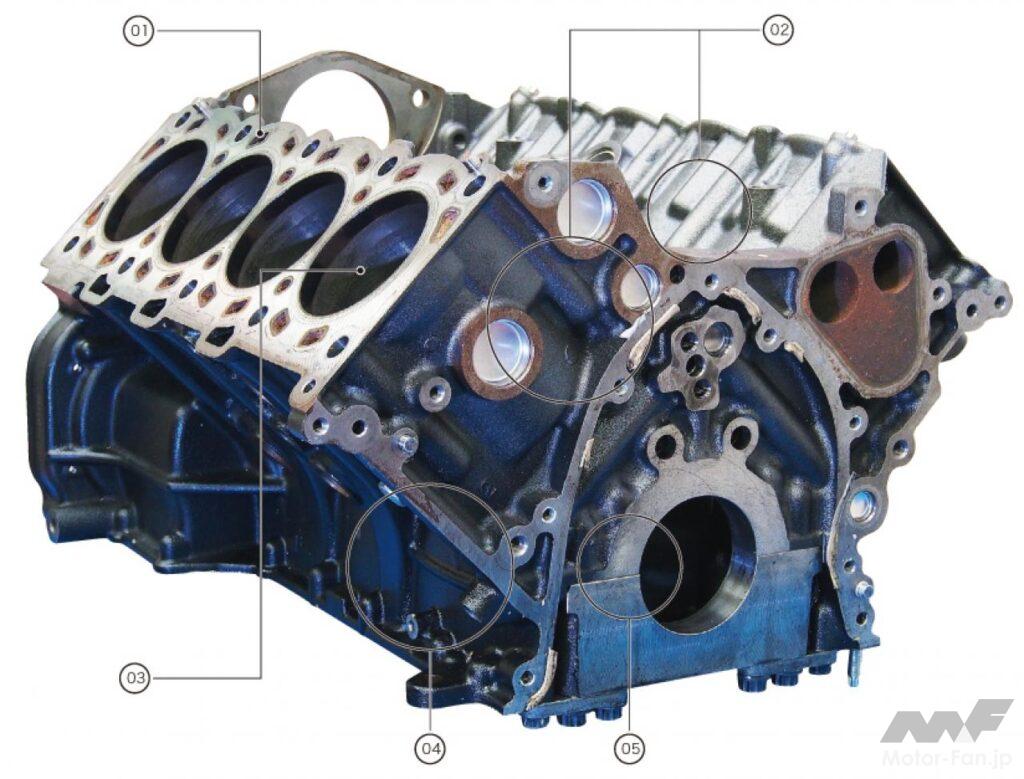
01:ヘッド面は球状化率25%
ヘッド面の硬度は230HV。水路が見えるオープンデッキ構造は現在のディーゼルエンジンの主流だ。この状態で見るとシリンダー側面が円弧状になっていることがよくわかり、ボア径86mmでもピッチをかなり攻めている。
02:徹底した薄肉化とリブ構造
ピストンが往復する部分にだけ冷却水の水路が鋳込まれている。リブを立て、量産できる限界まで薄肉化した。また、こうした部分は重力鋳造では最後に固まるため「鬆(す)」ができやすく、その予測も行なっている。
03:シリンダー内壁一体型
シリンダーライナーはなくボアはボーリング加工で仕上げる。この面もヘッド面同様に黒鉛球状化率25%、硬度230HV。ちなみにブロック質量は前の世代より30kg軽くアルミに匹敵する軽量化を達成した。
04:側面リブ構造の工夫
90度バンクの外側壁面は、冷却水路外壁をリブ構造に合体させたデザインである。引き締まった筋肉質の骨格を思わせ、見た目にも力強く美しい。機能が形に現れた例であり、エンジンならではの造形。
05:下面締結式で加工長低減
クランク軸まわりの構造は大幅に設計改良された。当初は横からボルトを差し込むサイドボルト式だったが、加工長を抑えて強度も確保する目的で下面締結式に変更された。ここだけで加工長300mmのセーブである。
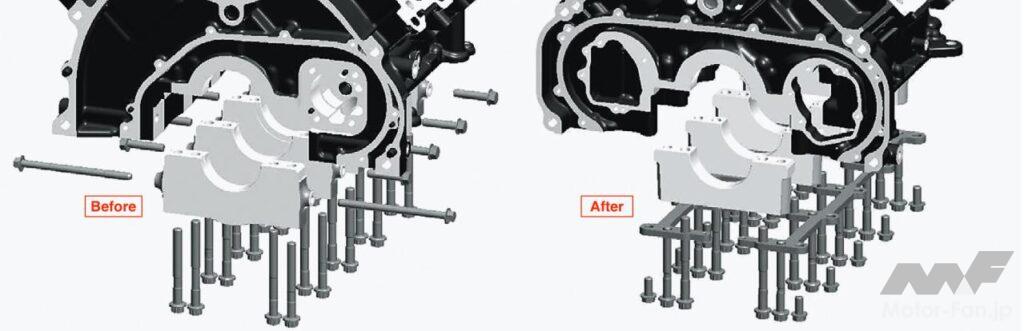