目次
ロータリーエンジンはもちろんMade in HIROSHIMA
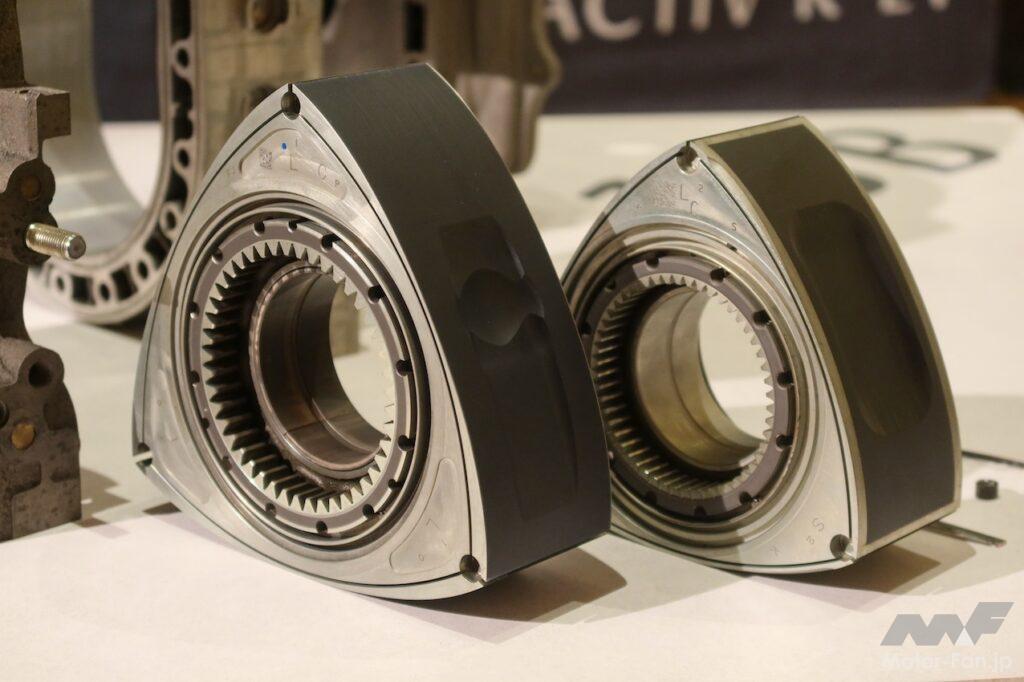
RX-8が搭載していた13B RENESISは排気量654ccの2ローターだった。これに対し、MX-30ロータリーEVの8Cは830ccの1ローターである。ローター幅は13B RENESISの80mmに対して8Cは76mmとスリムになっているが、回転中心からおむすび型ローターの頂点までの距離を指す創成半径は105mmから120mmへと拡大しており、ローターのサイズは大きくなっている。
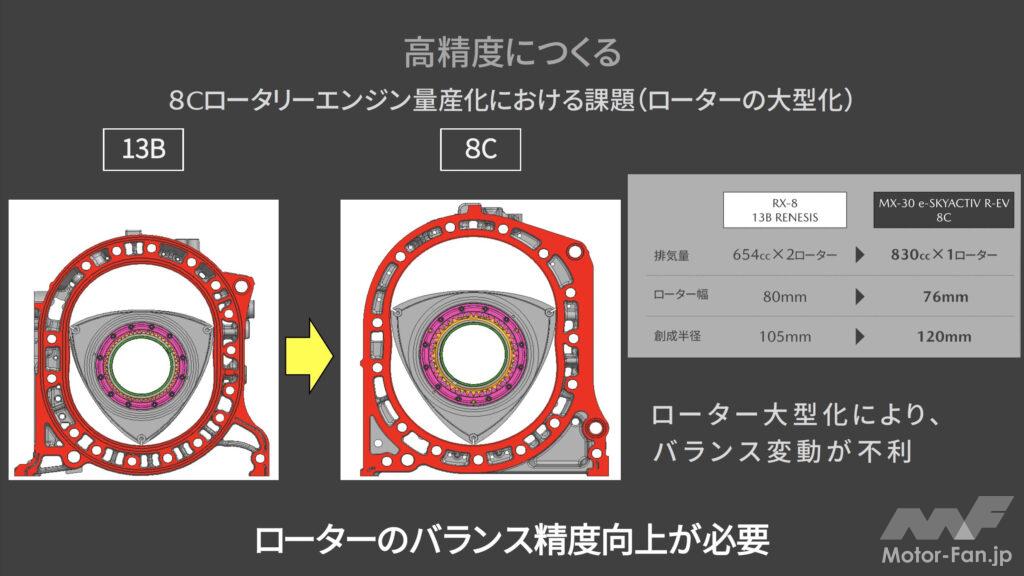
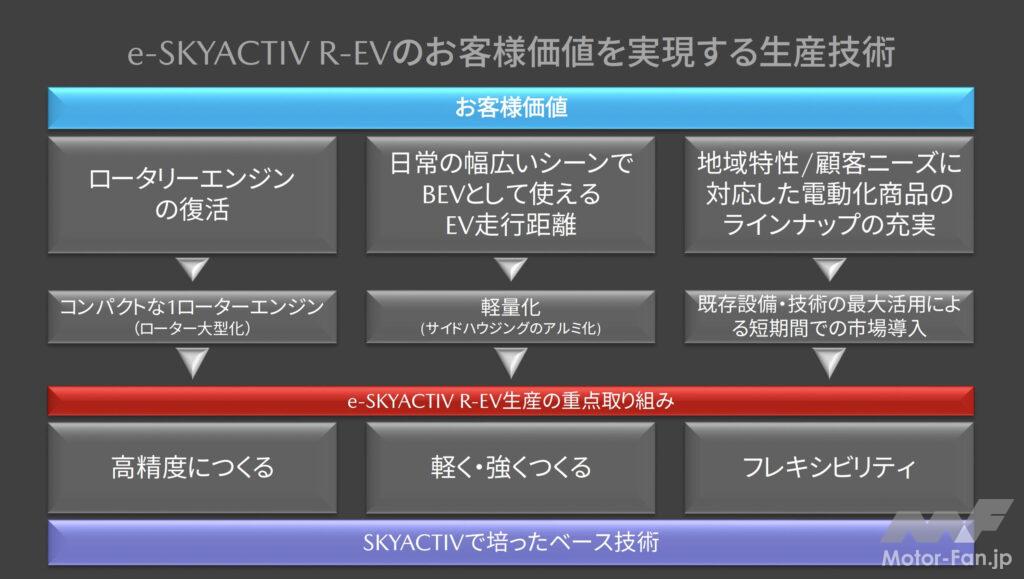
マツダは8Cを生産するにあたって3つの重点施策を定めた。すなわち、「高精度につくる」「強く・軽くつくる」「フレキシビリティ」である。13Bに比べてローターサイズが大きくなったので、回転バランスを取る難易度は高くなる。そこで高精度につくる必要がでてきた。
MX-30ロータリーEVは、普段はEVとしてバッテリーに蓄えた電気エネルギーを消費ながら走り、電気エネルギーがなくなったら燃料タンクのガソリンを使って8Cで発電し、引き続きモーターを駆動して走る。EV航続距離を少しでも長く確保するため、エンジンは軽くしたい。そこで、軽く・強くつくるこだわりが生まれた。
3つめのフレキシビリティは混流生産を指す。新たな電動車のラインアップを素早く、リーズナブルな価格で提供するには、既存の技術や設備を生かしたモノづくりをしていく必要がある。そこで、MX-30ロータリーEVも特別扱いはせず、これまでの他の車種と同様、混流生産に組み入れた。これら3つの取り組みは、クルマをゼロから見直して世界一を目指す開発活動のSKYACTIV(商品としては2012年のCX-5が最初)で培ったベース技術を進化させて適用したという。
広島県にある本社工場で、高精度、強く・軽く、混流生産の3つの重点施策が施された生産の現場を見せていただいた。本社工場の敷地面積は223万平方メートルで、マツダスタジアムが97個も入る広大な敷地を誇る。ここでは8Cの一貫生産が行なわれており、車両についてもプレス〜車体(溶接)〜塗装〜車両組立の各工程が効率良く流れるよう建屋が配置されている。
加工工程
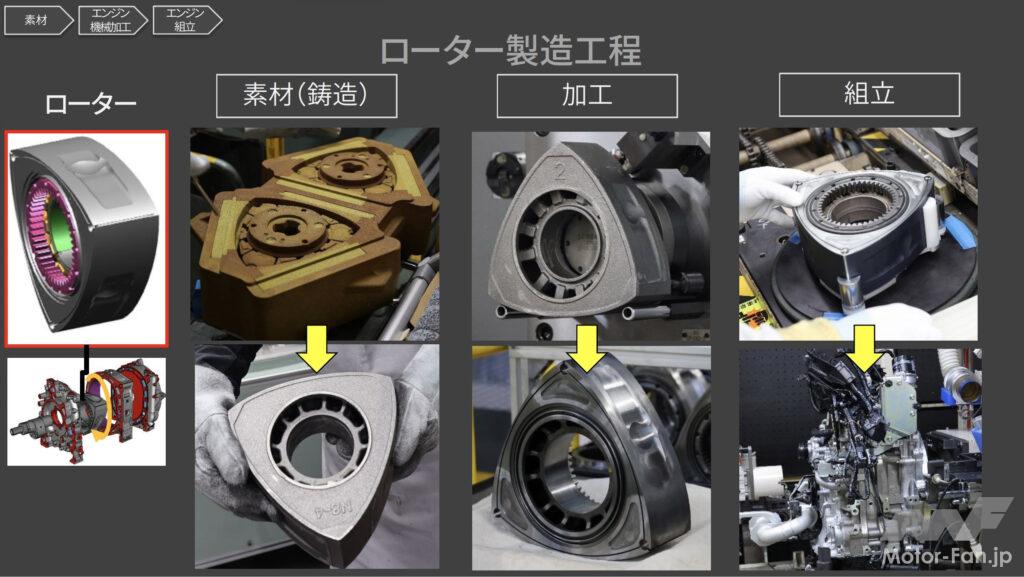
重点施策の1つめである「高精度につくる」については前述したように、ローターの大型化がモチベーションになっている。ローターが大きくなったためバランス変動が圧倒的に不利になり、バランス精度の向上が必要になったのだ。従来比(13B比)で75%の改善が必要になったという。
また、8Cは排気量の拡大によって13B比で燃焼圧力が大きくなるため、燃焼室の気密を保つシールの性能を高める必要が出てきた。ローターにはアペックスシール、サイドシール、コーナーシールが組み付けられており、これらのシールの寸法・形状・組付精度は従来比で50%の改善が必要になったという。
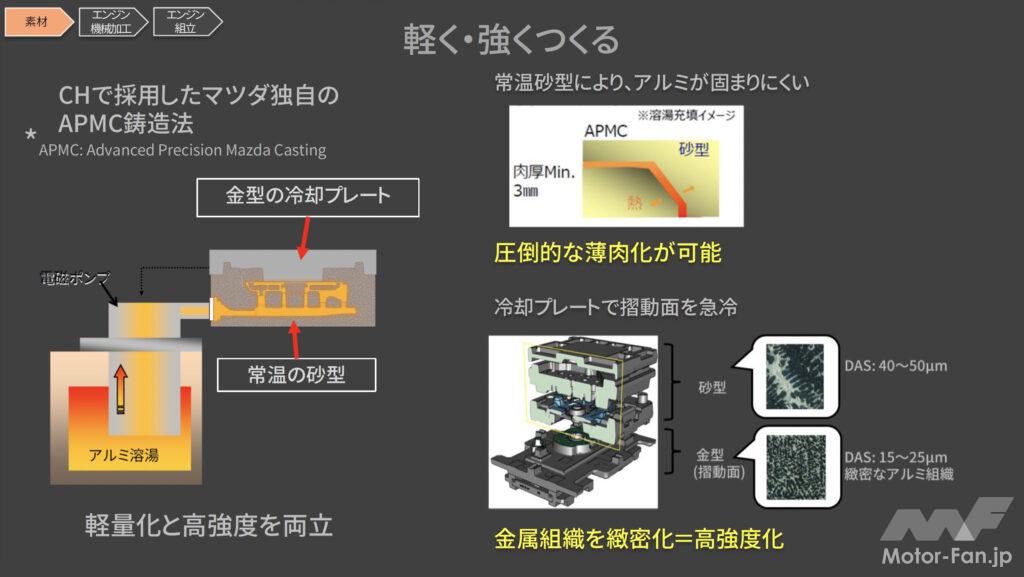
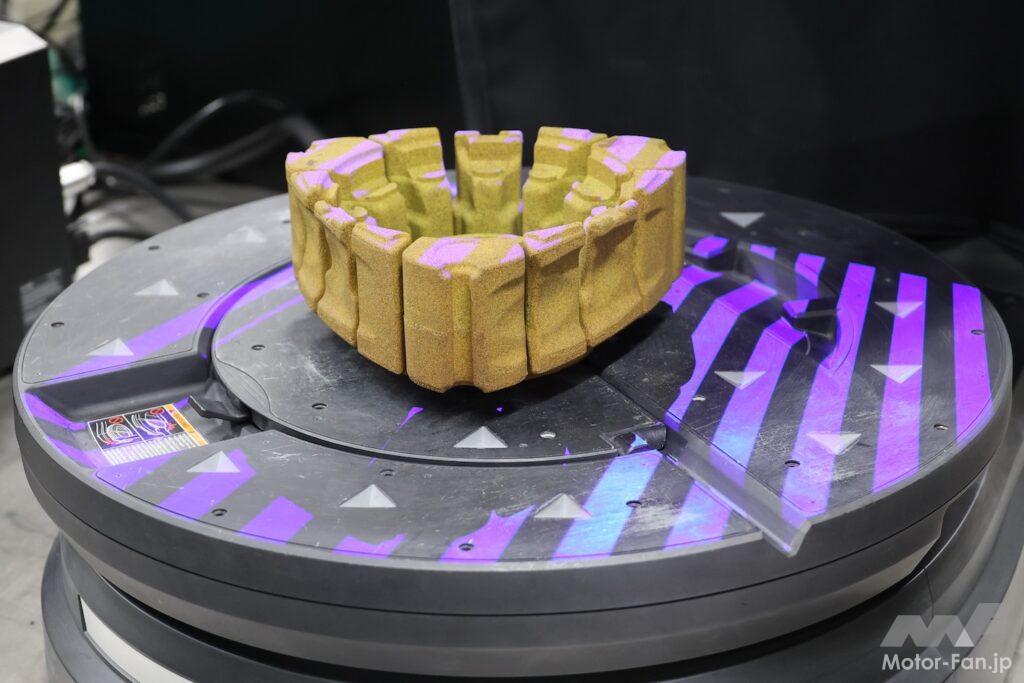
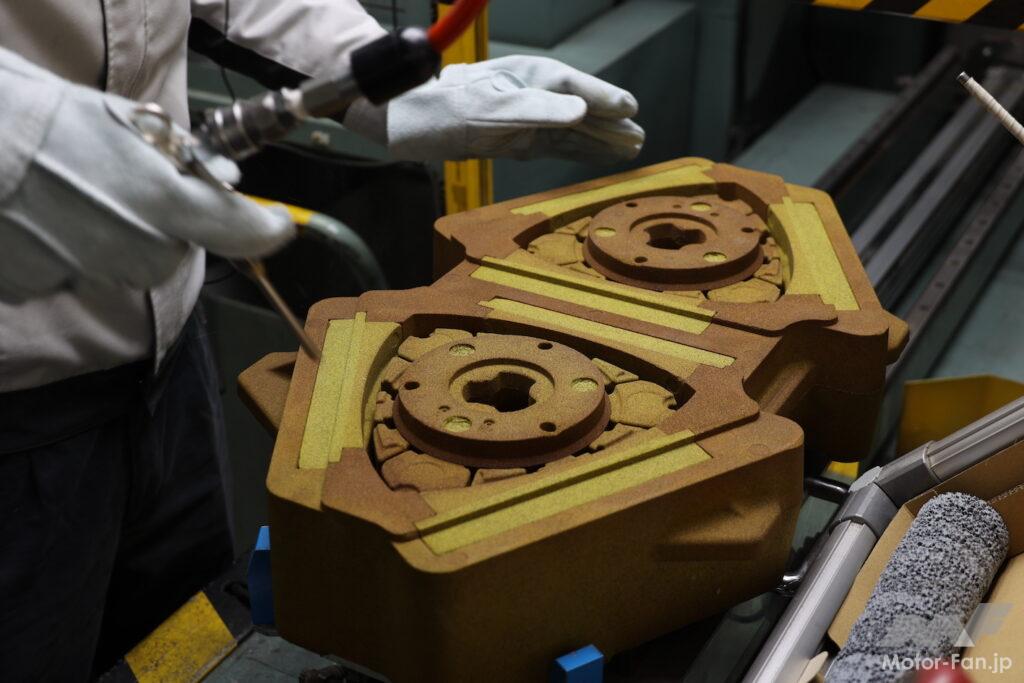
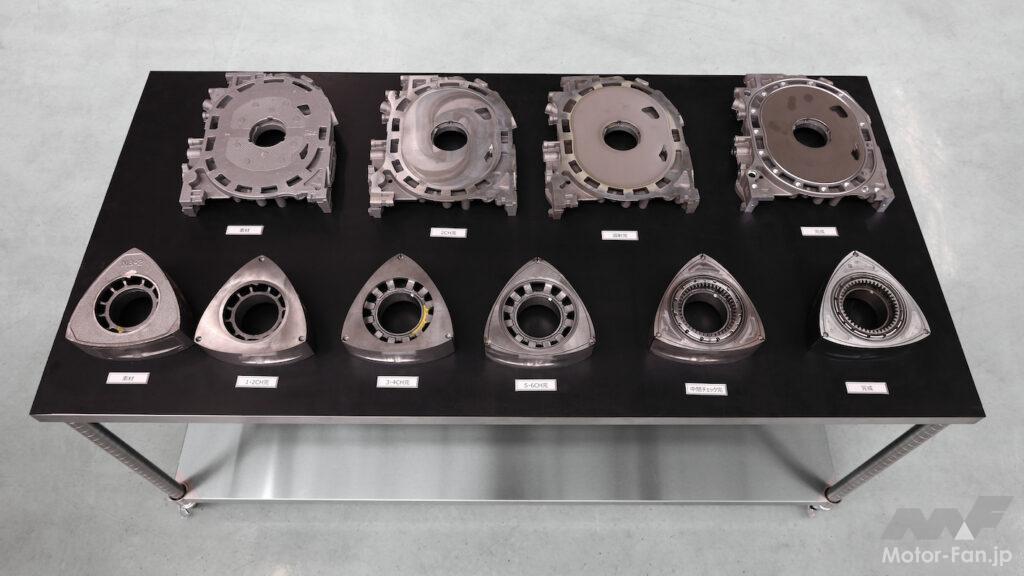
ローターは鋳型の上から溶けた鉄を自由落下させる重力鋳造によって製造する(8Cではこの作業を自動化した)。まず、特殊な接着材を含んだ砂を高温で焼き固めてつくる鋳型を成形。鋳型は複数の砂型の組み合わせからなり、ローターの中空部となる中子(これも砂型)が含まれる。回転バランスにとっては中子の寸法精度が重要。ローターの断面には冷却と軽量化のために多数のリブが入っている。このリブはローターの内部にあるので、鋳造後に機械加工で寸法を調整することができない。そのため、中子の段階で精度高くつくっておく必要があるのだ。
そこで、モデルベース(MBD)を活用して鋳造解析を行ない、鋳造時の熱収縮による変形やバランス悪化分をあらかじめ予測。変化しろを織り込んだ中子形状を設計した。さらに、できた中子は3Dスキャンで寸法を管理。これを保証することで、13B比で54%寸法精度を改善したという。
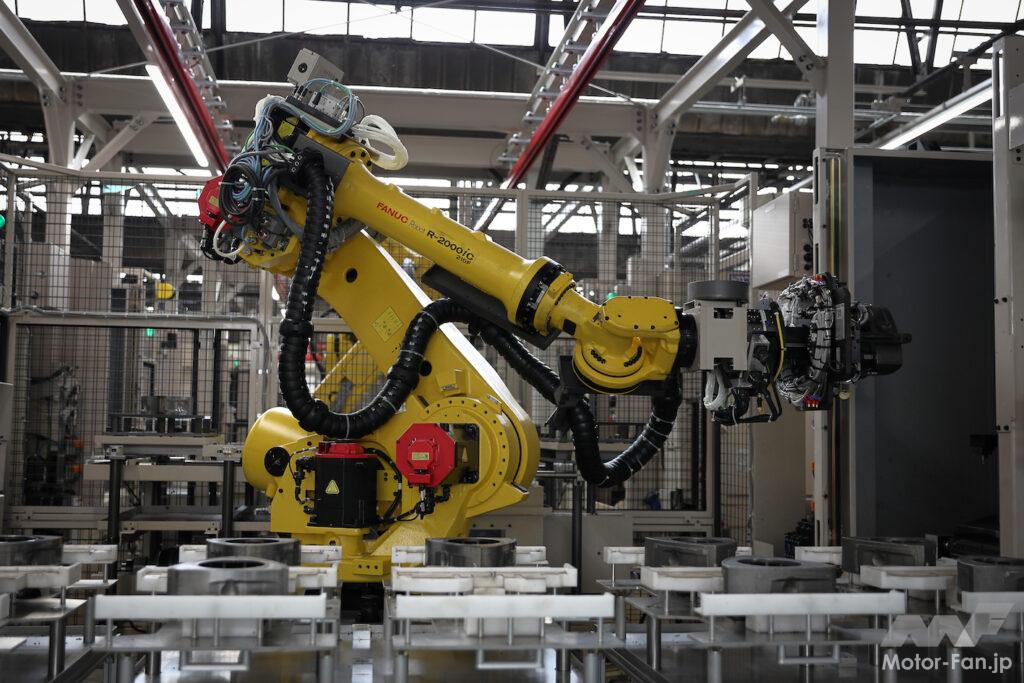
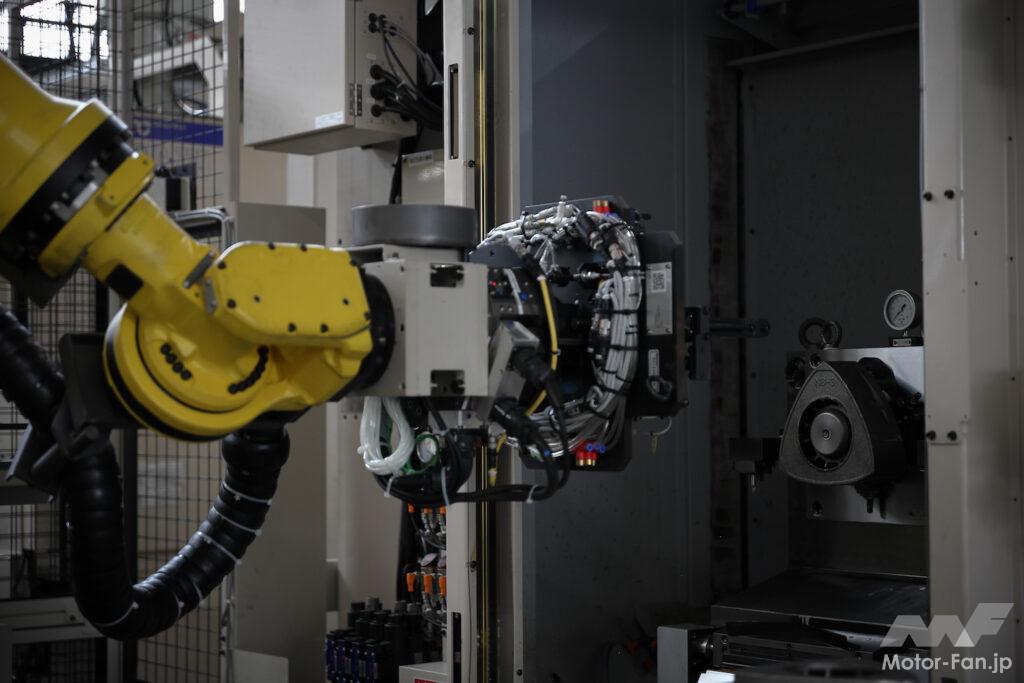
ここまでを素材工程で行なう。鋳造後のローター(素材)をロボットでつかみ、AGV(無人搬送車)に載せて加工工程に搬送。マシニングセンタにセットしてシール溝の加工などを行なった後、バランス取りを行ない、全数保証し、組立工程に出荷する。13B RENESISの加工ラインは、工程ごとに専用のマシンで加工していたため50工程あったという。8Cは汎用のマシニングセンタ1台ですべての加工を行なうよう集約したため9工程で済んでいる。寸法精度の保証に関して不利な素材のつかみ替えを最小限に抑えることにより、寸法公差半減(50%減)を実現した。
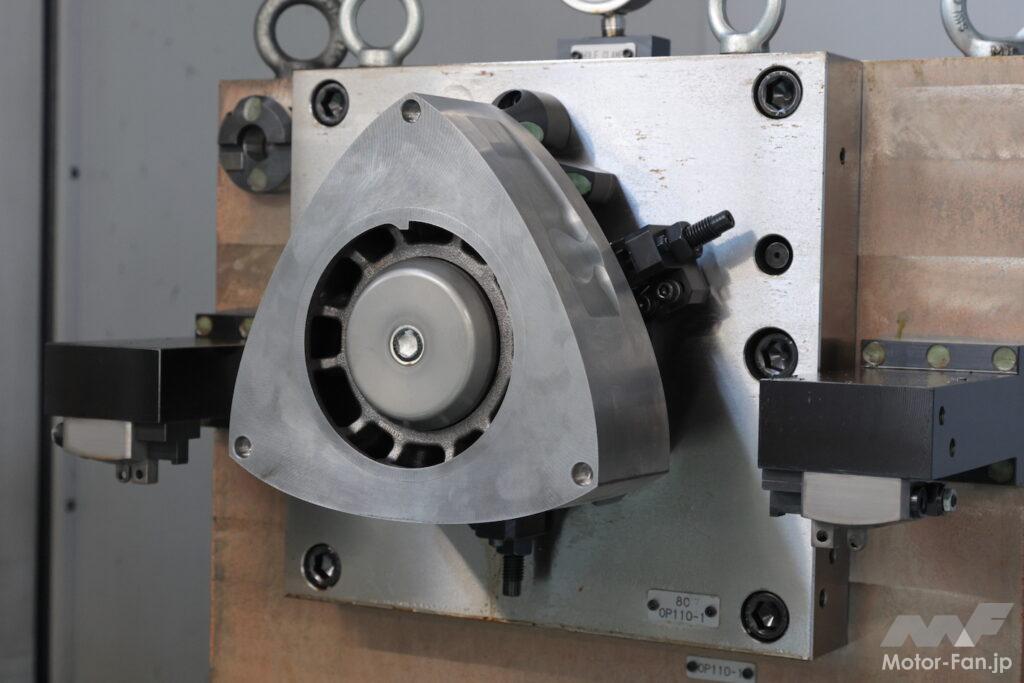
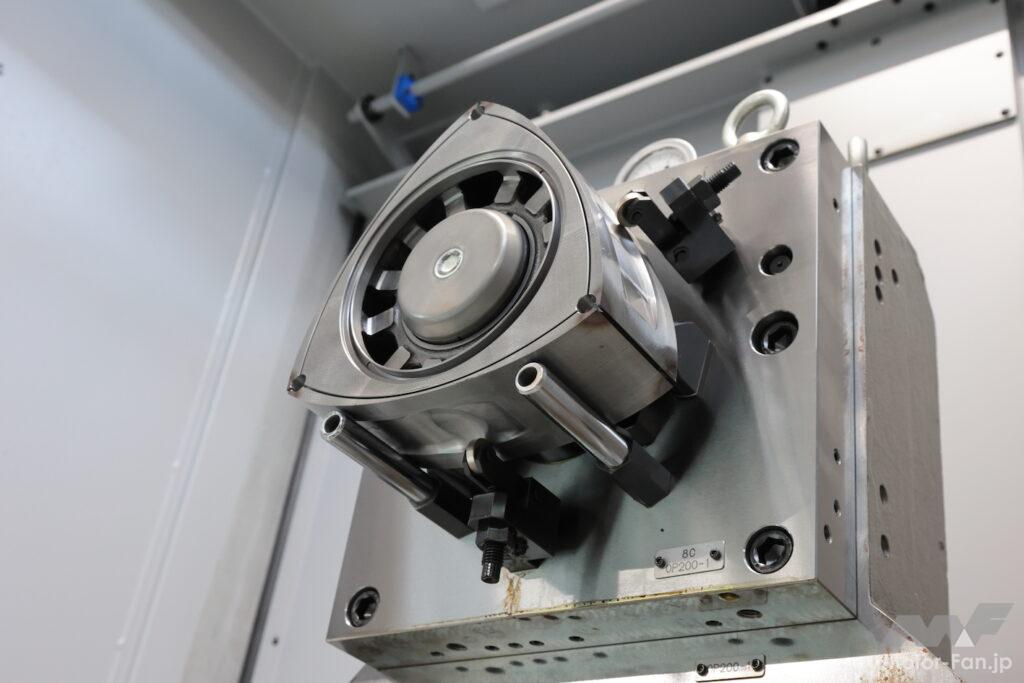
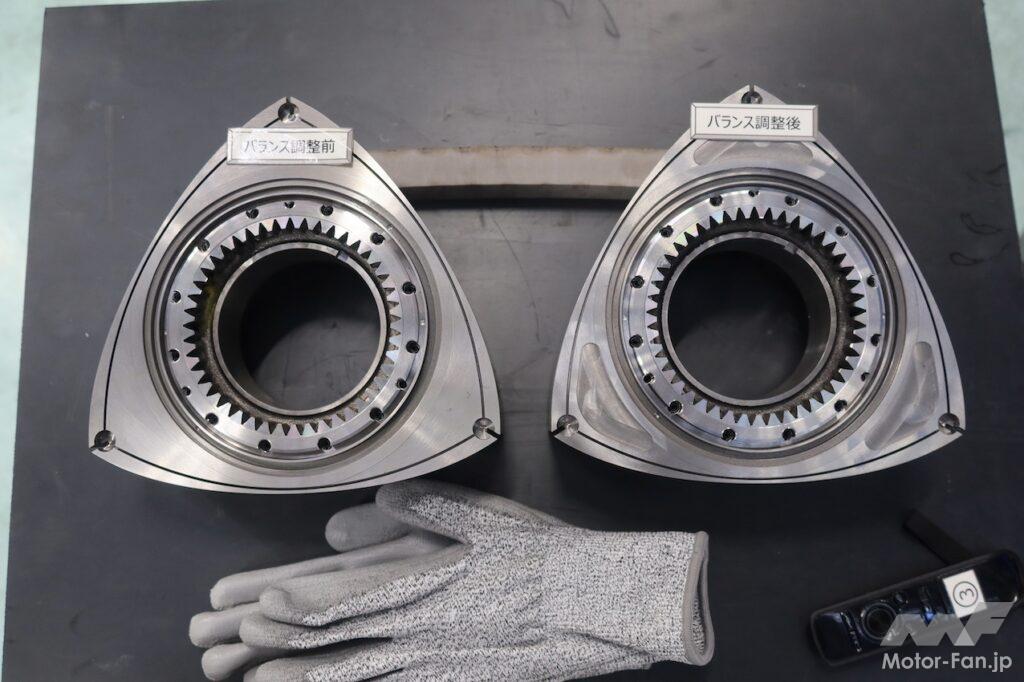
一時的に役目を終えていた建屋は8Cの生産に合わせて本格的に再生され、補修用13Bと8Cの機械加工が行なわれている。車両だけでなくローターも混流生産だ。ベージュ色をしたマシニングセンタが整然と並んでおり、ローター、ローターハウジング、サイドハウジングの加工が行なわれている。ベージュ色の箱の中には黄色いロボットがいて、AGVが運んできた素材の脱着を自動で行なっている。モジュールと称するロボットを増やすことで増産に対応。AGVで運ぶ治具の取り付け構造は13Bと8Cで共通なら、レシプロエンジン(宇品)やトランスミッション(防府工場)とも共通で、フレキシブルな対応が可能だ。
13Bは専用機を用いて切削加工を行ない、人がワーク(加工対象品)の脱着を行なっていた。加工の種類に合わせて製品の脱着を行なっていたので、どうしても誤差が生じた。8Cでは加工の全工程を1台のロボットが自動で行なう。治具のゼロ点とワークのゼロ点をタッチセンサーで確認し、ワークの位置をミクロン(1000分の1mm)単位で検知。その検知情報に合わせて補正しながら加工する。13Bの時代に比べて工程数が少ないし、同一基準で切削加工を行なうことで、寸法精度が格段に向上しているという。
次にバランス取りの工程を見せていただいた。13Bの時代はローターごとに重量バランスを測定し、測定した値を見ながら熟練の作業者がバランスの調整加工を繰り返すことで、狙いの値になるようにバランスを保証していた。あくまで人作業である。8Cでは職人技に頼ったバランス調整を改め、自動化を実現した。SKYACTIVで導入した技術の応用で、バランス測定を実施した後、その結果に基づいて修正量と位相を演算し、精度高く加工する自動調整加工を導入。この技術の導入により、バランス精度は75%改善したという。
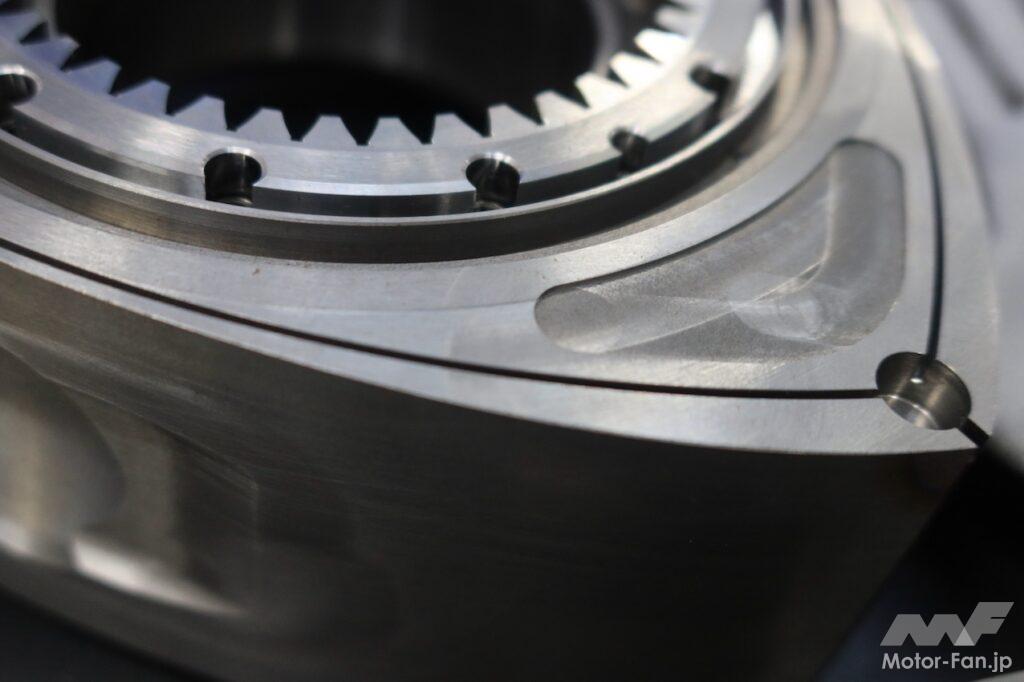
バランス調整前のローター側面はフラットだが、バランス調整後はローターの各頂点部分がブーメラン型に削り取られている。同じように見えて三辺の深さは微妙に異なり、これが調整加工の痕だ。ローターの情報はすべてひも付けられて管理されており、その情報を読み込んだ後、バランス測定機にセット。どこにどれだけのアンバランスが発生しているかを自動的に測定する。その測定値を元に上位サーバーがから、どの位置をどれだけの深さ(ミクロン単位だ)で加工するよう指示が出る仕組みだ。
タッチセンサーでゼロ点を厳密に合わせるのは、加工工程と同じだ。最終的にバランスを取るのはバランス取りの工程だが、すべての製造ばらつきをここで一気にキャンセルするのはなく、高精度なモノづくりを積み重ねたうえで、最終的にここでゼロを目指す考えだ。
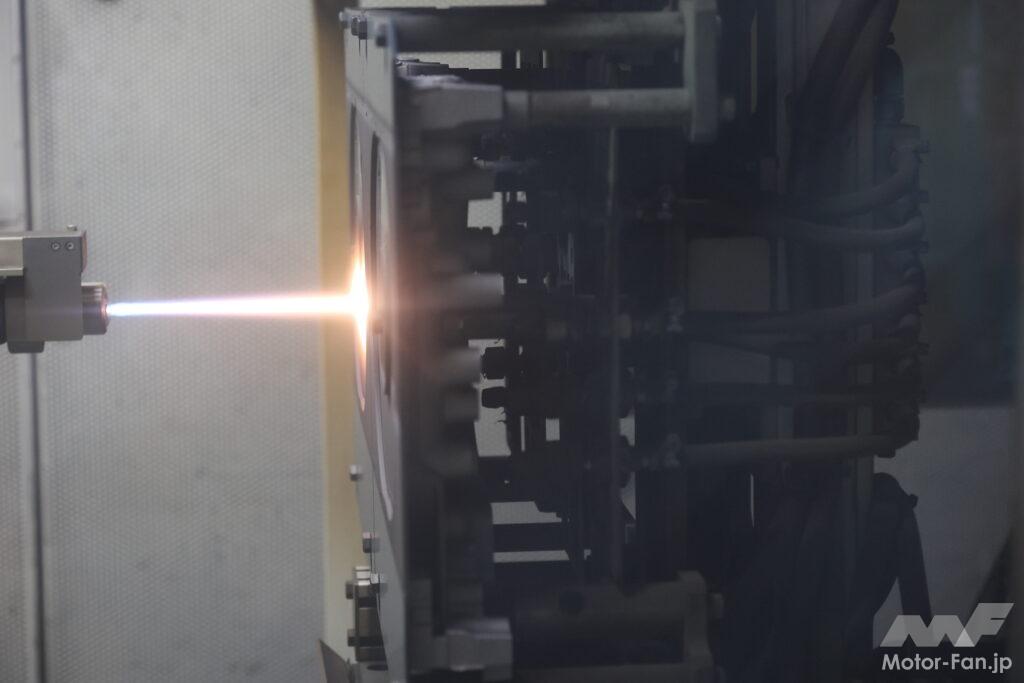
つづいて溶射工程を見せていただいた。この工程は3つの重点施策のうち、「強く・軽くつくる」を実現する技術である。軽量化のためにサイドハウジングを従来の鋳鉄からアルミに変更すると(エンジン単体で15kg以上の軽量化につながった)、ローター摺動面の耐摩耗性を強化する必要が出てくる。
そこで適用したのが高速フレーム法によるサーメット(セラミック)溶射だ。加熱して溶融した金属粉末をマッハ2以上の高速で素材の表面に衝突させ、偏平につぶれた粒子を基材に食い込ませ、堆積させることで、緻密な被膜を形成するコーティング技術である。ワークの並べ方(4枚取りに落ち着いた)や裏側からエアで冷却するなどの工夫により、柔らかいアルミ素材を変形させることなく、均一に膜を形成できる工法を実用化した。工場の中にある部屋の中では、ロボットが規則正しい動きで、高速火炎をサイドハウジングに吹きつけていた。
エンジン組立工程
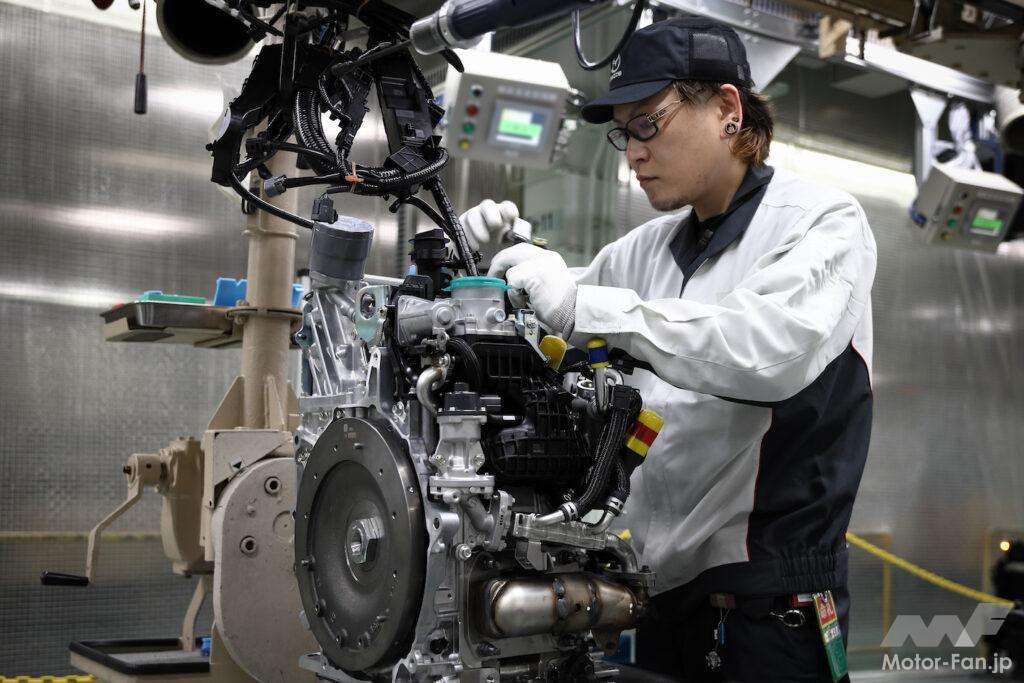
1974年からロータリーエンジンの組立を行なっているエンジン組立ラインに移動した。13Bの組立は三次(みよし)で行なっており、現在は8C専用の組立ラインに改修されている。3つの重点施策のうち「高精度につくる」を使命に組立を行なっている。
見学エリアにはSKYACTIV-G 2.5の直列4気筒エンジンと8Cの部品が並べてあった。8Cの部品点数は4気筒エンジンの約半分だという。カムシャフトやバルブといった吸排気にまつわる部品はロータリーエンジンの8Cには必要なく、それが部品点数の大きな違いに結びついている。2ローターの13Bと比べても、8Cは25%部品点数が少ないという。シングルローター化の影響だ。
建屋の一角に、壁とガラスに覆われた部屋があった。クリーンルームで、室内の気圧を外の部屋より少し高く設定することにより、ゴミやホコリが中に入りにくい状況をつくっている。RE匠工房と呼ぶこの部屋の中では、燃焼室の部品組付を行なっている。ローター、フロントハウジング、ローターハウジング、リヤハウジングにシール関連の部品を組み付け、吊り下げ搬送装置上でハウジングにローターやエキセントリックシャフトを組み付けていく。シール類は異なるサイズが用意されており、適切なクリアランスになるよう選択組み付けを行なう。最後に燃焼室を密閉。フタをされた状態で部屋の外に出てきて、品質保証を行ないながら内部部品、外部部品の順に組み付けていく。
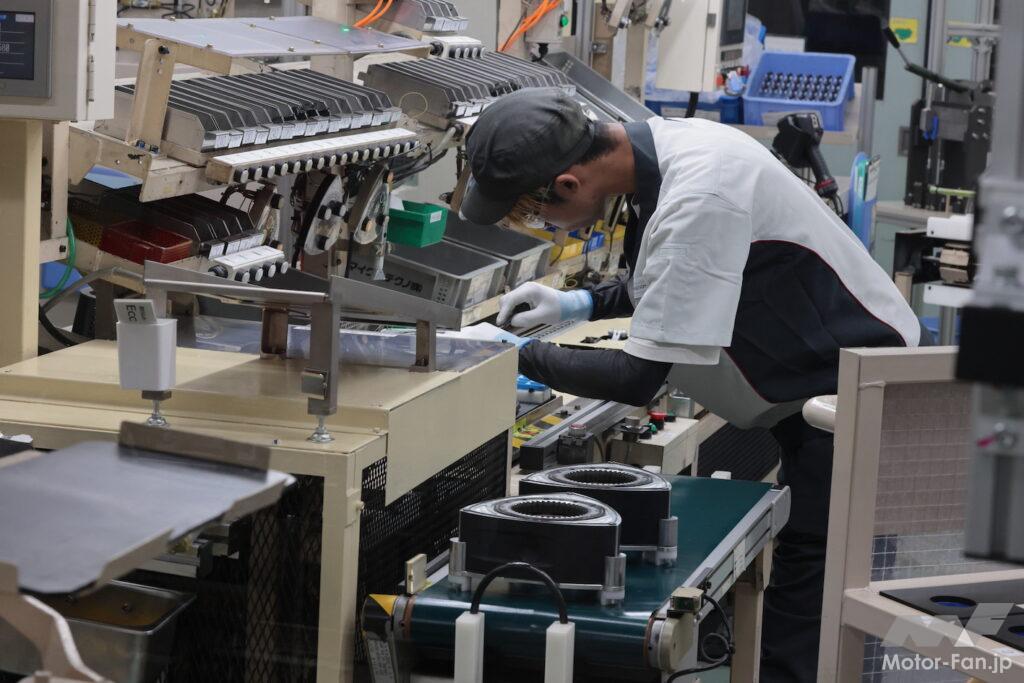
ローターにシールを組み付ける工程は高精度なエンジンをつくるために重要な工程だ。燃焼室の圧力を司るシールが適切に組み付けられていないと、燃焼室の圧力が落ちる。圧力が落ちれば発電能力が落ちる。ローターの3辺で圧力が異なると燃焼圧力にばらつきが出て振動の原因にもなる。組んだ後に測定し、異常があれば組み直しだが、それは最後の手段。そうならないよう、入念に組付を行なう。
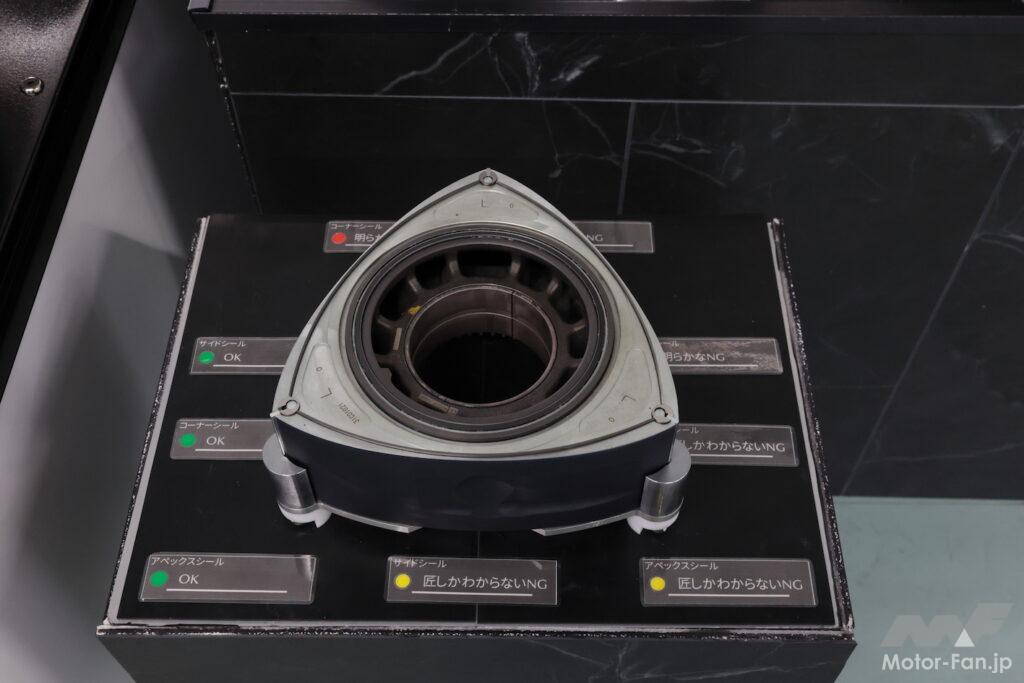
サイドシール、コーナーシール、アペックスシールの3つのシールは“匠”と呼ばれる卓越した指の感覚を持つ技能者が、作動チェックを行なっている。匠の育成に用いる教育ツールに触れることができた。各シールの下にはサイドハウジングの表面に追従するようスプリングが入っている。シールを押してスムーズに押し返してくればオーケー。返ってこなければガス抜け、圧縮漏れの原因になる。
教育ツールには「OK」「明らかなNG」「匠にしかわからないNG」と記してあるせいか、「匠にしかわからないNG」のような微妙な反発力の違いもわかった気になるが、実際に指先に伝わる微妙な感覚を頼りに合否を判断するのは繊細な感覚が求められるし、責任は重大だ。いかに自動化が進んでも、ばねの反発を判断するのは匠の技が欠かせないという。
外部部品の組み付けに必要な部品は、決められた部品が決められた位置、決められた方向に台の上にセットされており、オペレーターは前から順番に取っていくだけでいい仕組みになっている。組立に集中できるようにするためだ。使用するボルトは事前に、ペン立て様の小さな箱の中に準備しておくのだが、人がやるとミスが起きる可能性があるので、ロボットが決められたボルトを決められた容器に入れるのだという。
13Bはポート噴射だったが8Cは直噴となり、エンジンに高圧燃料ポンプを持たせる必要が生じた。エキセントリックシャフトの軸にチェーンをつないで高圧燃料ポンプを駆動する。燃焼のタイミングと燃料ポンプの圧力が上がるタイミングを合わせるため、チェーンのカラーリンク(ピンクとイエローのマーク)と、プーリーのポンチマークを合わせる必要がある。この保証をオペレーターが行なうのではなく、カメラ(画像処理)によって行なっている。Jバーと呼ぶ搬送装置で搬送中でもカメラが使えるよう可動式として持ち運べるようにしたのが工夫点だ。

8Cの生産ラインは7.8分に1台の完成エンジンができるスピードで動いているという。つまり、各オペレーターは7.8分の作業を覚えなければならない。無理ではないが、間違ってはいけないというプレッシャーの中で作業をするのはつらく、負担を軽減するために作業ナビゲーションシステムを導入した。SKYACTIVエンジンですでに導入している技術で、モニターに次に行なう作業の指示が出る。オペレーターは作業の手順を覚えているのが基本なので、いちいちモニター画面を確認することはないが、大きな安心材料になる。ツールから電気信号をとっており、決められた手順以外のことをするとラインが止まる仕組みだ。
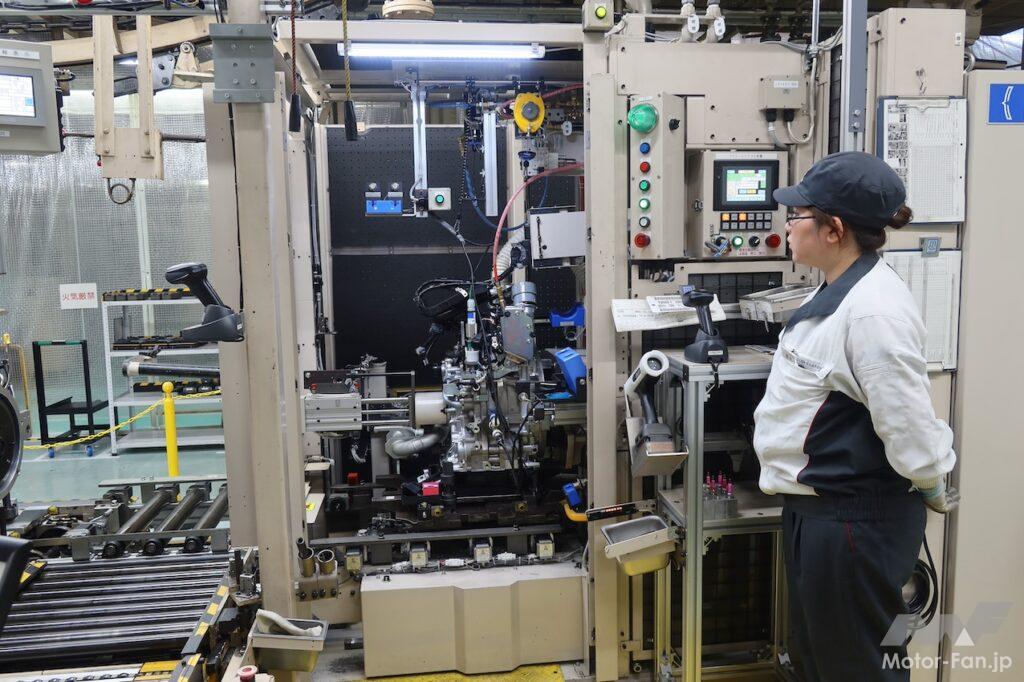
組立工程を経て完成したエンジンはモータリングテストの工程に進む。出力軸側からモーターで回す、いわゆるコールドテストだ。チェックする回転数は3種類。まず、実車で最もよく使う(つまり、最もエンジンとしての効率が高い)2300rpmで回し、スロットル制御、吸気の負圧、油圧、回転抵抗、燃焼室圧力を測定し、振動や異音がないかをチェックする。
次に1200rpmでチェックする。これは、以前13B RENESISで収集した膨大なデータとの突き合わせを行なうためだ。8Cのデータと13Bのデータを突き合わせ、もっといいエンジンにするための調査・分析に活用する。最後に250rpmでテスト。この回転数は、サービス工場などでエンジンのコンディションをチェックする際の回転数で、この後着火運転をした際に、燃焼室圧力などを突き合わせて相関がとれているかどうか確認する。
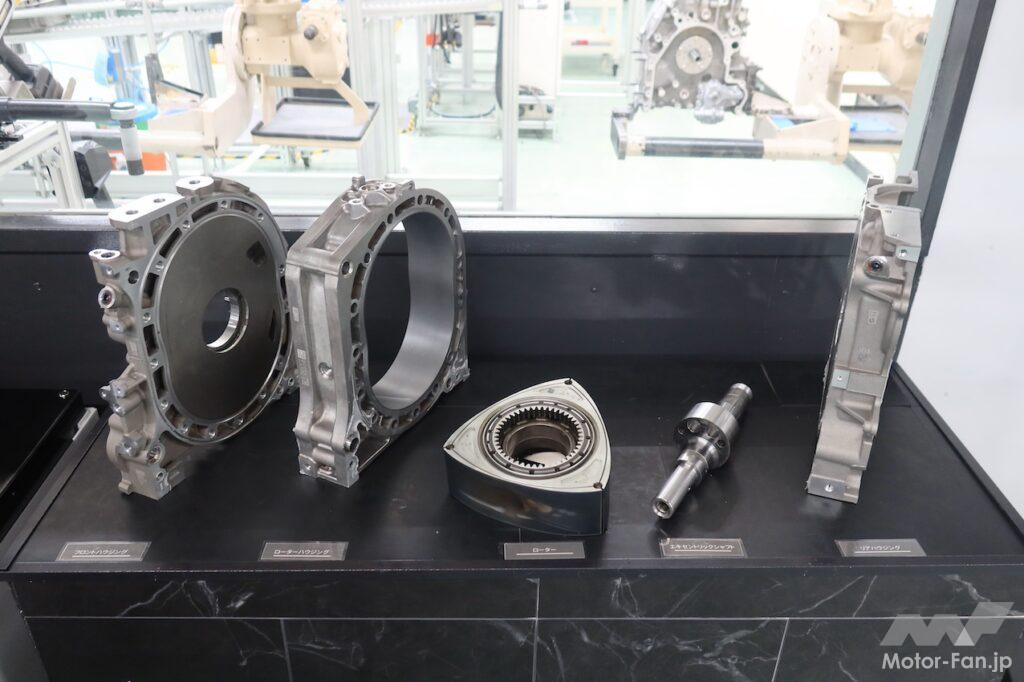
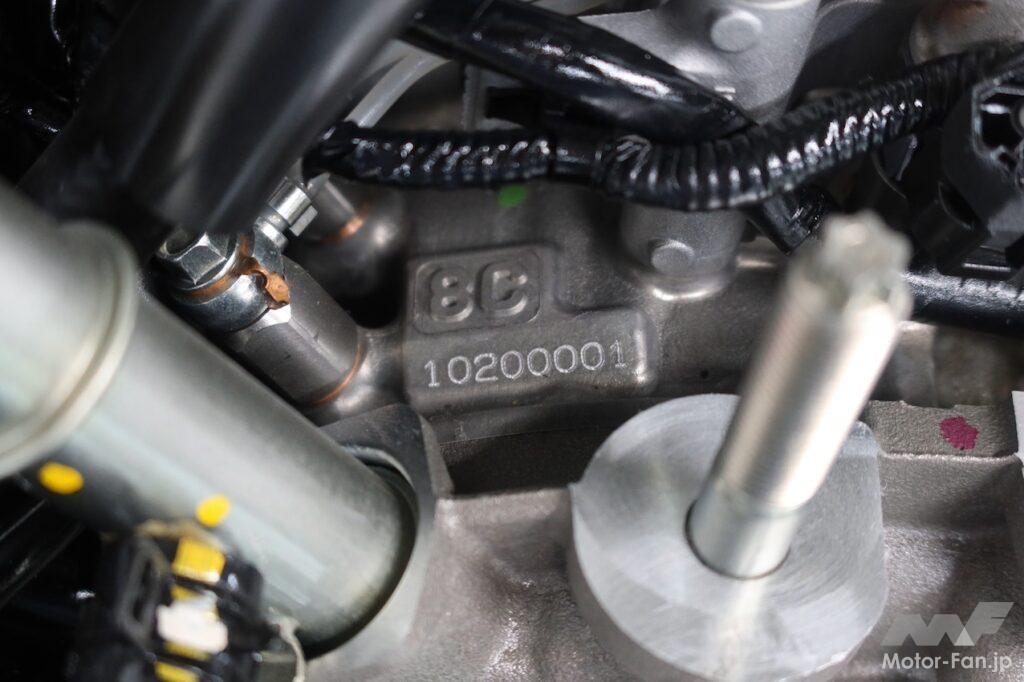
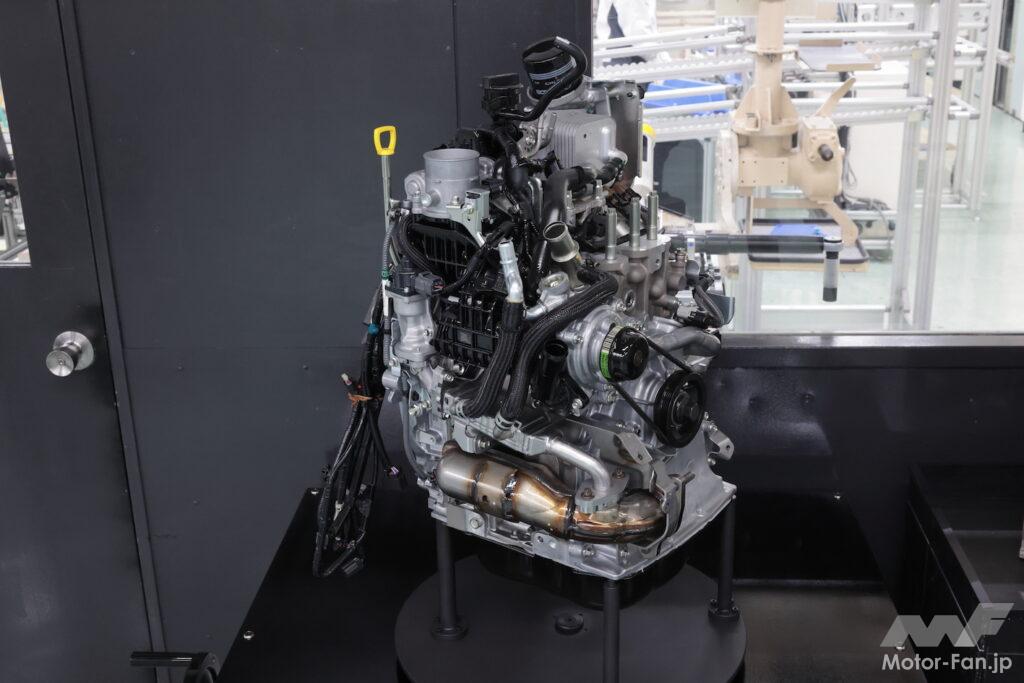
見学エリアには、「工場見学に来ていただいた多くのお客様に見ていただきたい」と、工場側で“購入”した、量産第一号のエンジンが展示されていた(末尾が1の刻印が確認できる)。組立に携わる人たちの誇りである。
車両組立工程
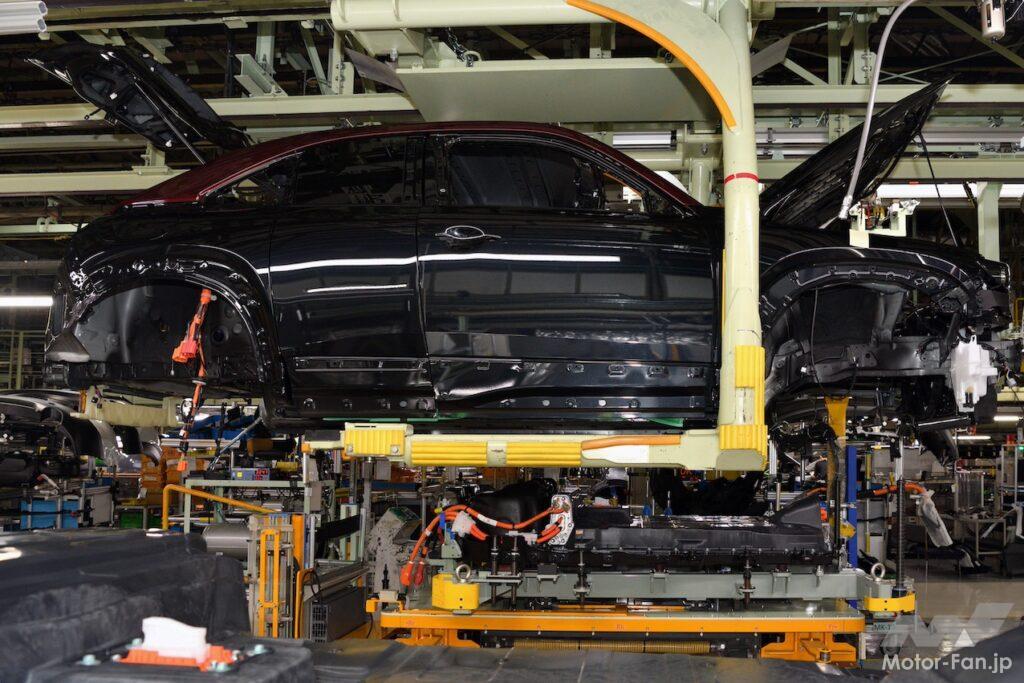
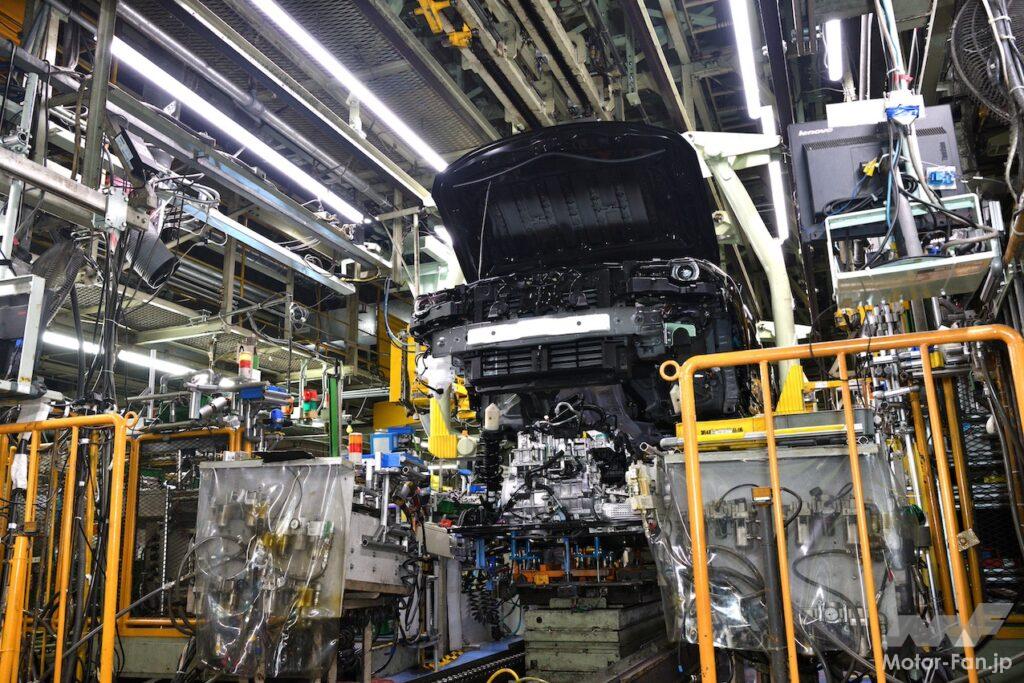
重点施策の3つめである「フレキシビリティ」を実現する車両組立ラインでは、数多くのパワートレーンをモジュール化することで、車種追加や機種追加があっても混流生産ができる態勢を整えている。しかも、既存設備・既存技術の進化で対応し、大規模な改修工事をせず、短期間での市場導入を狙っている。
MX-30ロータリーEVは、本社工場U1のNo.5のラインでパワートレーン縦置きレイアウトのロードスター、パワートレーン横置きレイアウトのCX-30、パワートレーン横置きレイアウトのMX-30のエンジン車やBEVが混流で流れている。メインラインの組立順序や構造は「固定」要素とし、バッテリーや燃料タンク、エンジンやモーターなどのパワーユニットは「変動」要素として、搭載前の準備をサブ組立ラインで行なう。
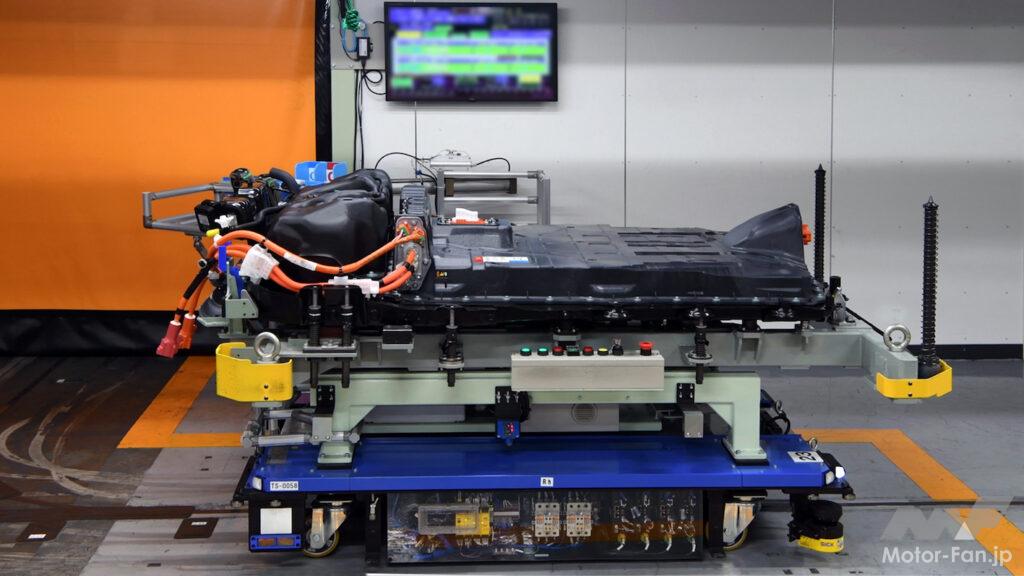
MX-30の場合、BEVにはバッテリーのみを、ロータリーEVにはバッテリーと燃料タンクを搭載するが、どちらも同じAGV・治具を使うことで混流生産を可能としている。パワーユニットを搭載するAGVも同様で、アタッチメントを交換するだけで内燃機関、BEV、ロータリーEVに対応できるような構造にした。
車両組立工場ではまず、車両組立ラインに隣接した建屋にあるバッテリーアッシー場に案内された。ここでは電池メーカーから供給されたバッテリーを、装置を使って鉄製のロワケースにセットしていく。モニターにはボルトを締め付ける順番が表示されており、締め付けが完了すると黄色の表示が緑に変わる。すべてが緑に変わらないと次の工程に進まない仕組みだ。
次に充電ルームを見学した。建屋の屋根には1.1MWの発電能力を持つソーラーパネルが設置されているという。晴れた日中であれば、系統電力に頼ることなくソーラーで発電した電力でまかなえるそう。ここでは、約20%の充電状態で電池メーカーから供給されたバッテリーを60%まで充電してラインに供給する(販売店で100%まで充電し納車)。この後、ロータリーEVの場合は燃料タンクをパレットに載せる。
バッテリーアッシー場からバッテリー搭載工程まで、100mほどの距離をAGVで搬送。ラインのサイクルタイムは3.4分だ。つまり、3.4分ごとにクルマが入れ替わる。ロードスターとMX-30が同じラインを流れている光景は、事前に聞いて知っていたにもかかわらず、実際に目にすると奇妙だ。MX-30ロータリーEVの順番がやってくると、待機していたパレットが持ち上がり、オペレーターによって車体にセットされていく。バッテリー/燃料タンクの仕様やパワーユニットの仕様によって異なる作業量をどう平準化するかが苦労する点だという。
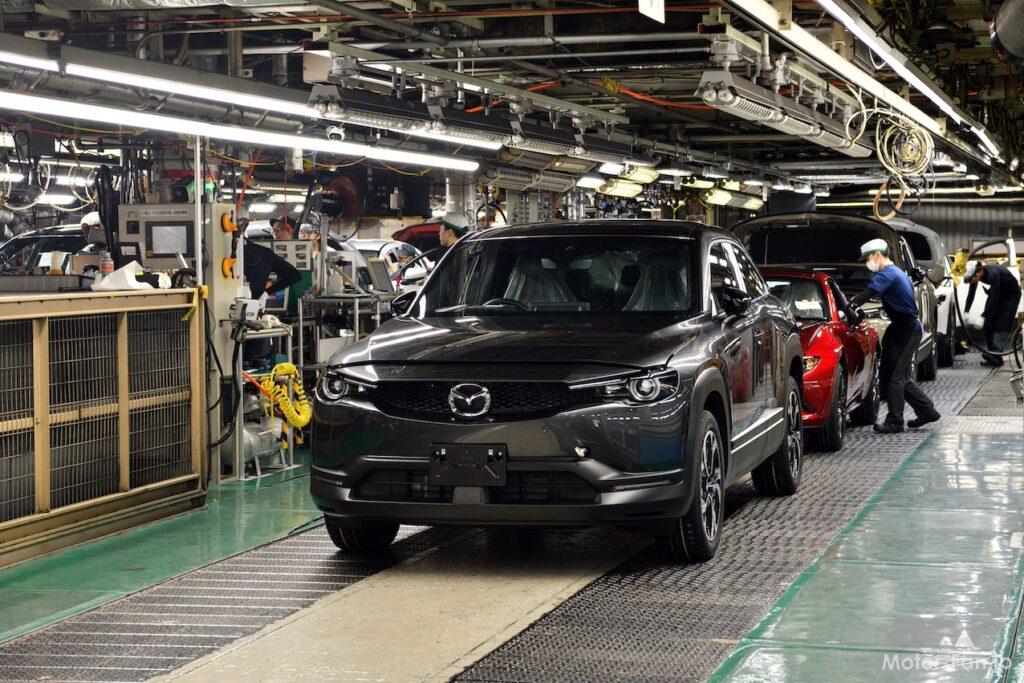
それができているから、ロードスターとCX-30のエンジン車、MX-30のエンジン車とBEV、ロータリーEVがあたかも平然と、同じラインを流れている。1967年からロータリーエンジンを作り続けるなかで培われた技術に、2010年代からSKYACTIVテクノロジーを適用する中で進化させてきた技術、それに最新の技術を加えることで、発電用に使う新しいロータリーエンジンと、そのエンジンを搭載した新しいクルマが、精度高く、効率的に生産できている。その現場を目の当たりにした。