F1は2014年からエンジンのフォーマットが変わり、1.6ℓ・V6ターボを搭載することになったが、設計部の4つの組織のうち、サンプ、ブロック、ポンプなどのエンジン下回りを1つめのチームが、新フォーマットに必須のターボチャージャーはシリンダーヘッドとエキゾーストを受け持つ2つめのチームが担当した。3つめのチームが受け持つのは、フューエルシステムなどのアッパーパート。4つめのチームはピストンやバルブなどのムービングパーツを受け持つ。
これら4つのチームのなかで組織横断的にコミュニケーションをとりながら活動するのがシミュレーション部だ。CFD、FEM、ダイナミクス解析などを行なう。
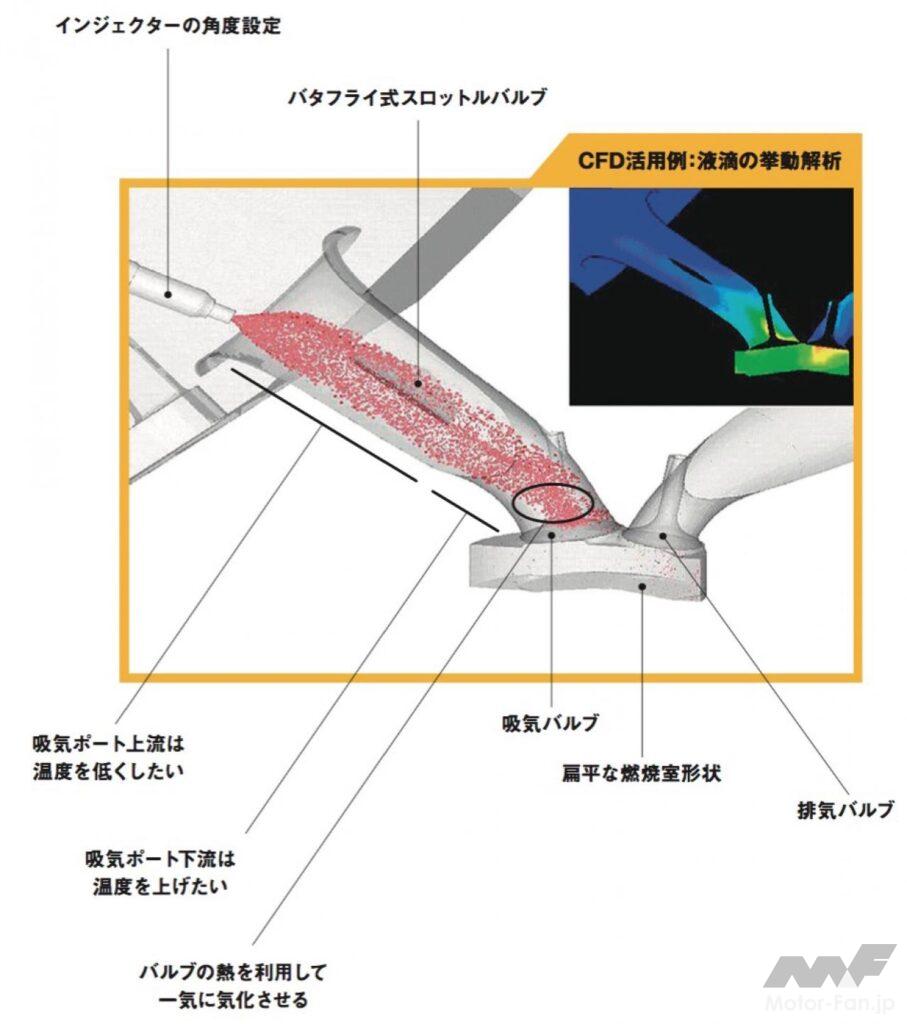
シミュレーション部はどんな活動を行なっているのか。2006年に投入した2.4ℓ・V8エンジンの燃料液滴挙動解析を例に紹介しよう。吸気には脈動があるので、その際、液滴がどのようなふるまいをするか解析すると同時に、液滴が気化して空気と混ざった状態である混合気がどう燃焼室に入るのか、シミュレーションする。バルブの開閉に対してどのタイミングで噴射すればいいのか、噴射角はどうするかといった要件に対し、適正な値を探り出すわけだ。
燃料が気化せず液滴のまま燃焼室に入らない方がいいことは、シミュレーション技術が現在ほど発達していない時期から経験でわかっていた。それを、シミュレーションで裏付けることができたという。液滴は、吸気バルブがまだ閉じた段階で十分に気化させ、バルブの裏に集めておいた方が、燃焼室に入ったときに一気に入って均質になる。燃焼室の熱を受けたチタン製バルブは高温になっているので、その熱を利用し、瞬時に気化させるわけだ。
一方で、吸気ファンネルの上流ではあまり気化させたくない。早い段階で気化させてしまうと、体積効率が落ちてしまうからだ。ミクスチャープリパレーション(混合気の生成)と体積効率、それに脈動のタイミングを合わせ、体積効率の高い均質な混合気が燃焼室に届くようシミュレーションを繰り返した。
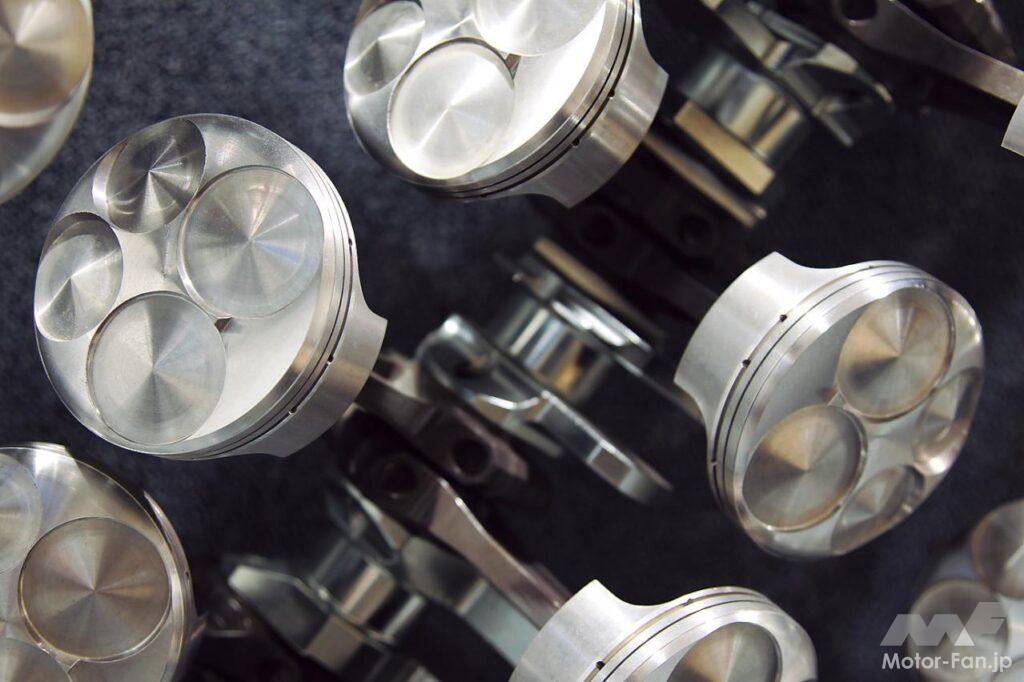
回転上限が18000rpmに制限されているとはいえ、F1エンジンが世界を見渡しても類い希な高回転エンジンであることに変わりはない。ピストンスピードの関係から、どうしてもショートストロークにならざるを得ないので、燃焼室は必然的に偏平になる。燃焼にとって理想からほど遠い環境で、いかに素早く燃焼させるか。それもシミュレーションで検証を行なった。実は2.4ℓ・V8エンジンを開発する際は、先にベンチで燃焼の発生速度が遅いことが指摘されたのだという。その解決に貢献したのがシミュレーション技術だった。
1基のエンジンで1レースだけを走ればよかった時代はFEMで構造解析をすれば事足りた。だが、1ドライバーあたり年間8基の規定が導入(2009年)され、3000km近いライフが求められるようになると、疲労破壊を避けるための、熱機構解析の重要度が増していった。それまで、応力の指標はフォン・ミーゼス応力(応力の6つの成分を統合した値。この値が降伏応力に達すると降伏する、という指標)に頼っていた。だが、フォン・ミーゼス応力が導き出す回答と、実際に壊れる部位が合致しないため、繰り返し回数を加味して疲労解析の指標を構築。コンロッドが1サイクル720度を回転する間に受ける、疲労の解析などに適用した。
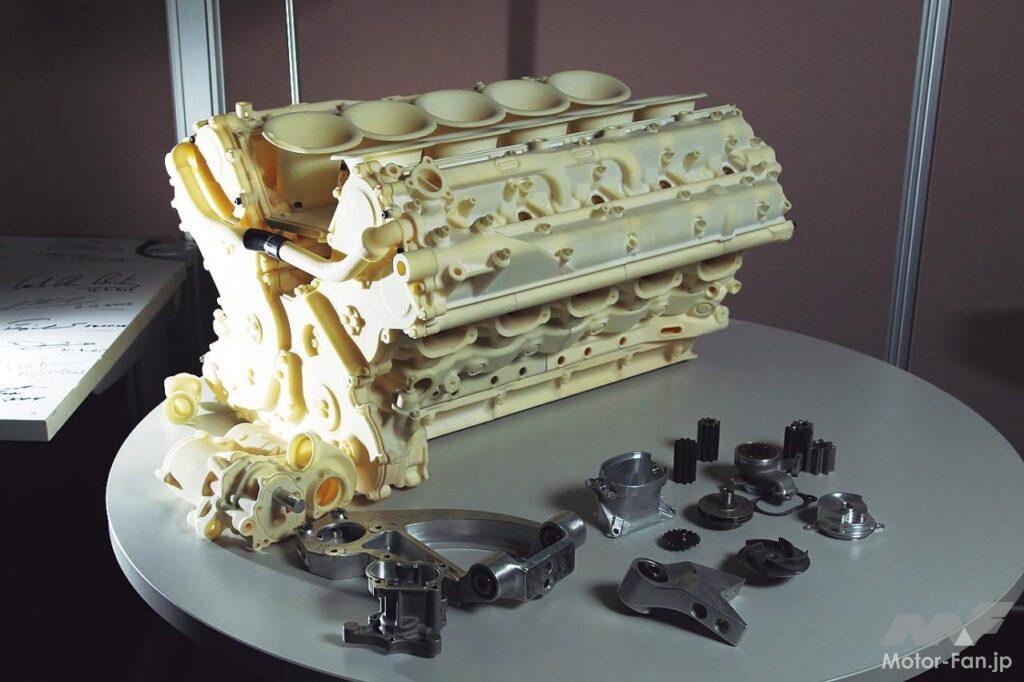
各種のシミュレーションを1気筒で行なった後は8気筒で計算する。それがマルチボディダイナミクス。クランクシャフトやカムシャフトの振動に由来する応力はここで計算。さらに、繰り返し回数を加えて疲労計算を行なう。1サイクルの間でピストンとコンロッドがシリンダーライナーを移動する際、コンロッドはシリンダーライナーに対する向きを変えながら移動する。垂直線に対するピストンの左右方向の移動量をシミュレーションで弾き出し、その数値を設計部にフィードバック。ストレスの少ない設計を求めていった。
耐久信頼性を向上させるシミュレーションは現在進行形だが、開発の軸足は1.6ℓ・V6ターボに移っている。直噴の液滴挙動と燃焼解析、ターボの効率を見極める解析が主眼だ。
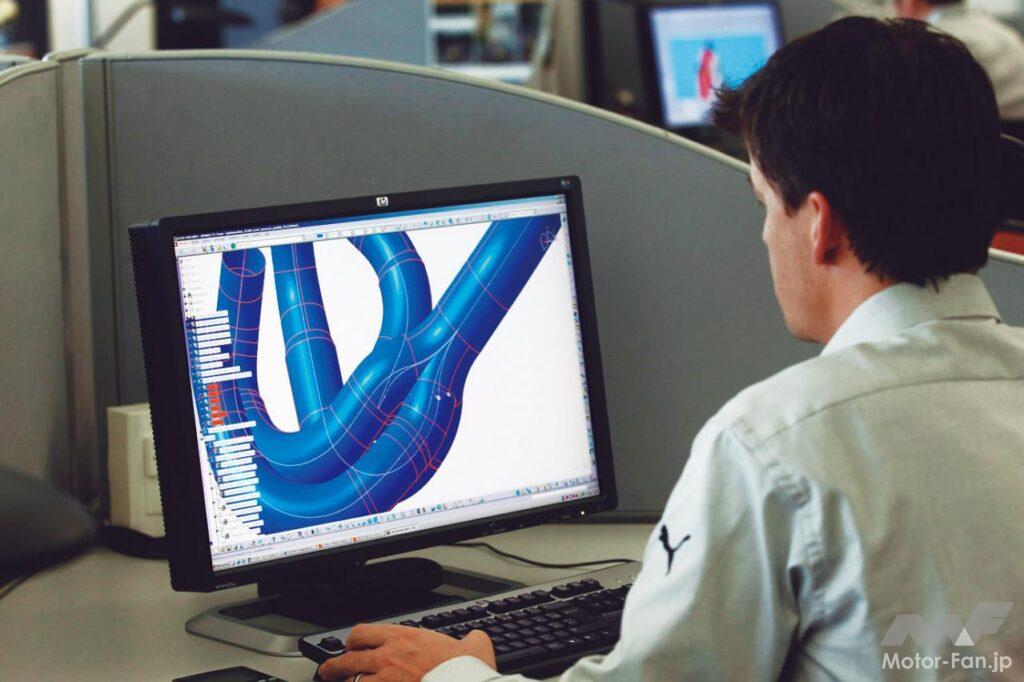