目次
50ヵ所の問題点を修正すると問題点が100ヵ所に増えた
鈑金職人の手叩きで成形されたボディ
TOYOTA 2000GTがスピードトライアルで78時間を走り切った頃、ヤマハ発動機では市販仕様の本格的な生産立ち上げに向けて準備が進んでいた。
TOYOTA 2000GTの生産工場として、急きょヤマハ発動機本社に新たに3号館が建設され、それまでの開発拠点だった日本楽器の試作工場から引っ越した。この3号館のラインから、試作車以外の市販仕様第1号車が生み出されることになる。
少量生産のTOYOTA 2000GTは、普通の乗用車とまったく異なる方法で生産された。通常、ボディの大まかな部品、フロア部分、ルーフ、前後フェンダーなどは油圧プレスでプレス加工して大量生産される。ところが、1日に1、2台しか生産しないTOYOTA 2000GTでは、プレス用の金型を何個も作っていてはとてもコストが合わない。
そこで、第1工程だけプレスで成形し、その後の加工をすべて手作業としたのだ。プレスで出来た部材の余計な部分を切り落とし、縁を曲げて穴を開けるなどの作業は人の手で行われた。
しかし、手で鉄板を成形して自動車のボディにするというのは容易なことではない。ましてやTOYOTA 2000GTのような微妙な曲線を描くスポーツカーとなると、工芸品レベルの技能が要求される。そのため、ヤマハ発動機では手鈑金の経験者や職人を苦労して集めたという。
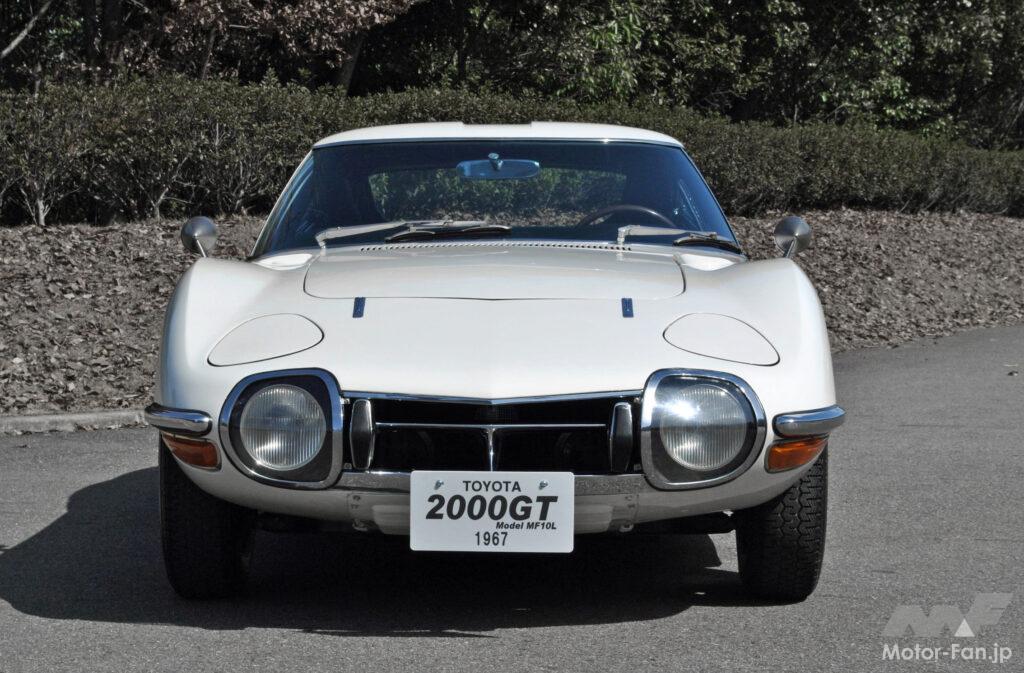
最初にプレスされた第1工程では、基本的に設計との誤差はゼロかせいぜい0.1mm程度。しかし、その後を手鈑金で成形するには、型の上で鉄板を叩くのではなく金床の上で叩いては型に合わせて検討するという、極めて地道な作業を繰り返す。さらに、プレス工程で出来たシワを縮めて取る“絞り”の作業も加わる。結果的にどうしても0.2mm程度の誤差がなくならなかったという。
さらにTOYOTA 2000GTの特徴でもある「継ぎ目のないボディ」も製造現場を悩ませた。通常の乗用車では、例えばフロントフェンダーはボディにボルトで取り付けられていることが多い。ところが、TOYOTA 2000GTの場合は、フロントフェンダーは溶接でボディに取り付けられていて一体化している。ボルト止めのように簡単に微調整が利かないのだ。パネルの継ぎ目はハンダを盛って埋める。
窓まわりのモール部分も苦労した。風切り音が出ないようにモールの取り付け部は凹ませて、モールとボディを面一化しているのだが、その凹みが合わなくてハンマーで修正すると、鉄板が部分的に伸びてしまい、微妙なボディの曲線が歪んでしまうのだ。
あまりにも作りにくい部分は、設計変更を余儀なくされたという。手作業で作り、手で修正を加えていった結果、ドアの寸法が左右で異なるということもあったようだ。そして、マニアの間には「TOYOTA 2000GTは1台1台の形が微妙に異なる」という定説が出来上がった。
水漏れが止まらず苦労したシャワーテスト
実際には採用されなかったが、軽量化のためにボンネットやリアゲートをFRPで試作したこともあった。しかし、塗装工程で変形したり、塗装した色が鉄板のボディと合わないことから採用を断念したという。
ガラスメーカーが作るフロントウインドウにも苦労があった。当時の日本のガラスメーカーは3次曲面のガラスを作った経験がないことから、設計通りのRが出ていなかったのだ。その3次曲面を拭き取るワイパーでも苦労した。最初は拭き残しが出て、その拭き残しがなくなったら今度はワイパーのビビリ音が出るといった具合である。
しかし、市販仕様でもっとも苦労したのは何といってもシャワーテストだった。ヤマハ発動機で完成したTOYOTA 2000GTは、ヤマハ発動機社内で完成検査を受ける。シャワーテスト場で水圧のかかったシャワーをボディに掛け、車内の検査員が懐中電灯であちこちの隙間を照らして水漏れがないかチェックするのだ。
手作業で作られたボディはプレスで大量生産する量産品とは違い、どうしても精度が出ないため水漏れが多かった。1台ずつ手直しして再度検査するのだが、どうしてもジワッとドアの隙間から漏れてきたという。ドアのウェザーストリップに新しい断面形状のものや別の素材を試したりしたが、最後まで水漏れには泣かされた。
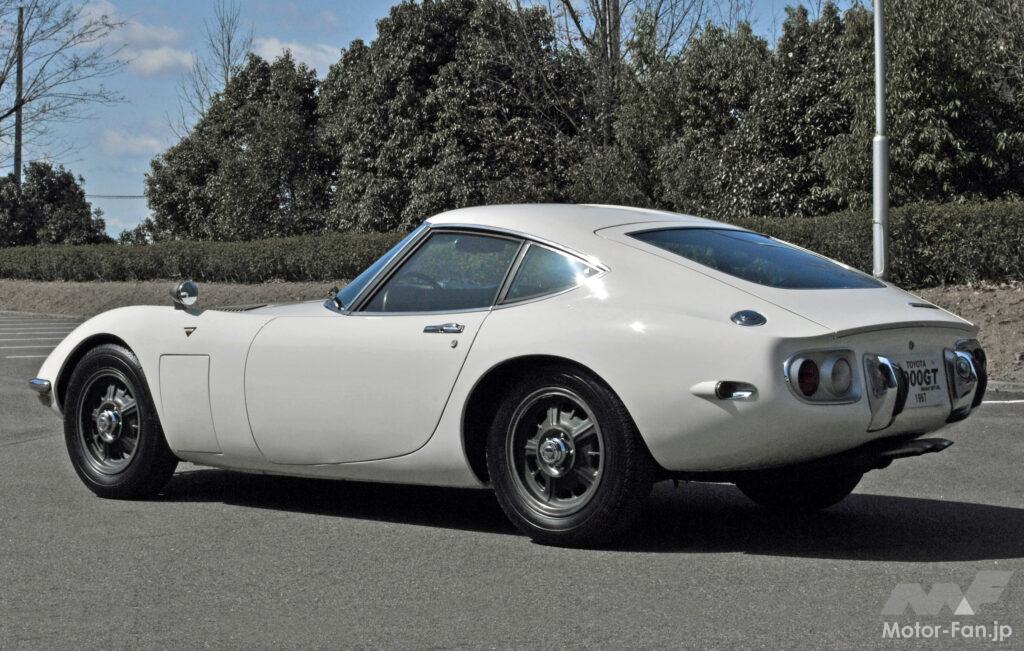
ヤマハ発動機の検査の後には、今度はトヨタの厳しい品質検査が待っていた。トヨタの検査員のチェックは、なめるように入念なものだったのだ。初期の頃は、トヨタから50項目の問題を指摘されてヤマハ発動機で修正すると、今度は問題点が70項目に増え、3回目には100項目になっていたという笑えない話もあった。
ヤマハ発動機の修正する技術が未熟で、どうやって修正すればいいかわからないまま修正を加えるものだから、修正した個所がキズになってしまう。それをさらに直そうとすると余計にキズが目立つという悪循環に陥り、問題点がどんどん増えていったというのだ。厳しい目で指摘される品質検査だったが、それによってTOYOTA 2000GTの品質が向上していったのは確かだ。
生産ラインの3号館では、ホディ、シャシー、エンジンが組みあがったところで合体させ、内装仕上げを4、5人で行なっていた。生産台数は1日に多くて2台。それでも現場では徹夜で作業することも度々あったという。