目次
生産における早期警報システムとしての予知保全
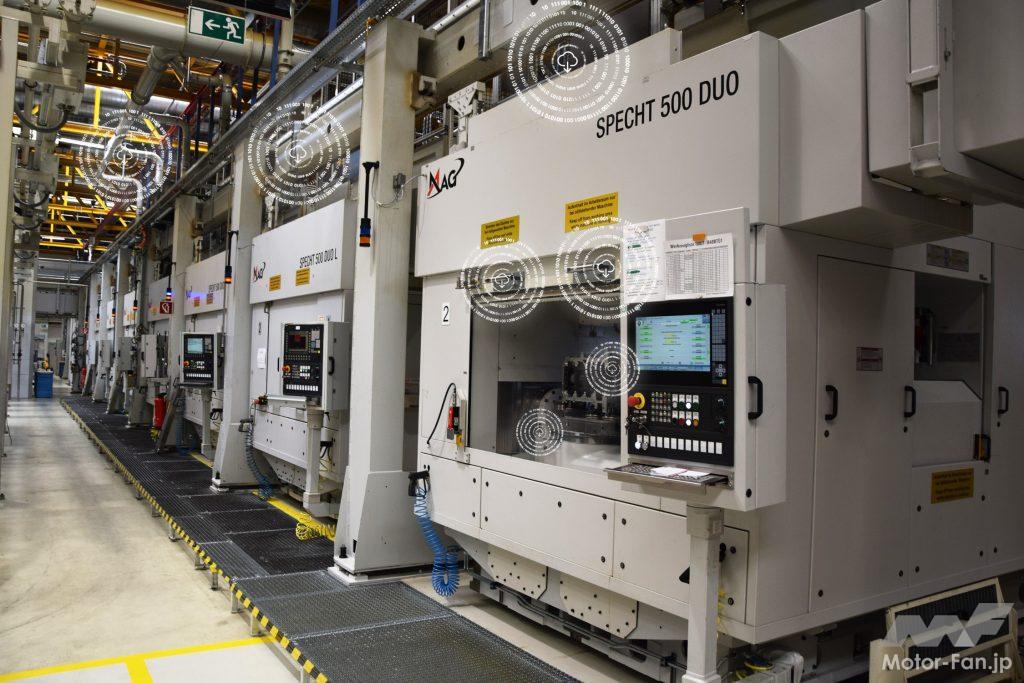
メンテナンスのデジタル化が進むにつれて、予測アプローチがますます重要になっている。予知保全では、機器のステータスデータを監視することにより、実際に発生する前にシステム障害を予測できる。システムの状態を常に最適化するためにデータを使用することで不必要なダウンタイムを防ぐ。その予防措置として、コンポーネントをいつ交換するかを決定する。予知保全とは無傷のコンポーネントの早すぎる交換を防ぐことでもあり、効率と持続可能性も向上させる。
クラウドベースのプラットフォームを介した状態の予測
BMWグループが生産において適用している予知保全システムでは、最先端のクラウドプラットフォームを使用して、潜在的な生産ダウンタイムに関する早期警告を取得している。データは製造システム自体から直接取得される。製造システム自体は、ゲートウェイを介してクラウドに接続されて監視されており、通常は1秒に1回データを送信している。プラットフォーム内の個々のソフトウェアモジュールは、必要に応じて柔軟にオンとオフを切り替えて、変化する要件に即座に対応している。また個々のコンポーネント間の高度な標準化により、システムはグローバルにアクセス可能であり、拡張性が高く、新しいアプリケーションシナリオの実装も容易であり、既存のソリューションを迅速に展開できる。
予知保全により、システムの実際の状態に応じて保守および修理プロセスを実行して、すでにスケジュールされている生産のダウンタイムを計画することもできる。修理は、これまでより正確に対象を絞り、よりコスト効率とリソース効率の高い方法で実行できる。さらに、実行時間を延長することで、ツールとシステムの耐用年数が大幅に延長される。このソリューションは、BMWグループの生産ネットワーク全体で開発され、頻繁に改修・展開される。
多様なアプリケーション
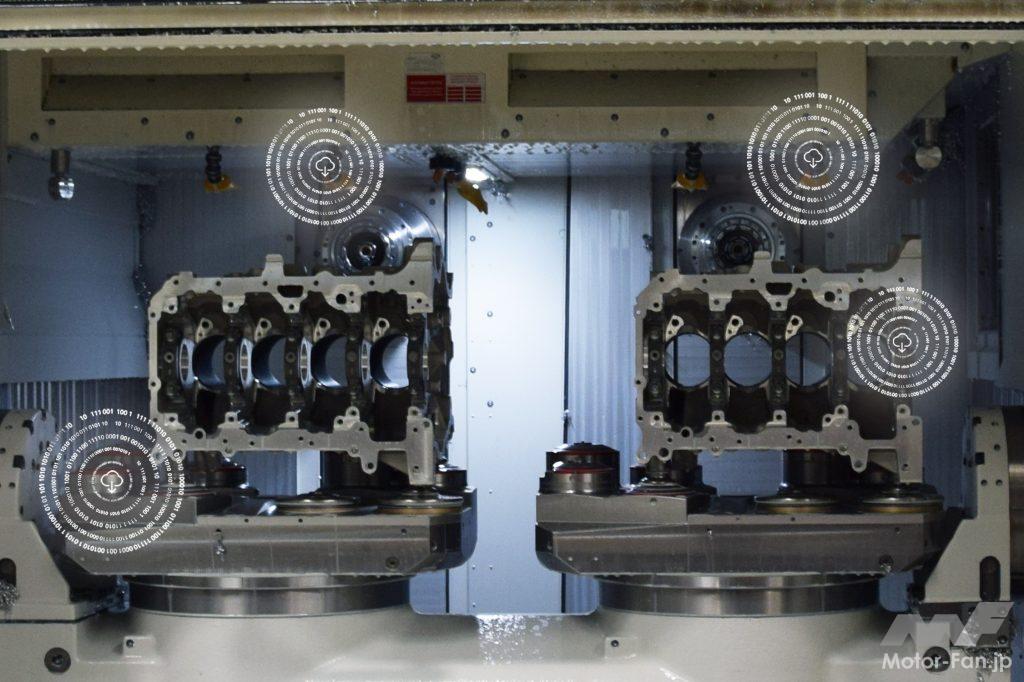
柔軟で高度に自動化された機械式ドライブトレイン製造システムは、従来のエンジンまたは電気モーター用のケーシングを毎分製造している。これらの生産設備を良好な状態に保つために、予知保全では単純な統計モデル、またより複雑なケースでは予測AIアルゴリズムを使用して、異常を検出している。そして視覚的な警告とアラートを発行して、メンテナンスが必要であることを従業員に通知している。
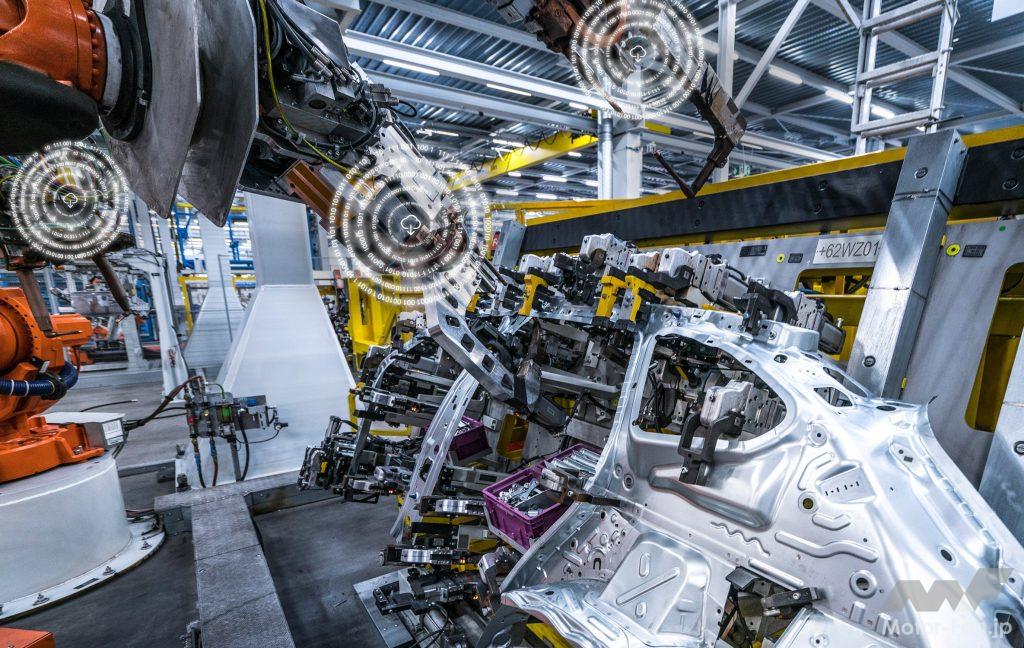
ボディショップでは、溶接ガンは1日あたり約1万5,000のスポット溶接を実行している。潜在的なダウンタイムを防ぐために、世界中の溶接ガンからのデータは、特別に開発されたソフトウェアによって収集されている。続いてアルゴリズムを使用して、照合および分析するためにクラウドに送信される。すべてのデータはダッシュボードに表示され、メンテナンスプロセスをサポートするために世界中で使用されている。
車両の組み立てでは、予知保全がコンベアのダウンタイムを防ぐのに役立っている。たとえばレーゲンスブルク工場では、コンベアシステムの制御ユニットが24時間年中無休で動作して、電流、温度などに関するデータをクラウドに送信、常に評価される。データスペシャリストは、任意の時点ですべてのコンベア要素の位置、状態、それにアクティビティを特定できる。予測AIモデルは、データを使用して異常を検出して、技術的な問題を特定している。