目次
Bentley Mulliner:460年以上前に遡る“マリナー”のヒストリー
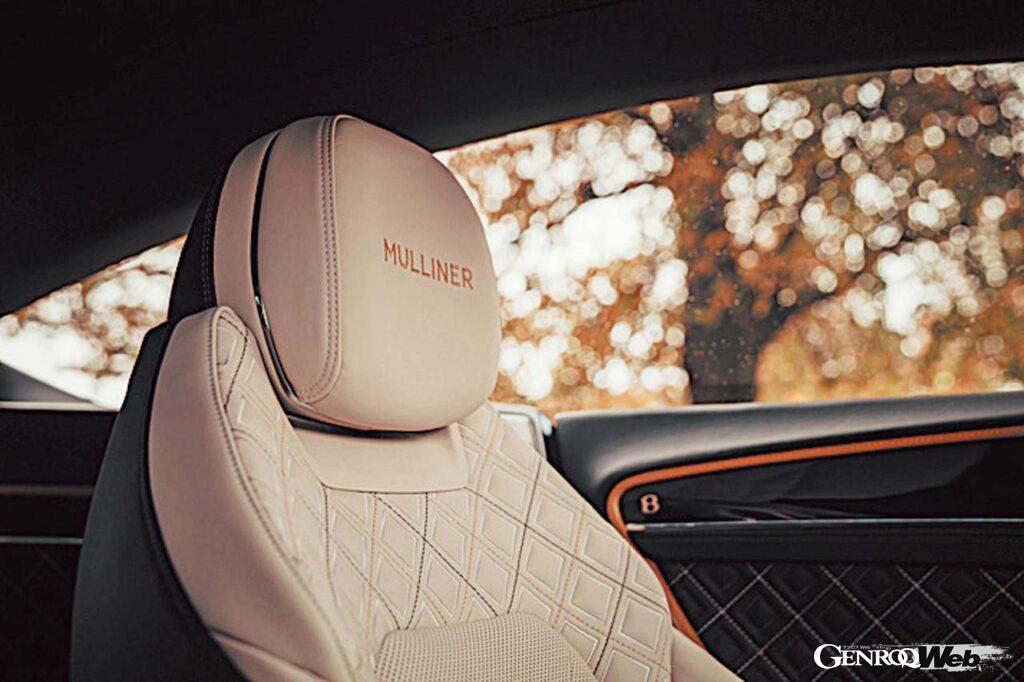
ベントレーのカタログやホームページを見ていると、オプションなどでよく目にするのが、“マリナー(Mulliner)”という名前だ。
果たしてマリナーとは何ものなのか? 話は18世紀のイギリスにさかのぼる。
1559年から馬車や鞍の製造を生業としてきたマリナー家は、1760年代にロイヤルメールの馬車製造とメンテナンスを受注したことで、一躍その名が知れ渡った。そして1870年にロバート・ブーヴェリー・マリナーが、馬車のコーチビルドを行うマリナー・ロンドン・リミテッドを設立し事業を拡大。その息子であるヘンリー・ジャーヴィス(H.J.)マリナーは1900年、当時最先端の乗り物であった自動車に興味を示し、ロンドン・メイフェアに自身の工房を立ち上げ、本格的に自動車のボディ製造に進出した。
自動車がまだ一部の特別な人たちの物であった時代、メーカーが製造したシャシーの上に、市井のコーチビルダーがオーナーからのオーダーに沿ったボディを製作し架装するのが一般的だった。その中で着実に実績を重ねていったH.J.マリナーは、1923年のオリンピア・ショーに展示するベントレー3リッターのボディを初めて製作。以来、両社の関係は親密となり、1920年代だけで240台のH.J.マリナー製ボディを架装したベントレーが造られた。
究極のクラフツマンシップを体現
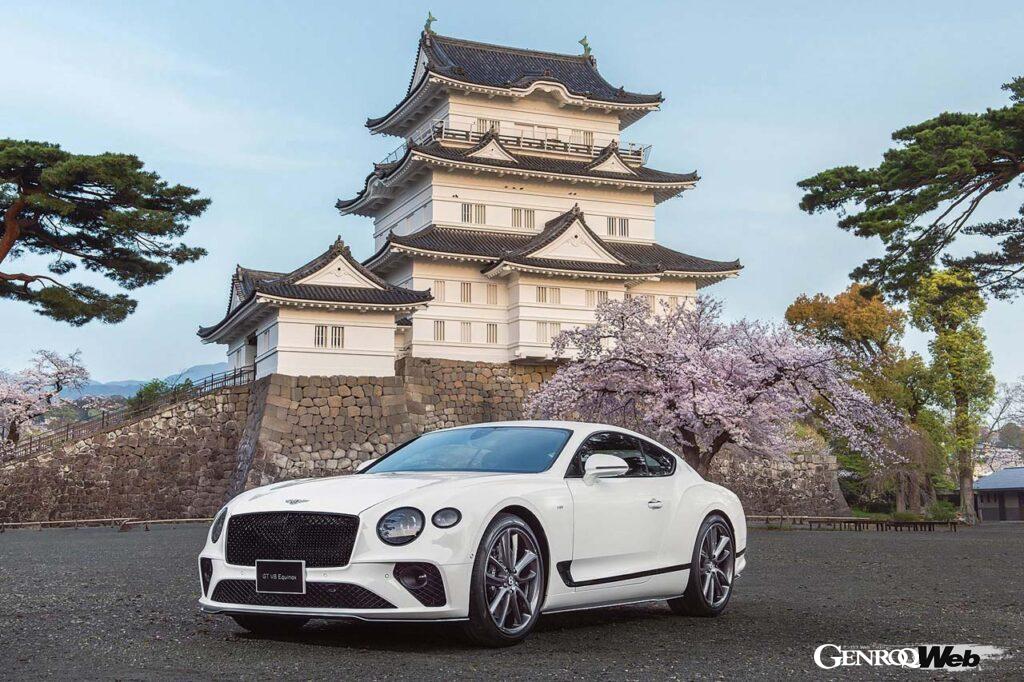
そんなマリナーの手がけた最高傑作が、現代ベントレーのデザインモチーフというべき1952年登場のRタイプ・コンチネンタルと、1957年登場のSタイプ・コンチネンタル・フライングスパーの流麗なボディである。
1959年、ついにH.J.マリナーはベントレーと合併を果たし、特注車や試作車などの製作を請け負うビスポーク部門となった。
かつてクルー本社工場の一角にあるマリナーの工房を訪ねた際、担当氏に「どんな方のどんな希望、要望にもお応えするのがこの部門の役割です。もちろん、相応の金額をお支払いいただければ、という条件はつきますが(笑)」と言われたことがある。その言葉の通りマリナーは、エリザベス女王即位50周年記念のステートリムジンをはじめとする数多くの特別なベントレーを送り出してきた、究極のクラフツマンシップをもつスペシャリスト集団なのである。
コーチビルド/クラシック/コレクションを展開
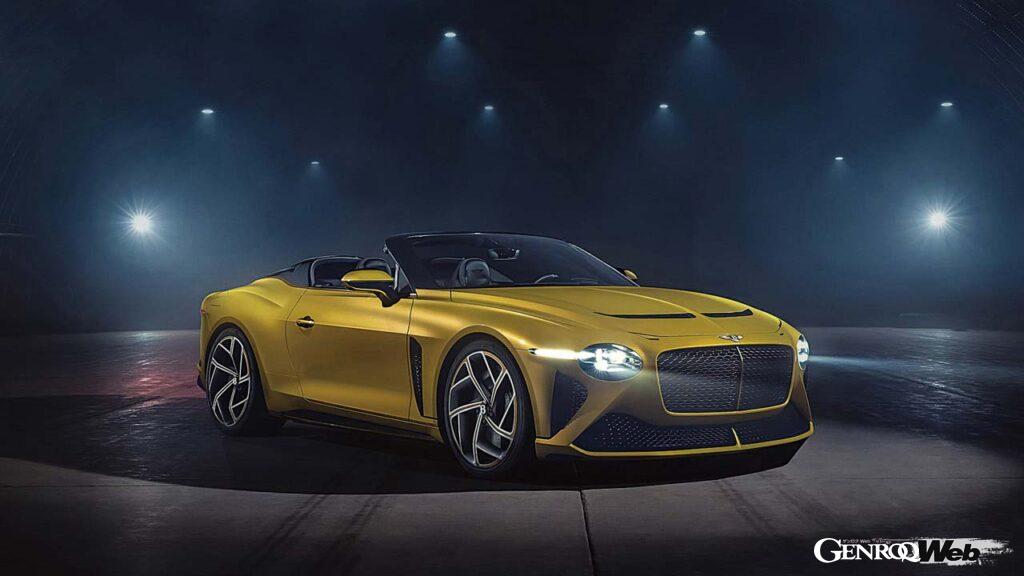
2020年、ベントレーはさらなる進化を目指してマリナーの体制を変更。ワンオフや、フューオフ・モデルを製作する“コーチビルド”と、レストアやコンティニュエーション・モデルを手がける“クラシック”と、レギュラーのスペシャルモデルを製造する“コレクション”の3つへと再編成した。
このうち“コーチビルド”を象徴するモデルとして発表されたのが、世界12台限定の2シーター・オープン“マリナー バカラル”だ。コンチネンタルGTと共通なのはドアハンドルのみで、あとはオーナーの好みに応じてハンドメイドで仕立てられるという2シーター・バルケッタは、まさにマリナーの真骨頂というべき作品。また彼らは“クラシック”においても1929年型の4・1/2リッターブロワーのコンティニュエーションを12台製造し、販売するほか、幻の1939年型コーニッシュをゼロから復元し発表するなど、精力的な活動を続けている。
ベントレーの特別仕様に冠される“マリナー”
さらに2020年にイギリス・ブレナム宮殿で開催されたサロン・プリヴェでは“コレクション”としてレギュラー化されるクーペとコンバーチブルのコンチネンタルGT マリナーを発表。艶やかなダブルダイヤモンド・マトリックスグリル、ダイヤモンド型テクニカルフィニッシュをあしらったセンターコンソール、ペイント&ポリッシュ仕上げの10スポーク22インチ・マリナーホイールなど、贅を尽くしたハンドメイドならではの内外装は、120年以上に渡って自動車のボディを造り続けてきたマリナーの名に相応しい、豪華で美しい仕上がりを見せる。
こうした活動を支えるために2014年に設立されたマリナー・デザインチームは、たった7年間で1000件ものビスポークプロジェクトとパーソナルコミッションを達成するに至ったという。そのことからもマリナーが世界の目利きたちにも支持される特別な存在であり、なぜベントレーの特別なオプション装備や仕様に“マリナー”の名が冠されているのか? その理由がお分かりいただけたと思う。
Home of Bentley:ベントレーが生まれる場所
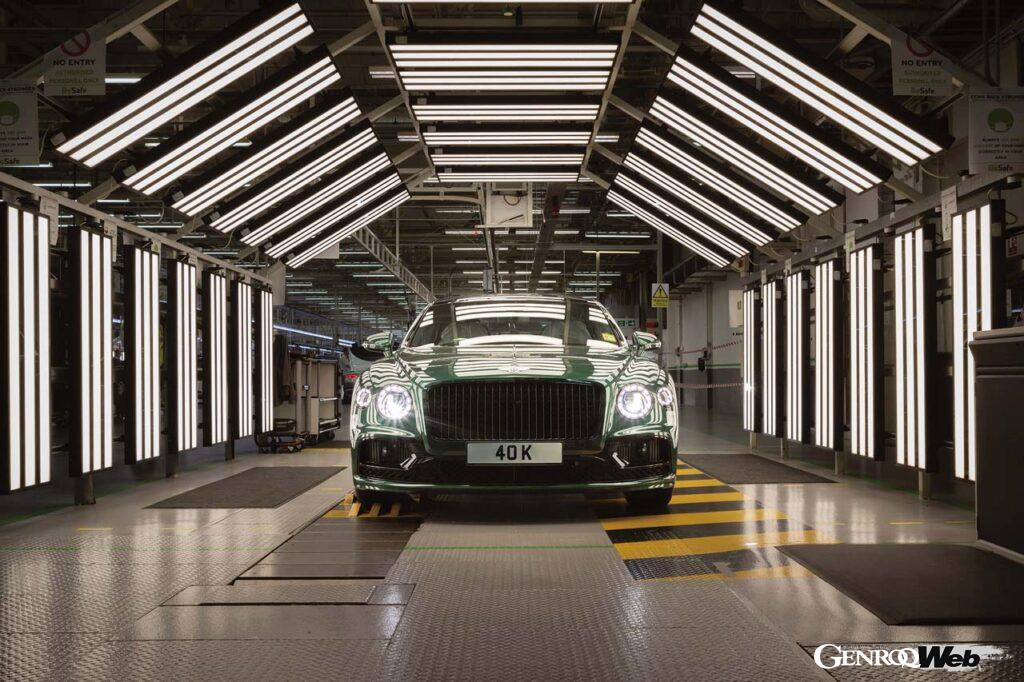
イギリス・チェシャー州クルーの外れにベントレーの本社工場はある。赤レンガ造りの建物自体は、1940年代から続くクラシカルなものだが、その中では伝統のクラフツマンシップと最新のテクノロジーが融合し、最適かつ最善のクルマ造りを目指して、日々進化が続いている。
イギリス・ヒースロー空港からバーミンガム方面にM40、M6と高速道路を走り続けておよそ3時間。イングランド北西部のチェシャー州にあるクルーという街の外れにベントレー・モーターズの本社工場はある。
彼らがダービーから新たに作られたクルー工場に本社機能を移転したのは1938年のこと。しかし折から勃発した第2次世界大戦のため、戦闘機スピットファイアのエンジンを作る軍需工場に転換され、乗用車の製造が始まったのは1946年になってからだった。
進化・拡張を続けるベントレーの本拠地
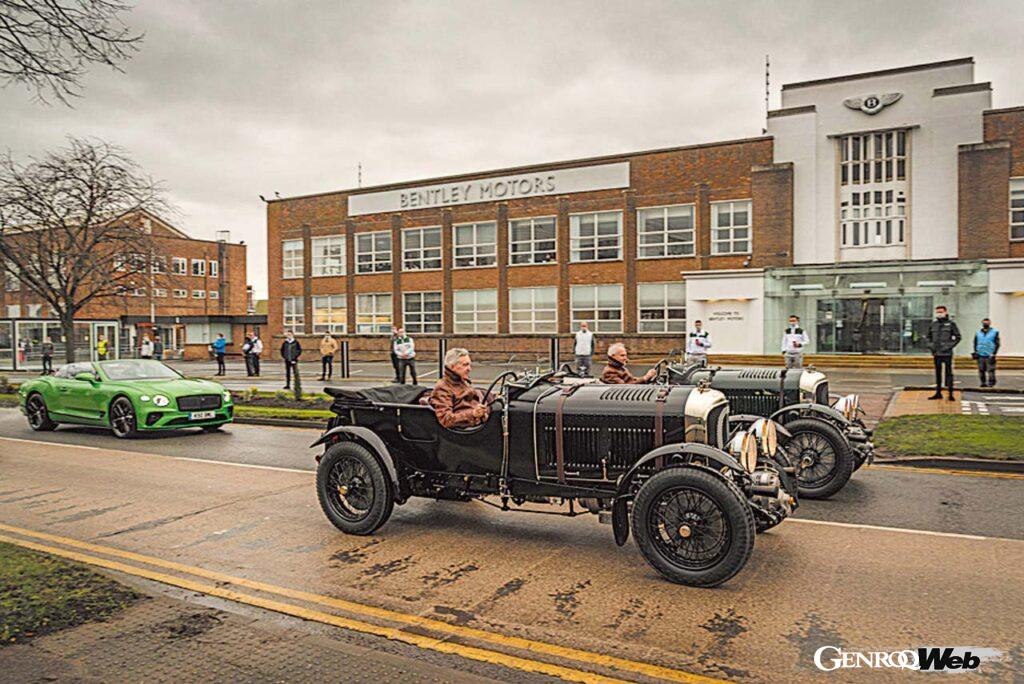
以来ベントレーはこの地で、会社創立以来の総生産台数の97%にあたる19万7086台のベントレーを送り出してきた。ちなみコンチネンタルGTが登場する2002年までのベントレーの全生産最数が4万4418台だったことを思うと、近年の飛躍ぶりが伺えるというものだ。
ほんの10年ほど前までは、建設当時の趣きのある赤レンガの工場群はそのままに、建物内だけを近代的にリノベーションした状態で製造が行われていたが、2008年登場のミュルザンヌに合わせて、スーパーフォーミング製法のアルミボディを製造する新しいボディ工場が建設されたのを皮切りに、工場屋根のソーラーパネル化、ベンテイガの生産に伴う製造ラインの改良、CW1ハウスと呼ばれるビジター・レセプションエリアの建設、さらに2021年にはそれまでマリナーのワークショップがあった場所に、50人のスペシャリストが650もの項目をチェックし、最終仕上げを行うエクセレンスセンターを新設(マリナーはこれまでミュルザンヌが使用していた生産ラインに移動した)するなど精力的に進化、拡張を続けている。
世界最先端の自動車ファクトリー
また2019年には高級車の生産工場として世界で初めてカーボンニュートラル認証を取得するなど、生産設備だけでなく環境面においても、世界最先端の機能を備えた自動車生産工場といえる。
このような最新な設備、機能と、古き良き赤レンガの外観とのコントラストは、まさに最新のテクノロジーと伝統のクラフツマンシップが融合したベントレーのプロダクトを象徴しているかのようでもある。
ラインはあるものの、多くの部門は手作業で施される
さて、52万平方メートル以上という広大な敷地内には、ボディ製造工場、エンジン製造工場のほか、ペイント部門、インテリアのウッドパネル、レザーの加工部門、裁縫部門、組み立てアッセンブリーなど、自動車を1台造るのに必要な様々な部門が隣接している。1998年にフォルクスワーゲン・グループになって以降、莫大な投資が行われた結果、機械化、自動化が加速し、ジャスト・イン・タイム方式を導入するなど効率化も図られてきたというが、それでも他メーカーの製造ラインに比べると、圧倒的に人の手に寄る部分は大きいという印象だ。
例えばフライングスパーV8の製造に必要な時間はおよそ130時間。全体で84もの工程があり、60ピースからなる内装の部品だけでも141人の職人が3kmの糸と350枚のレザーを駆使して製作する必要があるという。またボディペイントでは、1台、1台を手作業で丁寧に塗装。十分に乾燥させた後、サンドペーパーで研ぎ出し、さらに子羊の毛で12時間かけて磨きあげる。
1台1台に膨大な時間をかけて生産されるベントレー各車
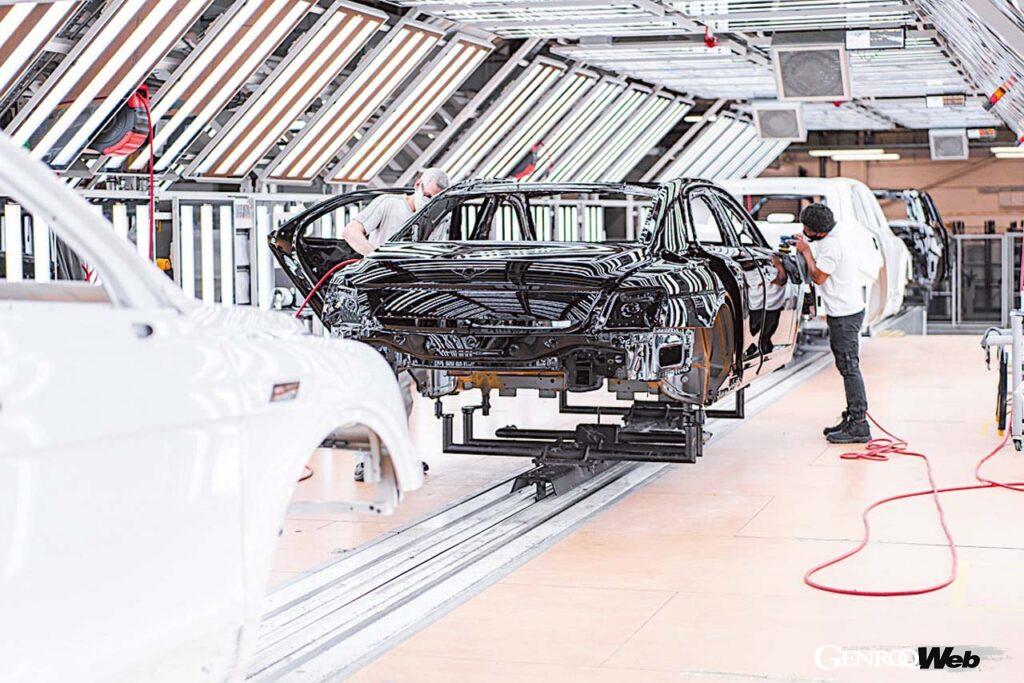
ちなみに一般的な日本車の1台あたりの製造時間は約18時間。そう思うと、いかに手間隙をかけ丁寧に造られているかが、お分かりいただけるはずだ。
実際、工場の各セクションを見学してみると、老若男女様々な人々が、丁寧かつ真摯に作業をしている光景に出会う。彼ら全員から感じるのは、ベントレーを造っているというプライドだ。無論作業中なので多くを語ることはできないが、以前に出会ったレザーを担当する職人のこんな言葉が忘れられない。
「ベントレーの魂はクルーにある」
「ベントレーの魂はクルーにあるんです。ロールス・ロイスがこの地を去った時も、働いていたほとんどの人がクルーに残ったことでもわかるように、今やこの地域にとってもベントレーはかけがえのない存在。私たちの誇りなんですよ」
世界中のベントレー・オーナーがクルーを“聖地”と呼ぶのは、歴史や実績だけでなく、こうした人々の温もりと情熱が、送り出される1台、1台に感じられるからに違いない。
Craftsmanship in Interior:至高のクラフツマンシップ
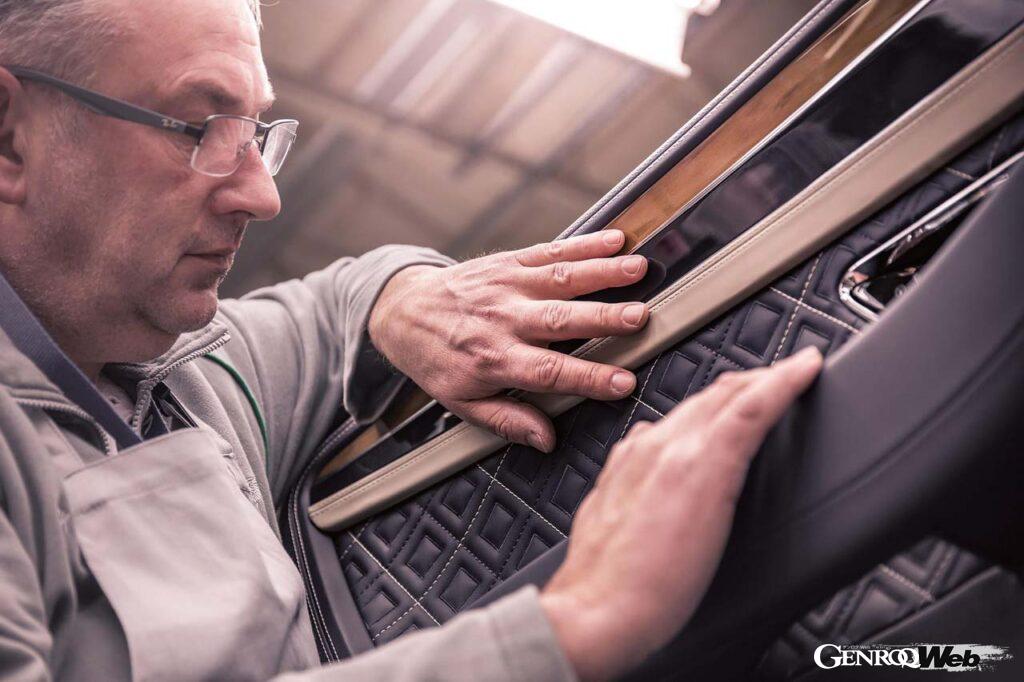
色とりどりのレザーとウッドなどによって彩られたベントレーのインテリア。他の高級車とは一線を画する、この特別な空間を支えているのが世界中から厳選して集められてきた上質な素材と、それを生かすデザイン、そしてクルー本社工場に代々受け継がれてきたクラフツマンシップだ。
クラフツマンシップ・・・日本語では“職人技”と訳されるこの言葉は、ベントレーのクルマ造りのハイライトのひとつである。
その真髄を最も感じられるのが、インテリアだ。
中でも、ふんだんに使われるウッドとレザーの織りなす、優雅で上品な空間は、ベントレーならではで、決して一朝一夕にできるようなものではない。
膨大な木材から厳選された部位のみを使用
近年、カーボンやアルミなど様々な素材を扱うようになったため“ウッドショップ”から“トリムショップ”へと改称したインテリア加工部門を訪れると、まず圧倒されるのが、目の前に現れる膨大な木材の山だ。
お馴染みのウォルナット、チェリー、オークをはじめ、エレガントで直線的な木目を持つコア、明るい材色と繊細な木目が美しいタモアッシュ、赤茶色の色味が特徴なレッドガムツリーなど、木材のスペシャリストが世界中を駆け巡り集めてきた木材が、厚さ0.6mmのベニヤの束に細かくスライスされ、種類ごとに積み上げられている。
ちなみにこれらは、新しい木を伐採したものではなく、自然に倒れた倒木のみを採取し、1本採取したら必ず新しい木を同じ場所に植樹するという、ベントレー独自のルールを徹底したうえで仕入れられたものだという。
ベントレーでは、コクピットを取り囲むウッドパネルが左右対称となるように、2枚に薄くスライスし、表裏を逆にして加工するミラーマッチングという技法を採用。すべてのウッドパネルは72時間硬化された後、ラッカー塗装と磨き上げの作業を5回も繰り返され、独特の艶と深みをもつウッドパネルへと仕上げられるのだ。
ベンテイガ1台に費やされるレザーは牛14頭分
もうひとつ、インテリアの特徴であるレザーは、有刺鉄線がなく涼しい北ヨーロッパの牧場で育てられた、虫刺されなどの傷がなく状態のいい牛皮が使われる。
原皮から毛や汚れを落として柔らかくなめし“皮”から“革”へと変化を遂げたレザーは、専門の検査官の手に委ねられ細かい傷をチェック。それを避けたうえで無駄が出ないよう、丁寧にカットされていく。それでもベンテイガを1台製作するのに約14頭分、フライングスパーでは13頭分、一番少ないコンチネンタルGTでも10〜11頭分のレザーが必要となる。
クルー工場ではダイヤモンド・イン・ダイヤモンド・ステッチなど、一部の複雑な裁縫に関しては最新のミシンを導入して自動化を果たしているが、それ以外の大部分は120人の裁縫職人チームの手作業で賄われている。もちろん仕様によって違いはあるが、フライングスパー1台のレザーを仕上げるために26時間もかかるという。
一方で従来の技術、技法に固執することなく、フライングスパーで乗用車用として世界で初めて採用された3Dレザーや、そのコンセプトをさらに進化させた3Dウッドなど、新たな技術の開拓にも積極的なのがベントレーの特徴だ。
技術と情熱が成しえる最上級のインテリア
また化石化したオーク材を再生したリバーウッドをコンセプトカーEXP100に続きマリナー・バカラルにも使用。新型フライングスパー・ハイブリッドに用意されるオデッシアエディションでは、100%英国産のウールを使ったツイードパネル、ラッカーの使用量を90%削減したオープンポア仕上げのコア材、耐久性が向上したサステナブル・レザーを採用するなど、持続可能性を高めた高級車のインテリアにおいても一歩先をいく存在であり続けている。
こうしたイノベーションを可能としているのは、インテリア部門とデザイン部門が近く、頻繁にデザイナーが現場を訪れて職人たちに意見を求め、アイデアを活かすことで、製品に繋げるという理想的な関係が構築されているからだ。
つまり、ベントレーのクラフツマンたちは、ただの職工ではなく、時に開発やデザインにも関与し、プロダクトをソフトとハードの両面から支える、かけがえのない存在なのだ。
ベントレーのインテリアが高級感やデザインだけでなく、その独特な世界観においても他の追随を許さないのは、そんな彼らの技術と情熱が惜しげもなく注ぎ込まれているからなのである。
REPORT/藤原よしお(Yoshio FUJIWARA)
MAGAZINE/GENROQ 2021年 10月号(特別付録 小冊子「THE WORLD OF BENTLEY」より)