テスラや中国勢を追撃、追い抜くための「ギガキャスト」
トヨタは2023年5月にバッテリーEV専任組織「BEVファクトリー」を発足させている。ここでは、クルマ・モノづくり・仕事を変革し、「BEVで未来を変える」ことをテーマに据えている。
クルマ軸では、次世代電池が主役となる。これについては、別稿で詳細にレポートする。
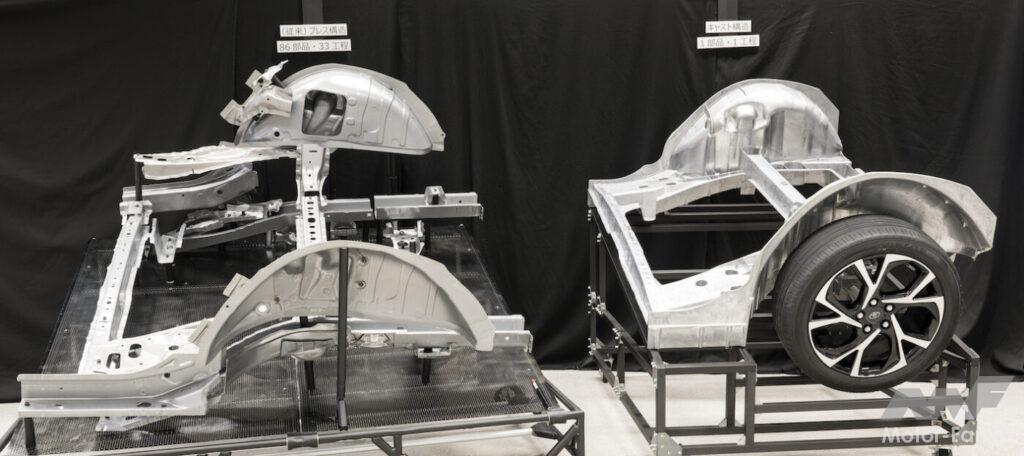
モノづくり軸のメイントピックは「ギガキャスト」の採用である。ギガキャストとはなにか?
これまでの……というか、一般的な工法だと、乗用車は鉄板をプレス成形して、多くの部品を溶接して組み上げたモノコック構造を採っている。大量生産がしやすい、材料費が安い(スチールだから)、剛性が出しやすい、多品種生産に対応しやすいなどのメリットがある。
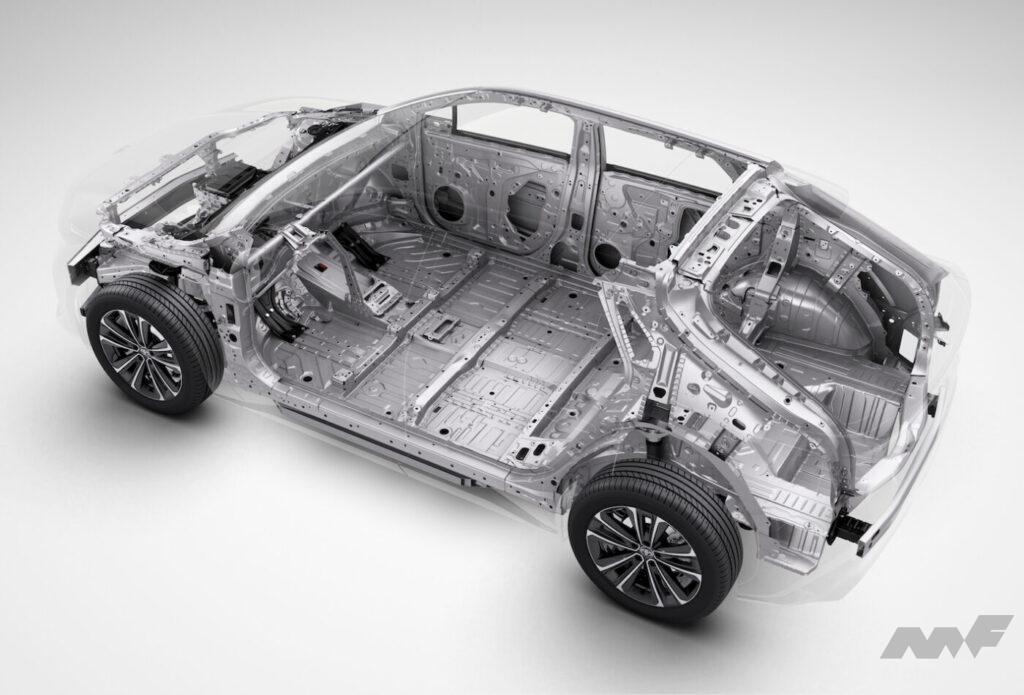

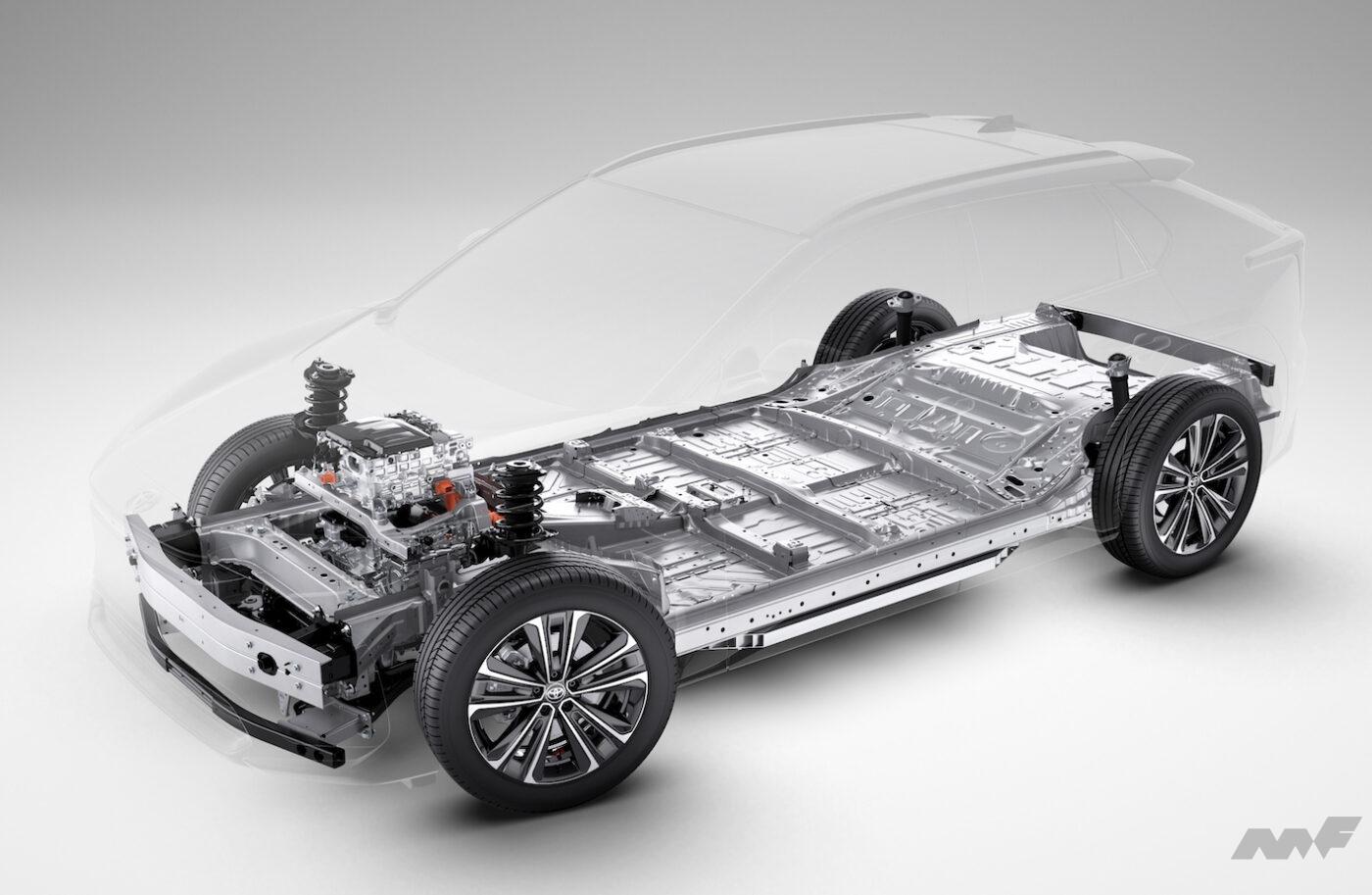

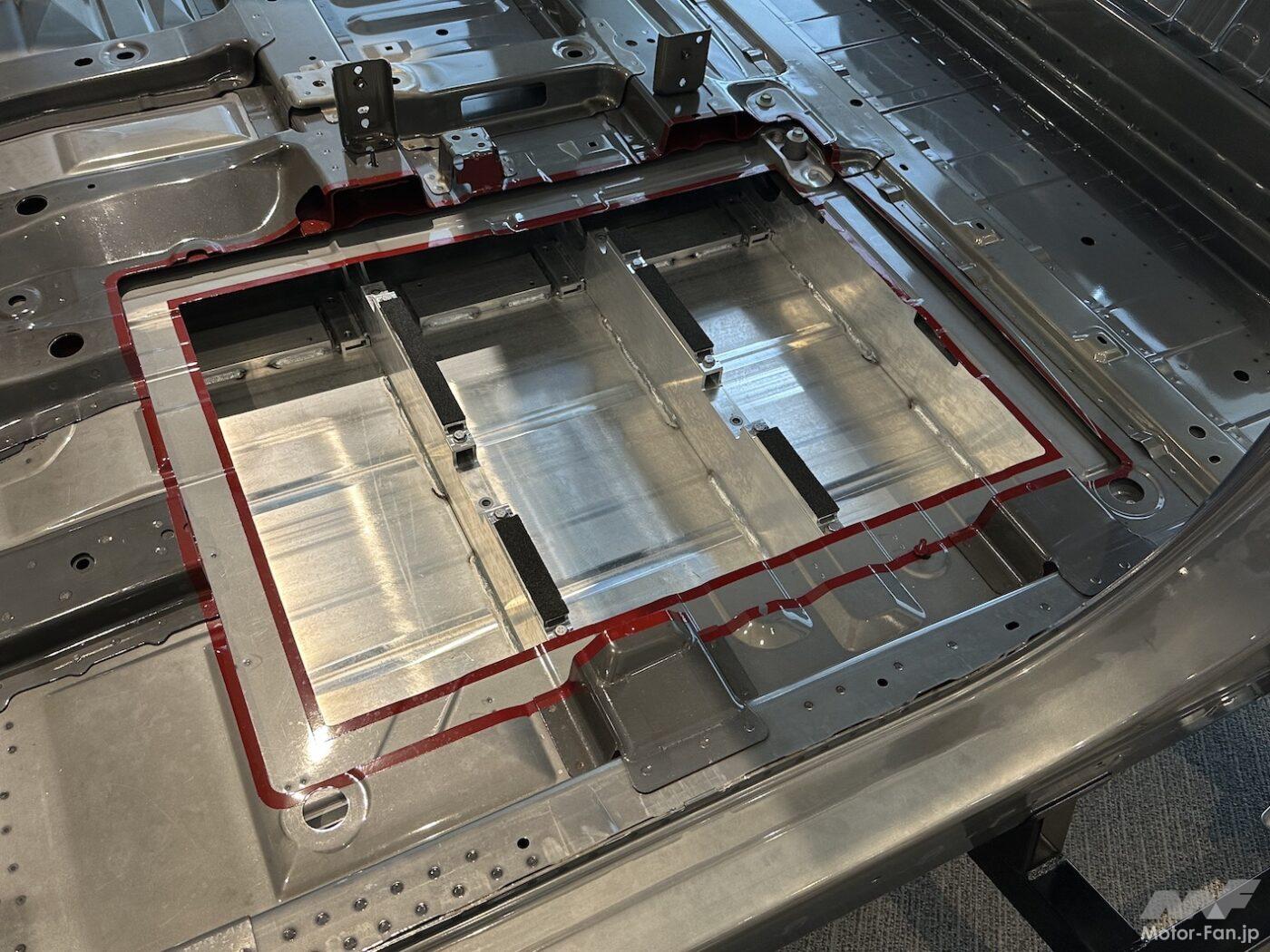



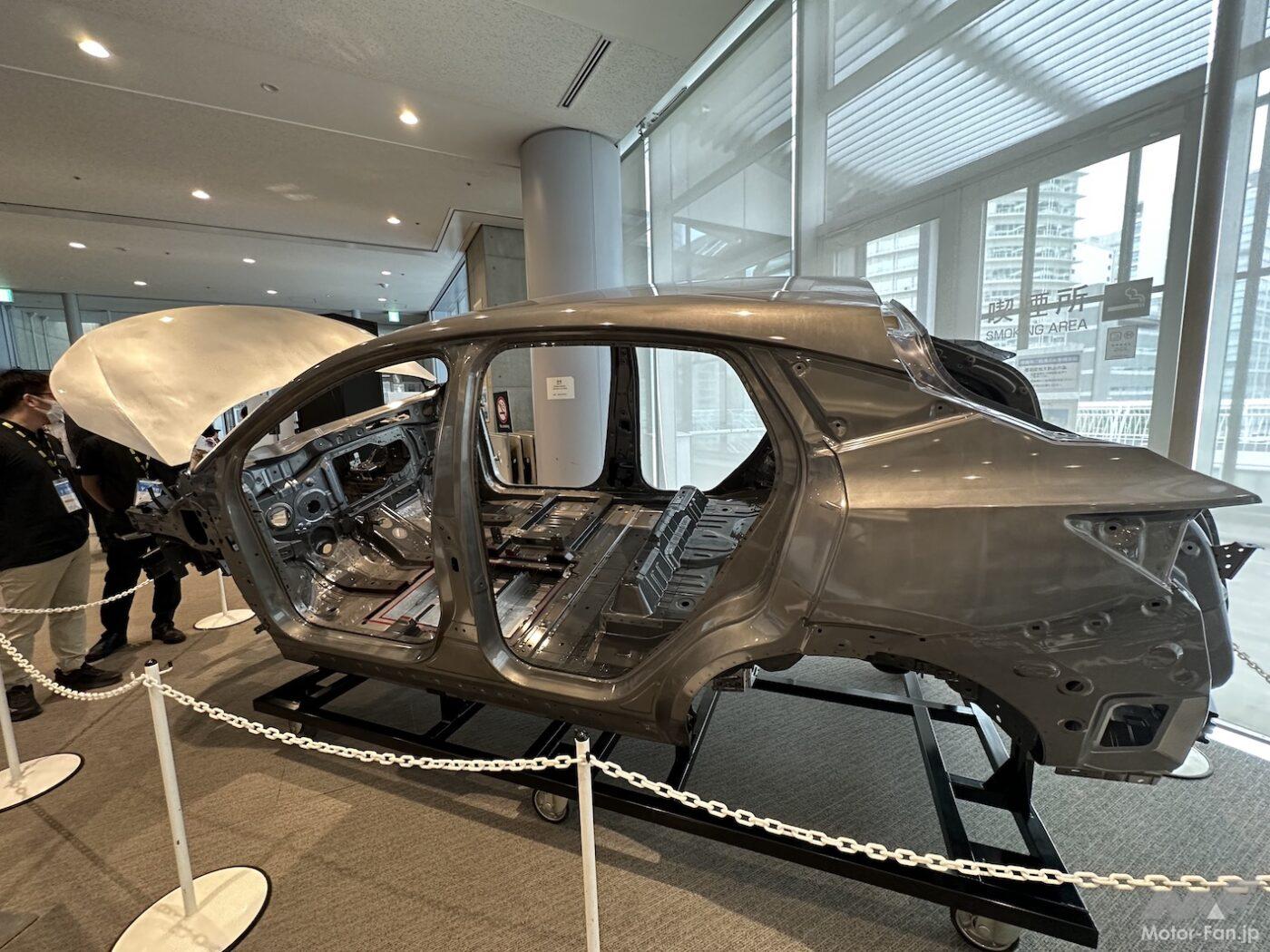
しかし、BEV時代になると、これまでの常識が通用しなくなる。
米・テスラが先鞭を付けた工法が「メガキャスティング」(ギガプレスともギガキャストとも呼ばれる)だ。簡単に言えば、アルミダイカスト(鋳造)で車体全体を一体成形する技術だ。無論、一体といっても、いくつかに分割して作るわけだが、それでも圧倒的に部品点数が少なくて済む。それはイコール工数の削減=コスト低減に繋がるわけだ。
今回、トヨタがTOYOTA TECHNICAL WORKSHOP2023で公開した「ギガキャスト」はトヨタ流のBEV時代のボディの作り方の回答だ。
展示されていたのは、トヨタのBEV、bZ4Xのリヤセクションとギガキャストでそれを造ったサンプルだ。
bZ4Xは、プラットフォーム(というか技術基盤)としてBEV用のe-TNGAを使う。しかし、工法は従来通り、板金を組み合わせて接合するものだ。
この場合は、
素材:鉄
部品数:86
工程数:33
である。
ではギガキャストはどうか?
素材:アルミ合金
部品数:1
工程数:1
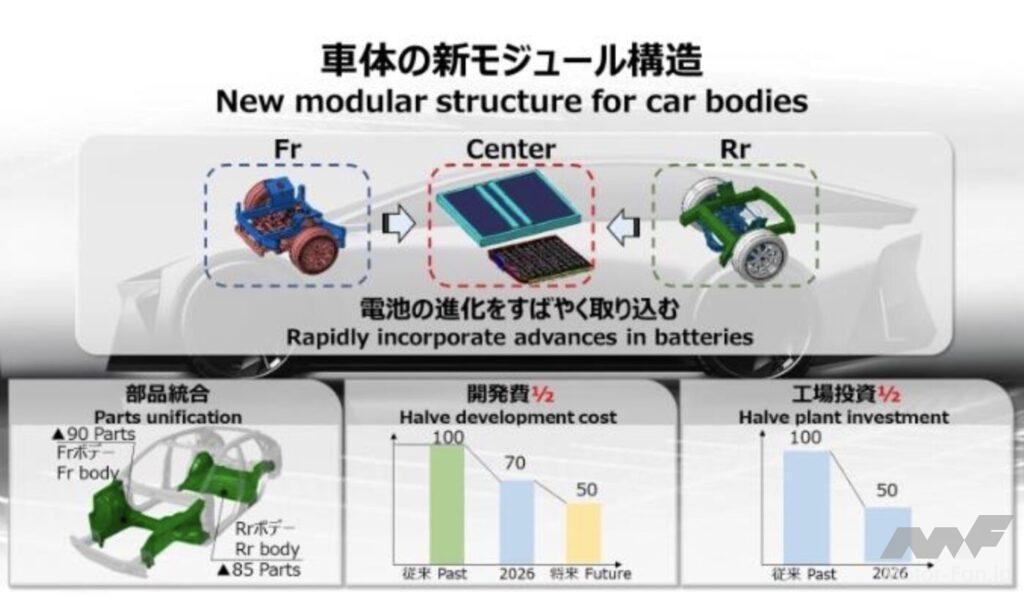
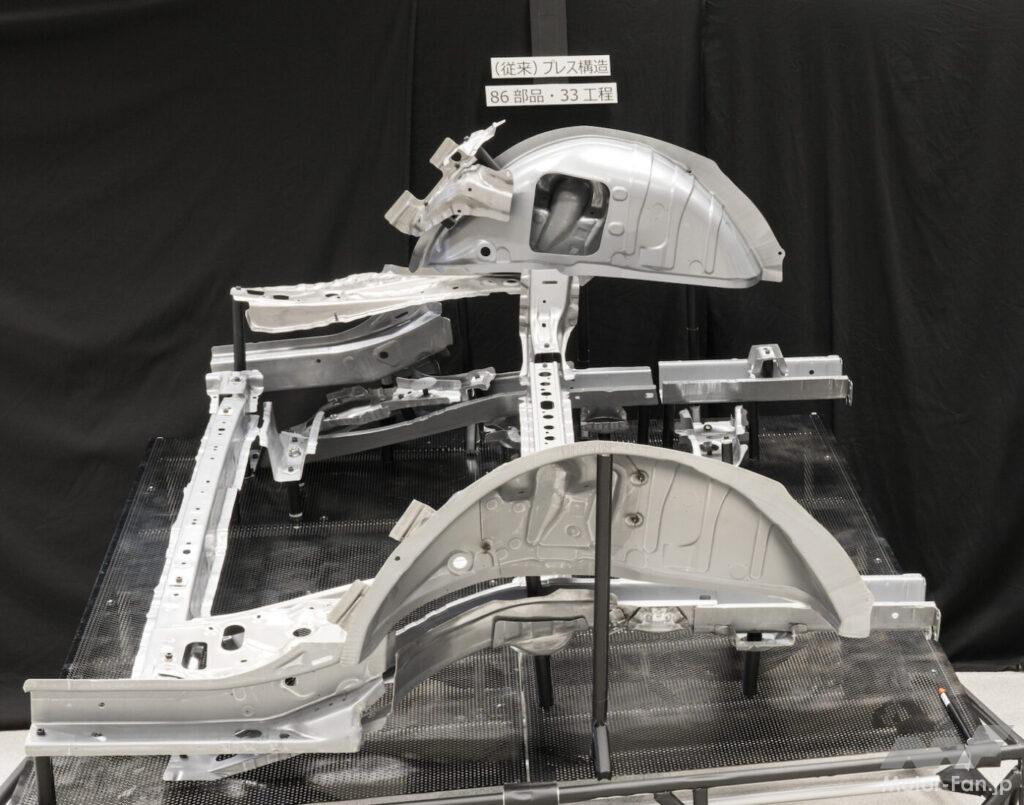
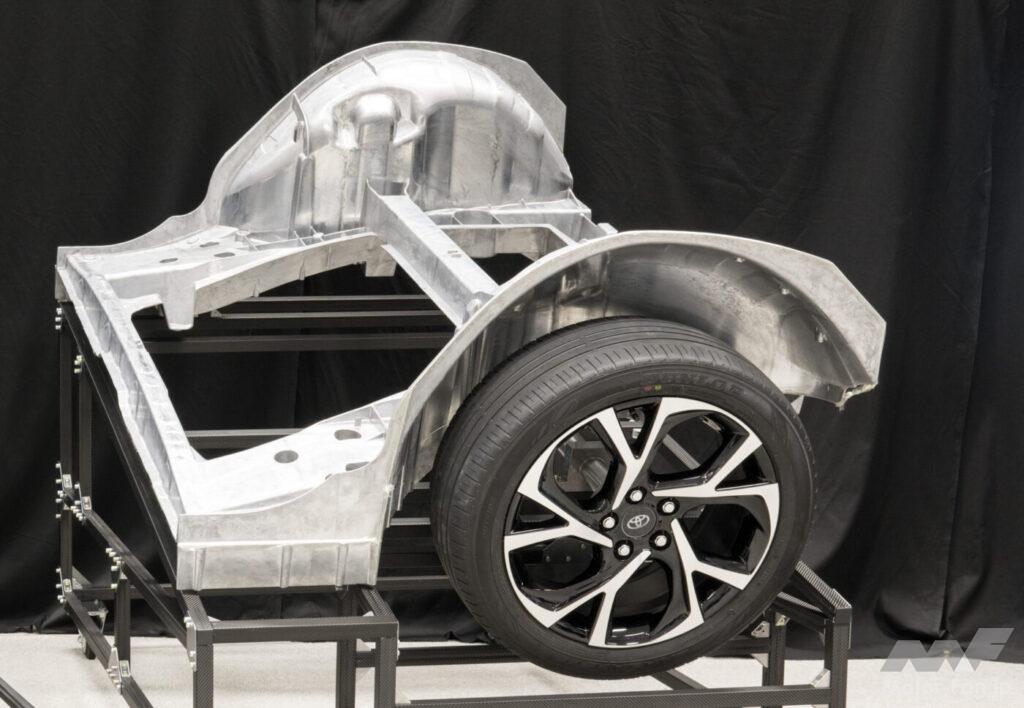
鉄からアルミに変わることで素材の価格は上がるが、工程が減ることでコストも削減できるという。そこには、もちろんトヨタ得意のTPS(トヨタ生産方式)による徹底した無駄の排除や、CAEやMBD(モデルベース開発)を駆使した開発が前提となるが、ギガキャストをものにすることで、トヨタの次世代BEVはボディ構造の上ではライバルたちと同じ土俵、あるいはそれより優位な場所に立てるはずだ。コストに関しては、「素材としてバージンアルミ材を使っていてはコストを下げられない。リサイクルしたアルミ材を使う」という。
「他社と比べて生産性は20%高い」と説明されたが、この場合の他社とは、おそらくテスラのことだろう。これだけ巨大な鋳造部品を造るには、巨大な型とダイカストマシンが必要になるが、それも「ライバルの3分の2程度の大きさに抑えられている」という。
アルミダイカスト(鋳造)だから、部分的に肉厚を変えることができる。そこで剛性を確保しつつ軽量化も可能になるという。「従来工法から劇的に、ではないが、ギガキャストで軽量化できる」とエンジニアは説明してくれた。
トヨタが考える次世代BEVの構造は、フロントとリヤをギガキャストで成形し、センターはバッテリーを敷き詰める部分ということになる。バッテリーの種類・量によって車両のサイズ、ホイールベースも変わるということだろう。
ギガキャストになれば、すべてがバラ色か、というと、当然のことながら課題はある。
まずは、鋳造後に冷却で収縮するので、寸法保証が難しいという。また、ギガキャストで造られた大型一体成形パーツとほかのパーツの接合も難しいのだという。これは寸法の問題と繋がっているのだろう。
また、テスラでも問題になっている「リペアビリティ」もギガキャストの大きな課題だ。つまり、修理のしやすさ、である。事故や衝突のたびにリヤセクションを丸ごと交換するのは、コスト的に現実的ではない。トヨタ技術陣は、ここにも一定の目処を付けたという。
具体的には、衝撃を吸収する部分をギガキャストとは別に用意するということらしい。確かに、現物で確かめると、リヤのバンパー/クラッシュストラクチャーは別体で付く構造になっていた。
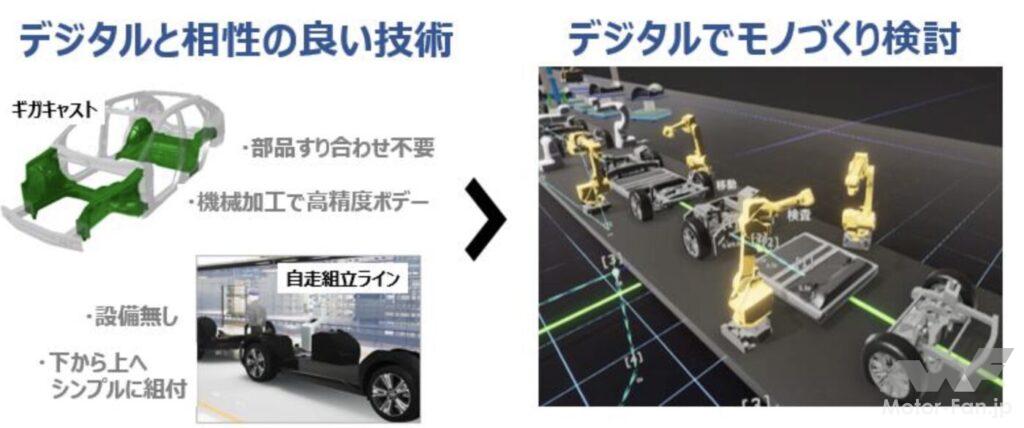
「コンベア」の概念をなくした次世代工場の設計にチャレンジする。 組立中の量産車が、自走して次工程に移動できるようにする技術として開発中だ。
フロントとリヤをギガキャストで造るとなると、車種のバリエーションをどう作るかも考えなくてはならない。前後ともに数種類の大型一体パーツを用意すれば、センターのバッテリー部分も組み合わせて多くのバリエーション(車種)を作り出せるが、それは現実的ではない。そのあたりを2026年までにどう整理して実用化に漕ぎ着けるかも注目だ。